- FMA
- The Fabricator
- FABTECH
- Canadian Metalworking
Our Publications
Categories
- Additive Manufacturing
- Aluminum Welding
- Arc Welding
- Assembly and Joining
- Automation and Robotics
- Bending and Forming
- Consumables
- Cutting and Weld Prep
- Electric Vehicles
- En Español
- Finishing
- Hydroforming
- Laser Cutting
- Laser Welding
- Machining
- Manufacturing Software
- Materials Handling
- Metals/Materials
- Oxyfuel Cutting
- Plasma Cutting
- Power Tools
- Punching and Other Holemaking
- Roll Forming
- Safety
- Sawing
- Shearing
- Shop Management
- Testing and Measuring
- Tube and Pipe Fabrication
- Tube and Pipe Production
- Waterjet Cutting
Industry Directory
Webcasts
Podcasts
FAB 40
Advertise
Subscribe
Account Login
Search
Behind the hype of additive manufacturing
3-D printing won’t change the world overnight, but change is coming
- By The Fabricator editors
- July 7, 2015
- Article
- Additive Manufacturing
Editor’s Note: This article is based on “Innovation & Disruption: Impact of 3-D Printing,” a keynote presented at the 2015 FABRICATOR®’s Leadership Summit and Toll Processing Conference at FMA’s annual meeting, Kissimmee, Fla., by Todd Grimm, president, T.A. Grimm & Associates, 3028 Beth Court, Edgewood, KY 41017, 859-331-5340, www.tagrimm.com. For more on FMA’s annual meeting, visit annualmeeting.fmanet.org.
Additive manufacturing, popularly known as 3-D printing, is no stranger to hype. Revolution is imminent; change is on the horizon. If you don’t get onboard now, according to the pundits, you’re going to be a buggy-whip manufacturer in the age of the automobile.
In fact, the automobile itself won’t be manufactured anymore, they say. It’ll be printed from the ground up. After all, a titanium bike already has being printed. At the International Manufacturing Technology Show last year, an entire car was printed in 44 hours. Then at the Detroit Auto Show earlier this year, a classic Shelby Cobra race car was printed in 24 hours. In the course of four months, we went from 44 hours to 24 hours. Oh my goodness, the world is going to change as we know it.
Or is it? Some don’t buy the hype. Sure, it takes 24 hours to print a car, but not every component was printed, a lot of pre- and postprocessing took place, and even the people who printed the car don’t believe that they’ll see 3-D printing take over automotive production within their lifetime. While their technology will disrupt the prototyping space, which is a big deal for the many prototyping shops, it won’t suddenly make current automotive manufacturing irrelevant. And, yes, a company has printed a titanium bike, but it was entirely experimental. The frame alone cost $30,000 to make—and that’s just the base cost, with no margin at all.
As is so often the case, the reality is somewhere in the middle, between the hype and skepticism. Additive manufacturing (AM) is here to stay, but it isn’t going to change the world overnight. Instead, it will change the manufacturing landscape in ways you might not imagine, especially when designers and engineers think differently.
Challenges and Opportunities
GE’s much-talked-about jet fuel nozzle exemplifies this perfectly. It made headlines because it was one of the first metal parts to be additively manufactured at production levels. The company plans to make 40,000 of these nozzles a year by the end of the decade—a huge number in the additive world. The company spent 12 years and millions of dollars in development, qualifying these parts for production. GE also announced that its manufacturing facility for this part will start with 10 machines and grow as production rates increase. That’s the reality check. The typical manufacturer wouldn’t think of using 10 laser cutting machines or stamping presses to produce just a few thousand parts.
The hype says that 3-D printing will eliminate many manufacturing steps. Why cut, bend, stamp, and weld when you can just print millions of parts? Well, at this point the math still greatly favors traditional production. The machines and materials used for metal AM remain expensive. One machine can cost roughly $500,000, and other needed equipment brings the total investment to around $1 million. Powdered metal for these machines starts at $150 a kilogram. Print something like Ti 6-4, and the price goes up to about $600 a kilogram.
