- FMA
- The Fabricator
- FABTECH
- Canadian Metalworking
Categories
- Additive Manufacturing
- Aluminum Welding
- Arc Welding
- Assembly and Joining
- Automation and Robotics
- Bending and Forming
- Consumables
- Cutting and Weld Prep
- Electric Vehicles
- En Español
- Finishing
- Hydroforming
- Laser Cutting
- Laser Welding
- Machining
- Manufacturing Software
- Materials Handling
- Metals/Materials
- Oxyfuel Cutting
- Plasma Cutting
- Power Tools
- Punching and Other Holemaking
- Roll Forming
- Safety
- Sawing
- Shearing
- Shop Management
- Testing and Measuring
- Tube and Pipe Fabrication
- Tube and Pipe Production
- Waterjet Cutting
Industry Directory
Webcasts
Podcasts
FAB 40
Advertise
Subscribe
Account Login
Search
R&D Update: Evaluating stamping lubricants using the ironing test
- October 23, 2017
- Article
- Bending and Forming
Lubricant Bench Tests
Lubricant selection is usually based on experience and trial and error, which is time-consuming and expensive. Several bench tests, such as strip drawing, draw bending, and bend-stretching tests, emulate different stages of the stamping process and are used in combination to evaluate lubricant performance.
However, most of these tribotests cannot emulate the big contact pressures and speeds found in severe deformation process, such as the ironing processes used in manufacturing cans. Most of these tests are conducted at room temperature, while process temperatures can be as high as 200 degrees C.
Ironing Tribotest
The ironing tribotest, developed by ERC/NSM, induces high contract pressure up to 650 megapascals and interface temperatures up to 300 degrees F, which emulate the conditions of real-world production environment. This test will allow lubricant manufactures to distinguish the right lubricants and additives for severe deformation stamping applications like can making.
The ironing die was designed so the ironing load is sensitive to changes in interface friction characteristics. A heating element allows testing at elevated temperatures (see Figure 1 ). The testing procedure involved deep drawing a round cup, trimming it to a height of 50 mm, and ironing it (see Figure 2 ). Test parameters emulated conditions in a typical stamping operation:
- Interface pressure levels
- Sliding velocity between the tool and the sheet interface temperature by heating the ironing ring insert to process temperatures.
- Interface temperature by heating the ironing ring insert to process temperatures.
- Surface topography of the workpiece and tooling.
Lubricant performance evaluation was based on:
- The ironing load attained (see Figure 3 ). (The lower the load, the better the lubricant.)
- The surface quality of the ironed cups after the test (see Figure 4 .) (The better the surface finish, the better the lubricant.)
- The temperature range at which the lubricant failed (see Figure 3), quantified in terms of ironing load and surface quality.
The ironing tribotest can predict a quantitive value for the coefficient of friction. Thus, results obtained from this test can be used as input for process modeling in severe deformation stamping operations.
subscribe now
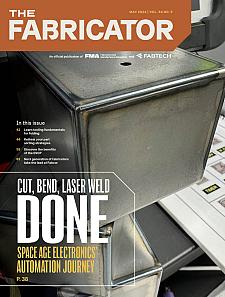
The Fabricator is North America's leading magazine for the metal forming and fabricating industry. The magazine delivers the news, technical articles, and case histories that enable fabricators to do their jobs more efficiently. The Fabricator has served the industry since 1970.
start your free subscription- Stay connected from anywhere
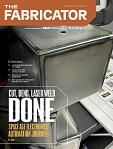
Easily access valuable industry resources now with full access to the digital edition of The Fabricator.
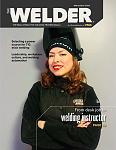
Easily access valuable industry resources now with full access to the digital edition of The Welder.
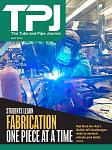
Easily access valuable industry resources now with full access to the digital edition of The Tube and Pipe Journal.
- Podcasting
- Podcast:
- The Fabricator Podcast
- Published:
- 04/30/2024
- Running Time:
- 53:00
Seth Feldman of Iowa-based Wertzbaugher Services joins The Fabricator Podcast to offer his take as a Gen Zer...
- Industry Events
Pipe and Tube Conference
- May 21 - 22, 2024
- Omaha, NE
World-Class Roll Forming Workshop
- June 5 - 6, 2024
- Louisville, KY
Advanced Laser Application Workshop
- June 25 - 27, 2024
- Novi, MI
Precision Press Brake Certificate Course
- July 31 - August 1, 2024
- Elgin,