Editor-in-Chief
- FMA
- The Fabricator
- FABTECH
- Canadian Metalworking
Categories
- Additive Manufacturing
- Aluminum Welding
- Arc Welding
- Assembly and Joining
- Automation and Robotics
- Bending and Forming
- Consumables
- Cutting and Weld Prep
- Electric Vehicles
- En Español
- Finishing
- Hydroforming
- Laser Cutting
- Laser Welding
- Machining
- Manufacturing Software
- Materials Handling
- Metals/Materials
- Oxyfuel Cutting
- Plasma Cutting
- Power Tools
- Punching and Other Holemaking
- Roll Forming
- Safety
- Sawing
- Shearing
- Shop Management
- Testing and Measuring
- Tube and Pipe Fabrication
- Tube and Pipe Production
- Waterjet Cutting
Industry Directory
Webcasts
Podcasts
FAB 40
Advertise
Subscribe
Account Login
Search
A new approach to trailer manufacturing
Adhesives emerge as a replacement for welding, mechanical fasteners
- By Dan Davis
- October 25, 2022
- Article
- Assembly and Joining
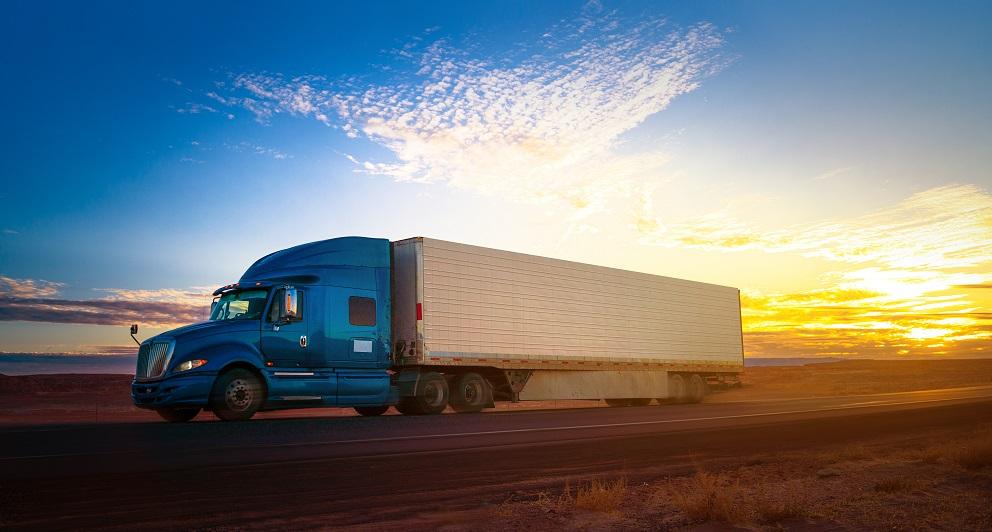
A semitruck and its 53-ft. trailer is a common sight on North American highways. Many drivers that share the roads with these vehicles might be surprised to learn that more trailers are being manufactured using adhesives than mechanical fasteners and welding. THEPALMER/E+/Getty Images
Editor’s Note: The following is loosely based on a Parker Lord webinar entitled “Structural Adhesives for Trailer Manufacturing,” hosted by John Higgins, central regional manager, and Stephen Webb, senior applications engineer. Steve Itoney, Parker Lord’s global market manager, product assembly adhesives, automotive assembly solutions and auto-aftermarket, contributed to this article as well in a follow-up interview.
An average person doesn’t need to be an economist to realize the importance of trailer manufacturers in North America. Semitrucks pulling these 53-ft. trailers on the highways and interstates across the continent help to keep the economy moving along. If the trucks and trailers were to disappear from the roads, life as most know it would stop almost immediately.
As such a vital part of the economy, trailer manufacturing companies invest in research and development to ensure that their products help trucking companies and owner/operators on the road. That has never been more evident than in the last 20 years as these trailer manufacturers have moved away from traditional welding and fasteners to the use of structural adhesives to fabricate trailers.
