Editor-in-Chief
- FMA
- The Fabricator
- FABTECH
- Canadian Metalworking
Categories
- Additive Manufacturing
- Aluminum Welding
- Arc Welding
- Assembly and Joining
- Automation and Robotics
- Bending and Forming
- Consumables
- Cutting and Weld Prep
- Electric Vehicles
- En Español
- Finishing
- Hydroforming
- Laser Cutting
- Laser Welding
- Machining
- Manufacturing Software
- Materials Handling
- Metals/Materials
- Oxyfuel Cutting
- Plasma Cutting
- Power Tools
- Punching and Other Holemaking
- Roll Forming
- Safety
- Sawing
- Shearing
- Shop Management
- Testing and Measuring
- Tube and Pipe Fabrication
- Tube and Pipe Production
- Waterjet Cutting
Industry Directory
Webcasts
Podcasts
FAB 40
Advertise
Subscribe
Account Login
Search
Automated fitting and welding becomes reality for Prospect Steel
Prospect Steel achieves new levels of productivity with recent capital equipment investment
- By Dan Davis
- Updated May 8, 2023
- April 5, 2018
- Article
- Automation and Robotics

Figure 1
Prospect Steel officials report that the steel beam assembly line took about four weeks to get up and running and another two weeks before it was operating in full production.
John Bailey, president of Little Rock, Ark.-based Prospect Steel, shakes his head when asked about hiring welders from off the street. His frustration is evident.
“We have welders come in that claim to have all of this experience and can do a variety of things, but before we give them an application, we ask them to answer a question, ‘How many sixteenths are in an inch?’ You’d be surprised how many can’t answer that question,” he said. “When they can’t, we’ll decide to go in a different direction.”
Of course, this structural steel fabricator isn’t alone as other manufacturing companies are experiencing the same frustrations looking for new talent to replace the skilled tradesmen that are headed for retirement. The American Welding Society predicts a shortage of over 200,000 skilled welding professionals by 2020 and that number is expected to grow rapidly in the years after. The situation is exacerbated for Prospect Steel, which has to contend with a tight labor market (Little Rock’s unemployment rate dropped to 3.5 percent in December 2017, according to the Federal Reserve Bank of St. Louis) and a community filled with large manufacturing companies, such as Caterpillar, LM Wind Power, and Weldspun Tubular, which are hungry for skilled workers.
Prospect Steel, which employs about 60 welders, also consistently is looking to find others skilled in fitting and detailing. They are in short supply as well.
It has not been shy about investing in new technology to boost productivity and quality in the face of the talent gap. For the last 10 years, the company has been using 3-D building information models to help create part drawings and power CNC equipment, such as burning tables and drilling lines. Prospect Steel, which has another location in Blytheville, Ark., also invested in a couple of PeddiWriter plasma marking systems about five years ago to automate the detailing work that used to take experienced individuals with soap stones and tape measures hours to do.
In his 18 years with the company, Bailey was constantly looking for ways to boost productivity on the shop floor. In particular, he was looking for the one technological development that no one could figure out: assembly. Robots are commonplace in many manufacturing settings, such as automotive assembly plants, and affordable and easy-to-program robotic welding cells can be found in even the smallest of job shops. Yet an automated fitting and welding system wasn’t catching anyone’s attention in the U.S.
Over the years, Bailey said he had seen several attempts to deliver such an automated system, but had not been sold on the end product. He had been to Poland to see a system, actually created by a structural steel company; that was a good start, but not as user-friendly as was desired. There was a gentleman in Michigan who looked to have a system that would work, but programming jobs took longer than the actual processing of the steel. Another machine tool vendor had an installation in Canada, but it was not robust enough to handle the large and long beams that Prospect Steel regularly handles.
About three years ago, Peddinghaus, which had supplied Prospect Steel with several pieces of equipment over the years, recommended that company management take a look at a robotic steel beam assembler from Austria’s Zeman Bauelemente, the same company that had installed the line in Poland several years before. Zeman had advanced the technology, and Peddinghaus, which was representing the company in the U.S., thought it might work for Prospect Steel.