The technology also can’t build parts to the tight tolerances of precision machining. Many applications out there involve an additive process followed by some finish-machining. The machining time isn’t long, compared to machining the entire part, but the secondary process remains necessary. For such applications, AM isn’t yet a done-in-one operation.
But does every surface of a component require such tight tolerances? Usually not, and AM can build up part geometries that just wouldn’t be practical in traditional machining. This has led some machine makers to introduce hybrid systems that feature both subtractive (machining) and additive processes. These systems both mill and perform an additive process where it makes sense for a specific job.
This is a young industry. Outside of some laser cladding systems used for additive processes, few AM machines have been around for more than a dozen years. Knowing this, it’s no surprise that the AM sector lacks industrywide quality standards. Many additive processes entail powder metallurgy; how do you qualify and inspect individual layers of material deposited by AM? What level of porosity within those layers is acceptable, and how consistent does the material density have to be? We don’t have reams of process data—yet. In fact, much of GE’s investment in AM was spent developing their own quality standards and methods and testing parts under those guidelines.
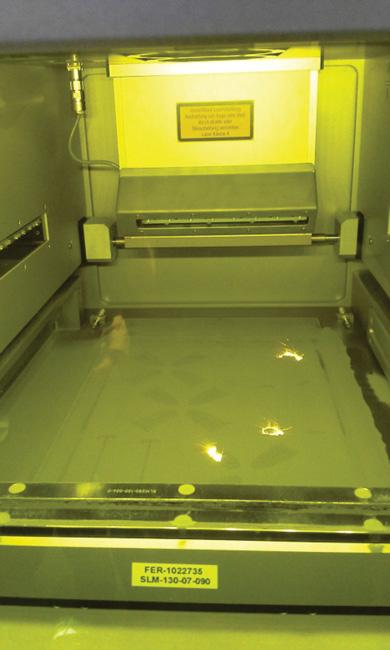
A laser-melting additive manufacturing process iteration, branded as Selective Laser Melting®, starts building up a part layer by layer. Photo courtesy of SLM Solutions, www.slm-solutions.us.
Moreover, few if any graduating from technical schools have experience with AM, and hiring people with expertise in the field is just as difficult. Technicians who really know additive processes tend to be well-paid. Many learn on the job, and companies need to do all they can to keep them onboard. The technology is just too new.
So why then has GE invested so much in this technology, just to produce a little fuel nozzle? As with anything in business, it comes down to dollars: $1.5 billion. That’s how much GE’s customers will save in fuel over the life of a plane. It has little to do with savings in manufacturing cycle time or unit costs. It also isn’t about pushing the envelope to tackle a futuristic manufacturing process, though no doubt this story hasn’t hurt GE’s brand. No, it is to save their customers serious money and thereby make GE that much more competitive.
This shows that the technology is now and will continue to make revolutionary changes for the right applications. The trick lies in first throwing out everything you know about traditional manufacturing. Machined parts are often bulky because manufacturers want to remove as little material as possible. Sheet metal parts may require minimum flange lengths and bend radii for forming, or they may need to be of a certain thickness or shape to ensure welders, be they manual or robotic, can access and make the joint without creating distortion. To think in these terms is to ignore what AM is best at.
AM’s principal constraints are long machine cycle times and high material costs. If you stamp a sheet or bend a tube and send it to the customer, AM probably isn’t for you. But if that flat sheet could benefit from having a honeycomb structure that drives out weight and costs, or if thin piping would benefit from ribbing or other components on the ID to aid fluid flow, now we’re talking.
Conventional manufacturing requires tooling and fixturing, so minimum economic order quantities are baked into a lot of organizations. For instance, a manufacturer might be interested in contracting out 5,000 pieces to a job shop specializing in additive manufacturing. The job shop manager will probably tell that manufacturer that he can’t help—the lead time and costs for 5,000 pieces would be astronomical.
But then the job shop manager asks an important question: “Why do you need 5,000 pieces?” This job previously was made using a method that involved significant tooling and development costs, so it made no sense to buy anything fewer than 5,000 pieces. That’s fine, but how many does the manufacturer really need? If it’s, say, 300 the first month and 300 the second month, that may open up opportunity for additive processing.
