- FMA
- The Fabricator
- FABTECH
- Canadian Metalworking
Categories
- Additive Manufacturing
- Aluminum Welding
- Arc Welding
- Assembly and Joining
- Automation and Robotics
- Bending and Forming
- Consumables
- Cutting and Weld Prep
- Electric Vehicles
- En Español
- Finishing
- Hydroforming
- Laser Cutting
- Laser Welding
- Machining
- Manufacturing Software
- Materials Handling
- Metals/Materials
- Oxyfuel Cutting
- Plasma Cutting
- Power Tools
- Punching and Other Holemaking
- Roll Forming
- Safety
- Sawing
- Shearing
- Shop Management
- Testing and Measuring
- Tube and Pipe Fabrication
- Tube and Pipe Production
- Waterjet Cutting
Industry Directory
Webcasts
Podcasts
FAB 40
Advertise
Subscribe
Account Login
Search
Die Science: How to shape and spot a binder properly
- July 27, 2018
- Article
- Bending and Forming
A binder, also called a blank holder or drawing pad, is a pressure-loaded, flat or contoured plate that controls metal flow in a drawing operation. For the binder to function properly, it must be the correct shape and fitted to the die face (the surface surrounding the draw die cavity).
Binder Basics
The binder shape is critical to drawing operation success. It also must be thick enough to resist even a slight amount of deflection under load, as minor deflection amounts can cause loss of metal flow control.
How thick should the binder be? It’s a judgment based on numerous factors, including the part material, thickness, and size; binder material and shape; and press shut height limitations. In general, it is better to design a binder to be too thick than not thick enough.
The Wrap
The shape the sheet metal takes when being formed to the binder is called the wrap. It usually follows the basic top contour of the drawing punch.
The two types of binder wraps are developable and undevelopable. The latter means the binder shape will force extra metal to be pushed to the center of the blank before the drawing punch makes contact. This is desired when stretch-drawing parts that require stretching or embossing. As an example, inner automobile doors often use an undevelopable wrap. The inner door usually is not defined as a Class A or exposed surface, so minor defects caused by the metal being creased before punch contact are permissible. Using an undevelopable wrap to stretch-draw a Class A part often results in surface defects in the center area of a part that are pre-established during draw pad contact, and they are nearly impossible to remove.
If a wrap is developable, it means the blank will not buckle, twist, or crease when taking the shape of the draw pad. This wrap type is desirable when stretch-drawing items such as exposed Class A body panels like outer doors and fenders.
Shaping the binder also helps to equalize the drawing depth throughout the part, thus reducing the forming severity, and it saves material. Binders usually are made from a hardened, wear-resistant tool steel; solid carbide; or hardenable cast iron.
Spotting a Binder
The process of fitting the binder to the die face—called spotting—is performed in a stamping press using a variety of large and small hand grinders. First, finish half the die, usually the draw die cavity, to the final geometry and a satisfactory surface appearance. This half of the die is commonly referred to as the master.
Before spotting, make sure the ram is parallel to the press bolster plate; if it isn’t, you will need to fix it or put even blocking in all four corners of the ram. You also can spot the binder on the pressure system, such as gas springs or press cushions. Keep in mind, though, that different pressure systems result in different binder deflection rates.
Once everything is ready, the first step is to perform a die-to-die spot, which involves grinding the binder to fit the shape of the master die face. Thinly coat the upper face of the master die with spotting blue, a special nondrying ink. Then lower the ram in extremely small increments until the die face touches the binder surface; it will leave a small amount of ink on the binder in each place it touched. Grind away the ink and repeat the process until the binder surface is level and covered in ink; 80 to 90 percent coverage usually is acceptable.
The next step is to clean the die and put sheet metal in. Raise the ram at least one sheet thickness before introducing it into the die. The blank now is covered with spotting blue on both sides. Again, lower the ram in very small increments until it strikes the blank. If blue ink is missing off both sides of the blank in the same area, it means the metal is being squeezed, and you will need to grind the area. Repeat the process until 80 to 90 percent of coined marks show up on the binder.
When you are confident that the binder has been spotted to the die face, you can start drawing material down into the cavity. For certain geometries, especially parts with curved, deeply profiled surfaces, the metal may thicken when drawing occurs. This shows up as coining on the binder surface. You will need to grind the binder with respect to compressive thickening that occurs as the metal flows inward. This process, called draw spotting or a running spot, is a critical part of fitting and spotting a binder.
After you complete the draw spotting, you can finish and polish the binder. Don’t expect a large amount of bearing on initial pad contact, because the draw pad has been fitted to metal flowing conditions.
Related Companies
subscribe now
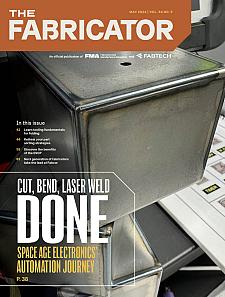
The Fabricator is North America's leading magazine for the metal forming and fabricating industry. The magazine delivers the news, technical articles, and case histories that enable fabricators to do their jobs more efficiently. The Fabricator has served the industry since 1970.
start your free subscription- Stay connected from anywhere
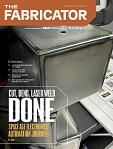
Easily access valuable industry resources now with full access to the digital edition of The Fabricator.
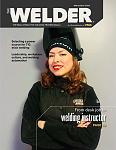
Easily access valuable industry resources now with full access to the digital edition of The Welder.
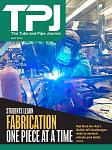
Easily access valuable industry resources now with full access to the digital edition of The Tube and Pipe Journal.
- Podcasting
- Podcast:
- The Fabricator Podcast
- Published:
- 04/30/2024
- Running Time:
- 53:00
Seth Feldman of Iowa-based Wertzbaugher Services joins The Fabricator Podcast to offer his take as a Gen Zer...
- Industry Events
Pipe and Tube Conference
- May 21 - 22, 2024
- Omaha, NE
World-Class Roll Forming Workshop
- June 5 - 6, 2024
- Louisville, KY
Advanced Laser Application Workshop
- June 25 - 27, 2024
- Novi, MI
Precision Press Brake Certificate Course
- July 31 - August 1, 2024
- Elgin,