- FMA
- The Fabricator
- FABTECH
- Canadian Metalworking
Categories
- Additive Manufacturing
- Aluminum Welding
- Arc Welding
- Assembly and Joining
- Automation and Robotics
- Bending and Forming
- Consumables
- Cutting and Weld Prep
- Electric Vehicles
- En Español
- Finishing
- Hydroforming
- Laser Cutting
- Laser Welding
- Machining
- Manufacturing Software
- Materials Handling
- Metals/Materials
- Oxyfuel Cutting
- Plasma Cutting
- Power Tools
- Punching and Other Holemaking
- Roll Forming
- Safety
- Sawing
- Shearing
- Shop Management
- Testing and Measuring
- Tube and Pipe Fabrication
- Tube and Pipe Production
- Waterjet Cutting
Industry Directory
Webcasts
Podcasts
FAB 40
Advertise
Subscribe
Account Login
Search
Optimizing hydraulic presses for deep drawing
Suitable frame, action, design, ancillary functions yield best results
- By Greenerd Press & Machine Co.
- May 25, 2016
- Article
- Bending and Forming
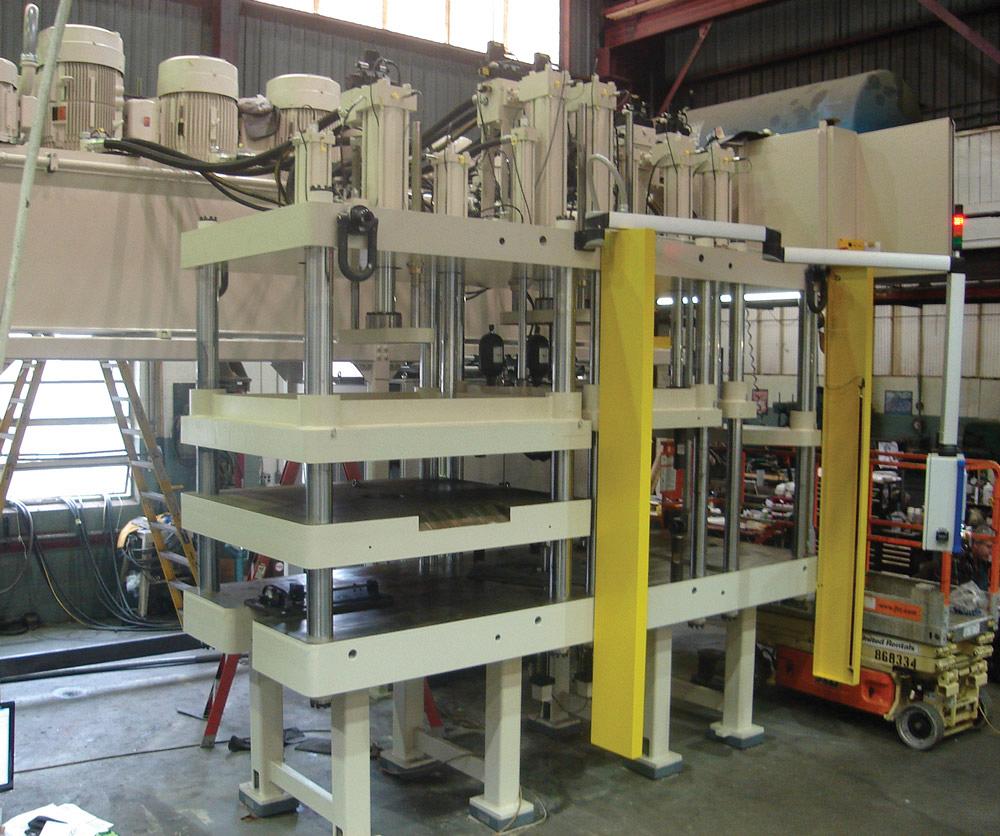
An inline, multistation deep-draw press can perform additional operations such as punching, coining, and trimming.
For deep-drawing applications, hydraulic presses provide exceptional flexibility. They also offer programming versatility, which can be used to optimize them for each specific use for maximum productivity and finished-product integrity.
Frame Styles
Several press frame styles allow for multiple draws to be performed in one press. Frame styles typically used in deep-draw applications are vertical action, horizontal action, and inline multistation. Any of these designs can incorporate multiple rams for double or triple action.
Vertical Action. The standard press frame for deep draws is a four-post press. While a C-frame design can also be used, a four-post press can be accessed from all four sides, making tooling accessible and enabling automatic blank feeding into a draw die from any of its four sides.
Vertical-action presses allow for draws to be done in one fluid motion. These presses have multiple openings for the drawn blank, or shell, to be redrawn once—or several times if required—to achieve the final diameter and length (see Figure 1). Examples of parts formed on these presses include propane tanks, fire extinguishers, cookware, and battery casings.
Horizontal Action. Some stamping manufacturers prefer to use a horizontal-actuated press for deep draws of large-diameter blanks or if the height of a vertical press is a problem. The horizontal orientation of this design allows blanks to be loaded overhead using a crane, robot, or other type of lift device. Like a vertical press, a horizontal press can perform multiple actions, including redraws when necessary.
