Contributing Writer
- FMA
- The Fabricator
- FABTECH
- Canadian Metalworking
Categories
- Additive Manufacturing
- Aluminum Welding
- Arc Welding
- Assembly and Joining
- Automation and Robotics
- Bending and Forming
- Consumables
- Cutting and Weld Prep
- Electric Vehicles
- En Español
- Finishing
- Hydroforming
- Laser Cutting
- Laser Welding
- Machining
- Manufacturing Software
- Materials Handling
- Metals/Materials
- Oxyfuel Cutting
- Plasma Cutting
- Power Tools
- Punching and Other Holemaking
- Roll Forming
- Safety
- Sawing
- Shearing
- Shop Management
- Testing and Measuring
- Tube and Pipe Fabrication
- Tube and Pipe Production
- Waterjet Cutting
Industry Directory
Webcasts
Podcasts
FAB 40
Advertise
Subscribe
Account Login
Search
Consuming plasma consumables too quickly?
Combating premature tip wear
- By Kent Swart
- March 1, 2010
- Article
- Consumables
All plasma systems—whether it's a portable, 30-amp unit or a high-precision, automated system that can cut material up to 6 inches thick at 100 percent duty cycle—use consumables that have an expected life. In high-use environments, the cost of consumables can become considerable over time. Familiarizing yourself with what causes premature consumable wear and how to prevent it can help extend the life of your consumables and, in turn, cut down on the cost of continuous consumable replacement.
Respect the Tip
Plasma tips are designed and machined to very tight tolerances to optimize the pilot and cutting arcs. Anything that alters the physical characteristics of the tip will have a detrimental effect on its performance and parts life.
Most tip problems stem from the blockage or expansion of the tip orifice. Blockage occurs when molten material comes in contact with the tip, most commonly during piercing. If the blockage cools and hardens near the orifice, it could alter the plasma flow, causing poor or degraded cutting capacity. To prevent this, move the torch slightly away from the material after the pilot arc transfers, and then lower it slowly as the piercing-hole gets deeper. This will reduce material buildup on the tip. For manual applications, slightly tilt the torch—off perpendicular to the workpiece—to force material away from the torch tip.
A distorted, enlarged, or out-of-round tip orifice will negatively affect your plasma system's overall performance. Orifice distortion can be attributed to several factors, the most common of which is excessive piloting. This refers to the amount of time the arc is initiated before you transfer it to the workpiece. Excessive piloting will erode the orifice exit, allowing the arc to widen and diffuse prematurely.
Another cause of orifice distortion is improper edge starts. To perform edge starts correctly, you should use a roll-in technique with the torch at a slight angle when the arc is initiated and then cut the top edge of the workpiece first. Once the arc transfers, move the torch to a more perpendicular position along the cutting plane, which will help to ensure that the tip is in the appropriate position when the arc transfers and that the plasma stream flows straight out of the tip orifice.
If, for example, the tip is below the work surface when the pilot is initiated, the arc could transfer and force the plasma stream to the side. This angled flow direction will blow out the tip as the orifice becomes more oval or enlarged. Once the tip suffers this effect, its performance will begin to deteriorate at an alarming rate, and you will need to replace it to regain full cut capacity and performance.
Slowing Tip Wear
Selecting the right tip size will also help your consumables reach their expected life. Most modern plasma systems have operator-selectable amperage output. Cutting thicker material requires higher-amperage consumables and output setting. Switching from thin material to thicker is not as easy as increasing the cutting amperage; you must also ensure that the appropriate consumables are in place to match the application. Using lower-amperage consumables with a higher-amperage setting will cause what's known as an enlarged tip orifice, loss of cut quality and capacity, and part failure. Failing to size the consumable properly to the application will accelerate normal consumable wear.
Excessive heat buildup at the tip also accelerates tip wear. Plasma systems are designed to move gas over the electrode and out of the tip orifice in a swirling motion. This swirling motion allows the plasma stream to be centered around the electrode. This also ensures that the cutting arc exits the tip centered in the orifice. As mentioned earlier, an off-center plasma stream will prematurely wear the tip orifice.
Gas flow through the tip also helps to dissipate heat and prevent excessive buildup. Anything that impedes gas flow through the torch will have a detrimental effect on performance and consumable life. Heat dissipation is an even larger issue with automated systems compared with manual units because amperage levels and duty cycles are much higher. Automated systems use liquid-cooled torches, which should be monitored for proper functioning, as the cost of consumables in these systems is much higher. Coolant should be free of contaminants, filtered properly, and changed on a regular basis to provide proper cooling. (Note: Coolant is a specialized mixture, not simply tap water.)
Most plasma system manufacturers recommend using gases that are dry and clean, because contaminants can reduce efficiencies by clogging critical passageways through the torch. These passageways can be found in tips or swirl rings, but are critical to a plasma system's performance. Using gas that is humid or wet can cause an excessive buildup of contaminants as the water is exposed to excessive heat, becomes vaporized, and leaves deposits on the consumables.
Normally found on the electrode and the interior of the plasma tip, damage caused by moisture first appears on the electrode in a swirl pattern. As operation continues, the electrode can become covered in black deposits, decreasing its level of performance. When this happens, you will need to replace the consumables.
Tips to Remember
- Remember these tips when programming your automated system or running your manual plasma unit. They will help you to extend the life of your consumables and reduce cost.
- Minimize slag buildup by using good piercing techniques.
- Decrease pilot time prior to transfer.
- Use correct edge-start techniques.
- Ensure proper cooling by using clean, dry air and proper gas distribution.
About the Author
Kent Swart
Thermadyne's Thermal Dynamics® brand of plasma systems
16052 Swingley Ridge Road Suite 300
St. Louis, MO 63017
636-728-3000
About the Publication
subscribe now
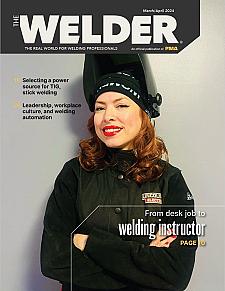
The Welder, formerly known as Practical Welding Today, is a showcase of the real people who make the products we use and work with every day. This magazine has served the welding community in North America well for more than 20 years.
start your free subscription- Stay connected from anywhere
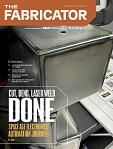
Easily access valuable industry resources now with full access to the digital edition of The Fabricator.
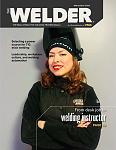
Easily access valuable industry resources now with full access to the digital edition of The Welder.
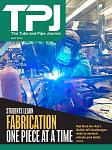
Easily access valuable industry resources now with full access to the digital edition of The Tube and Pipe Journal.
- Podcasting
- Podcast:
- The Fabricator Podcast
- Published:
- 04/30/2024
- Running Time:
- 53:00
Seth Feldman of Iowa-based Wertzbaugher Services joins The Fabricator Podcast to offer his take as a Gen Zer...
- Industry Events
Pipe and Tube Conference
- May 21 - 22, 2024
- Omaha, NE
World-Class Roll Forming Workshop
- June 5 - 6, 2024
- Louisville, KY
Advanced Laser Application Workshop
- June 25 - 27, 2024
- Novi, MI