Servo Press Scientist
- FMA
- The Fabricator
- FABTECH
- Canadian Metalworking
Categories
- Additive Manufacturing
- Aluminum Welding
- Arc Welding
- Assembly and Joining
- Automation and Robotics
- Bending and Forming
- Consumables
- Cutting and Weld Prep
- Electric Vehicles
- En Español
- Finishing
- Hydroforming
- Laser Cutting
- Laser Welding
- Machining
- Manufacturing Software
- Materials Handling
- Metals/Materials
- Oxyfuel Cutting
- Plasma Cutting
- Power Tools
- Punching and Other Holemaking
- Roll Forming
- Safety
- Sawing
- Shearing
- Shop Management
- Testing and Measuring
- Tube and Pipe Fabrication
- Tube and Pipe Production
- Waterjet Cutting
Industry Directory
Webcasts
Podcasts
FAB 40
Advertise
Subscribe
Account Login
Search
R&D Update: Predicting off-center loading in sheet metal forming operations, Part II
Why off-center loading is so critical in a transfer die forming operation for stampers
- By David Diaz-Infante, Dr., Hitansh Singhal, Jamie Bowman, and Neil Parker
- December 10, 2019
- Article
- Bending and Forming
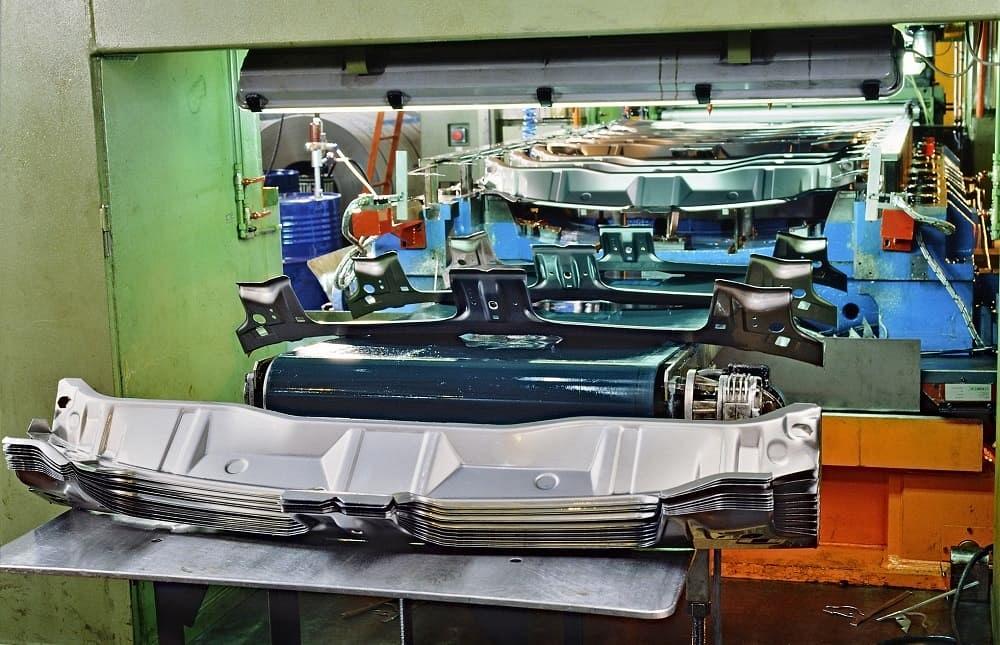
Researchers at the Center for Precision Forming share their methodology for predicting off-center loading in a transfer die set. Getty Images
Editor’s Note: This is Part II of a two-part series. Part I discussed how to predict off-center loading when forming with a single tool.
In a transfer die forming operation, a blank/initial part is transferred to several individual dies/stations to form the final part. As illustrated in Figure 1, differences between the forming and cutting forces and the distances of the individual stations from the press center can generate an off-center load, which leads to an imbalance on the press (trying to tilt the press bolster). Because the press is large, the magnitude of this imbalance produced by each station also is large. Therefore, off-center loading is a more critical issue in a transfer die forming operation than in a single die forming operation.
Case Study: Transfer Die Set
Researchers at The Ohio State University’s Center for Precision Forming studied a part provided by Bowman Precision Tooling. The transfer die set for forming this part was about 6,000 by 1,700 millimeters, comprising seven individual dies (see Figure 2). The distance between the centers of each station was 800 mm.
The aim of this case study was to develop a methodology for predicting off-center loading in a transfer die set using a commercially available finite element (FE) software package (AutoForm R8 in this case), and to estimate the forces on the four columns of the press. The off-center loading calculation was done only at bottom dead center (BDC).
