Editor-in-Chief
- FMA
- The Fabricator
- FABTECH
- Canadian Metalworking
Categories
- Additive Manufacturing
- Aluminum Welding
- Arc Welding
- Assembly and Joining
- Automation and Robotics
- Bending and Forming
- Consumables
- Cutting and Weld Prep
- Electric Vehicles
- En Español
- Finishing
- Hydroforming
- Laser Cutting
- Laser Welding
- Machining
- Manufacturing Software
- Materials Handling
- Metals/Materials
- Oxyfuel Cutting
- Plasma Cutting
- Power Tools
- Punching and Other Holemaking
- Roll Forming
- Safety
- Sawing
- Shearing
- Shop Management
- Testing and Measuring
- Tube and Pipe Fabrication
- Tube and Pipe Production
- Waterjet Cutting
Industry Directory
Webcasts
Podcasts
FAB 40
Advertise
Subscribe
Account Login
Search
A tale of two worlds in one shop
Electronics assembly and metal fabricating make for a unique value-added offering
- By Dan Davis
- June 13, 2012
- Article
- Assembly and Joining
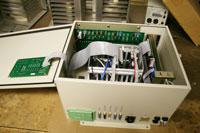
Figure 1: Vista Manufacturing Co. not only fabricates this box and some of the plate parts inside of it, but also makes five of the printed circuit board assemblies that go into it.
Sometimes it pays for metal fabricators to think inside the box—electrical enclosures, to be precise.
The production of National Electrical Manufacturers Association-rated boxes and similar enclosures are the bread-and-butter jobs for numerous fabricators. They cut the blank, bend it into a box, and weld it up so efficiently that some of the workers probably can do the job blindfolded.
But what about the components inside the box? Most shops aren’t involved in that. A few, meanwhile, have jumped into the electronics assembly, where they pull the parts together and assemble the final box before it’s shipped to the customer. And a select few actually make some of the electronic components that are put into the enclosure.
Vista Manufacturing Co., Kansas City, Kan., has been a turnkey electronics assembler (see Figure 1)—with manufacturing capabilities—and metal fabricator for more than 40 years. The company was a value-added manufacturer before adding “value” to simple metal fabrications became cool.
A Little History
It wouldn’t be fair to describe how Vista became this doubly talented shop without saying that the company actually had its own product lines during the early days of the business. One of the partners was a talented electrical engineer who created items such as a nondirectional beacon for small airports that don’t have a large air traffic control tower. The company still gets calls from transportation officials from South Dakota to South America looking for technical support.
That really is the basis for how Vista established its electronics manufacturing capabilities. This tale of two manufacturing worlds actually goes a little farther back on the metal fabricating side.
The Gredell family (see Figure 2), who are now full owners of the company but have been part owners from the very beginning, arguably have metalworking in their blood. Genealogical research suggests that many members of the family were machinists in the early 20th century, according to Becky Gredell, who oversees administrative functions and manages the electronics side of the business.
“My grandfather actually worked for Standard Steel Works, and he had lots of patents and designs on the first tanker-type trucks. That’s where they just didn’t set a tank on top of a frame, they engineered the tank into the frame,” said Andy Gredell, Vista’s general manager for the metal fabricating business.
Dick Gredell, the father of Andy, Becky, and Dennis, who works in metal fabricating, became one of two owners of the business in the early 1980s. That’s when they sold off the remaining electronic product lines and focused more on the contract manufacturing activities.
The current generation of Gredells became involved in the business in the 1990s, working periodically during their high school and college years. Andy and Becky came back in 2000 as “management in training,” according to Becky, joining their brother Dennis who had been working on the shop floor for several years.
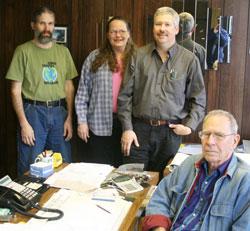
Figure 2: The Gredell family is the force behind Vista’s two-pronged manufacturing operations. (From left) Dennis oversees the punching operations; Becky handles the electronics side of the company; Andy manages the metal fabricating business; and Dick still keeps an eye on things. The 89-year-old fabricator retired earlier this year.
