Senior Editor
- FMA
- The Fabricator
- FABTECH
- Canadian Metalworking
Our Publications
Categories
- Additive Manufacturing
- Aluminum Welding
- Arc Welding
- Assembly and Joining
- Automation and Robotics
- Bending and Forming
- Consumables
- Cutting and Weld Prep
- Electric Vehicles
- En Español
- Finishing
- Hydroforming
- Laser Cutting
- Laser Welding
- Machining
- Manufacturing Software
- Materials Handling
- Metals/Materials
- Oxyfuel Cutting
- Plasma Cutting
- Power Tools
- Punching and Other Holemaking
- Roll Forming
- Safety
- Sawing
- Shearing
- Shop Management
- Testing and Measuring
- Tube and Pipe Fabrication
- Tube and Pipe Production
- Waterjet Cutting
Industry Directory
Webcasts
Podcasts
FAB 40
Advertise
Subscribe
Account Login
Search
3-D metal printing meets the office
Fused deposition modeling with metal powders
- By Tim Heston
- June 7, 2018
An FDM-style system prints metal components using powders similar to those developed for metal injection molding.
The plastic and metal sides of the additive manufacturing business seem to live in two economic worlds. The laser- and electron-beam-based metal additive processes, like powder bed fusion and directed energy deposition, tend to focus on high-end precision markets like aerospace, medical, and dental. The plastic side of additive touches not only a variety of businesses but also the consumer and education worlds. My daughter’s middle school has a 3-D printer.
But technology is emerging to bridge the gap.
“This is an office-friendly 3-D printing system.”
So said Larry Lyons, vice president, product, for Desktop Metal, Burlington, Mass., at the RAPID +TCT show in March, pointing to a 3-D printer that looks a little like the one in my daughter’s classroom, only it’s printing metal. It looks like a fused-deposition-modeling printing process, but with an added debinder and furnace, both small enough to be wheeled through an office door. Everything looks like office equipment; there’s nothing industrial about it. The company calls this three-step process—printing, debinding, and sintering—”bound metal deposition.”
Lyons picked up a cartridge of metal powder. “It uses almost the exact same material that the MIM [metal injection molding] industry uses. We process it and load it into cartridge for easy material loading and unloading. And basically, instead of injection molding the material, we’re extruding it through an FDM-style extruder. This FDM-style printer is very common in the plastic world.”
The company also has developed production metal printing systems for the factory floor, based on another process called single-pass jetting. But during the booth tour, my eye kept going back to the office printing system.
I’ve visited many fabricators with small plastic 3-D printers in their engineering offices. They’re great for developing fixtures for inspection, perhaps printing some scale models for large fabrications—good for planning and sales. Customers and shop workers alike can see how their part will fit into a much larger whole.
But what if a shop needed, say, six sheet metal assemblies with a small 6061 aluminum component. For a run of six parts, should the shop go through all the trouble and tie up a vertical mill, outsource it to a local machine shop, or, well, just print it in the front office?
All this is just conjecture, of course. But when you see the new ways metal parts are being created these days, the mind races.
About the Author
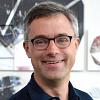
Tim Heston
2135 Point Blvd
Elgin, IL 60123
815-381-1314
Tim Heston, The Fabricator's senior editor, has covered the metal fabrication industry since 1998, starting his career at the American Welding Society's Welding Journal. Since then he has covered the full range of metal fabrication processes, from stamping, bending, and cutting to grinding and polishing. He joined The Fabricator's staff in October 2007.
About the Publication
- Podcasting
- Podcast:
- The Fabricator Podcast
- Published:
- 04/16/2024
- Running Time:
- 63:29
In this episode of The Fabricator Podcast, Caleb Chamberlain, co-founder and CEO of OSH Cut, discusses his company’s...
- Trending Articles
- Industry Events
16th Annual Safety Conference
- April 30 - May 1, 2024
- Elgin,
Pipe and Tube Conference
- May 21 - 22, 2024
- Omaha, NE
World-Class Roll Forming Workshop
- June 5 - 6, 2024
- Louisville, KY
Advanced Laser Application Workshop
- June 25 - 27, 2024
- Novi, MI