Editor-in-Chief
- FMA
- The Fabricator
- FABTECH
- Canadian Metalworking
Categories
- Additive Manufacturing
- Aluminum Welding
- Arc Welding
- Assembly and Joining
- Automation and Robotics
- Bending and Forming
- Consumables
- Cutting and Weld Prep
- Electric Vehicles
- En Español
- Finishing
- Hydroforming
- Laser Cutting
- Laser Welding
- Machining
- Manufacturing Software
- Materials Handling
- Metals/Materials
- Oxyfuel Cutting
- Plasma Cutting
- Power Tools
- Punching and Other Holemaking
- Roll Forming
- Safety
- Sawing
- Shearing
- Shop Management
- Testing and Measuring
- Tube and Pipe Fabrication
- Tube and Pipe Production
- Waterjet Cutting
Industry Directory
Webcasts
Podcasts
FAB 40
Advertise
Subscribe
Account Login
Search
The pace of bending innovation picks up
Bystronic introduces its Mobile Bending Cell to the North American market
- By Dan Davis
- September 3, 2017
- Article
- Bending and Forming
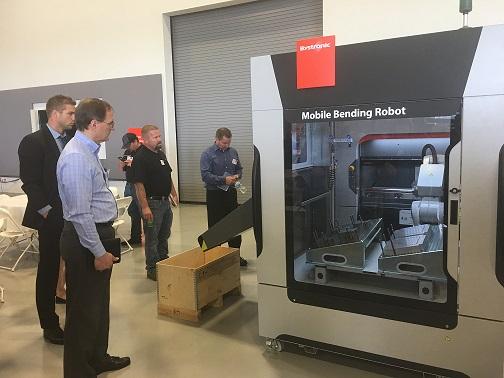
Figure 1. Bystronic’s Mobile Bending Cell can be added to the front of its stand-alone Xpert 40 press brake to create an automated bending cell. It is designed to be removed quickly if the fabricator wishes to revert the brake back to its manual format.
“Never before in history has innovation offered promise of so much to so many in so short a time.”
That’s a quote from Bill Gates, founder of Microsoft. Brody Fanning, vice president, sales, Bystronic Inc., shared it with fabricators attending the premier event for the company’s new Mobile Bending Cell on Sept. 13. To further prove the point, Fanning recapped the last seven years as they relate to Bystronic’s innovation evolution:
- In 2010 Bystronic introduced its first fiber laser in the North American market. The 2-kW laser was seen as an alternative tool for fabricators that processed thin sheet metal. The 4-kW CO2 laser cutting machine was the king of the mountain in the world of metal fabricating.
- In 2011 Bystronic unveiled 3- and 4-kW fiber laser cutting machines.
- In 2014 a 6-kW fiber laser not only was redefining fast cutting in sheet metal applications, but also cutting at twice the speed of CO2 lasers on 0.25-in. plate.
- In 2016 the company introduced 8- and 10-kW power sources, which made these fiber laser cutting machines the most suitable cutting alternative across various metals and thicknesses.
So the laser market has been turned upside down in seven years. In fact, Fanning said that Bystronic now is selling only a handful of CO2 lasers per year to shops that process a lot of 0.625- to 0.750-in. plate.
Just what kind of an impact has this technology made in that time? It’s totally changed the way shops approach quoting and fabricating. Fanning shared the story of a stamping company that got into laser cutting about the same time that fiber lasers were making their debut. The company used to push jobs of 5,000 parts or more toward the stamping press. When the 6-kW fiber laser debuted, investing in stamping tooling for a job could only be justified when volumes reached 20,000. Today, with the 10-kW fiber laser, the same company can produce jobs reaching 50,000 parts more economically on the laser bed than in the stamping press.
That leaves a question that a lot of metal fabricators are currently asking themselves: What do you do about the forming now?
“People have been laser cutting unattended for years on overnight shifts,” Bystronic President Bob St. Aubin said. “Why can’t you do that with bending?”
That’s what the Mobile Bending Cell (see Figure 1) is meant to address. It attaches to the company’s Xpert 40 press brake, which made its debut in 2014.