Today Vista is doing similar type of work in the 27,000-sq.-ft., three-story building that it was doing 30 years ago. The big change is that manufacturing processes are a lot more productive.
“There were times when things were more labor-intensive, and at that time, we had about 50 employees working here,” Becky said.
The company has about 25 employees now. Six employees work on the electronics side and the rest in metalworking. Occasionally some of the employees from both sides of the business come together on the third floor and help out with mechanical assembly projects that pull together electronics and metal parts.
Becky estimated that almost 75 percent of Vista’s $2 million business comes from metal fabricating. However, the electronics manufacturing and assembly, although a smaller part of the overall business, remains important because some of the electronics work actually requires contributions from the metal shop.
Different but the Same
Even though the business, with its full-blown electronics capabilities, is not your typical metal fabricating operation, Vista does share a lot of similarities with its peers, like focusing on the basics.
Quality. Becky said that the company has never really advertised, except for the annual Yellow Pages ad. Customers keep coming back and often refer other companies to Vista. For that type of word-of-mouth promotion to work, the company has to be committed to producing quality parts.
“As I like to explain it, the person that does the next operation, part of their job is to check what the last person did. They have to keep their eyes open for something that is not right,” she said.
“Quality control is not about placing blame. It’s trying to keep it from happening again. If we have problems, we go back and see what happened. How can we keep it from repeating? Not necessarily saying that you screwed up.”
Becky admitted that she didn’t know a lot about electronics manufacturing until she jumped into the business after a leadership change in the department. “So I threw myself into it for a couple of years and picked up a whole hell of a lot,” she said.
She actually applied what she learned working on the metals side of the business during those summers of her youth: Document how things should be done. Ensure that they are done correctly. When a problem occurs, find the cause of the problem and enact corrective action so it doesn’t happen again. In the end, it was all about understanding the manufacturing flow and how to keep it running (see Figure 3).
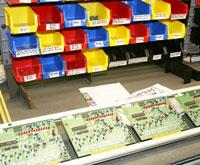
Figure 3: This type of manufacturing line, where electrical parts are placed on a printed circuit board, might look foreign to a fabricator, but the same principles apply: Follow the instructions in terms of placement, work safely and efficiently, and test the product to ensure it meets customer specs. Although Vista is not ISO-certified, Becky Gredell said the company’s documentation and quality practices most likely would meet those types of guidelines.
Equipment. Of course, electronics assembly equipment (see Figure 4) is going to be different than metal fabricating equipment, but it still has to be precise. It operates using the same CNC principles as the metal fabricating equipment, like the company’s Trumatic 260A punching press (see Figure 5) from TRUMPF.
Electronics assembly and metal fabricating equipment is also expensive. It’s not like picking up another welding power source at the industrial supply store one afternoon. A lot more paperwork is required.
Employees. “The main challenge is finding skilled people that we can train to do things, so we can do more managing,” Andy Gredell said.
That’s a common refrain from people in all aspects of manufacturing. Talent tailored to job openings is not readily available.
Still Different, However
Before the argument can be made that a metal fabricator can jump into electronics assembly with good-quality systems, equipment, and talent, the reality of the situation needs to be further explored. There’s a reason more companies don’t jump into the electronics manufacturing services arena.
New Technology. The machines involved in electronics assembly might be based on CNC principles, but they are totally different from the punching and laser cutting machines that are ubiquitous in shops today. Pick-and-place machines, reflow ovens, deionized wash systems, and wave soldering equipment not only sound foreign to a metal fabricator, but they also require an extensive learning curve.
Becky stressed that, with the ever increasingly complex equipment in the marketplace, operators must be technically skilled and display a willingness to learn.
Lead-Times. This is where the world has completely turned upside down in electronics assembly. Vista typically quotes a four-week delivery time for electronic components, but that is valid only if it can get the parts it needs. The recession forced everyone to look at their own operations and free up cash anywhere they could, and for many that meant eliminating excess inventory. The electronic parts that were once readily available are increasingly at risk of being out of stock.