Before the Prospect Steel management team headed back to Austria to see the line in action, it provided the Zeman representatives with a request to provide parts that would correspond with 10 jobs that came from the Prospect Steel library. Zeman only got the bill of materials for the work; it wouldn’t get the actual 3-D models on which the jobs were based until the Arkansas structural steel fabricators stepped foot into its facility.
“We came over and had the models on a thumb drive. They had the parts there, and I said, ‘OK. Show us,’” said Steve Grandfield, Prospect Steel’s executive vice president. “I stood behind them and watched them stick the thumb drive in the machine and pull up the model. They looked at the TEKLA model and exported it into their own software program. Within five minutes, it was running.
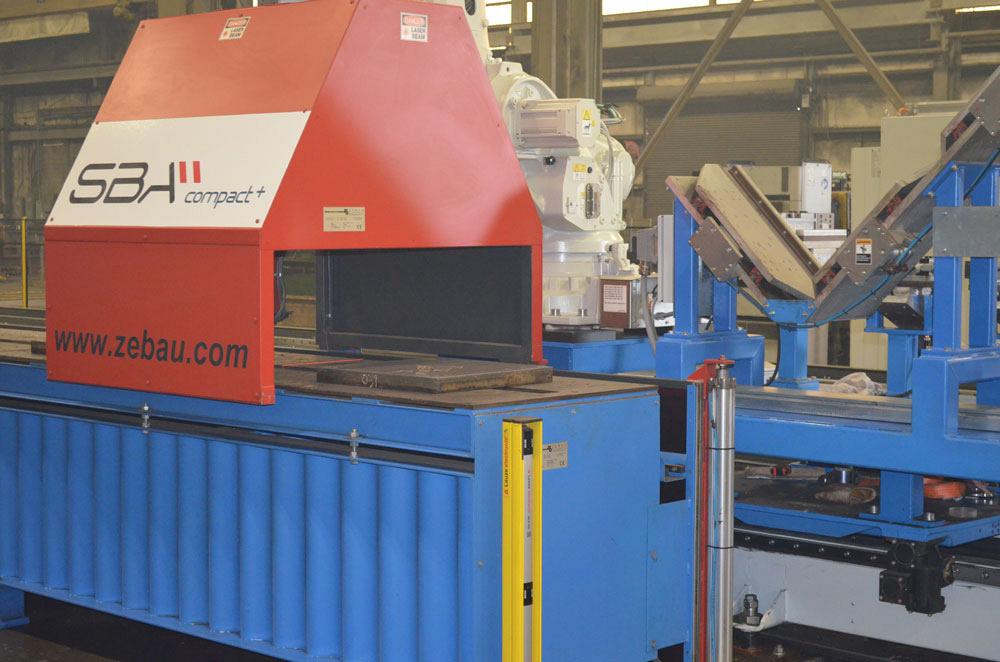
Figure 2
The assembly robot on the line also plays a key role in scanning parts that are destined to be attached to structural steel workpieces. The robot picks up a scanning hood and moves down a table where parts are stationed prior to assembly. The scanner matches the parts to the upcoming job and also provides size and orientation data to the control software.
“They could adjust the programs. They could fit up the parts without any problems,” he added. “It went to work.”
Prospect Steel went home with the intention of putting one of the lines in its Little Rock facility. It just needed to find room in its main fabrication facility for the large line, which is roughly about 170 feet long by 33 feet wide. (Prospect Steel has about 400,000 square feet of manufacturing space between its two facilities.) It would use the months before the arrival of the equipment in September 2016 to create that space.
Prospect Steel Put the Automation to Work
The other factor that management had to address before the SBA Compact + beam assembler line showed up was the Little Rock workforce. When robots show up on a manufacturing floor, workers typically may think that they are being brought in to take work away from humans. Bailey said company managers wanted to stress that the new system was actually brought in to provide more work for the humans.
