- FMA
- The Fabricator
- FABTECH
- Canadian Metalworking
Categories
- Additive Manufacturing
- Aluminum Welding
- Arc Welding
- Assembly and Joining
- Automation and Robotics
- Bending and Forming
- Consumables
- Cutting and Weld Prep
- Electric Vehicles
- En Español
- Finishing
- Hydroforming
- Laser Cutting
- Laser Welding
- Machining
- Manufacturing Software
- Materials Handling
- Metals/Materials
- Oxyfuel Cutting
- Plasma Cutting
- Power Tools
- Punching and Other Holemaking
- Roll Forming
- Safety
- Sawing
- Shearing
- Shop Management
- Testing and Measuring
- Tube and Pipe Fabrication
- Tube and Pipe Production
- Waterjet Cutting
Industry Directory
Webcasts
Podcasts
FAB 40
Advertise
Subscribe
Account Login
Search
R&D Update: Warm-forming magnesium sheet, Part II
- August 18, 2017
- Article
- Bending and Forming
In Figure 1 , a warm deep-drawn aluminum sheet is divided into five regions (A-B, B-C, C-D,D-E, and E-F) to illustrate the heated and the cooled areas of the deforming material. The portion of the blank between the blank holder and the die (E-F) is heated up to 300 degrees C to decrease compressive stress and facilitate metal flow.
To heat the material, heating elects are incorporated into the blank holder and the die. When the sheet enters the die corner (E-D) the punch wall (D-C) and the corner area (C-B) are cooled to increase strength and prevent premature sheet fracture. Heat transfer during the warm-drawing operation causes the punch temperatures to increase, as shown in Figure 2.
Warm-forming Research
Studies conducted at the Institute Metal Forming (IFUM) at the Technical University of Hannover, Germany, found that when the die and blank holder are heated to approximately 200 to 240 degrees C, the punch temperature increases as much as 50 degrees C above room temperature. As a result, punch cooling is necessary because elevated temperatures can affect the limiting draw ratio.
Other important warm-forming tool design issues include uniform temperature distribution and heating and cooling. The blank holder and die’s temperature should not vary from E to F (see Figure 1). Depending on the material, cooling the die ring and the punch is important to achieve higher draw ratios. For aluminum, heating preferably should take place only at the flange area. For magnesium, the effect of the cooled die corner needs to be investigated.
Many research institutes, including the ERC/NSM, are studying the warm forming of aluminum and especially magnesium. The Institute for Production Engineering and Forming Machines (PtU) of the University of Darmstadt has developed tooling for warm-forming aluminum alloys that uses a heating and cooling technique similar to that shown in Figure 1.
This tooling can be used for hydromechanical deep drawing, in which a sheet is drawn against heated fluid under pressure, which increases drawability at elevated temperatures. Results of these experiments show significant improvement in drawability when the die corner and the punch are cooled.
The Institute for Metal Forming Technology (IFU) at the University of Stuttgart has developed pneumatic bulge tooling that allows forming operations at elevated temperatures. The tooling consist of an upper and lower die, and both are heated. The upper die contains an intel for internal pressure and is heated by cartridge heaters.
To ensure that metal doesn’t flow into the die cavity during deformation, lock beads are used to provide a seal. In Figure 3, the lower die is heated by a band heater with a pressure inlet that forms that part using counter pressure.
The use of magnesium in manufacturing is under investigation. One key for unlocking this material’s potential is tooling that provides temperature distribution and control in the die, blank holder, and punch.
Part III will cover preliminary design guidelines and example parts manufactured from magnesium sheet using the warm-forming process.
subscribe now
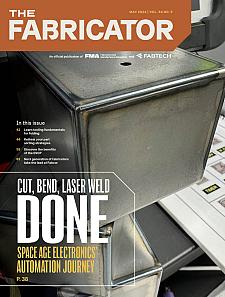
The Fabricator is North America's leading magazine for the metal forming and fabricating industry. The magazine delivers the news, technical articles, and case histories that enable fabricators to do their jobs more efficiently. The Fabricator has served the industry since 1970.
start your free subscription- Stay connected from anywhere
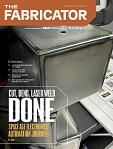
Easily access valuable industry resources now with full access to the digital edition of The Fabricator.
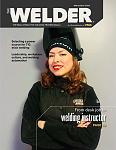
Easily access valuable industry resources now with full access to the digital edition of The Welder.
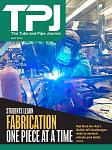
Easily access valuable industry resources now with full access to the digital edition of The Tube and Pipe Journal.
- Podcasting
- Podcast:
- The Fabricator Podcast
- Published:
- 04/30/2024
- Running Time:
- 53:00
Seth Feldman of Iowa-based Wertzbaugher Services joins The Fabricator Podcast to offer his take as a Gen Zer...
- Industry Events
Pipe and Tube Conference
- May 21 - 22, 2024
- Omaha, NE
World-Class Roll Forming Workshop
- June 5 - 6, 2024
- Louisville, KY
Advanced Laser Application Workshop
- June 25 - 27, 2024
- Novi, MI
Precision Press Brake Certificate Course
- July 31 - August 1, 2024
- Elgin,