Senior Editor
- FMA
- The Fabricator
- FABTECH
- Canadian Metalworking
Categories
- Additive Manufacturing
- Aluminum Welding
- Arc Welding
- Assembly and Joining
- Automation and Robotics
- Bending and Forming
- Consumables
- Cutting and Weld Prep
- Electric Vehicles
- En Español
- Finishing
- Hydroforming
- Laser Cutting
- Laser Welding
- Machining
- Manufacturing Software
- Materials Handling
- Metals/Materials
- Oxyfuel Cutting
- Plasma Cutting
- Power Tools
- Punching and Other Holemaking
- Roll Forming
- Safety
- Sawing
- Shearing
- Shop Management
- Testing and Measuring
- Tube and Pipe Fabrication
- Tube and Pipe Production
- Waterjet Cutting
Industry Directory
Webcasts
Podcasts
FAB 40
Advertise
Subscribe
Account Login
Search
A tale of two young sibling welders who defy stereotypes
Minnesota brother and sister embrace hands-on learning metal fabrication offers
- By Tim Heston
- April 10, 2020
- Article
- Arc Welding
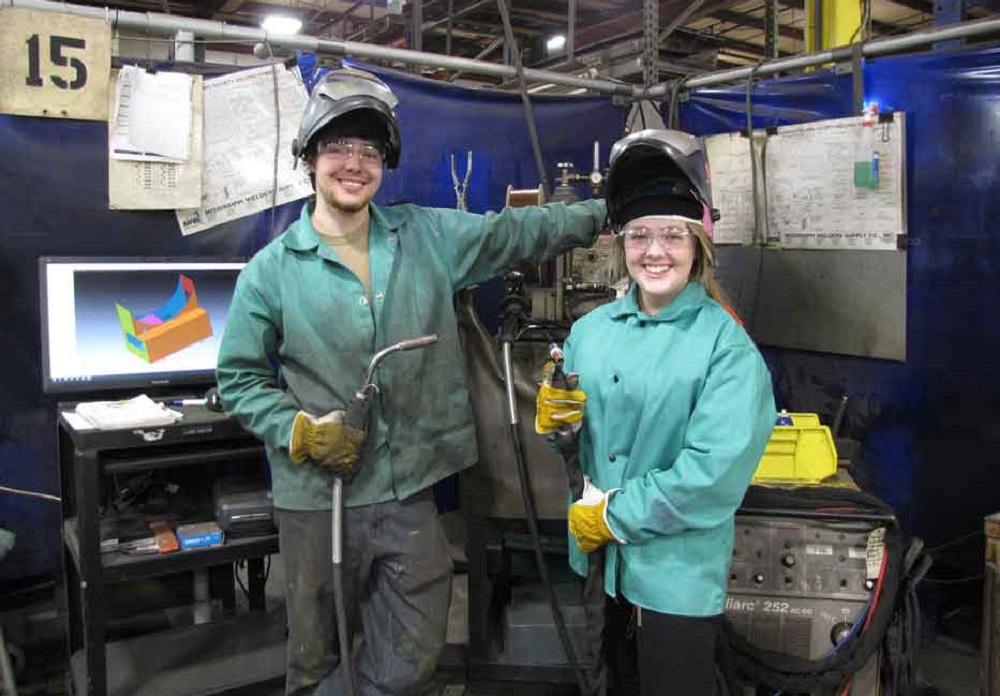
Tom and Lindsey Lawton are just starting their careers in metal fabrication, and they’re not likely to put down the welding torches anytime soon. Images provided
A dozen years ago an 8-year-old boy and his friend rode their bikes around the streets of Mankato, Minn. One rode his bike behind some businesses while the other kept watch. Yes, they were dumpster-diving, but not for anything nefarious, just a bit of scrap metal. Both loved history and epic medieval battles. They had knights to dub, and for that, obviously, they needed swords.
And no, discarded broomsticks wouldn’t do, not with a makeshift forge in the backyard. The two pedaled home with scrap metal in tow, prepped the fire, and began hammering away. The boy’s younger sister watched, entranced, handed over tools, and helped out where she could.
Today that young blacksmith, Tom Lawton, is 20 years old and has just stepped over the threshold into what’s likely to be a long career in metal fabrication. The same could be said for his sister Lindsey. Tom is an up-and-coming welder at Jones Metal Inc., a custom metal fabricator with deep roots in Mankato. Lindsey, a high school senior who turns 18 this year, is already interning at Jones, coming into the shop for a few hours before school. Both have been welding since the ninth grade, and neither is likely to put down the welding torch anytime soon.