The press brake is designed to be mobile as well. Weighing 8,818 lbs., it can be moved with a typical lift truck, and after being plugged in and connected to the internet, it can be running in about seven minutes, according to Bystronic officials. The 44-ton brake can bend lengths up to 40.5 in. and has an open height of 20.2 in.
The Mobile Bending Cell connects directly to the front of the Xpert 40. Two Bystronic technicians rolled the automated unit, which includes a robotic arm, from the back of the showroom, connected it to the press brake, and had it producing parts in just under nine minutes.
“The concept here is that it’s as easy as hooking a boat to your truck,” Fanning said.
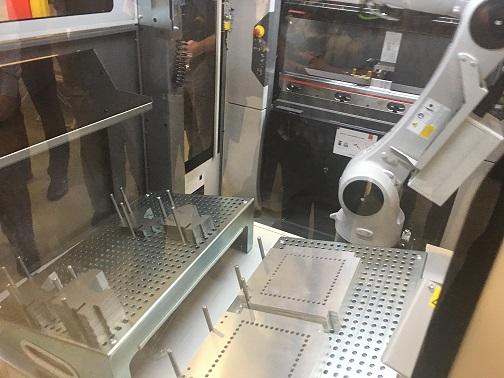
Figure 2. The reference tables in the bending cell can hold multiple blanks so the robot can run several jobs unattended.
The automated cell can handle blanks up to 11.8 by 27.5 in. and 12 lbs. The robot can use either mechanical pinchers or suction cups to pick up the parts. Finished parts must fit within a 5- by 23-in. window to exit the cell through a slot on its side.
The cell includes a reference table where blanks are located and a regripping station where the robot can place the part as it repositions its grip for further bending. During the demonstration at the open house, the robot was processing a seven-bend part.
Fanning said that this automation is meant to help those fabricators looking for a productivity boost where they currently aren’t getting it. The ideal situation is a fabricator that uses the Xpert 40 during the day for complex, short runs of parts and the Mobile Bending Cell on the night shift for simpler, high-volume runs. Disconnecting the automated cell from the press brake takes only about five minutes, according to Fanning.
Fabricators interested in seeing this new automated cell will have the chance at FABTECH 2017 in Chicago, Nov. 6-9.
About the Author
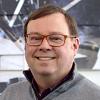
Dan Davis
2135 Point Blvd.
Elgin, IL 60123
815-227-8281
Dan Davis is editor-in-chief of The Fabricator, the industry's most widely circulated metal fabricating magazine, and its sister publications, The Tube & Pipe Journal and The Welder. He has been with the publications since April 2002.
Related Companies
subscribe now
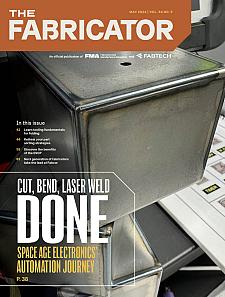
The Fabricator is North America's leading magazine for the metal forming and fabricating industry. The magazine delivers the news, technical articles, and case histories that enable fabricators to do their jobs more efficiently. The Fabricator has served the industry since 1970.
start your free subscription- Stay connected from anywhere
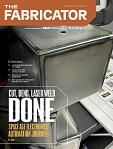
Easily access valuable industry resources now with full access to the digital edition of The Fabricator.
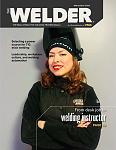
Easily access valuable industry resources now with full access to the digital edition of The Welder.
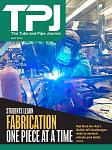
Easily access valuable industry resources now with full access to the digital edition of The Tube and Pipe Journal.
- Podcasting
- Podcast:
- The Fabricator Podcast
- Published:
- 04/30/2024
- Running Time:
- 53:00
Seth Feldman of Iowa-based Wertzbaugher Services joins The Fabricator Podcast to offer his take as a Gen Zer...
- Industry Events
Pipe and Tube Conference
- May 21 - 22, 2024
- Omaha, NE
World-Class Roll Forming Workshop
- June 5 - 6, 2024
- Louisville, KY
Advanced Laser Application Workshop
- June 25 - 27, 2024
- Novi, MI
Precision Press Brake Certificate Course
- July 31 - August 1, 2024
- Elgin,