- FMA
- The Fabricator
- FABTECH
- Canadian Metalworking
Our Publications
Categories
- Additive Manufacturing
- Aluminum Welding
- Arc Welding
- Assembly and Joining
- Automation and Robotics
- Bending and Forming
- Consumables
- Cutting and Weld Prep
- Electric Vehicles
- En Español
- Finishing
- Hydroforming
- Laser Cutting
- Laser Welding
- Machining
- Manufacturing Software
- Materials Handling
- Metals/Materials
- Oxyfuel Cutting
- Plasma Cutting
- Power Tools
- Punching and Other Holemaking
- Roll Forming
- Safety
- Sawing
- Shearing
- Shop Management
- Testing and Measuring
- Tube and Pipe Fabrication
- Tube and Pipe Production
- Waterjet Cutting
Industry Directory
Webcasts
Podcasts
FAB 40
Advertise
Subscribe
Account Login
Search
Oklahoma shop wins aerospace contract to 3D-print Microvanes
- February 5, 2021
- News Release
- Additive Manufacturing
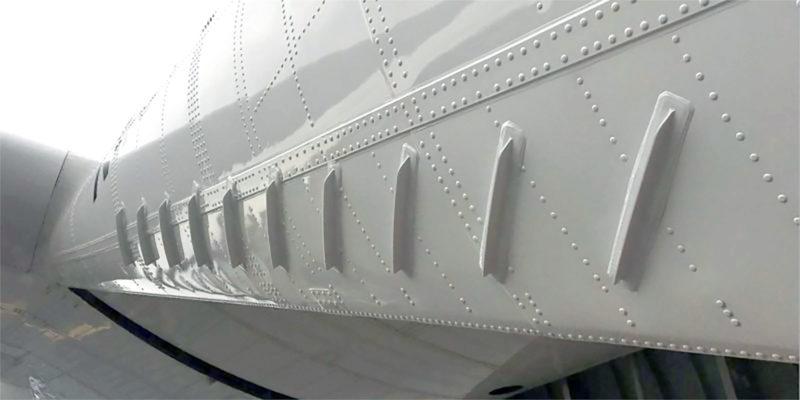
Mircovanes, which Rapid Application Group has been contracted to print using SLS technology for Metro Aerospace, reduce aircraft fuel consumption by up to 4% while reducing carbon emissions. Metro Aerospace
Rapid Application Group has signed an agreement to supply Metro Aerospace with additively manufactured Microvanes, which affix to the exterior of an aircraft’s fuselage to reduce drag and improve fuel efficiency.
“Given the rigorous standards and the extreme operating conditions for the Microvanes, SLS (selective laser sintering) with glass-filled materials [is] the only realistic choice,” said Jason Dickman, the Broken Arrow, Okla., company’s COO. “To meet the rigorous manufacturing requirements, we qualified our sPro 60 HD-HS SLS platforms and Duraform GF materials from 3D Systems, achieving the first article inspection reports and traceability to meet FAA regulations.”
Metro agrees SLS technology was the best choice. “From the start of this as a commercial project in 2017, additive manufacturing was an obvious choice and SLS was the best solution,” said Metro Aerospace Vice President of Business Development Tim Watkins. He added that with low volumes of parts, the cost of injection molding would have driven costs too high.
Microvanes originally were developed and patented by Lockheed Martin. Metro holds the exclusive global license for the production, sale, and distribution of the product. The devices reduce fuel consumption by up to 4% while reducing carbon emissions, engine wear, and operational costs.
- Podcasting
- Podcast:
- The Fabricator Podcast
- Published:
- 04/30/2024
- Running Time:
- 53:00
Seth Feldman of Iowa-based Wertzbaugher Services joins The Fabricator Podcast to offer his take as a Gen Zer...
- Trending Articles
- Industry Events
Pipe and Tube Conference
- May 21 - 22, 2024
- Omaha, NE
World-Class Roll Forming Workshop
- June 5 - 6, 2024
- Louisville, KY
Advanced Laser Application Workshop
- June 25 - 27, 2024
- Novi, MI
Precision Press Brake Certificate Course
- July 31 - August 1, 2024
- Elgin,