Senior Editor
- FMA
- The Fabricator
- FABTECH
- Canadian Metalworking
Categories
- Additive Manufacturing
- Aluminum Welding
- Arc Welding
- Assembly and Joining
- Automation and Robotics
- Bending and Forming
- Consumables
- Cutting and Weld Prep
- Electric Vehicles
- En Español
- Finishing
- Hydroforming
- Laser Cutting
- Laser Welding
- Machining
- Manufacturing Software
- Materials Handling
- Metals/Materials
- Oxyfuel Cutting
- Plasma Cutting
- Power Tools
- Punching and Other Holemaking
- Roll Forming
- Safety
- Sawing
- Shearing
- Shop Management
- Testing and Measuring
- Tube and Pipe Fabrication
- Tube and Pipe Production
- Waterjet Cutting
Industry Directory
Webcasts
Podcasts
FAB 40
Advertise
Subscribe
Account Login
Search
Amada America celebrates 50 years
As demand for machines reaches record highs, Carolina Technical Center opens its doors
- By Tim Heston
- November 9, 2021
- Article
- Automation and Robotics
One late October afternoon, a crowd of owners and managers in metal fabrication walked under the awning at Amada America’s new Carolina Technical Center in High Point, N.C., adjacent to the company’s Carolina Manufacturing Facility. As the technical center’s glass doors slid open quietly, a flatbed truck roared by. Another truck had departed that morning, and one more would depart later that afternoon. All were fully loaded with newly manufactured press brakes.
“In my 43 years with the company, this is the busiest I’ve ever seen it.”
So said Mike Guerin, CEO of Amada America, at an Oct. 28 event celebrating Amada’s 50 years in the U.S. and (belatedly) the opening of the Carolina Technical Center. Completed in September 2020, the center has hosted more than 300 virtual customer visits over the past year as well as a number of in-person meetings.
These include Amada’s new Bending Academy classes. Different from equipment-specific training, “the bending academy focuses on making press brake operators,” said Matthew Adkinson, technical center general manager, adding that classes are kept small, each with only a handful of students. “We’ve had almost 30 classes already, and almost 100 people have been trained through the academy thus far.”
Amada’s North Carolina campus, including the manufacturing plant next door, which produces press brakes and laser cutting automation equipment, has remained open since the first machines were produced in December 2019.
“We were deemed an essential business during the pandemic,” Guerin said, “so we just kept rolling. By the end of October, [the North Carolina manufacturing plant] will have produced more than 400 units.”
Amada America’s roots go back to 1971, when its Japanese parent company opened a small R&D office in Seattle. Today the company has more than 1 million sq. ft. of under-roof real estate in the U.S., including three manufacturing plants.
“Here’s another number to think about,” Guerin said. “We have had more than 16,000 customers over 50 years … The tale of our company is the tale of our customers.”
Shortly after Guerin’s comments, one of those customers made his way to the stage for a voice-of-the-customer interview: Perry Jones, director of engineering at Anord Mardix USA, a manufacturer of low-voltage power distribution products. Its plant outside Richmond, Va., is the U.S. operation of a company based in Ireland with additional plants in the U.K., where recent changes reflect broader trends in manufacturing: to produce more in less space. “In the U.K, they consolidated from nine separate facilities down to five,” Jones said, “but they’ve also increased overall manufacturing capacity by about a third.”
Considering the lack of available labor combined with the need for higher throughput, fabricators like Anord Mardix having been shifting their capex strategies. Manual operation just isn’t an option anymore. “We are looking to add automation to our existing equipment,” Jones said, “and we’re not evaluating any new machinery that doesn’t include automation.”
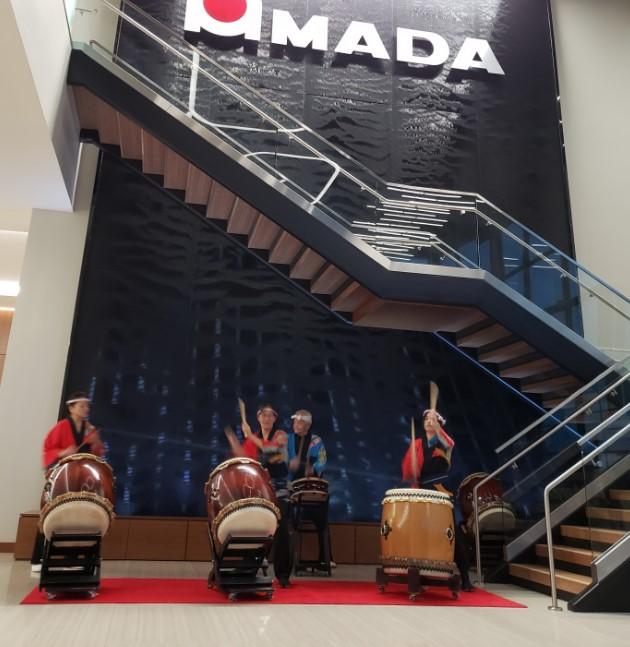
A Japanese drum ensemble performs in the Carolina Technical Center atrium during Amada America’s 50th anniversary celebration.
