Contributing Writer
- FMA
- The Fabricator
- FABTECH
- Canadian Metalworking
Categories
- Additive Manufacturing
- Aluminum Welding
- Arc Welding
- Assembly and Joining
- Automation and Robotics
- Bending and Forming
- Consumables
- Cutting and Weld Prep
- Electric Vehicles
- En Español
- Finishing
- Hydroforming
- Laser Cutting
- Laser Welding
- Machining
- Manufacturing Software
- Materials Handling
- Metals/Materials
- Oxyfuel Cutting
- Plasma Cutting
- Power Tools
- Punching and Other Holemaking
- Roll Forming
- Safety
- Sawing
- Shearing
- Shop Management
- Testing and Measuring
- Tube and Pipe Fabrication
- Tube and Pipe Production
- Waterjet Cutting
Industry Directory
Webcasts
Podcasts
FAB 40
Advertise
Subscribe
Account Login
Search
Taking the heat, keeping the current
Heat sinks provide thermal conductivity, electrical isolation
- By Ken Wesseln
- July 24, 2003
- Article
- Bending and Forming
![]() |
A DaimlerChrysler powertrain control module cover/heat sink assembly needed to be thermally conductive yet electrically isolated. The populated circuit board—one with all components in place—had to be bonded to the heat sink and postcured in a vacuum laminating press. The entire module assembly was to be installed at DaimlerChrysler's electronics plant.
By devising a proprietary system of in-die component insertion, Buhrke Industries, a Tier 1 metal stamper, created thermal conductive and electrically isolated conditions on a 5052 aluminum heat sink assembly for the automotive powertrain control module (see Figure 1).
Root of the Problem
![]() |
Figure 1 Three tin-plated brass ground posts were inserted in-die into this heat sink stamped from 5052 aluminum. The part goes into an electronic powertrain control module on various DaimlerChrysler vehicles. |
Buhrke's first challenge was to address the considerable heat present in the small package of multilayer circuit boards. Because only a 0.004-inch layer of thermoset adhesive lies between the printed circuit board (PCB) and the aluminum heat sink, any contact between the board and the heat sink would fry the PCB.
In a typical electronics system, an epoxy adhesive bonds the circuit board to the stamped aluminum heat sink and powertrain control module cover. The goal was to pull the maximum amount of heat off the PCB without making contact. Various adhesive systems were tested, but the necessary heat reduction was not achieved. An adhesive did help to solve part of the problem because it provided the necessary isolation, but the adhesive did not allow selective conductivity. The PCB had to be grounded to the module to provide electrical isolation.
Soldering and hard-brazing as secondary operations were explored but were not viable options because they were not compatible with the aluminum substrate. Also, cost projections were about $250,000 annually.
Turning Down the Heat
After testing components, the stamper suggested a ground postsoldering concept. DaimlerChrysler engineers suggested a copper plate, which wasn't a cost-effective option. After considerable trial and error, the project team recommended inserting several tin-plated brass ground posts into the heat sink. The tin plating solved the brass and aluminum incompatibility with soldering yet still provided sufficient electrical isolation on the heat sink.
The other grounding systems under review were mechanical, including screws through the aluminum and a drawn housing to interface with the solder pads, as well as cold bonding of the brass and aluminum. All were found to be unreliable.
The grounding location was near the outside edge of the PCB. Buhrke's solution brought the ground posts closer to the connectors for better electromagnetic interference and radio frequency interference reduction.
Positioning was the second challenge. Ground post height, diameter, parallelism, and location all were major concerns.
The stamping team looked at DaimlerChrysler's concerns about precision and accuracy of placement and high-speed run time. The ground post, which measured 0.79 mm tall, had to maintain a ±0.13-mm clearance on the top of the heat sink and a zero clearance on its back side for proper soldering.
![]() |
Figure 2 A stamping die with vibratory bowl feed inserts three tin-plated brass ground posts into a heat sink. The vibratory bowl feeds components into a nesting channel, where a proprietary Buhrke Industries feed system inserts the ground posts to tight tolerances. |
The team devised a vibratory bowl feed and nesting channel in-die system for inserting three ground posts into the heat sink (see Figure 2). A system of cams pushed the three ground posts into their proper position in-die.
