Quality
- FMA
- The Fabricator
- FABTECH
- Canadian Metalworking
Categories
- Additive Manufacturing
- Aluminum Welding
- Arc Welding
- Assembly and Joining
- Automation and Robotics
- Bending and Forming
- Consumables
- Cutting and Weld Prep
- Electric Vehicles
- En Español
- Finishing
- Hydroforming
- Laser Cutting
- Laser Welding
- Machining
- Manufacturing Software
- Materials Handling
- Metals/Materials
- Oxyfuel Cutting
- Plasma Cutting
- Power Tools
- Punching and Other Holemaking
- Roll Forming
- Safety
- Sawing
- Shearing
- Shop Management
- Testing and Measuring
- Tube and Pipe Fabrication
- Tube and Pipe Production
- Waterjet Cutting
Industry Directory
Webcasts
Podcasts
FAB 40
Advertise
Subscribe
Account Login
Search
Is it the aluminum … or the process?
How to determine if “bad metal” is to blame for your forming problems
- By Beth Wickett and Scott Warford,
- May 23, 2017
- Article
- Bending and Forming
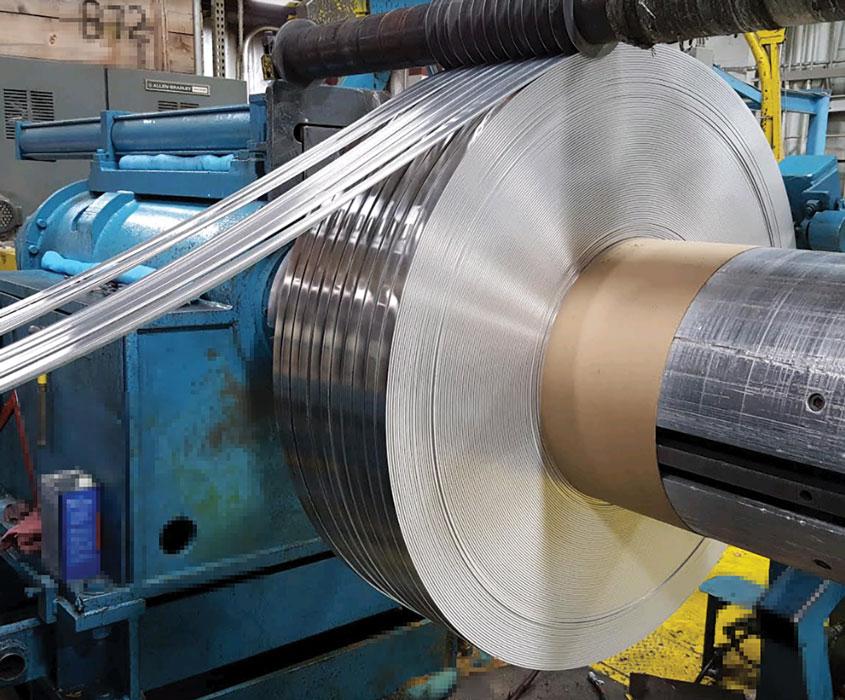
It may be tempting to blame forming problems on the material, but many times something else is the culprit.
As industry recognizes aluminum’s beneficial characteristics, the metal has evolved into a cornerstone material of transportation and building projects.
Aluminum is lightweight yet durable, corrosion-resistant, and 100 percent recyclable. The automotive industry is increasing aluminum content in the production of lightweight vehicles in efforts to meet increasing corporate average fuel economy (CAFE) standards.
It may be tempting to blame aluminum forming problems on the material, but many times something else is the culprit. Here is how you can determine whether or not the problem is materialrelated.
The Making of an Aluminum Alloy
An aluminum alloy is made by combining aluminum with another metal or metals. This is done to impart specific strengths and properties. You should consider each alloy’s strength when you choose material for a process. For example, the 2XXX, 6XXX, and 7XXX series respond well to heat treatment to obtain material strength.
Alloys must meet exact specifications before they are approved for rolling, tempering, and the intended end use. What may look like the perfect alloy chemical makeup on paper may result in a poorly produced alloy. A discussion with the aluminum supplier about how you intend to form and stamp the aluminum can rule out the use of an unsuitable alloy for your application.
Facing increased demand for aluminum, mills adapted ingot processing via computer programming to increase output speed and improve quality monitoring. Ingot can be produced in a direct cast or a continuous cast formation—with the latter providing higher productivity and greater efficiency because the ingot is fed directly into a rolling operation. However, because continuous casting is a one-step process, slag and particles may not be filtered well and can remain in the produced ingot. These impurities can cause materials to have problems during postprocess forming or in end use (see Figure 1).
How Stamping Processes Affect Metal
When forming problems occur, your first impulse may be to blame the material, but there might be other causes.