Still, the automation needs to be flexible, capable of handling both volume and high-product-mix production. “Although the shells [enclosures] around our equipment are produced in high volumes, we have many adaptations we need to make on the inside,” Jones said, adding that the company’s expanding forming capability is designed around this product mix. Specifically, the plant sends small lots of interior components through an Amada automatic-tool-change brake, then forms its higher-volume shells on the traditional brake, also from Amada.
That product mix exemplifies the nature of modern manufacturing: Fabricators need both flexibility and throughput, and Anord Mardix’s rapid growth shows what happens when a manufacturer achieves both. The company began its U.S. operations just seven years ago. In 2015 it opened 50,000 sq. ft. of manufacturing space and in spring 2021, just six years later, it expanded again to a 248,000-sq.-ft. plant.
Such rapid growth hints at just how robust the manufacturing sector is in 2021—and why so many press brakes left Amada’s High Point manufacturing plant on just one late-October day.
About the Author
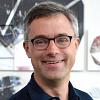
Tim Heston
2135 Point Blvd
Elgin, IL 60123
815-381-1314
Tim Heston, The Fabricator's senior editor, has covered the metal fabrication industry since 1998, starting his career at the American Welding Society's Welding Journal. Since then he has covered the full range of metal fabrication processes, from stamping, bending, and cutting to grinding and polishing. He joined The Fabricator's staff in October 2007.
Related Companies
subscribe now
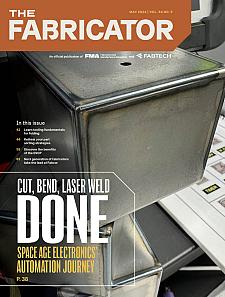
The Fabricator is North America's leading magazine for the metal forming and fabricating industry. The magazine delivers the news, technical articles, and case histories that enable fabricators to do their jobs more efficiently. The Fabricator has served the industry since 1970.
start your free subscription- Stay connected from anywhere
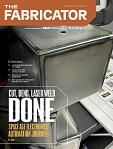
Easily access valuable industry resources now with full access to the digital edition of The Fabricator.
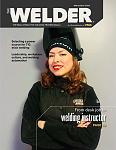
Easily access valuable industry resources now with full access to the digital edition of The Welder.
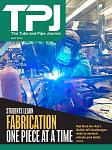
Easily access valuable industry resources now with full access to the digital edition of The Tube and Pipe Journal.
- Podcasting
- Podcast:
- The Fabricator Podcast
- Published:
- 04/16/2024
- Running Time:
- 63:29
In this episode of The Fabricator Podcast, Caleb Chamberlain, co-founder and CEO of OSH Cut, discusses his company’s...
- Trending Articles
Tips for creating sheet metal tubes with perforations
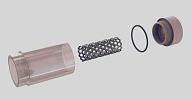
Supporting the metal fabricating industry through FMA
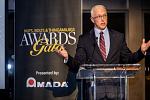
JM Steel triples capacity for solar energy projects at Pennsylvania facility
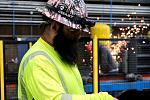
Fabricating favorite childhood memories
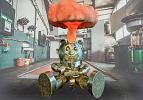
Omco Solar opens second Alabama manufacturing facility
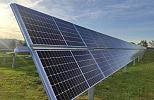
- Industry Events
16th Annual Safety Conference
- April 30 - May 1, 2024
- Elgin,
Pipe and Tube Conference
- May 21 - 22, 2024
- Omaha, NE
World-Class Roll Forming Workshop
- June 5 - 6, 2024
- Louisville, KY
Advanced Laser Application Workshop
- June 25 - 27, 2024
- Novi, MI