The two talk as a team. They’re articulate and engaged, and they often finish each other’s sentences, showing obvious signs of mutual respect—perhaps to the slight disappointment of co-workers. Lindsey laughed. “Yes, sometimes I arrive in the morning and I hear, ‘Hey Lindsey! Time to show up your brother!’ But no. I just laugh. We’re a team.”
During this 50th year of The FABRICATOR magazine and its publisher, the Fabricators & Manufacturers Association International (FMA), we’ve talked to longtime industry veterans, some of whom have been in the industry just about as long as the magazine has. This month we’re talking to two individuals just entering the profession. They weren’t around 50 years ago, but they’re very likely to be around for the magazine’s centennial 50 years from now.
Exposure Makes a Difference
Mankato East High School still has something too many schools don’t: a robust vocational training program. Both Tom and Lindsey took Welding I in ninth grade and Welding II in 10th—that’s right, a full two years of welding in high school.
“Our shop teacher [Dave Evans] was really great,” Tom said. “We were given a broad overview of all the weld processes, including MIG, TIG, and stick, as well as some oxyfuel welding and brazing. And there’s a manual lathe and a plasma cutter. The class sizes were pretty big, about 27 students, but you still get a lot of one-on-one time with the instructor.”
“We didn’t go in-depth,” Lindsey added. “If you were really interested in something, you could get an internship or learn more in technical college. But it’s a very good gateway.”
Tom recalled the first time he struck an arc during his freshman year. “I put the hood down, struck the arc, and started welding. It was just awesome,” adding that the excitement he felt smithing medieval gear in the backyard came rushing back. “I’ve been hooked ever since.”
Lindsey echoed his sentiment. “I remember hearing the buzz, seeing the light, and making a bead. From the first bead I put down, I knew this was something I wanted to do.”
Both have a knack for drawing, carpentry, and art, and Lindsey especially has a keen interest in sculpture, including ceramics. Some art comes to fruition slowly, though, and Lindsey thrives when it doesn’t. “I guess I’m a little impatient. That’s why I love the pottery wheel. I love to watch things come together quickly.” When she struck an arc, she saw things come together very quickly, literally and figuratively.
What if neither were exposed to welding in high school? Would they have chosen a different path? It’s impossible to know. But even if the siblings had never struck an arc until after high school, their desire to build and create probably wouldn’t have abated. Both have been drawn to the building of things, be it through metalworking, carpentry, or anything else, for as long as they can remember.
The two thank their parents, John and Kristi, both educators. John teaches eighth-grade science and Kristi teaches sixth-grade math. “They were very supportive with anything we wanted to pursue, as long as we were safe and didn’t break the rules and get in trouble,” Tom recalled. “They wanted to make sure we could follow any dreams we had”—even if that entailed building a small forge in the backyard.
The siblings conceded that some teachers and guidance counselors tended to encourage the four-year-college track, but their parents didn’t think a four-year degree was an absolute necessity. “They believe in continuing education,” Tom said, “but that doesn’t mean it has to be at a four-year college.”
About Education
The Lawtons come from a teaching family—including their parents and uncles on both sides—and this is perhaps why they feel right at home at Jones Metal. Tom started several years ago at Jones as a welding intern, just as Lindsey is doing now.
“They gave me the initial tour of the entire shop,” Tom said, “but then my focus really was on welding. I would shadow a welder, and he would explain to me what they were doing and why they were doing it. And after a little more training, they had me working. They shadowed me and gave me tips. That feedback gave me the tools for further improvement that I could work on myself. And I wasn’t just welding. I was grinding and straightening, taking weld distortion into account, and welding parts up to customer specifications. It was no longer just about making a weld bead. It was making sure that weld met customer requirements.”
Tom now works full-time as a second-shift welder, and when I spoke to him in February, he had just passed a certification test for one of Jones’ largest customers. He had also completed a welding certificate course at South Central College, a community college with a campus in North Mankato. Down the road he sees himself becoming a certified welding inspector (CWI) and perhaps even a certified welding educator (CWE).
That said, he concedes that he probably wouldn’t have these aspirations if he had a different experience at Jones. Two things make him excited to come to work. One is the variety. He works on a range of projects every day, from the smallest brackets to the largest enclosures. Two, he works in a family-oriented, friendly environment with supportive people who don’t hesitate to share what they know. They’re at Jones to fabricate, but they’re also there to teach. After all, if knowledge isn’t shared, a workplace can become stagnant in a hurry.
