- FMA
- The Fabricator
- FABTECH
- Canadian Metalworking
Categories
- Additive Manufacturing
- Aluminum Welding
- Arc Welding
- Assembly and Joining
- Automation and Robotics
- Bending and Forming
- Consumables
- Cutting and Weld Prep
- Electric Vehicles
- En Español
- Finishing
- Hydroforming
- Laser Cutting
- Laser Welding
- Machining
- Manufacturing Software
- Materials Handling
- Metals/Materials
- Oxyfuel Cutting
- Plasma Cutting
- Power Tools
- Punching and Other Holemaking
- Roll Forming
- Safety
- Sawing
- Shearing
- Shop Management
- Testing and Measuring
- Tube and Pipe Fabrication
- Tube and Pipe Production
- Waterjet Cutting
Industry Directory
Webcasts
Podcasts
FAB 40
Advertise
Subscribe
Account Login
Search
R&D Update: Forming high-strength steels, Part II
Part II: Selecting tool materials
- August 23, 2017
- Article
- Bending and Forming
Selecting appropriate tool materials requires a good understanding of tool steel properties, load distribution , tooling design (monoblock or segmented), and surface treatments.
Tool Developments
Along with tool steel properties, design and development also play crucial role in successfully forming HSS parts. Some design considerations are:
- Determining the chemical and metallurgical tool steel properties that will affect the performance of the steel in the application. These properties include hardness, yield strength, were resistance, fracture toughness, machinability, and dimensional stability during hardening and at high temperatures.
- Identifying process parameters such as tool steel composition, melting and refining methods, and theremomechanical treatments that may influence tool steel’s properties during production.
- Testing the material to validate the necessary material to validate the necessary material properties. Critical tool steel material properties associated with metal forming processes such as blanking and shearing, drawing, stamping and rolling are toughness, hardness, compressive strength, yield strength, and wear resistance.
Tool Steel Properties
Toughness. Transitioning from conventional steel sheets to HSS increases the need for tool steel toughness because of design modifications such as springback compensation. Generally, the steel’s impact toughness is measured to estimate its capacity to withstand fracture or chipping and severe stress concentrations in demanding geometries, such as small radii.
Hardness. Common indentation tests are used as an index to correlate hardness with other significant material properties, such as tensile, yield, and compressive (in the case of ceramic dies) strength. The hardness levels shown in Figure 1 are more critical when forming HSS sheets such as TRIP or CP (about 1,000 MPa), MART (1,200-1,500 MPa), and press-hardened MART (about 1,700 MPa) steels.
Wear Resistance. Adhesive and abrasive are the most common types of wear in stamping HSS. The amount of wear that occurs depends on the complexity of the die shape, type of sheet material being formed, and the tool steel. Wear resistance depends on the properties of a tool’s surface. Increased use of HSS has led to the development of new surface coating to improve wear resistance and tribological surface conditions.Popular coating methods include the nitriding process and chemical vapor deposition (CVD), physical vapor deposition (PVD), and plasma-assisted chemical vapor disposition (PACVD). Figure 2 shows the relative tool wear that occurs when punching mild steel sheet with conventional tool steel dies compared to punching DP 600 with uncoated and coated P/M tool steel dies.
Tool Design Guidelines
Tool and die design is greatly influenced by the operation sequence such as the number of forming stations, strokes per minute, lubrication conditions (dry film or spray), press characteristics, and in-house design guidelines. HSS tool design guidelines for forming conventional steel materials with allowances for higher forming forces. The following rules should be considered when forming HSS parts.
- Design the drawing process for a single operation.
- Stretch drawing is an alternative to conventional deep drawing.
- To minimize or compensate for springback, incorporate features that improve stiffness, such as coining around the punch corner radii.
- Increase radii in critical zones, if possible.
- Avoid deep contours inside a part.
For higher process forces and temperatures, consider the following guidelines:
- Appropriate tool materials, including heat-treated and coated, are necessary to withstand the higher forming loads and shear forces encountered.
- Draw die cooling may be necessary for high stroking rates.
- Coat punches and other contact surfaces to improve surface friction conditions.
- Higher stripper forces may be necessary.
- Consider ceramic tool materials in hot forming as inserts or as thermally sprayed coatings.
subscribe now
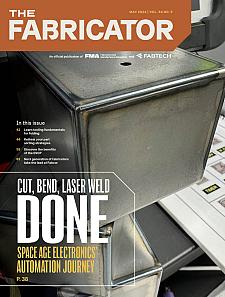
The Fabricator is North America's leading magazine for the metal forming and fabricating industry. The magazine delivers the news, technical articles, and case histories that enable fabricators to do their jobs more efficiently. The Fabricator has served the industry since 1970.
start your free subscription- Stay connected from anywhere
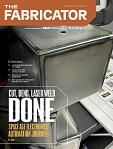
Easily access valuable industry resources now with full access to the digital edition of The Fabricator.
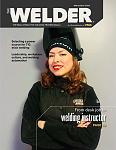
Easily access valuable industry resources now with full access to the digital edition of The Welder.
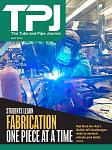
Easily access valuable industry resources now with full access to the digital edition of The Tube and Pipe Journal.
- Podcasting
- Podcast:
- The Fabricator Podcast
- Published:
- 04/30/2024
- Running Time:
- 53:00
Seth Feldman of Iowa-based Wertzbaugher Services joins The Fabricator Podcast to offer his take as a Gen Zer...
- Industry Events
Pipe and Tube Conference
- May 21 - 22, 2024
- Omaha, NE
World-Class Roll Forming Workshop
- June 5 - 6, 2024
- Louisville, KY
Advanced Laser Application Workshop
- June 25 - 27, 2024
- Novi, MI
Precision Press Brake Certificate Course
- July 31 - August 1, 2024
- Elgin,