- FMA
- The Fabricator
- FABTECH
- Canadian Metalworking
Categories
- Additive Manufacturing
- Aluminum Welding
- Arc Welding
- Assembly and Joining
- Automation and Robotics
- Bending and Forming
- Consumables
- Cutting and Weld Prep
- Electric Vehicles
- En Español
- Finishing
- Hydroforming
- Laser Cutting
- Laser Welding
- Machining
- Manufacturing Software
- Materials Handling
- Metals/Materials
- Oxyfuel Cutting
- Plasma Cutting
- Power Tools
- Punching and Other Holemaking
- Roll Forming
- Safety
- Sawing
- Shearing
- Shop Management
- Testing and Measuring
- Tube and Pipe Fabrication
- Tube and Pipe Production
- Waterjet Cutting
Industry Directory
Webcasts
Podcasts
FAB 40
Advertise
Subscribe
Account Login
Search
R&D Update: Springback in stamping, Part II
- September 4, 2017
- Article
- Bending and Forming
Springback is cased by a formed part’s elastic recovery, which is a serious problem for the stamping industry. A part’s elastic recovery at a given point is very small. However, spingback can produce a significant change in geometry because of its mechanical multiplying effect on other locations when curved surfaces are involved.
Springback in HSS part is greater than in mild steel parts because HSS has higher yield strength than mild steel. Springback may distort a stamped part’s bend angle, side wall curls, or overall formed geometry from its design specifications.
Prediction and Control Techniques
Several prediction and control techniques can reduce springback in HSS stamped parts. Some are:
- Compression during forming. Elastic stresses in the thickness direction of a formed material cause springback. Elastic stresses and springback can be reduced by applying compressive stress. The first technique uses a counter pressure. The first technique uses a counter pressure at the punch bottom. The second technique presses at the punch corner with a specially designed die or blank holder edge (see Figure 1 ).
- Variable blank holder force. Another method of reducing springback in HSS is to apply variable blank holder force (BHF). In this method, BHF is increased in the final stage of forming, which drastically reduces springback. However, it requires a press that can vary blank holder force during forming. Multiple-point cushion technology can vary blank holder force in space, location, and in stroke during the forming process. In other words, if there are four cushion pins, for example, each pin can be programmed differently to provide constant or variable force during the forming stroke. The ERC/NSM has conducted finite elements analysis (FEA) of stamping processes to predict optimum variable blank holder force that reduces springback.
- Form-draw process. This technique is effective in reducing side wall curls in HSS stamped parts. Figure 2 illustrates this process for a vehicle bumper part. Initially the punch and pad form the sheet’s bottom profile (see Figure 2a). The side walls then are formed by the upward movement of the bottom dies (see Figure 2b). At the end of the process, blank holder force is applied to the sheet’s edges, generating large tensile stresses (see Figure 2c). The process’s main advantages is that the side wall does not undergo bend unbend deformation as in a conventional drawing processes, so springback is reduced (see Figure 2d).
Finite Element Simulations
In addition to these techniques for controlling springback, predicting it first through FE simulations and modifying the die shape is becoming more useful and practical. Several studies have been conducted to validate FEM springbuck predictions in HSS experiments.
An FEM springback study conducted at ERC/NSM in cooperation with a press builder used a commercial FE package to simulate the flanging process for a curved part made from AHSS DP980 steel. Figure 3 shows the parts obtained from experiments and FE simulations. In the springback simulation, conducted at the end of the forming and after that part was removed from the die, the part was allowed to recover elastically, in the absence of tooling. It was conducted that the FE simulations. In the springback study conducted at the end of the forming and after the part was removed from the die, the part was allowed to recover elastically, in the absence of tooling. It was concluded that the FE simulation predicted the wrinkling, thickening and thinning distribution, and part geometry after springback, which matched well with the experimental measurements.
subscribe now
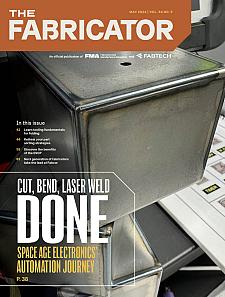
The Fabricator is North America's leading magazine for the metal forming and fabricating industry. The magazine delivers the news, technical articles, and case histories that enable fabricators to do their jobs more efficiently. The Fabricator has served the industry since 1970.
start your free subscription- Stay connected from anywhere
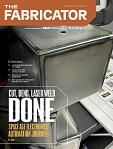
Easily access valuable industry resources now with full access to the digital edition of The Fabricator.
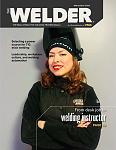
Easily access valuable industry resources now with full access to the digital edition of The Welder.
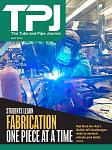
Easily access valuable industry resources now with full access to the digital edition of The Tube and Pipe Journal.
- Podcasting
- Podcast:
- The Fabricator Podcast
- Published:
- 04/30/2024
- Running Time:
- 53:00
Seth Feldman of Iowa-based Wertzbaugher Services joins The Fabricator Podcast to offer his take as a Gen Zer...
- Industry Events
Pipe and Tube Conference
- May 21 - 22, 2024
- Omaha, NE
World-Class Roll Forming Workshop
- June 5 - 6, 2024
- Louisville, KY
Advanced Laser Application Workshop
- June 25 - 27, 2024
- Novi, MI
Precision Press Brake Certificate Course
- July 31 - August 1, 2024
- Elgin,