AM requires big changes in how people think about manufacturing, and people often resist change. The change puts them outside of their comfort zone, for sure. But additive manufacturing isn’t about to force organizations to abandon decades of conventional manufacturing practices. It will just require people to think differently.
Technology Basics
When it comes to product development and prototyping, additive manufacturing has become a serious tool. In the production space, major applications for metal AM are emerging in the medical, dental, and defense sectors. Up-and-coming sectors include luxury goods (think high-end watches) and power generation. Much of the production AM work has two things in common: It is low volume and has high value.
The AM industry remains extremely small. Although major machine tool players are moving into the metal AM space, the total install base is now only about 2,000 machines—that’s not just in the U.S., but globally. It’s certainly growing rapidly, at 100 to 200 percent a year. But even at this rapid pace, it will take decades for the AM machine market to come close to the size of the machine tool market for metal fabrication and machining.
The majority of those 2,000 machines perform a process called laser melting. This uses a laser between 400 and 1,000 W to fully melt metal powder layer by layer, and it’s delivering parts that are more than 99 percent dense. It’s producing parts made of Ti 6-4, cobalt chrome, INCONEL® alloys, and more.
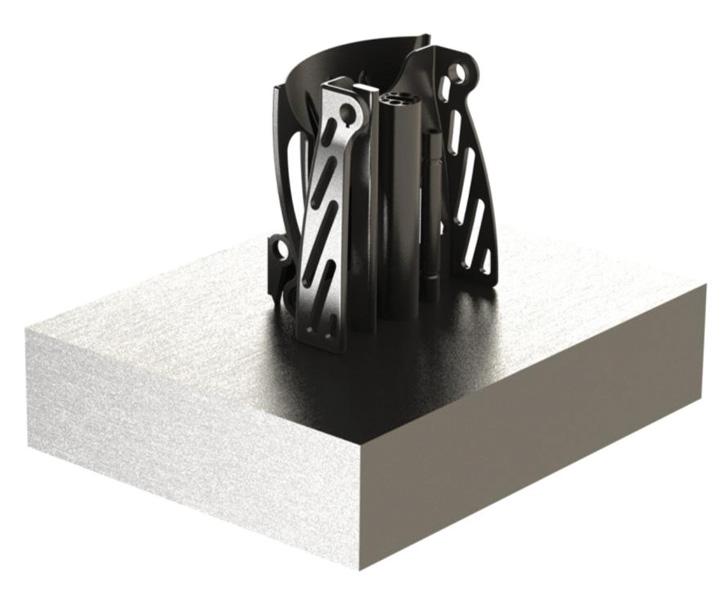
Produced via a laser-melting additive manufacturing process, this seat belt buckle for the aerospace industry is made of Ti 6-4 material. Photo courtesy of EOS , www.eos.info.
Another iteration is laser cladding. Here, a high-energy laser develops a melt pool, and nozzles surrounding the beam direct fine metal powder into the molten pool. It’s a welding operation turned into a part-creation technology. With this approach, most applications don’t make parts from the ground up, but instead add features to an existing part that you really can’t machine, because of its complex geometry or material requirements, like adding titanium or cobalt chrome on top of a less expensive substrate. It also has been used to repair large or expensive parts, many of which would be expensive or impossible to replace.
The electron beam method directs a multikilowatt beam onto a bed and uses powdered metal to build up a part layer by layer. A high-energy process with high throughput (at least by additive manufacturing standards), this technology has been used to build up parts that are then finish-machined down to specifications.
In binder jetting, a system selectively deposits a liquid binding agent to join powdered particles (including metal), and layers of material are then bonded together. The part then is sent to a furnace to burn off the binder and sinter the part. Unlike other technologies, this AM method has been used to make very large parts.
Finally, lamination uses ultrasonic welding to merge layers and create a solid-state weld between layers of metal foil. Once the part is built up, the excess material is milled away to produce the desired part profile and surface tolerance.
