- FMA
- The Fabricator
- FABTECH
- Canadian Metalworking
Categories
- Additive Manufacturing
- Aluminum Welding
- Arc Welding
- Assembly and Joining
- Automation and Robotics
- Bending and Forming
- Consumables
- Cutting and Weld Prep
- Electric Vehicles
- En Español
- Finishing
- Hydroforming
- Laser Cutting
- Laser Welding
- Machining
- Manufacturing Software
- Materials Handling
- Metals/Materials
- Oxyfuel Cutting
- Plasma Cutting
- Power Tools
- Punching and Other Holemaking
- Roll Forming
- Safety
- Sawing
- Shearing
- Shop Management
- Testing and Measuring
- Tube and Pipe Fabrication
- Tube and Pipe Production
- Waterjet Cutting
Industry Directory
Webcasts
Podcasts
FAB 40
Advertise
Subscribe
Account Login
Search
R&D Update: Sheet hydroforming (part II)
- September 1, 2017
- Article
- Bending and Forming
SHF-D
During SHF-D, pressure in generated by pumping fund into the pressurizing chamber where the sheet comes in contact with the top die (see Figure 1 ). The sheet blank then deforms into the die cavity because of the applied pressure. As a result, blank deformation changes the volume of the pressurizing chamber.
Fluid pressure slowly increases until the blank is in full contact with die. Pressure then increases rapidly to form sharp corners. However, the volume of the pressure chamber does not change significantly with blank deformation. Therefore, the shape of the pressure curve versus the time curve in SHF-D depends on sheet deformation and die geometry.
Blank deformation for a given pressure can be controlled by blank holder force during the process as shown in Figure 2 . In SHF-D, higher pressure and less blank holder force can result in wrinkling and leaking. Less pressure and higher blank holder force can result in excessive thinning from stretching. Therefore, it’s important to estimate the process parameters (blank holder force) as a function of pressure to form a part successfully without defects.
SHF-P
During SHF-P, the sheet is deformed by punch motion while the blank holder force and the pot pressure are process parameters adjusted independently to form a good part. Excessive pressure and insufficient blank holder force can result in wrinkling and leakage. Insufficient pressure and high blank holder force similar to conventional deep drawing can create wrinkles on a part’s side wall, depending on part geometry. Therefore, it’s important ti determine the process parameters (blank holder force and pressure in the pot) as a function of punch stroke to form a part without defects.
SHF-D Process Parameters
Process parameters like blank holder force in the SHF-D process are estimated by trail and error and usually are kept constant throughout the forming process. The minimum blank holder force required to prevent wrinkling and leakage results in more drawing and less thinning in the formed part.
At the ERC/NSM, optimization techniques and FE simulations were used to estimate blank holder force as a function of pressure to form an asymmetric part using SHF-D tooling (see Figure 3 ). Figure 4 and Figure 5 are examples of pressure versus time and pressure versus blank holder force for the asymmetric part, respectively, which is aluminum alloy A5754-O from a 1.15-mm-thick blank.
Predicted blank holder force profiles were used in experiments to form the part. The blank holder force profile resulted in negligible amount of leakage of the pressurizing medium. Thinning distribution from the formed part worked well with experimental results (see Figure 6 ). As a result, FE simulation could be used to estimate process parameters instead of costly trial-and-error tryout in the press.
subscribe now
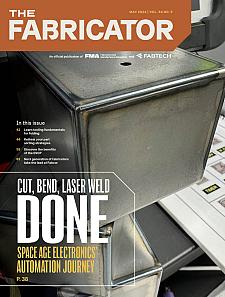
The Fabricator is North America's leading magazine for the metal forming and fabricating industry. The magazine delivers the news, technical articles, and case histories that enable fabricators to do their jobs more efficiently. The Fabricator has served the industry since 1970.
start your free subscription- Stay connected from anywhere
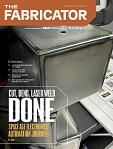
Easily access valuable industry resources now with full access to the digital edition of The Fabricator.
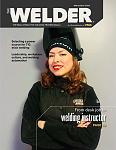
Easily access valuable industry resources now with full access to the digital edition of The Welder.
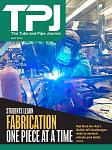
Easily access valuable industry resources now with full access to the digital edition of The Tube and Pipe Journal.
- Podcasting
- Podcast:
- The Fabricator Podcast
- Published:
- 04/30/2024
- Running Time:
- 53:00
Seth Feldman of Iowa-based Wertzbaugher Services joins The Fabricator Podcast to offer his take as a Gen Zer...
- Industry Events
Pipe and Tube Conference
- May 21 - 22, 2024
- Omaha, NE
World-Class Roll Forming Workshop
- June 5 - 6, 2024
- Louisville, KY
Advanced Laser Application Workshop
- June 25 - 27, 2024
- Novi, MI
Precision Press Brake Certificate Course
- July 31 - August 1, 2024
- Elgin,