Senior Editor
- FMA
- The Fabricator
- FABTECH
- Canadian Metalworking
Our Publications
Categories
- Additive Manufacturing
- Aluminum Welding
- Arc Welding
- Assembly and Joining
- Automation and Robotics
- Bending and Forming
- Consumables
- Cutting and Weld Prep
- Electric Vehicles
- En Español
- Finishing
- Hydroforming
- Laser Cutting
- Laser Welding
- Machining
- Manufacturing Software
- Materials Handling
- Metals/Materials
- Oxyfuel Cutting
- Plasma Cutting
- Power Tools
- Punching and Other Holemaking
- Roll Forming
- Safety
- Sawing
- Shearing
- Shop Management
- Testing and Measuring
- Tube and Pipe Fabrication
- Tube and Pipe Production
- Waterjet Cutting
Industry Directory
Webcasts
Podcasts
FAB 40
Advertise
Subscribe
Account Login
Search
Tackling additive manufacturing with an open mind
- By Tim Heston
- September 12, 2018
Kuldeep Agarwa is associate professor at Minnesota State University, Mankato’s department of automotive and manufacturing engineering technology. He is also co-director of the Minnesota Center for Additive Manufacturing.
“In today’s world, why would you ever machine a custom jig or fixture component? Sure, if you have a heat-intensive, harsh environment, you may have no choice. But for 90 percent of the jigs and fixtures out there, which don’t need to endure high temperatures or high stresses, why would you need to machine them?”
So said Kuldeep Agarwal, associate professor at Minnesota State University, Mankato’s department of automotive and manufacturing engineering technology. As co-director of the school’s Minnesota Center for Additive Manufacturing, Agarwal is on a mission to connect local manufacturing businesses—especially small and medium-sized ones—with students and university researchers. The grant-funded center has invested in various 3-D printing machines, from material-extrusion-based fused filament fabrication to direct metal printing that uses technology with materials evolved from powders initially developed for metal injection molding.
Over the years, Agarwal has read the hype about the potential of printing parts instead of machining them, casting them, forging them, or fabricating them—about how 3-D printing will change the world as we know it. That’s all fine, but after years of visiting local manufacturers, including Jones Metal Inc., a custom sheet metal fabricator based in Mankato, he and his students have discovered something different. Shops may not be able to print high-volume parts cost-effectively, but what about components that aid the manufacturing of those parts? They discovered so many areas where additive manufacturing (AM) could help make existing manufacturing methods easier.
Nowhere is this more apparent than in metal jigs and fixturing. In fact, does a fixture really need to be made out of metal? Could it be made out of plastic? If so, could it be printed?
Agarwal emphasized that fabricators shouldn’t fall into the common trap that pervades manufacturing and, for that matter, any situation involving new technology. People tend to focus on extreme cases where a new technology can’t work and then assume the technology won’t work anywhere, period.
“There’s so much ingrained in manufacturing,” he said. “When I visit a shop and I look at a part that will require a custom gauge, people say, ‘Let’s machine it.’ But why? Why do you want to machine it? Just because you’ve been making [custom gauges] that way for 20 years?”
Agarwal conceded that some challenges remain, including material and process certification. In fact, because AM processes are advancing and changing so rapidly, certification becomes a challenge. And it’s difficult for companies and the standards-writing community to keep up, though new processes at the American Society for Testing and Materials (ASTM) and partner organizations are attempting to address the issue.
But again, Agarwal cautioned that this shouldn’t cause fabricators and other manufacturers to dismiss new methods and technologies outright. Just because AM won’t work in some situations doesn’t mean AM won’t work in any situation.
To illustrate, Agarwal described how he and his team worked with Jones Metal to produce a plastic press brake tool set that forms sheet metal to a specific, rather wide radius. They began by seeing if a printed tool set, designed the same way as a steel tool set, would work. New tooling design concepts would come later; the first step was simply to see if printing a press brake tool would work at all.
“This application wasn’t that simple, but it wasn’t extraordinarily complex either,” he said. “It was right in the middle. It proved that it can be done, and that was telling enough.”
Considering the inertia, the “this is the way we’ve always done it” mentality that pervades most businesses, making the first step is perhaps the greatest challenge. Jones Metal and Agarwal’s team looked at AM with an open mind and, rather than look at extreme situations and assume the worst, they tackled an unconventional, but still not overly challenging, bending application. They found success, and now they’re moving forward to build on that success.
About the Author
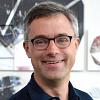
Tim Heston
2135 Point Blvd
Elgin, IL 60123
815-381-1314
Tim Heston, The Fabricator's senior editor, has covered the metal fabrication industry since 1998, starting his career at the American Welding Society's Welding Journal. Since then he has covered the full range of metal fabrication processes, from stamping, bending, and cutting to grinding and polishing. He joined The Fabricator's staff in October 2007.
About the Publication
Related Companies
- Podcasting
- Podcast:
- The Fabricator Podcast
- Published:
- 04/30/2024
- Running Time:
- 53:00
Seth Feldman of Iowa-based Wertzbaugher Services joins The Fabricator Podcast to offer his take as a Gen Zer...
- Trending Articles
- Industry Events
Pipe and Tube Conference
- May 21 - 22, 2024
- Omaha, NE
World-Class Roll Forming Workshop
- June 5 - 6, 2024
- Louisville, KY
Advanced Laser Application Workshop
- June 25 - 27, 2024
- Novi, MI
Precision Press Brake Certificate Course
- July 31 - August 1, 2024
- Elgin,