“If it’s not a mover, the distributors don’t want to carry it,” Becky said.
The complexity of the electronic assemblies exacerbates the situation. Working with so many small components, the assembler needs to be very organized to stay on top of the assembly process. A bill of materials for a simple metal fabricated part looks likes a short grocery list for an evening meal in comparison.
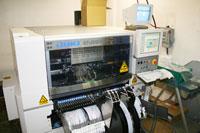
Figure 4: This Juki 2060RL pick-and-place machine is not something seen on a lot of metal fabricating shop floors. It’s used to place surface mount technology components on printed circuit boards.
For its regular customers, Vista will keep some hard-to-get parts, such as a trimmer capacitor, in inventory so that the orders can be delivered within expected windows. But that’s not always possible.
Even with the talk of electronics assembly and metal fabricating, the business still boils down to personal relationships. After all, people are getting on the phone or sending an e-mail to place an order. Manufacturing productivity has improved greatly over the years, but people are still an integral part of any operation.
“I know that people think the Internet is going to change all of that, but I don’t think that’s going to happen in the long run,” Becky said.
Who would have thought an old-school approach could work so well in the “new” era of doing business? Maybe that’s the type of out-of-the-box thinking that keeps the customers coming back to Vista.
About the Author
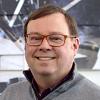
Dan Davis
2135 Point Blvd.
Elgin, IL 60123
815-227-8281
Dan Davis is editor-in-chief of The Fabricator, the industry's most widely circulated metal fabricating magazine, and its sister publications, The Tube & Pipe Journal and The Welder. He has been with the publications since April 2002.
subscribe now
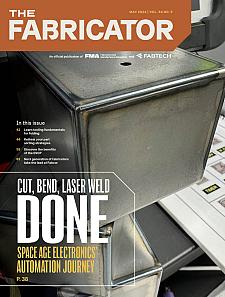
The Fabricator is North America's leading magazine for the metal forming and fabricating industry. The magazine delivers the news, technical articles, and case histories that enable fabricators to do their jobs more efficiently. The Fabricator has served the industry since 1970.
start your free subscription- Stay connected from anywhere
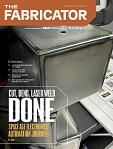
Easily access valuable industry resources now with full access to the digital edition of The Fabricator.
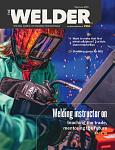
Easily access valuable industry resources now with full access to the digital edition of The Welder.
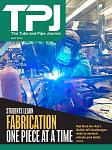
Easily access valuable industry resources now with full access to the digital edition of The Tube and Pipe Journal.
- Podcasting
- Podcast:
- The Fabricator Podcast
- Published:
- 05/14/2024
- Running Time:
- 62:12
Cameron Adams of Laser Precision, a contract metal fabricator in the Chicago area, joins the podcast to talk...
- Trending Articles
White House considers China tariff increases on materials
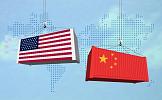
A visit to Automate 2024 reveals the future might be now
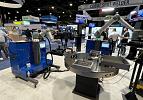
Majestic Steel Arkansas fully operational
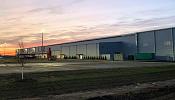
Why employee-owned companies make sense in manufacturing
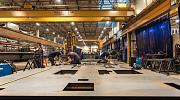
Rivian to expand Illinois facility to manufacture midsized SUV
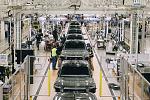
- Industry Events
Laser Welding Certificate Course
- May 7 - August 6, 2024
- Farmington Hills, IL
World-Class Roll Forming Workshop
- June 5 - 6, 2024
- Louisville, KY
Advanced Laser Application Workshop
- June 25 - 27, 2024
- Novi, MI
Precision Press Brake Certificate Course
- July 31 - August 1, 2024
- Elgin,