Four Pillars
Many elements need to come together for a job to be a good candidate for AM, and most can be categorized into specific areas—think of them as the four pillars of AM. If the job meets just one pillar, AM isn’t for you. If the job meets two pillars, we get into a gray area. If the job meets all four pillars, it really can’t be done without some type of AM technology.
1. Low volume. Because of the throughput available from machines today, most applications involve between 1 and 100 pieces, though a few jobs run as many as 5,000. True, the GE fuel nozzle job calls for 40,000 pieces produced by many machines, a major upfront investment. But again, the complexity of that part (see the second pillar), its internal channels and odd shapes that can be made effectively only with AM, will save airlines billions in fuel costs.
2. High complexity. AM thrives on high complexity and low volume, a rarity for any automated manufacturing process. Ignoring AM, that combination usually calls for manual operations. Many designs that AM produces, such as complex honeycomb structures to save weight and add structural integrity, would be extremely difficult or simply impossible to produce even with manual methods.
A key time driver in AM is the size of the part. The larger the size, the longer it takes to print. That’s why, except for binder jetting, most metal AM processes produce parts from the ground up, or add features to other parts, that are about the size of a softball or smaller. Still, that softball-sized component can have internal channels, a honeycomb structure, or other elements of seemingly limitless complexity.
Complexity also includes the material aspect. Materials literally can be engineered layer by layer—adding strength here, ductility there, all in an effort to fine-tune a material’s physical attributes to match the part’s design intent.
3. High efficiency. With AM you can be building parts within an hour of finalizing designs, all with little direct labor, setup, or contemplation on how to go about making those tricky bits. Certainly, that efficiency translates to time savings, but more important, it creates a path of least resistance. If traditional manufacturing is a project, AM is more akin to a task: Think it, do it; instead of think it, plan it, prepare it, and then do it.
That efficiency allows you to get more done in less time. It also opens the door to doing more work, the kind of work that would be nice to do but there is never enough time. A simple example is fixture-making. Imagine designing a new fixture, making it, and putting it in service in less than a day. Would that efficiency allow you to put more fixtures on the production floor? Odds are that the answer is “absolutely.” That efficiency also gives you a tool to respond quickly to the problems and challenges that crop up throughout the day.
4. Flexibility. AM has no fixed assets—no tooling, no fixturing. What if a design changes? No worries, just change the CAD file, send it to the machine, and print another part. This not only benefits certain parts, but also helps make conventional manufacturing and quality processes more flexible. Why isn’t a robot used to weld this part? Perhaps the fixturing isn’t flexible enough for all the part variation. Why isn’t a robot used to carry that part? Perhaps it’s because part shapes change, and you can’t design an end effector to handle all of the variation. Why does the quality tech spend so much time repositioning a part under an inspection device? Maybe because it’s not cost-effective for him to build a custom fixture for every part that needs to be inspected.
With AM, you may be able to print the fixture or end effector that you need. And in these instances, the components don’t necessarily need to be made out of metal. This opens you up to less expensive AM technology.
Note that reducing time to market isn’t a pillar. When people think about time to market, they make an apples-to-apples comparison with current manufacturing practices. People want the same part characteristics made to the same quality, only faster. AM really can’t help accomplish that; it’s not a faster substitute. Instead, it is a fast alternative.
It can offer something different, which can turn into savings elsewhere in the value chain, be it more design flexibility, fewer manufacturing steps, or $1.5 billion in fuel savings for customers.
About the Author
About the Publication
- Podcasting
- Podcast:
- The Fabricator Podcast
- Published:
- 04/16/2024
- Running Time:
- 63:29
In this episode of The Fabricator Podcast, Caleb Chamberlain, co-founder and CEO of OSH Cut, discusses his company’s...
- Trending Articles
- Industry Events
16th Annual Safety Conference
- April 30 - May 1, 2024
- Elgin,
Pipe and Tube Conference
- May 21 - 22, 2024
- Omaha, NE
World-Class Roll Forming Workshop
- June 5 - 6, 2024
- Louisville, KY
Advanced Laser Application Workshop
- June 25 - 27, 2024
- Novi, MI