“We told them well in advance what was coming, what it was going to do, and that we did not buy it to replace them. We said we bought it to be able to increase our throughput, which means more tons, which means fewer hours per ton, which means fewer dollars-per-ton cost, which means we can sell more work and we can make more money,” Bailey said.
“So it’s all about throughput. It was not about eliminating people,” he added.
Some people groused, according to Bailey, but the majority maintained a positive attitude about the new technology introduction. He believed that they recognized if the company could process more work, that meant more opportunities for increased compensation. Success was good for all.
The line arrived in September 2016 (see Figure 1). About four weeks were needed for installation. Bailey said the line has been operating seven days per week over three daily shifts since going into full production mode.
So how does it work? Without too much human intervention would be the correct answer.
Bailey said for the most part BIM provides the information necessary to produce clean CAM instructions inside the robotic assembler’s ProFit software. Still, Prospect Steel does employ someone to review all of the jobs before they are sent to the shop floor. If a problem exists in the model, such as a welding gun not being able to reach a joint, a red marker appears. In this case, a change in the welding sequence or repositioning the welding torch can solve the problem, which causes the red marker to turn to green, indicating the job can proceed without any worries. The reviewer is also looking for correct weld sizes, order of operations, how the magnet on the assembly robot picks up pieces, and the location of the turning devices to see if there are any interferences.
The first step of the operation is the parts table (see Figure 2). Parts can be put on the table in any order or orientation, for one job or multiple jobs. Next the assembly robot picks up a scanning hood and scans all the pieces on the table, looking for the parts to run the next job. When it finds those parts, it sends the information back to the control station to see if the parts that were scanned match up with what is detailed on the model in terms of features and tolerances (see Figure 3). Again, a green or red mark against the individual pieces of the assembly in the model indicates whether the job is ready to go.
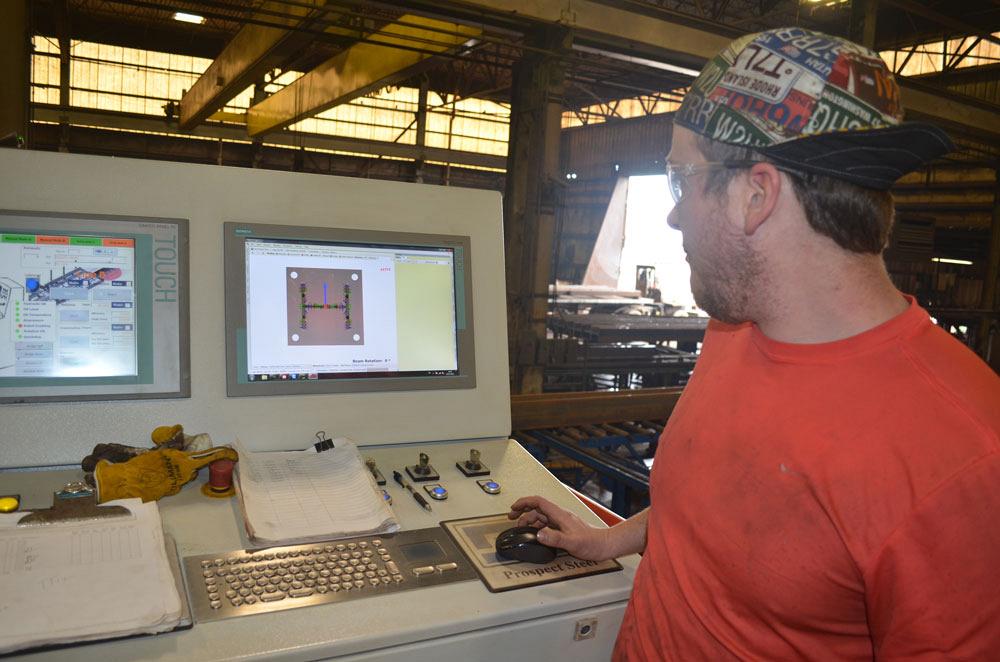
Figure 3
The line operator checks to see if the base plate to be placed on the beam matches up against tolerances indicated in the original model. If the operator sees green markings, he can begin the job knowing that everything will fit properly.
