Senior Editor
- FMA
- The Fabricator
- FABTECH
- Canadian Metalworking
Our Publications
Categories
- Additive Manufacturing
- Aluminum Welding
- Arc Welding
- Assembly and Joining
- Automation and Robotics
- Bending and Forming
- Consumables
- Cutting and Weld Prep
- Electric Vehicles
- En Español
- Finishing
- Hydroforming
- Laser Cutting
- Laser Welding
- Machining
- Manufacturing Software
- Materials Handling
- Metals/Materials
- Oxyfuel Cutting
- Plasma Cutting
- Power Tools
- Punching and Other Holemaking
- Roll Forming
- Safety
- Sawing
- Shearing
- Shop Management
- Testing and Measuring
- Tube and Pipe Fabrication
- Tube and Pipe Production
- Waterjet Cutting
Industry Directory
Webcasts
Podcasts
FAB 40
Advertise
Subscribe
Account Login
Search
Finite element analysis meets metal additive manufacturing
Can we print it? Sure, but can we simulate the effects of printing it?
- By Tim Heston
- May 31, 2018
A simulation of a heat exchanger component shows displacement and other attributes. Photo courtesy of ANSYS.
Metal fabrication is a broad world, encompassing both traditional sheet metal and structural metal fabrication technologies like laser cutting and press brake bending, as well as high-end processes like laser welding, laser cladding, and electron beam welding.
Those high-end fabricators are a target audience for many of today’s sophisticated 3-D metal printing technologies, including both directed energy deposition and powder bed fusion. In powder bed fusion an electron beam or laser beam fuses metal powders in a powder bed, layer by layer. Once the laser or electron beam fuses one layer, the platen holding the powder moves down, and a new layer of powder is fused on top. In directed energy deposition, a deposition head feeds powder or wire into a laser beam, which builds a part layer by layer. The machines also print supports for the built-up piece to sit on during the printing process. If they’re not part of the design, those supports are usually removed during post-processing.
Powder bed fusion has gained serious footing in industries like medical and dental, serving companies that need many intricate, small parts. Directed energy deposition has been used extensively to repair or refurbish expensive, precise parts.
3-D metal printing is a complex business. “When you’re printing metal, you’re doing metallurgy at the same time as the fabrication.”
So said Rich Baker, chief technology officer of Maple Plain, Minn.-based Proto Labs, an exhibitor at this year’s RAPID +TCT event, which took place in Fort Worth, Texas, in March. Proto Labs performs not only 3-D printing but also machining, plastic injection molding, and sheet metal fabrication.
“Properties in the part depend on where they were made as well as the heat transfer,” Baker said. “That adds complexity.”
Brent Strucker, Ph.D., has devoted much of his career to managing that complexity. As founder of 3DSIM, Strucker developed an approach to finite element analysis that simulates the metal 3-D printing process. “We essentially rethought the approach to finite element analysis,” he said. Instead of looking at the millions (and sometimes billions) of particles being printed individually, “we look for repeated behaviors and patterns, and how it repeats mathematically. This speeds the entire process.”
His company was purchased by ANSYS in 2017, and today Strucker is director of ANSYS’s additive manufacturing business.
“When you get into [metal] additive technologies, you need to know the properties of the part,” Strucker said. “What’s going to happen when form it? How does my process affect the part? Where do I need my supports? Will the metal distort when I cut those supports off after printing? Will we need stress relief, or can I compensate for the distortion? These are the kinds of questions that we now can answer beforehand through simulation.
“Metal parts can cost thousands of dollars each to print. If this part isn’t feasible, that’s a lot of waste,” he continued. “Software can now help eliminate that trial and error.”
Strucker added that software can be used to do cost justifications: that is, should this part really be printed, and what’s the best design to use? Software can now help answer those questions. If an engineer makes a change, he or she can immediately see how that design change will affect the printing process.
In the high-end world of metal additive manufacturing, software may be the key component to jumpstart technology adoption. Everyone knows the potential: Combining different parts into one, having just one inspection process rather than many, shorten overall fabrication time. This all sounds great, but as Strucker explained, combining already complex parts into one highly complex printed part is easier said than done. Moving forward, software simulation (to detect distortion and other issues) and software design aids will perhaps make 3-D metal printing both easier to say and do.
About the Author
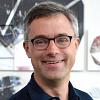
Tim Heston
2135 Point Blvd
Elgin, IL 60123
815-381-1314
Tim Heston, The Fabricator's senior editor, has covered the metal fabrication industry since 1998, starting his career at the American Welding Society's Welding Journal. Since then he has covered the full range of metal fabrication processes, from stamping, bending, and cutting to grinding and polishing. He joined The Fabricator's staff in October 2007.
About the Publication
- Podcasting
- Podcast:
- The Fabricator Podcast
- Published:
- 04/16/2024
- Running Time:
- 63:29
In this episode of The Fabricator Podcast, Caleb Chamberlain, co-founder and CEO of OSH Cut, discusses his company’s...
- Trending Articles
- Industry Events
16th Annual Safety Conference
- April 30 - May 1, 2024
- Elgin,
Pipe and Tube Conference
- May 21 - 22, 2024
- Omaha, NE
World-Class Roll Forming Workshop
- June 5 - 6, 2024
- Louisville, KY
Advanced Laser Application Workshop
- June 25 - 27, 2024
- Novi, MI