- FMA
- The Fabricator
- FABTECH
- Canadian Metalworking
Our Publications
Categories
- Additive Manufacturing
- Aluminum Welding
- Arc Welding
- Assembly and Joining
- Automation and Robotics
- Bending and Forming
- Consumables
- Cutting and Weld Prep
- Electric Vehicles
- En Español
- Finishing
- Hydroforming
- Laser Cutting
- Laser Welding
- Machining
- Manufacturing Software
- Materials Handling
- Metals/Materials
- Oxyfuel Cutting
- Plasma Cutting
- Power Tools
- Punching and Other Holemaking
- Roll Forming
- Safety
- Sawing
- Shearing
- Shop Management
- Testing and Measuring
- Tube and Pipe Fabrication
- Tube and Pipe Production
- Waterjet Cutting
Industry Directory
Webcasts
Podcasts
FAB 40
Advertise
Subscribe
Account Login
Search
Google’s advanced tech lab 3D-prints a mold
A Formlabs 3D printer helped Google validate its design of a wearable, over-molded electronic device.
- By Kip Hanson
- Updated September 23, 2019
- September 24, 2019
- Article
- Additive Manufacturing
To someone needing molded parts pronto, a week is an eternity. This is one reason why 3D printer manufacturer Formlabs Inc. sees a strong call for molds made using stereolithography (SL) technology.
According to Andrew Edman, industry manager for product design, engineering, and manufacturing at Formlabs, SL produces the fine detail and smooth surface finishes needed for plastic injection molding. It’s also known for its ability to produce patterns for investment casting, one of the first uses of the technology.
Edman agreed that speed is swell but identified another, often more important reason to use 3D-printed molds.
“The majority of cases I see are for manufacturing validation,” he said. “A customer might have a part that’s quite finicky to mold, for example, or looking at pulling the trigger on an expensive multicavity tool. Perhaps they’re making a consumer product with a Class A surface finish on all sides of the part, or they want to do mechanical or chemical testing. There are a lot of good reasons for getting your hands on a few dozen parts so you can make sure they’ll perform as planned before you commit to hard tooling.”
In terms of customer-use cases, Edman said most of his are hush-hush, but he did discuss the Google Advanced Technology and Projects lab wanting to validate a product’s design before moving into large-scale production of a wearable, over-molded electronics device.
The solution? Use one of Formlabs’ 3D printers and a high-temp resin to build a temporary mold, thus “bridging the gap between prototype and production, reducing turnaround time for a crucial component by 85 percent while saving over $100,000,” said Edman.
That’s a big wad of cash, for sure, but few companies are the size of Google, nor do they have to validate a mold that might cost more than a yacht. In some cases, Edman pointed out, it might be simpler to just print the parts.
“It’s all a question of your reasons for building a mold and what you’re willing to put up with,” he said. “These are pretty low-cost tools made of relatively inexpensive material, so if you have any sort of production quantities, you could just plan on burning through a handful of printed molds. That said, an increasing number of companies are choosing to go the direct-print route, especially in light of increasingly faster print speeds and the availability of robust, end-use materials.
About the Author
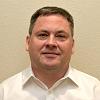
Kip Hanson
About the Publication
- Podcasting
- Podcast:
- The Fabricator Podcast
- Published:
- 04/16/2024
- Running Time:
- 63:29
In this episode of The Fabricator Podcast, Caleb Chamberlain, co-founder and CEO of OSH Cut, discusses his company’s...
- Trending Articles
- Industry Events
16th Annual Safety Conference
- April 30 - May 1, 2024
- Elgin,
Pipe and Tube Conference
- May 21 - 22, 2024
- Omaha, NE
World-Class Roll Forming Workshop
- June 5 - 6, 2024
- Louisville, KY
Advanced Laser Application Workshop
- June 25 - 27, 2024
- Novi, MI