If everything checks out, the operator commences the job. At this point, the structural steel member is fed into the turning device (see Figure 4). Beams and other structural steel segments, which have been cut to length and drilled in a separate facility next door to the main fabrication building, are staged on a conveyor system that feeds into the robotic assembly system.
Once the structural steel is in place, the assembly robot on one side of the workpiece grabs a part, such as a base plate or a clip, with one of its three magnetic parts-handling tools. There is a plate turning device nearby if the assembly robot decides it needs to set down the part and grab it from the other side. With part in hand, the assembly robot positions it where the weld will occur.
Each of the two welding robots have a scanning device just above the welding gun. When the workpiece comes into position, the welding robot will scan the end of the beam and find the data point, or the zero point, from which all other measurements will be taken. The scanner also checks the material for mill variations in the workpiece, so it can make adjustments to ensure fit-up.
Bailey said that because the welding robots can adjust automatically to joint gaps in fit-up, programmers will take advantage of it during part design. For example, part designers will make stiffeners a little shorter than they normally would have if a human was fitting them. This ensures that the stiffeners will always fit in no matter how the flanges present themselves.
“We just make them a little shorter and let the robots split the difference. If it needs to increase the weld size, it will,” Bailey said. “It really doesn’t matter. The welds will still meet code.”
The assembly robot holds each part in position while one of the two welding robots tack weld them to the beam. When all parts have been tack welded, the robot can go to work to finish all of the welds (see Figure 5).
A plasma head also can be changed out on the welding robots. For example, if a beam has a cope at the end, the software automatically guides the robot to change out from the welding torch to the plasma cutting tool.
The turning devices can move the beam so the part is rotated 360 degrees if necessary (see Figure 6). This way the robots always have easy access to the areas that need to be addressed.
Right now, when the welding is completed (see Figure 7), the line operator shuts down the equipment so that he can attach chains from an overhead conveyor and move the beam to a staging area for cleaning and finishing. Bailey said the company is looking to add an automated beam extracting capability to the line in the near future. Again, it will have to find more room, about 75 ft., to accommodate the new addition, but he said the investment will be worth it because the line will become more productive. The time typically dedicated to moving the beams with the crane now can be used for more steel processing.
“This is the only application I have ever seen for a robot that was nonrepetitive and that also involved materials that were totally inaccurate. The tolerances from the mill are huge. That’s been the stumbling block with robotics for all of these years,” Bailey said.
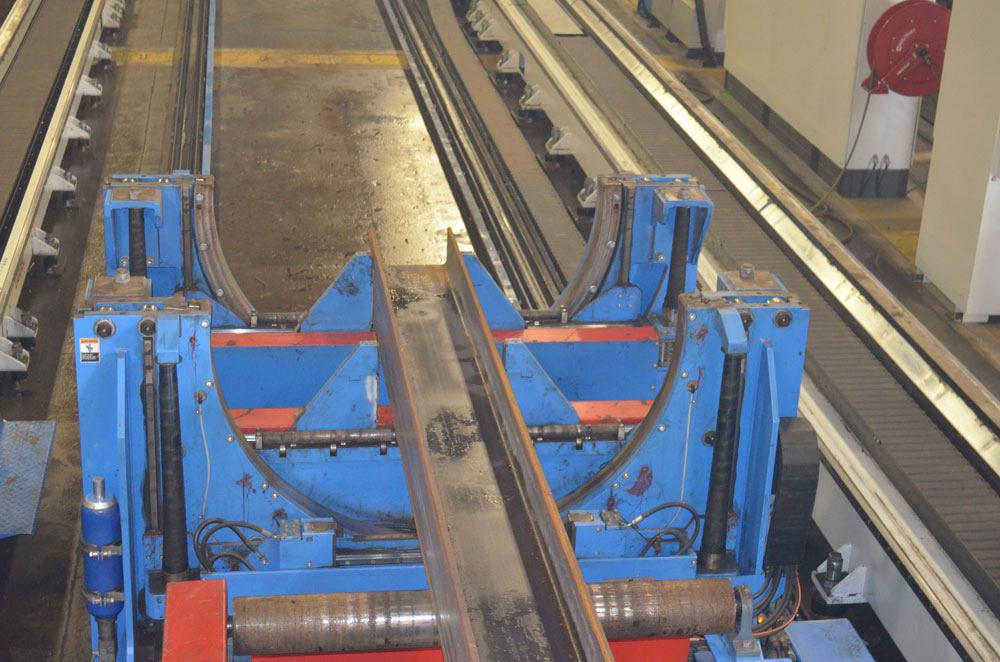
Figure 4
The turning device or “cradle” sits on rails. It moves into position to grab the beam from the conveyor and moves it into place for fitting and welding to begin.