However, proper support of the moving platen on horizontal presses is critical to maintaining alignment between the ram centerline and the tooling. To achieve this alignment, a horizontal press incorporates platen support and adjustment mechanisms, enabling the manufacturer to achieve and maintain system alignment throughout the stroke as the bearing plates gradually wear.
Examples of parts made on these types of presses include compressed natural gas tanks; high-pressure, military-grade tanks; and any pressure vessel that is too large to manipulate by hand.
Inline Multistation. While multiple draws and certain other operations can be achieved with a single-centerline press like a vertical or horizontal press, a broader variety of operations can be achieved using an inline multistation press design. This press’s fundamental design distinction is that it comprises, within one press frame, multiple pressing stations that can be controlled independently to perform drawing and other operations.
Following each cycle, the partially processed parts at each station are simultaneously advanced to the next station using a part transfer device for the next stage of draw; redraw; and downstream operations such as trimming, punching, and coining (see lead image). This enables a manufacturer to complete all of the part processing operations required within a single press, rather than several presses.
This inline multistation press style can be equipped with as many stations as needed to perform all the necessary draws and other operations. Usually it results in a higher product throughput than alternatives.
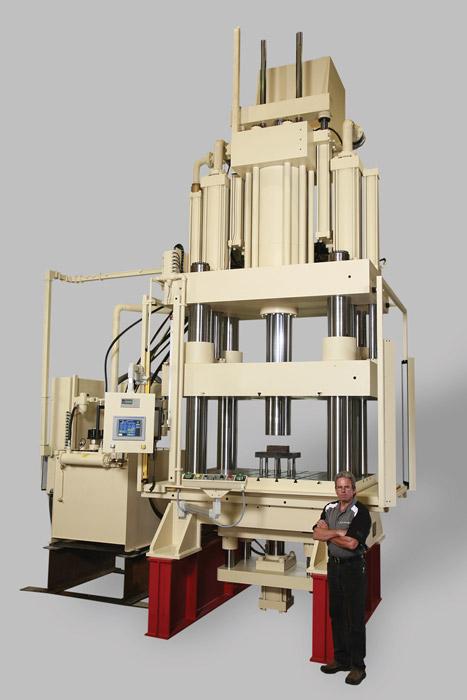
Figure 1
Vertical-action presses, such as this press
with a 600-ton punch ram, 325-ton cushion,
and 200-ton blank holder platen, typically
allow for deep draws to be performed in one
fluid motion.
Hydraulic Circuit
A stamping manufacturer needs to consider which hydraulic circuit design is appropriate for its application. Knowledge of the optimal and maximum draw speeds of the material to be drawn, and having a circuit design that can adjust to those draw speeds, is essential to reducing cycle time while maintaining part quality.
The simplest hydraulic system is a single, fixed, displacement-pump circuit. This circuit is suitable for deep-drawing applications in which the drawn shell is pushed out through the bottom of the die. This allows the punch to be set just above the blank’s load height. As soon as the cycle is initiated, the punch engages the blank and begins the draw, pushing the part out of the bottom of the die and returning to the pre-programmed top stop set point.
For increased advance and retract speeds, multiple pumps and a regenerative (regen) hydraulic circuit design typically is used. This regen design can more than double the advance speed with a minimal increase in power. A double-pump circuit can increase the approach and retract speeds using the same size (horsepower motor) as a single-pump circuit by using the available motor horsepower when the press is not drawing. A regen circuit directs the oil from the rod end of the cylinder to the piston end of the cylinder. With this type of hydraulic system, rapid advance speeds of 1,000 to 2,000 inches per minute (IPM) can be achieved with little or no additional horsepower required. The system is designed to achieve the full flow and pressure required of the pressing pump during the draw phase while still delivering high rapid advance and retract speeds to reduce the overall cycle time.
With today’s advancements in hydraulic pumps, it is possible to accurately adjust pressures and flows of the oil for any particular part of the press cycle. HP-limited pumps ensure that the maximum flow of oil is being introduced to the cylinder to minimize the draw time required. The ability to control the pump output provides exceptional flexibility in the hydraulic circuit.
For added repeatability and accuracy, proportional valves are used for directional and pressure control. With proportional directional valves offering less than 0.1 percent hysteresis, it is possible to achieve ±0.001-in. positional accuracy. Proportional relief valves compensate for changes in oil temperature and flow to achieve repeatable pressure.
Ancillary Functions
Drawing shells often requires that a reverse force be applied to “clamp” the material as it is being drawn. Any of the press styles can incorporate a cushion/blank holder to help manufacture the part. Usually the cushion/blank holder is used to clamp the material at a certain pressure to control the flow of the material as it is being drawn into the draw die. This pressure can be adjusted throughout the draw to accommodate the material’s characteristics and prevent it from wrinkling or tearing.
Another feature available in a deep-draw press is a knockout, which is generally ram-mounted (see Figure 2). This can be used to punch out a hole in the end of the shell, coin the bottom, or retain the drawn shell on the tooling as the punch returns to the pre-programmed top stop set point.