“The industry has been using sealants for a very long time. Of course, the focus was sealing around rivets and other components,” said John Higgins, central regional manager, Parker Lord. “But with an interest in lightweighting, companies began to look into replacing rivets in the trailers.”
That type of R&D in the 2000s looks prescient now, given the cost of diesel, but those involved in the transportation industry knew what was ahead. No one is ever interested in spending more on fuel, and the desire for society to move away from fossil fuels grows stronger with each generation.
But that proved only to be one motivation as trailer manufacturers recognized the benefits of using structural adhesives. Other ones became evident as they took a closer look at the alternative to welding and mechanical fasteners.
The one that quickly became obvious is that adhesives-based assembly operations cost less than traditional alternatives. For example, welders are skilled workers, if a company can find them, but with that skill comes a higher-per-hour wage than that of a typical assembly worker.
“I might not be able to easily teach a person to weld a stack of dimes like a welder, but I can teach that same person to lay a bead of adhesive in one day,” said Steve Itoney, Parker Lord’s global market manager.
Moving away from welding also takes any need for postweld finishing off the board. Anything that minimizes the amount of manual grinding an employee has to do is a winning idea with both production managers and safety coordinators.
“We worked with a small firetruck manufacturer. After they welded their doors, it took them more than six hours to reduce weld scars to get a nice clean surface,” Higgins said. “After they started bonding their doors, they were a little skeptical of the strength of the doors, but after putting them through impact and rugged testing, they learned that the adhesive would hold up just as well as the weld. And they didn’t have any extra finishing take place. They could take the bonded doors right to the paint process.”
These trailer sections are some of the areas where adhesive bonding is being used in place of mechanical fasteners and welding.
Rivets and huck fasteners also cost more per foot of use when compared to structural adhesives. In general, when these types of mechanical fasteners are used, more people are needed in the assembly process compared to a similar manual application system involving the application of bonding agents.
One more thing that is noteworthy about the use of adhesives and how they can save money is that adhesives both seal and bond—the same material can be used for both functions. If using rivets, the adhesive has to be placed first, and then the rivet installed. That’s extra labor time to perform both functions.
The use of structural adhesives also can dramatically change assembly times. Higgins offered up three examples:
- Roof applications where traditional means of assembly involved multiple operators putting rivets in their place and then having to seal afterwards. The use of structural adhesives reduced the number of workers and process steps to finish the roof assembly.
- Continuous welds in interlocking floor extrusions can be replaced with adhesives, resulting in reduced assembly time.
- Bonded logistic strips and D-rings, used to lock shipped goods in place inside the trailer during delivery, also can be installed more quickly with adhesives than mechanical fasteners.
The use of structural adhesives also opens the door to more design flexibility in trailer manufacturing, according to Higgins. Instead of relying on traditional sheet metal and post construction for the trailers, design engineers can incorporate lighter materials, such as composite walls, which are held in place with the adhesives. Translucent roofs, made from fiberglass-reinforced plastic, can be bonded to upper extrusions and J channels easily with adhesives. Higgins added that the ability to join different types of materials to each other with adhesives opens the door even further when it comes to design choices.
Another benefit to keep in mind when replacing rivets with adhesives in trailer manufacturing is related to aesthetics. Graphics on the side of the trucks are going to look better.
“When you reduce those rivets, it makes it a lot easier and quicker to put the graphics on the side of the trailer. When rivets are present, those people that are applying the graphics on the trailer actually have to cut around the rivets during the application process,” Higgins said.
Real-world Examples
It’s one thing to talk about migrating to adhesives in trailer manufacturing. It’s another to actually see how it works. Here are some examples to provide that real-world perspective.
