Senior Editor
- FMA
- The Fabricator
- FABTECH
- Canadian Metalworking
Our Publications
Categories
- Additive Manufacturing
- Aluminum Welding
- Arc Welding
- Assembly and Joining
- Automation and Robotics
- Bending and Forming
- Consumables
- Cutting and Weld Prep
- Electric Vehicles
- En Español
- Finishing
- Hydroforming
- Laser Cutting
- Laser Welding
- Machining
- Manufacturing Software
- Materials Handling
- Metals/Materials
- Oxyfuel Cutting
- Plasma Cutting
- Power Tools
- Punching and Other Holemaking
- Roll Forming
- Safety
- Sawing
- Shearing
- Shop Management
- Testing and Measuring
- Tube and Pipe Fabrication
- Tube and Pipe Production
- Waterjet Cutting
Industry Directory
Webcasts
Podcasts
FAB 40
Advertise
Subscribe
Account Login
Search
Sheet metal fabrication meets additive manufacturing: Insights from RAPID+TCT
Additive manufacturing's evolution seems to be at an inflection point
- By Tim Heston
- April 27, 2018
This printed V die, on display at Cincinnati Inc.'s booth at RAPID+TCT, air-formed the pictured aluminum part. The die width is customized, designed to air form a specific inside radius. The company said that the concept is still undergoing testing. But the solution could work well for jobs within certain tonnage limits.
Scurrying around the FABTECH® show in November, I ran into the owner of a custom fabricator from the upper Midwest. Her shop has your typical metal fabrication technology: press brakes, laser cutting machines, welding robots. Knowing this, I asked her what she was looking for at the show.
She said she was looking at the latest sheet metal fabrication technology, as usual, but she was also spending some time in the show’s additive pavilion. I asked why. After all, she ran a job shop, not GE or Lockheed Martin. What is a small custom fabricator doing with additive technology?
She told me that she was checking with an additive job shop (or “service bureau,” as they’re known in the additive business) that was printing custom nonmetal tools strong and hard enough to bend short runs of certain sheet metal gauges (mainly thin aluminum) in a press brake. The job couldn’t be formed cost effectively with off-the-shelf brake tooling, and ordering a custom machined tool was too expensive. But printing a tool—well, that was another story.
The shop essentially won the work by thinking differently. Sure, the printed tools weren’t made of tool steel; they were polycarbonate. It’s the kind of 3D printing you see everywhere, even my daughter’s middle school science class, though of course the fabricator’s press brake tools came from industrial grade versions of the technology.
Because of this, the tools certainly don't last long. But they don't need to last. They just need to bend a few hundred parts. When the job comes up again, the shop simply orders more tools to be printed.
Stories like this are what drew me to Fort Worth, Texas, earlier this week, where the RAPID+TCT show took place. Additive manufacturing has evolved into an incredibly dynamic industry, one where industry standards can’t keep up with the release of new technology. ASTM International and other industry partners, including show organizer SME, are working together to accelerate standards development.
It seems everyone in manufacturing, from plastics to machining to sheet metal, has an eye on additive. High-end welding shops, already versed in laser or perhaps even electron beam welding, have their eye on laser- or electron beam-based powder bed fusion and directed-energy-deposition technologies.
Fabricators are looking to additive (both metal and nonmetal) for tools and fixtures, from custom brake punches to special end-effectors for robotics. And they’re looking to additive as a potential technology that could add value to their sheet metal assemblies. Many fabricators have machining departments, and perhaps one day they will have “additive departments.”
At RAPID+TCT earlier this week, I saw literally dozens of booths showing how additive could be used to make unique fixtures, including some poka-yoke fixtures for sheet metal and weldment assemblies. I saw robotic end effectors designed to handle large, awkward parts. Looking at some of them, I imagined such end effectors being printed for use on a robotized press brake cell.
Will shops adopt additive manufacturing quickly? In the recent years, I thought not. I thought it might be a slow evolution. After all, it took decades for this business to adopt the laser as a mainstay technology.
But now, technology in general seems to be moving faster. And if the latest RAPID + TCT show is any indication, the evolution of additive manufacturing seems to be on hyperdrive. With this in mind, we'll be launching The Additive Report, a supplement to The FABRICATOR that will showcase how the fabrication industry is adopting additive manufacturing technology, from the last in metal additive processes to the use of 3-D printing for tools and fixtures. In the years to come additive may touch every corner of manufacturing, metal fabrication included. It's an exciting story, and we'll be there to tell it.
About the Author
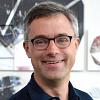
Tim Heston
2135 Point Blvd
Elgin, IL 60123
815-381-1314
Tim Heston, The Fabricator's senior editor, has covered the metal fabrication industry since 1998, starting his career at the American Welding Society's Welding Journal. Since then he has covered the full range of metal fabrication processes, from stamping, bending, and cutting to grinding and polishing. He joined The Fabricator's staff in October 2007.
About the Publication
Related Companies
- Podcasting
- Podcast:
- The Fabricator Podcast
- Published:
- 04/30/2024
- Running Time:
- 53:00
Seth Feldman of Iowa-based Wertzbaugher Services joins The Fabricator Podcast to offer his take as a Gen Zer...
- Trending Articles
- Industry Events
16th Annual Safety Conference
- April 30 - May 1, 2024
- Elgin,
Pipe and Tube Conference
- May 21 - 22, 2024
- Omaha, NE
World-Class Roll Forming Workshop
- June 5 - 6, 2024
- Louisville, KY
Advanced Laser Application Workshop
- June 25 - 27, 2024
- Novi, MI