- FMA
- The Fabricator
- FABTECH
- Canadian Metalworking
Categories
- Additive Manufacturing
- Aluminum Welding
- Arc Welding
- Assembly and Joining
- Automation and Robotics
- Bending and Forming
- Consumables
- Cutting and Weld Prep
- Electric Vehicles
- En Español
- Finishing
- Hydroforming
- Laser Cutting
- Laser Welding
- Machining
- Manufacturing Software
- Materials Handling
- Metals/Materials
- Oxyfuel Cutting
- Plasma Cutting
- Power Tools
- Punching and Other Holemaking
- Roll Forming
- Safety
- Sawing
- Shearing
- Shop Management
- Testing and Measuring
- Tube and Pipe Fabrication
- Tube and Pipe Production
- Waterjet Cutting
Industry Directory
Webcasts
Podcasts
FAB 40
Advertise
Subscribe
Account Login
Search
Applications: Electric press brakes set the pace for lighting products manufacturer
- May 23, 2016
- Article
- Bending and Forming
Situation:
Kenall Mfg. is a manufacturer of energy-efficient lighting products for challenging environments. In late 2014 the company moved its production and office operations from Gurnee, Ill., to Kenosha, Wis., while also reducing its fabrication operation from three shifts to two.
Continued and expected growth in business made the company realize it needed to create additional fabrication capacity to address its forming requirements in one less shift.
Resolution:
Kenall decided to purchase five new E-brake electric press brakes from SafanDarley to help increase productivity. The brakes set the pace for the company’s flexible linear cell environment, called fabrication tracks, which begin with forming. Once formed on the brakes, the parts move through the tracks for welding, hardware insertion, and spot welding until they are complete for the next department.
Kenall’s previous press brakes didn’t have safety guarding, so the purchase of these new brakes—which feature integrated light guard technology—eliminated the need to retrofit light curtains to the old machines.
“The patented light curtain system requires zero setup when going from job to job,” said Mauricio Gutierrez Matta of SafanDarley. “And it is the only light curtain system in the world that can detect a safe condition and, through the CNC, allow for ram travel to occur automatically.”
Some employees who were seasoned on the old press brakes had reservations about the new machines, and the new brakes required a learning curve because of new controls, but the transition went smoothly. Offline programming from the previous press brakes continues on the new machines. Maintenance is minimal, primarily involving some greasing of fittings. Hydraulic oil changes have been eliminated. And most important, forming quality has remained high.
Currently about 90 percent of the company’s products are formed on the electric press brakes. It moved one of the old press brakes to the new fabrication track to allow flexibility for the 10 percent of jobs not run on the electric brakes.
Related Companies
subscribe now
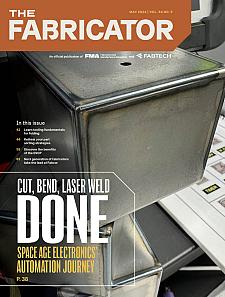
The Fabricator is North America's leading magazine for the metal forming and fabricating industry. The magazine delivers the news, technical articles, and case histories that enable fabricators to do their jobs more efficiently. The Fabricator has served the industry since 1970.
start your free subscription- Stay connected from anywhere
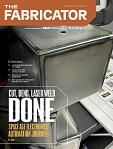
Easily access valuable industry resources now with full access to the digital edition of The Fabricator.
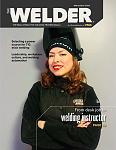
Easily access valuable industry resources now with full access to the digital edition of The Welder.
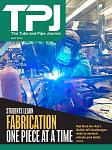
Easily access valuable industry resources now with full access to the digital edition of The Tube and Pipe Journal.
- Podcasting
- Podcast:
- The Fabricator Podcast
- Published:
- 04/30/2024
- Running Time:
- 53:00
Seth Feldman of Iowa-based Wertzbaugher Services joins The Fabricator Podcast to offer his take as a Gen Zer...
- Trending Articles
JM Steel triples capacity for solar energy projects at Pennsylvania facility
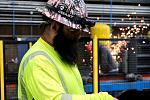
Fabricating favorite childhood memories
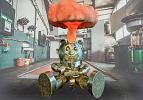
How laser and TIG welding coexist in the modern job shop
Robotic welding sets up small-batch manufacturer for future growth
Ultra Tool and Manufacturing adds 2D laser system
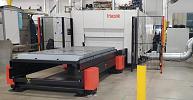
- Industry Events
Pipe and Tube Conference
- May 21 - 22, 2024
- Omaha, NE
World-Class Roll Forming Workshop
- June 5 - 6, 2024
- Louisville, KY
Advanced Laser Application Workshop
- June 25 - 27, 2024
- Novi, MI
Precision Press Brake Certificate Course
- July 31 - August 1, 2024
- Elgin,