Automation of the system overcame the customer's third challenge of eliminating labor from the assembly process. The three ground posts were precisely inserted in the heat sink at a rate 50 times faster than a conventional, labor-intensive, and less accurate secondary hard operation, according to Buhrke.
The process automated the assembly and the inspection processes. Nine electronic sensors in each press checked the force and positioning height of the ground posts, during and after insertion, into the heat sink in-die (see Figure 3).
![]() |
Figure 3 Buhrke stamps the heat sink with in-die ground posts on a 150-ton press. Nine sensors check the ground post insertion force, height, position, and presence in-process. |
Piezoelectric force measurement, a method used to translate mechanical movement to electrical movement, and conventional proximity sensors precisely monitored all aspects of this process, including the height and position of the ground post, and measured the dimensional accuracy of the post to ensure a good solder joint during subsequent assembly.
The Path Least Traveled
Previously this application had substantial costs related to heat sinking the components on the module. The radio frequency (RF) ground from the PCB had to be routed into the housing through a RF shield soldered to the board, then to the vehicle chassis through screws in sheet metal brackets. To cut costs, Buhrke suggested using RF ground posts to bond the PCB directly to the heat sink, with the solder liquefying around the posts.
An overall total seal was achieved once the module connector was in place. This eliminated the RF ground to the chassis and related problems, such as tachometer flutter. The mounting screws in the chassis now contacted the aluminum heat sink, achieving the shortest possible RF ground path.
A documented $1 million savings over the life of the program was achieved because of the in-die component insertion system.
Ken Wesseln, vice president of sales; Harold Breen, account manager; Paul Kozlowski, director of tooling; and Keith Krutz, process improvement manager work for Buhrke Industries Inc., 511 W. Algonquin Road, Arlington Heights, IL 60005-4499, 847-981-7550, fax 847-981-0772, info@buhrke.com, www.buhrke.com.
DaimlerChrysler Corp., Auburn Hills, MI 48236-2766, 248-576-5741, fax 248-576-4742, www.daimlerchrysler.com.
About the Author
subscribe now
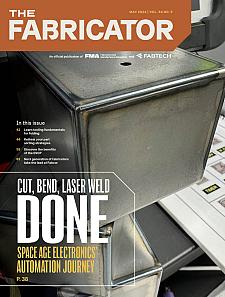
The Fabricator is North America's leading magazine for the metal forming and fabricating industry. The magazine delivers the news, technical articles, and case histories that enable fabricators to do their jobs more efficiently. The Fabricator has served the industry since 1970.
start your free subscription- Stay connected from anywhere
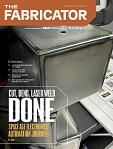
Easily access valuable industry resources now with full access to the digital edition of The Fabricator.
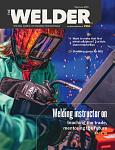
Easily access valuable industry resources now with full access to the digital edition of The Welder.
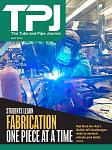
Easily access valuable industry resources now with full access to the digital edition of The Tube and Pipe Journal.
- Podcasting
- Podcast:
- The Fabricator Podcast
- Published:
- 05/14/2024
- Running Time:
- 62:12
Cameron Adams of Laser Precision, a contract metal fabricator in the Chicago area, joins the podcast to talk...
- Trending Articles
Why employee-owned companies make sense in manufacturing
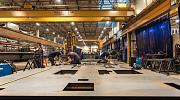
What software automation means for custom fabrication
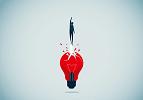
Nucor’s weekly steel price announcement continues to rattle markets
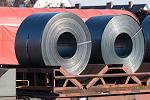
Press brakes, panel benders, and flat blank calculations
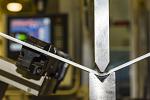
Washington artist creates life-size elk sculptures
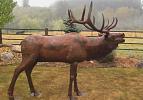
- Industry Events
Laser Welding Certificate Course
- May 7 - August 6, 2024
- Farmington Hills, IL
World-Class Roll Forming Workshop
- June 5 - 6, 2024
- Louisville, KY
Advanced Laser Application Workshop
- June 25 - 27, 2024
- Novi, MI
Precision Press Brake Certificate Course
- July 31 - August 1, 2024
- Elgin,