- FMA
- The Fabricator
- FABTECH
- Canadian Metalworking
Categories
- Additive Manufacturing
- Aluminum Welding
- Arc Welding
- Assembly and Joining
- Automation and Robotics
- Bending and Forming
- Consumables
- Cutting and Weld Prep
- Electric Vehicles
- En Español
- Finishing
- Hydroforming
- Laser Cutting
- Laser Welding
- Machining
- Manufacturing Software
- Materials Handling
- Metals/Materials
- Oxyfuel Cutting
- Plasma Cutting
- Power Tools
- Punching and Other Holemaking
- Roll Forming
- Safety
- Sawing
- Shearing
- Shop Management
- Testing and Measuring
- Tube and Pipe Fabrication
- Tube and Pipe Production
- Waterjet Cutting
Industry Directory
Webcasts
Podcasts
FAB 40
Advertise
Subscribe
Account Login
Search
R&D Update: Evaluating dry film lubricants for automotive applications, Part II
Part II: The ironing test
- October 23, 2017
- Article
- Bending and Forming
The ironing test, developed at the ERC/NSM, reproduces production conditions of contract pressure up to 94 kilo pounds per square inch (KSI) and temperatures up to 300 degrees F to evaluate lubricant performance quantitatively. During the ironing test, lubricant performance on different sheet materials. In this test, the temperature and pressure at the tool-workpiece interface can be emulated by heating the ironing die and selecting a desired ironing ratio:
(R= (t0- tf / t0 ) x 100 )
Where: t0, tf = Initial and final thickness
On the left side of Figure 1 , a tool setup is shown in a hydraulic press with a CNC hydraulic cushion. The punch is stationary, and the ironing moves downward with the upper ram. The ironing ring’s derails are shown on the right side. The right is heated with a band heater that is insulated from a drawing die.
Testing lubricants is real-world production conditions is difficult and expensive. Lubricants should be tested in production conditions is difficult and expensive. Lubricants should be tested in production only after they have been proven effective in laboratory tests that emulate production conditions.
Recently the ERC/NSM conducted ironing tests to evaluate dry film lubricants with AISI 1018 sheet materials (initial sheet thickness, t0 =0.083 inch) at room temperature and tool temperature (68 degrees F and 168 degrees F, respectively). Detailed specifications of tested lubricants are given in Figure 2. A phosphate coating was used for comparison and benchmarking purposes.
Evaluation Criteria
Qualitative and quantitive analyses to determine lubricant effectiveness were tested on the following evaluation criteria:
- Maximum ironing load (the lower the load, the better the lubricant)
- Ironed cup surface topography after testing (the lower the surface roughness, the better the lubricant)
- Cup wall thinning (the lower the wall thinning, the better the lubricant)
- Lubricant buildup on die (good lubricants have minimum coating loss though die contact)
Test Results, Conclusions
Maximum ironing loads were compared for different lubricant and testing temperatures ( see Figure 3a and Figure 3b ). Lubricant C performed best regardless of temperature. However, as the testing temperature increased, lubricant B reacted similarly to lubricant C. Lubricant A displayed high friction at both testing temperatures.
Die lubricant buildup was indirectly quantified by measuring the specimen’s initial and final weights. In Figure 4 lubricant performance ranks are summarized in terms of evaluation criteria.
It should be note that specimens coated with lubricant C were not ranked in surface analyses, because phosphate coating is difficult to remove with chemical agents to measure surface roughness. In comparison to the phosphate coating (lubricant C), lubricant B displayed superior performance to lubricant A with the exception of buildup. This study illustrates that lubricant weigh directly affects die buildup characteristics.
By comparing laboratory test results with industrial results, the ERC ironing test was validated as a reliable method for evaluating lubricant performance under production-like conditions.
subscribe now
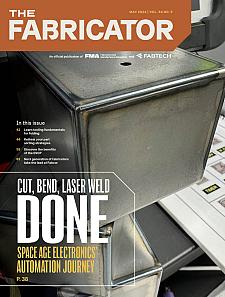
The Fabricator is North America's leading magazine for the metal forming and fabricating industry. The magazine delivers the news, technical articles, and case histories that enable fabricators to do their jobs more efficiently. The Fabricator has served the industry since 1970.
start your free subscription- Stay connected from anywhere
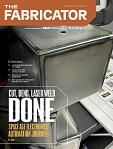
Easily access valuable industry resources now with full access to the digital edition of The Fabricator.
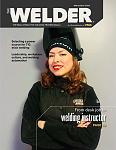
Easily access valuable industry resources now with full access to the digital edition of The Welder.
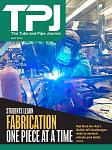
Easily access valuable industry resources now with full access to the digital edition of The Tube and Pipe Journal.
- Podcasting
- Podcast:
- The Fabricator Podcast
- Published:
- 04/30/2024
- Running Time:
- 53:00
Seth Feldman of Iowa-based Wertzbaugher Services joins The Fabricator Podcast to offer his take as a Gen Zer...
- Trending Articles
JM Steel triples capacity for solar energy projects at Pennsylvania facility
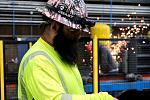
Fabricating favorite childhood memories
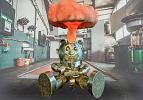
How laser and TIG welding coexist in the modern job shop
Robotic welding sets up small-batch manufacturer for future growth
Ultra Tool and Manufacturing adds 2D laser system
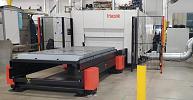
- Industry Events
Pipe and Tube Conference
- May 21 - 22, 2024
- Omaha, NE
World-Class Roll Forming Workshop
- June 5 - 6, 2024
- Louisville, KY
Advanced Laser Application Workshop
- June 25 - 27, 2024
- Novi, MI
Precision Press Brake Certificate Course
- July 31 - August 1, 2024
- Elgin,