Roofs. In traditional roof assembly, either translucent fiberglass materials or an aluminum sheet are placed down on the roof. A one-component sealant or a urethane material is applied to the roof posts, and then around the perimeter, after the material is tensioned, there are holes punched or drilled through the material to be filled with rivets. One-component sealants are then used to prevent links around the rivets.
Where using adhesives diverge would be after the one-component sealant has been used at the roof posts, with the translucent fiberglass material or the aluminum sheet, according to Stephen Webb, a Parker Lord senior applications engineer. The roof material is tensioned with minimal fasteners and laid into the J channels. But before that happens, a two-part adhesive is applied all around the perimeter. A second bead is then applied to the top of the roof sheet, and the J channel is forced down into that. A number of clamps are run around the outside of the perimeter to compress the adhesive bead.
“At this point, the adhesive bonding is complete. There is no need to add a sealant,” Webb said. “The steps and the time normally associated with punching the holes and performing the riveting operation is pretty much eliminated.
An overview of where structural adhesives are used in a roof application on a 53-ft. trailer is shown.
“This is one of those areas using the adhesives in the roof bonding that not only means a time savings for the manufacturer, but also a cost savings. And that’s not even mentioning the savings relative to worker injuries related to repetitive motions and high-decibel noise.”
Trailer Noses. The trailer nose is a part of the trailer that is exposed to the elements head-on as the semitruck drives down the highway. Even with the level of forces levied at this area of the trailer, structural adhesives can be used here as well.
Where can two-component adhesives be used to replace mechanical fasteners, sealants, or combinations of both? These are the front nose quarter round, which is typically made of aluminum or polished stainless steel; the stainless steel sheet that encloses the front end of the cap or the composite plates themselves, which likely are shiplap bonded; the upper and lower extrusions; and the corner caps, whether they are plastic or a casting. In all of these areas, extensive testing is done with trailer manufacturers to ensure that adhesives are suitable for the job.
Sidewalls. When it comes to the use of structural adhesives for sidewalls, the focus of this discussion will be on composite sidewalls, which are assembled in a shiplap manner. This is not the typical aluminum or painted steel that is applied to a Z-post construction. These composite sidewalls, which are marketed under various trade names, are basically two sheets of prepainted steel with a composite core, usually polyethylene or polypropylene.
Where the two sheets of composite sidewalls overlap during assembly is called the shiplap. This is typically assembled in an offline assembly area before they are completed and brought back to the main assembly line. This allows for the adhesive to be applied efficiently, giving it a short amount of time to cure so that it is strong enough for the final assembly process.
Upper and lower extrusions in the sidewalls can be bonded, or a minimal number of rivets can be used in conjunction with adhesives. If the trailer manufacturer isn’t ready to go this route yet, then the traditional rivets can be used with the adhesives.
“Some of these trailer manufacturing companies have a portion of their customer base that, even though the trailers are improved by bonding and enjoy all of the other associated benefits, still want to see the rivets,” Higgins said. “They like them. Some of them actually call them ‘rhinestones.’”
Reefer Floors. The trailer floor is another area where adhesives can be used. In the case of reefer floors, bonding can actually replace welding.
In these reefer floor applications, the trailer manufacturer needs a continuous seal between the aluminum extrusions that are joined together to create the trailer floor. The seal keeps the road grime out of the trailer and any moisture inside of the trailer from escaping to the road, which might occur in a refrigerated trailer.
These reefer floors usually are made from aluminum extrusions that are interlocked and then welded together on a large gang welding machine. The process to fabricate these floors is long, and quality issues often arise on these large gang welders as the machines will skip certain areas during the joining process, leading to rework, Webb said.
The front end of a trailer endures a lot of abuse over a trailer’s lifetime, but structural adhesives remain a viable alternative to traditional joining methods in fabricating these key trailer segments.
These types of reefer floors can be fabricated with two-part adhesives that can stand up to both the outside elements and the interior cargo. The adhesives join the aluminum extrusions together and provide a sealant function in one application.