Develop a Methodology. The methodology developed through this case study involved five steps:
- Calculate the net load (sum of all forming and cutting loads) for each station at BDC.
- Locate the net load (point B in Figure 3) at BDC. Divide the total moment about a known reference point (point A in Figure 3) produced in a station by the corresponding total force to obtain the location of net load in the station (distance D in Figure 3).
- Determine the distance of net force location for each station from the press center (see Figure 4).
- Multiply the net load for each station (determined in Step 1) by the corresponding distance of these net forces for each station (determined in Step 3) to calculate the moment produced by each station at BDC. Add the moments produced by each station to obtain the off-center loading in the press at BDC.
- Compensate for the off-center loading by using the “false load” method. Install nitrogen cylinders at the extreme end of the transfer die to maximize the moment produced by each nitrogen cylinder. Divide the total moment caused by off-center loading by the distance from press center to the nitrogen cylinder to determine the total force required. Divide this total force by the force capacity of each nitrogen cylinder for the total number of cylinders required. Other methods for balancing the off-center loading can be found in Part 1 in the September/October 2019 issue.
Estimate Forces. Researchers divided the net moment on the press by the net force (sum of forces on all stations) to obtain the distance of net force (D1 and D2 in Figure 5) from the press center. To calculate the forces on the four columns, the net force (F) and the value of distances (D1 and D2) can be substituted in the formulas below:
- Force on post 1 (F1) = [F⋅(L+D1)⋅(W-D2)]/4⋅L⋅W
- Force on post 2 (F2) = [F⋅(L+D1)⋅(W+D2)]/4⋅L⋅W
- Force on post 3 (F3) = [F⋅(L-D1)⋅(W+D2)]/4⋅L⋅W
- Force on post 4 (F4) = [F⋅(L-D1)⋅(W-D2)]/4⋅L⋅W
- D1= Distance of net force location from press center in feeding direction
- D2= Distance of net force location from press center in transverse direction
- 2L= Length of the press bolster in feeding direction
- 2W = Width of the press bolster in transverse direction
Case Study Results
Figure 6 shows the calculated values of net force, force location from press center, and the moment produced by each station for this case study. To compensate for the moment produced by off-center loading, researchers installed 11 nitrogen cylinders, each producing 22 tons of force, at the extreme end of the transfer die set and balanced the press.
This methodology also can be used to predict off-center loading in a transfer die set for simulations developed in an alternative FE package, such as PAM-STAMP. AutoForm R8 has the capability to directly calculate the off-center loading in a progressive die.
About the Authors
David Diaz-Infante, Dr.
250 W 5th St.
Minster, OH 45865
o 419 628 2331, d 419 501 1890, m 419 733 7971
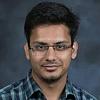
Hitansh Singhal
Graduate Student - Center for Precision Forming
Jamie Bowman
President
55 Sinclair Blvd.
Brantford, ON N3S 7X6 Canada
(800)-250-3004
Neil Parker
Engineering Manager
55 Sinclair Blvd.
Brantford, ON N3S 7X6 Canada
(800)-250-3004
Related Companies
subscribe now
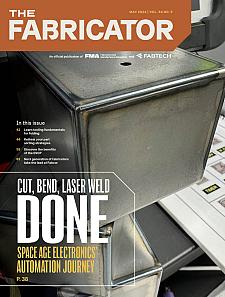
The Fabricator is North America's leading magazine for the metal forming and fabricating industry. The magazine delivers the news, technical articles, and case histories that enable fabricators to do their jobs more efficiently. The Fabricator has served the industry since 1970.
start your free subscription- Stay connected from anywhere
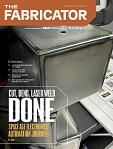
Easily access valuable industry resources now with full access to the digital edition of The Fabricator.
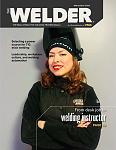
Easily access valuable industry resources now with full access to the digital edition of The Welder.
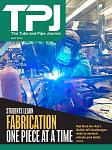
Easily access valuable industry resources now with full access to the digital edition of The Tube and Pipe Journal.
- Podcasting
- Podcast:
- The Fabricator Podcast
- Published:
- 04/30/2024
- Running Time:
- 53:00
Seth Feldman of Iowa-based Wertzbaugher Services joins The Fabricator Podcast to offer his take as a Gen Zer...
- Industry Events
Pipe and Tube Conference
- May 21 - 22, 2024
- Omaha, NE
World-Class Roll Forming Workshop
- June 5 - 6, 2024
- Louisville, KY
Advanced Laser Application Workshop
- June 25 - 27, 2024
- Novi, MI
Precision Press Brake Certificate Course
- July 31 - August 1, 2024
- Elgin,