Prospect Steel Needed More Productivity
Since the robotic beam assembler has gotten up and running, Bailey said Prospect Steel has added more people to its shop floor, and a lot more overtime has been made available to the staff. Tom Shueck, who founded the company more than 50 years ago, added that the new system has made people more aware of what’s happening on the shop floor.
“People are paying much more attention to the costs associated with the work they are doing every day,” Schueck said. “They are much more aware of what’s helping them to make money.”
As a result, Schueck said that the staff is going out of their way to take care of the equipment, ensuring that the area remains as clean as possible and collisions between beams and robots are avoided at all cost.
The robotic beam assembler also has changed the trajectory of Prospect Steel’s business (see Figure 8). Coming out of the Great Recession, the company had focused on a lot more bridge work, which was complex and large, an area that frankly didn’t have as many competitors as straight structural steel fabrication. Now Prospect Steel can be much more competitive on this less complex and straightforward fabrication work, Bailey said, and the automated fitting and welding line is the main reason for that. The company can process more work and take on more customers.
Bailey also said that the company has plans to add another SBA Compact+ in the Blytheville facility. If business continues to grow, Prospect Steel will add two more robots to that line in Blytheville, doubling its capacity.
As manufacturers often will joke, robots don’t take breaks, and they always show up ready to work. They are also giving these structural steel fabricators a reason to show up.
Prospect Steel, www.lexicon-inc.com/prospect-steel
Peddinghaus Corp., www.peddinghaus.com
Zeman Bauelemente, www.zebau.com
A Changing Role for Prospect Steel
When the SBA Compact+ steel beam assembly system was installed at Prospect Steel in Little Rock, Ark., in the fall of 2016, company president John Bailey knew that he wanted an experienced welder to be running the system. Anyone can learn to use a machine tool, but only experienced eyes can recognize when the welding torch may not be able to reach a welding joint or the surface condition of a beam can pose quality issues with a weld.
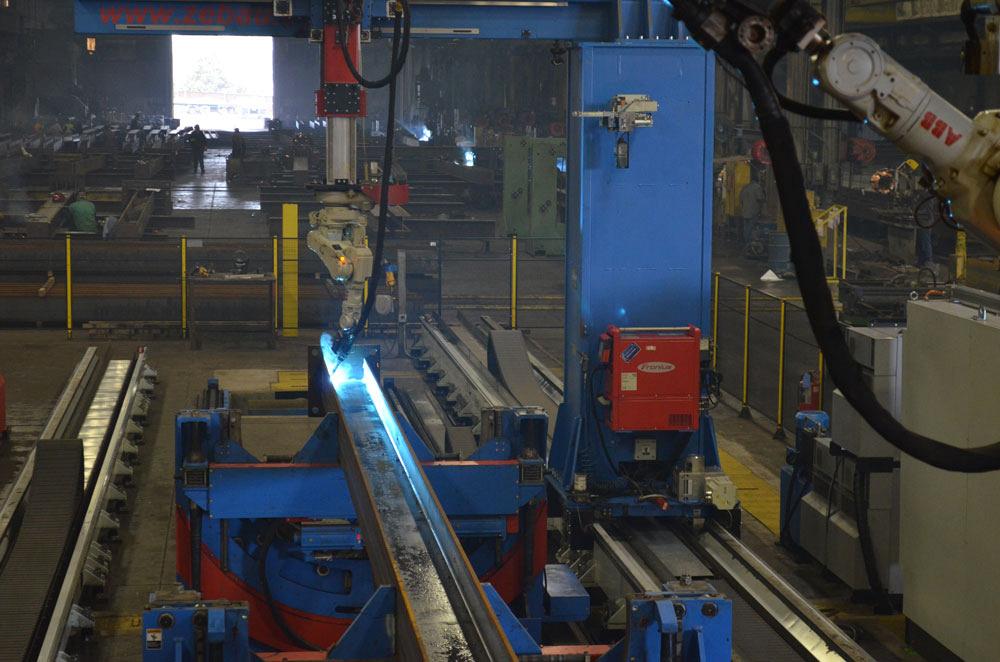
Figure 5
One of the robots needs only seconds to complete the weld between a base plate and a steel beam.