Increasing Applications
It should be noted that the use of structural adhesives is not just limited to 53-ft. trailers. They are being used in manufacturing of cargo and box trucks and even fifth-wheel animal trailers. Successes achieved in one area of the transportation industry often can be applied to other areas, which helps to expand the use of adhesives in these types of applications.
R&D into adhesives continues as well. As more people look to adopt bonding as a replacement for mechanical fasteners or welding, their expectations drive improved adhesive performance.
“One of the main reasons why people specify structural adhesives for trailers is fatigue resistance,” Higgins said. “You get a lot of vibration with trailers as they roll down the road. So, a lot of research has gone into developing not only strong, but flexible adhesives. That’s where these newer-generation materials really stand out.”
This push for innovation is likely to increase as the transportation industry embraces the electrification trend. Higgins said that new engineers are flocking to these tech startups, particularly those focusing on final-mile delivery vans, like Amazon vehicles for example, and the engineers are entering the field with a fresh mindset when it comes to manufacturing. They aren’t wed to the ways things were done for the past 50 years.
For those metal fabricators reading this and wondering about the inevitable rework, Higgins said that repair guides have been developed for all these trailer applications. The guides walk the manufacturer through the steps, perhaps involving heating up the part and then cutting out the adhesive seam with a vibrating knife tool.
About the Author
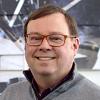
Dan Davis
2135 Point Blvd.
Elgin, IL 60123
815-227-8281
Dan Davis is editor-in-chief of The Fabricator, the industry's most widely circulated metal fabricating magazine, and its sister publications, The Tube & Pipe Journal and The Welder. He has been with the publications since April 2002.
subscribe now
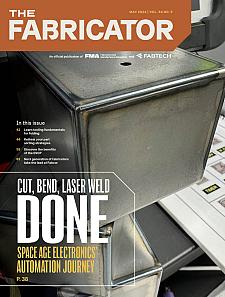
The Fabricator is North America's leading magazine for the metal forming and fabricating industry. The magazine delivers the news, technical articles, and case histories that enable fabricators to do their jobs more efficiently. The Fabricator has served the industry since 1970.
start your free subscription- Stay connected from anywhere
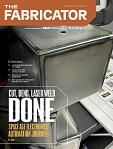
Easily access valuable industry resources now with full access to the digital edition of The Fabricator.
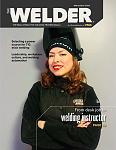
Easily access valuable industry resources now with full access to the digital edition of The Welder.
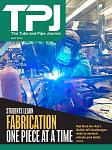
Easily access valuable industry resources now with full access to the digital edition of The Tube and Pipe Journal.
- Podcasting
- Podcast:
- The Fabricator Podcast
- Published:
- 04/16/2024
- Running Time:
- 63:29
In this episode of The Fabricator Podcast, Caleb Chamberlain, co-founder and CEO of OSH Cut, discusses his company’s...
- Trending Articles
Tips for creating sheet metal tubes with perforations
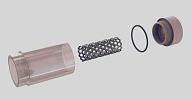
Supporting the metal fabricating industry through FMA
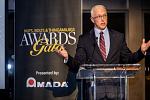
JM Steel triples capacity for solar energy projects at Pennsylvania facility
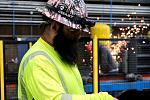
Fabricating favorite childhood memories
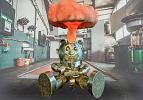
Omco Solar opens second Alabama manufacturing facility
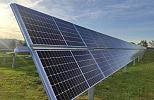
- Industry Events
16th Annual Safety Conference
- April 30 - May 1, 2024
- Elgin,
Pipe and Tube Conference
- May 21 - 22, 2024
- Omaha, NE
World-Class Roll Forming Workshop
- June 5 - 6, 2024
- Louisville, KY
Advanced Laser Application Workshop
- June 25 - 27, 2024
- Novi, MI