Various stamping manufacturing processes can damage the aluminum, just as they can damage any material. For example, some forming and blanking operations can wrinkle the surface or stretch the metal, which thins the material gauge, causing the aluminum to crack or tear.
Other factors, such as the use of incorrect tooling, clearance, coolants, and lubricants, may be causing forming problems.
Testing to Determine Cause
The first step in determining the cause of your forming problem is having a sample tested at a metal testing facility or lab to see if the material can be ruled out. Often both the stamping manufacturer and the material supplier send out samples, each using a trusted facility with which it has a history and a good working relationship.
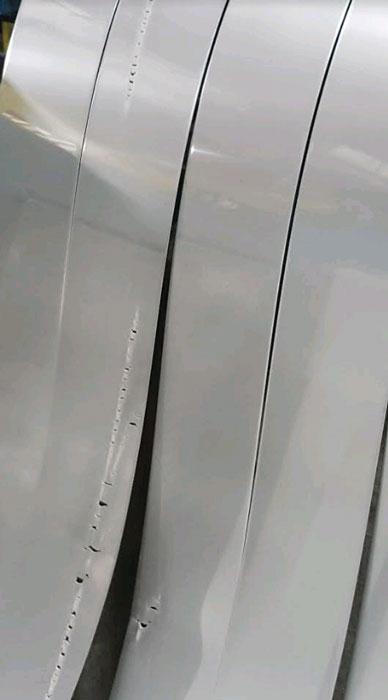
Figure 1
This material was found to have impurities in its chemistry makeup that caused the aluminum to crack and tear.
Testing should verify if the aluminum alloy meets both chemical and mechanical standards (see Figure 2). During ingot production, chemical distribution may not be uniform, resulting in areas that are susceptible to weakness or out-of-spec standards.
Chemical testing will determine if the material has been affected by the stamping process; whether it will fail under extreme conditions; and whether flaws, such as surface scratches, may affect its ability to do the job. Then the alloy’s mechanical properties—strength, hardness, ductility, and malleability—are tested to see how it performs under force or stress.
Because mills have differing processes and controls, alloys obtained from one can have entirely different properties from another (see Figure 3). This happens because alloying elements and impurities differ at each mill. In other words, because of the process, the same alloys from different mills may each meet standard specifications, but one may work well for you while the other one fails.
If the test results clear the material from blame, next scrutinize the tooling. If a machine, such as a decoiler or payoff, is not maintained, the material might not feed properly, causing the machine to jam or mar its surface. Using an incorrect welding technique may crack and weaken the part.
If the process is running as it should be, the next step in determining the cause is to try the same alloy from a different mill process. For example, if your material was produced by a continuous cast method initially, you might attempt using material made by a direct cast method.
Second, you might look at altering the temper to see if that improves the forming and finish.
Your last option is to use another alloy that is a better fit for your process. Often the material used in a job initially is found to be less than ideal once production begins and processes have been verified.
Communication is important to resolving most problems, because determining if the product or the process is the root cause isn’t simple. As long as all parties are willing to work together to obtain a mutually beneficial resolution, odds are good that most forming problems can be solved.
About the Authors
subscribe now
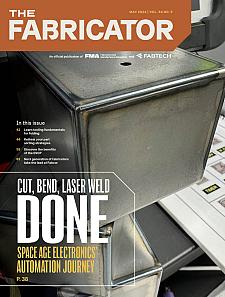
The Fabricator is North America's leading magazine for the metal forming and fabricating industry. The magazine delivers the news, technical articles, and case histories that enable fabricators to do their jobs more efficiently. The Fabricator has served the industry since 1970.
start your free subscription- Stay connected from anywhere
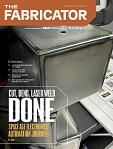
Easily access valuable industry resources now with full access to the digital edition of The Fabricator.
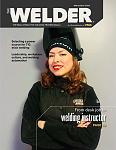
Easily access valuable industry resources now with full access to the digital edition of The Welder.
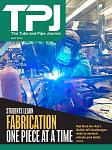
Easily access valuable industry resources now with full access to the digital edition of The Tube and Pipe Journal.
- Podcasting
- Podcast:
- The Fabricator Podcast
- Published:
- 04/30/2024
- Running Time:
- 53:00
Seth Feldman of Iowa-based Wertzbaugher Services joins The Fabricator Podcast to offer his take as a Gen Zer...
- Industry Events
Pipe and Tube Conference
- May 21 - 22, 2024
- Omaha, NE
World-Class Roll Forming Workshop
- June 5 - 6, 2024
- Louisville, KY
Advanced Laser Application Workshop
- June 25 - 27, 2024
- Novi, MI
Precision Press Brake Certificate Course
- July 31 - August 1, 2024
- Elgin,