He later learned that the productivity of the automated fitting and welding system really called for a renewed focus on the front-end of the assembly process. The skilled welder’s eyes needed to recognize if parts were going to work before they were actually tack welded onto the beam.
“If you don’t have good parts, the robot’s not going to be happy. That’s why the focus has to be on making sure the parts are ready and that they are accurate,” Bailey said.
That’s why the line operator has to check each model against the scans made of parts that are destined to be attached to the structural steel workpiece in the turning devices. If tolerances don’t match up with the model, the operator can stop the job and make changes, either taking steps to resolve the issue or moving on to another job that doesn’t have the same quality obstacles.
The welder running Prospect Steel’s line actually has complete control of its operations. But he’s not just involved in monitoring a computer from the mezzanine that oversees the line. He’s shutting down the line when necessary to preheat certain beams if the welding procedure specification calls for it or check that the welding torches are in optimal shape for operation.
The nature of heavy fabricating is changing with the advent of automation. It’s no coincidence that the job of a heavy fabricator working alongside this type of robotics is going to change as well.
About the Author
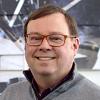
Dan Davis
2135 Point Blvd.
Elgin, IL 60123
815-227-8281
Dan Davis is editor-in-chief of The Fabricator, the industry's most widely circulated metal fabricating magazine, and its sister publications, The Tube & Pipe Journal and The Welder. He has been with the publications since April 2002.
subscribe now
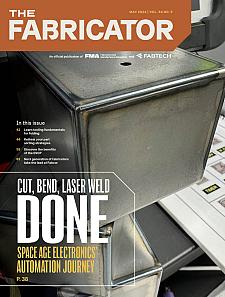
The Fabricator is North America's leading magazine for the metal forming and fabricating industry. The magazine delivers the news, technical articles, and case histories that enable fabricators to do their jobs more efficiently. The Fabricator has served the industry since 1970.
start your free subscription- Stay connected from anywhere
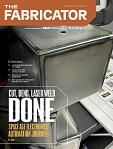
Easily access valuable industry resources now with full access to the digital edition of The Fabricator.
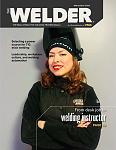
Easily access valuable industry resources now with full access to the digital edition of The Welder.
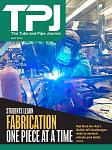
Easily access valuable industry resources now with full access to the digital edition of The Tube and Pipe Journal.
- Podcasting
- Podcast:
- The Fabricator Podcast
- Published:
- 04/30/2024
- Running Time:
- 53:00
Seth Feldman of Iowa-based Wertzbaugher Services joins The Fabricator Podcast to offer his take as a Gen Zer...
- Industry Events
Pipe and Tube Conference
- May 21 - 22, 2024
- Omaha, NE
World-Class Roll Forming Workshop
- June 5 - 6, 2024
- Louisville, KY
Advanced Laser Application Workshop
- June 25 - 27, 2024
- Novi, MI
Precision Press Brake Certificate Course
- July 31 - August 1, 2024
- Elgin,