Some auxiliary hydraulics might be added to enable side punching. In addition, hydraulic oil flow and pressure might be required within the die itself. This can be designed into the hydraulic press and integrated into the controls to allow actuation when needed within the cycle.
Electrical Controls, Human-Machine Interface
Today’s hydraulic presses can be very technologically advanced. Most are now controlled by a programmable logic controller (PLC), and many presses today are equipped with human-machine interfaces (HMIs) to allow the manufacturer to quickly and easily change stroke, pressure, dwell time, ram speed, and many other press parameters throughout a cycle (see Figure 3).
More importantly, the HMI allows stampers to run the parts the same way time after time, whether the part was last run a week ago or three years ago, because all of the fine adjustments made throughout the cycle to achieve the optimal part quality and cycle time are saved as parameters and stored along with the program through the HMI. This reduces setup time and ensures that the parts are run consistently every run.
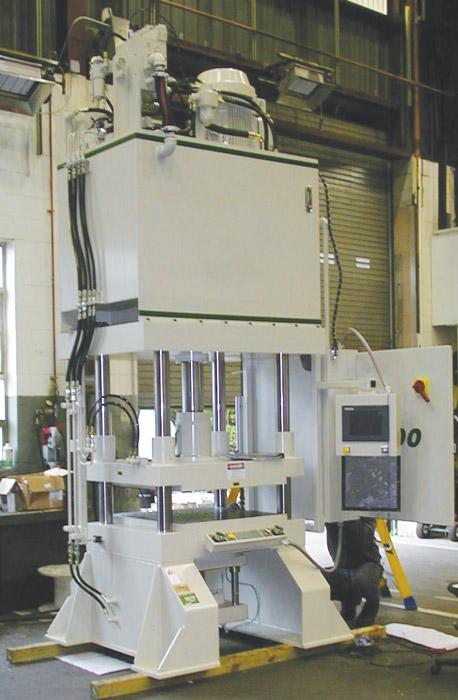
Figure 2
A ram-mounted knockout, as shown here,
can be used to punch out a hole in the end
of the shell, coin its bottom, or retain the
drawn shell for redraws.
With the addition of the HMI, manufacturers can now use their press as an R&D device to learn how changes in stroke signatures affect their product. They can determine where and when the stroke pressure is increasing or decreasing. This information can then be displayed in a trending chart or graphically, depending on the level of technology in the HMI.
Many other options are available to minimize job setup and tool identification time. Bar code readers are commonly used to ensure the correct program has been called up. When the job ticket is scanned, the press automatically selects the program previously established for that job. The same can be accomplished with radio frequency identification (RFID), although RFID enables significantly more capabilities. Stampers can use RFID to confirm that the correct combination of tooling, dies, and part programming has been selected for a given part before allowing the press to cycle. This can prevent significant tool damage caused by human error during setup.
Stampers commonly customize the HMI to reflect their individual needs so that their specific manufacturing process is documented and stored. Serializing of press stroke signatures for aerospace components is done through the HMI. Trending of actual press stroke positions and pressures is commonly used for evaluation purposes. Uploading of these press signatures to a SQL server can also be accomplished for historical documentation purposes.
Stampers should not underestimate what they can accomplish on a deep-draw hydraulic press. Unlike the past when hydraulic presses had to be set up manually, today’s hydraulic presses have considerable control and flexibility throughout the press cycle, and they can provide the manufacturer with valuable information about the way each operation is affecting their final product. A modern hydraulic press allows stamping manufacturers to take advantage of these updated features and their benefits.
About the Author
subscribe now
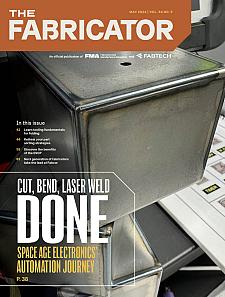
The Fabricator is North America's leading magazine for the metal forming and fabricating industry. The magazine delivers the news, technical articles, and case histories that enable fabricators to do their jobs more efficiently. The Fabricator has served the industry since 1970.
start your free subscription- Stay connected from anywhere
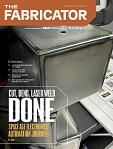
Easily access valuable industry resources now with full access to the digital edition of The Fabricator.
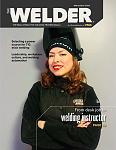
Easily access valuable industry resources now with full access to the digital edition of The Welder.
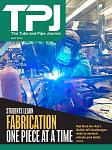
Easily access valuable industry resources now with full access to the digital edition of The Tube and Pipe Journal.
- Podcasting
- Podcast:
- The Fabricator Podcast
- Published:
- 04/30/2024
- Running Time:
- 53:00
Seth Feldman of Iowa-based Wertzbaugher Services joins The Fabricator Podcast to offer his take as a Gen Zer...
- Industry Events
Pipe and Tube Conference
- May 21 - 22, 2024
- Omaha, NE
World-Class Roll Forming Workshop
- June 5 - 6, 2024
- Louisville, KY
Advanced Laser Application Workshop
- June 25 - 27, 2024
- Novi, MI
Precision Press Brake Certificate Course
- July 31 - August 1, 2024
- Elgin,