Senior Editor
- FMA
- The Fabricator
- FABTECH
- Canadian Metalworking
Our Publications
Categories
- Additive Manufacturing
- Aluminum Welding
- Arc Welding
- Assembly and Joining
- Automation and Robotics
- Bending and Forming
- Consumables
- Cutting and Weld Prep
- Electric Vehicles
- En Español
- Finishing
- Hydroforming
- Laser Cutting
- Laser Welding
- Machining
- Manufacturing Software
- Materials Handling
- Metals/Materials
- Oxyfuel Cutting
- Plasma Cutting
- Power Tools
- Punching and Other Holemaking
- Roll Forming
- Safety
- Sawing
- Shearing
- Shop Management
- Testing and Measuring
- Tube and Pipe Fabrication
- Tube and Pipe Production
- Waterjet Cutting
Industry Directory
Webcasts
Podcasts
FAB 40
Advertise
Subscribe
Account Login
Search
3-D printing, thinking anew, and breaking the rules
Whether printing with plastic or metal, additive manufacturing demands a fresh approach
- By Tim Heston
- UPDATED December 31, 1899
- June 1, 2018
A plastic fixture, printed by 3-D Systems, holds a metal part, on display at RAPID+TCT earlier this year.
Whenever anyone talks about 3-D printing, the first process that comes to many people’s minds is SLA, or stereolithography apparatus. VAT photopolymerization is the generic term for it. A laser (or other light source) passes through a tank full of photopolymer resin and, layer by layer, turns liquid resin into a solid. It’s one of the oldest of the modern-day additive technologies out there.
“And it’s still one of the dominant technologies in 3-D printing today.”
So said Phil Schultz, senior vice president, general manager, on-demand solutions for Rock Hill, S.C.-based 3D Systems, at the RAPID + TCT show earlier this year. Schultz added that the company now offers not just SLA but a portfolio of technologies, including five different plastic additive processes as well as direct-metal additive manufacturing.
3D Systems offers software, design consulting services, and has a service bureau, the additive world’s term for “job shop.” There’s a reason behind the name. Additive isn’t a make-this-part-to-print ("blueprint," that is) business, not by a long shot. Instead, additive is an entirely new way of thinking about building parts, tools, and fixtures, and it requires knowledge of an array of printing methods, not just SLA.
Low-tonnage printed press brake tools, like the ones on display at Cincinnati Incorporated's RAPID+TCT booth, are a prime example. For years brake operators have chosen the closest available die opening to achieve the air-bent radius they need. But what if they could choose the perfect die opening, with no compromises? Bend calculations become more accurate, and setup time plummets, even on older press brakes without advanced controls. Why? Because the tool was engineered exactly for the application.
And yes, this may take more than simply printing a polycarbonate copy of a steel tool. Tonnage and load limits need to be determined. Where will the force be, and how will that force affect the tool’s integrity? Here engineering and software will probably play a vital role. And today, that’s often the “service” of the service bureaus.
New ways of thinking about tool life enter the picture too. What if a printed press brake tool lasts for a few hundred or even just a few dozen bending cycles? Well, what if the tool was printed for the job and, say, traveled with the job traveler? It bends parts perfectly, no marring or scratches, and no need for off-the-shelf urethane tools, either. The printed tool may not last long, but it’s also no trouble to print another one. Twenty years ago no fabricator would have dreamed they could print a bending tool, but now they can, at least for the right applications.
After I described this example to 3D Systems’ Schultz at the RAPID show, he said that the scenario was entirely plausible, not just for bending but for assembly and other tooling and fixturing situations.
“If someone works in a company that’s new to additive [manufacturing], the challenge comes in thinking anew,” Schultz said. “People have been trained for decades to fabricate in a traditional fashion. When going to additive, all those rules are broken.”
About the Author
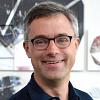
Tim Heston
2135 Point Blvd
Elgin, IL 60123
815-381-1314
Tim Heston, The Fabricator's senior editor, has covered the metal fabrication industry since 1998, starting his career at the American Welding Society's Welding Journal. Since then he has covered the full range of metal fabrication processes, from stamping, bending, and cutting to grinding and polishing. He joined The Fabricator's staff in October 2007.
About the Publication
Related Companies
- Podcasting
- Podcast:
- The Fabricator Podcast
- Published:
- 04/16/2024
- Running Time:
- 63:29
In this episode of The Fabricator Podcast, Caleb Chamberlain, co-founder and CEO of OSH Cut, discusses his company’s...
- Trending Articles
- Industry Events
16th Annual Safety Conference
- April 30 - May 1, 2024
- Elgin,
Pipe and Tube Conference
- May 21 - 22, 2024
- Omaha, NE
World-Class Roll Forming Workshop
- June 5 - 6, 2024
- Louisville, KY
Advanced Laser Application Workshop
- June 25 - 27, 2024
- Novi, MI