Lindsey concurs. Now in the middle of a semester-long welding internship, she arrives at Jones every weekday before school at 7 a.m. “The shop’s clean and well-lit, and I knew right away it would be a great fit. I primarily work with the welding trainer, Jordan Hall, who heads the training program here. He works right alongside me as I weld coupons and try to perfect my technique.
“If he can’t make it in the morning, I get to shadow other welders who are working on actual products. That allows me to ask questions that pertain to a workday at Jones. And that’s interesting to me. I gain insight into what grinding looks like, and what a finished part is supposed to look like. I look at blueprints and can ask questions about those as well.”
About Asking Questions
Asking questions, taking notes, leadership skills—the Lawtons took a certain high school class for all that. It’s called AVID, short for Advancement Via Individual Determination. “It’s basically a college and life-prep class,” Lindsey said. “It teaches you about public speaking and helps you build resumes and gain contacts with people for job-shadowing.”
The class also invites local employers to speak about opportunities and working life in general. One of those speakers happened to be Sarah Richards, president of Jones Metal. A junior in the class was listening.
“She really caught my ear,” Tom said. “She told us about her life and how she got back into the family business. And when I heard she was offering an internship, I jumped on it.”
Tom interned the last semester of his senior year, then was hired on shortly after graduation with an offer that included a paid semester for earning a welding certificate at South Central College, made possible through a training grant from the state of Minnesota. His positive experience eventually spurred Lindsey to take the same internship.
“We went on tours at Jones Metal through our high school welding program,” Lindsey recalled. “And then when I heard a woman was president, and there was a lot of women representation at the company, I felt that was just awesome.”
Lindsey expects to graduate at the end of the school year, and like her brother, her eyes are set on a welding career. The knowledge-sharing and support continue to this day—without, the Lawtons insist, any sibling rivalry whatsoever. Tom paused. “Well, not yet at least.” Laughter all around.
Into the Future
If you consider the Lawtons’ story in isolation, you might not think a skilled labor crisis exists at all. Of course, the Lawtons’ tale isn’t typical, at least not yet. But their story could be a positive harbinger, especially for merit-rewarding operations that embrace knowledge-sharing and support a friendly, family-based atmosphere.
Teaching seems to be in the Lawtons’ DNA. They’re at home in a hands-on-learning environment—a common trait of those who make a career out of metal fabrication. And it’s one that, regardless of what technologies reach the shop floor, isn’t likely to change over the next 50 years.
About the Author
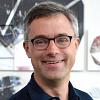
Tim Heston
2135 Point Blvd
Elgin, IL 60123
815-381-1314
Tim Heston, The Fabricator's senior editor, has covered the metal fabrication industry since 1998, starting his career at the American Welding Society's Welding Journal. Since then he has covered the full range of metal fabrication processes, from stamping, bending, and cutting to grinding and polishing. He joined The Fabricator's staff in October 2007.
Related Companies
subscribe now
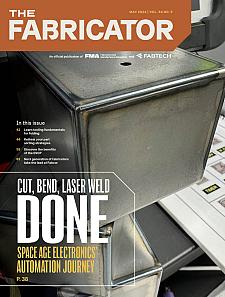
The Fabricator is North America's leading magazine for the metal forming and fabricating industry. The magazine delivers the news, technical articles, and case histories that enable fabricators to do their jobs more efficiently. The Fabricator has served the industry since 1970.
start your free subscription- Stay connected from anywhere
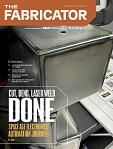
Easily access valuable industry resources now with full access to the digital edition of The Fabricator.
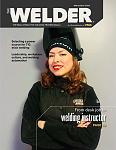
Easily access valuable industry resources now with full access to the digital edition of The Welder.
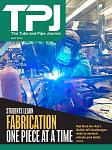
Easily access valuable industry resources now with full access to the digital edition of The Tube and Pipe Journal.
- Podcasting
- Podcast:
- The Fabricator Podcast
- Published:
- 04/30/2024
- Running Time:
- 53:00
Seth Feldman of Iowa-based Wertzbaugher Services joins The Fabricator Podcast to offer his take as a Gen Zer...
- Industry Events
Pipe and Tube Conference
- May 21 - 22, 2024
- Omaha, NE
World-Class Roll Forming Workshop
- June 5 - 6, 2024
- Louisville, KY
Advanced Laser Application Workshop
- June 25 - 27, 2024
- Novi, MI
Precision Press Brake Certificate Course
- July 31 - August 1, 2024
- Elgin,