Servo Press Scientist
- FMA
- The Fabricator
- FABTECH
- Canadian Metalworking
Categories
- Additive Manufacturing
- Aluminum Welding
- Arc Welding
- Assembly and Joining
- Automation and Robotics
- Bending and Forming
- Consumables
- Cutting and Weld Prep
- Electric Vehicles
- En Español
- Finishing
- Hydroforming
- Laser Cutting
- Laser Welding
- Machining
- Manufacturing Software
- Materials Handling
- Metals/Materials
- Oxyfuel Cutting
- Plasma Cutting
- Power Tools
- Punching and Other Holemaking
- Roll Forming
- Safety
- Sawing
- Shearing
- Shop Management
- Testing and Measuring
- Tube and Pipe Fabrication
- Tube and Pipe Production
- Waterjet Cutting
Industry Directory
Webcasts
Podcasts
FAB 40
Advertise
Subscribe
Account Login
Search
Understanding press tonnage
Deformation, capacity, rating, load, forward and reverse tonnage in stamping operations
- By David Diaz-Infante, Dr.
- June 10, 2021
- Article
- Bending and Forming
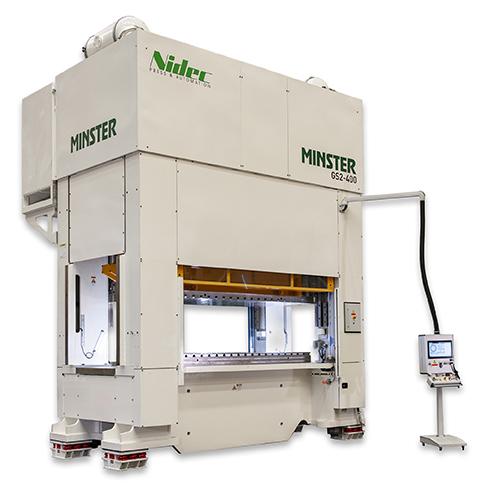
In stamping operations, the press must overcome a material’s resistance to deformation and other forces opposing the press motion. The forces, or tonnage that a press can withstand and apply should be higher than those required by the forming process. To size a press properly, stampers should understand these different but related concepts.
Every material shows certain resistance to being deformed. In stamping operations, the press must overcome this resistance and other forces opposing the press motion. In other words, the forces or tonnage that a press can withstand and apply should be higher than those required by the forming process. To size a press properly, stampers should understand these different but related concepts.
Press Tonnage Capacity
Even though it may not be obvious to the naked eye, every press goes through elastic deflections during a forming process. The maximum tonnage that a press can withstand without compromising any of its components is called press tonnage capacity. However, the tonnage capacity is valid only to describe the press’s structural limits under the forward tonnage required to form the part (when connections between the shaft and the drive are in compression and uprights are in tension). Thus, while the tonnage capacity typically is the first indicator of the press size or strength, additional aspects bear consideration.
Snap-through and Reverse Tonnage
In addition to forward tonnage, snap-through and reverse tonnage should be taken into account (see Figure 1). Often these terms are used incorrectly as synonyms; they are not.
On one hand, snap-through can be defined as the sudden release of stresses that leads to rapid acceleration of the press slide and the connected components, after material breakage.
On the other hand, the reverse tonnage can be defined by the forces creating tension on the connections. Even though both typically occur together, one can exist without the other.
Each is related to different failure modes: Snap-through is related to vibration issues, while reverse tonnage is related to problems with the press components’ elastic limits.
In general, a press’s reverse tonnage capacity is lower than the forward tonnage. A common value for acceptable reverse tonnage is 10% of the tonnage capacity. Depending on the press manufacturer and model, the reverse tonnage capacity can be above 50% of the tonnage capacity. This is important to consider because, in certain cases, reverse tonnage could be the limiting factor, even when the full forward press capacity has not been met.
Typically, snap-through and reverse tonnage increase with increasing material thickness and strength, or with increasing press speed. Finally, while reverse tonnage can be observed to some extent using a tonnage monitor system, vibration analysis methods are required to capture snap-through.
Off-center Load
Typically, the press tonnage capacity is given for centered loads when both connections take similar forces. For example, they might absorb up to 200 tons per connection in a 400-ton press with two connections (see Figure 2).
However, under off-center loading conditions, the connections do not absorb the same forces. For this reason, the tonnage capacity decreases as the resultant load deviates from the press center line. This is important to consider, because in some scenarios, the connections are overloaded even when the forming tonnage is below the tonnage capacity, compromising the press structure. The resultant load magnitude and location should be calculated and compared with the press off-center load capacity.
Each press has its own behavior under off-center loads, depending on press construction, number of connections, and guiding mechanisms. Presses with one connection have the lowest resistance to tilting because of off-center loads. Presses with two connections add resistance on the left-to-right direction, while those with four connections also add support on the front-to-back direction.
Concentrated Loads
In general, the tonnage capacity is valid when a percentage of the die space—at least 66% of the bed length—supports the load. The elastic deflections that the press manufacturer indicates on the spec sheet correspond to these conditions.
The OEM’s specified elastic deflections may not be valid if loads are concentrated in a smaller portion of the bed. This is the case with concentrated loads. For concentrated loads, it is recommended that the tonnage capacity be reduced to maintain elastic deflections within specified limits. This reduction can be calculated simply by using the principle of ratios for the conditions that the manufacturer indicated. For example, if 100% of the tonnage capacity corresponds to a 66% usage of bed length, 50% of the tonnage capacity would correspond to a 33% usage of bed length—half the original values.
Tonnage Available
Even though a press can withstand the full tonnage capacity at any time, it may not be able to apply full tonnage throughout the stroke. This is the case for mechanical presses that use the slider-crank mechanism—the most common type of mechanical presses. Because of the nature of this mechanism, the available tonnage increases as the rotation angle gets closer to 0 and 180 degrees—top dead center (TDC) and bottom dead center (BDC), respectively.
In theory, the available tonnage would reach an infinite value at BDC and TDC. In reality, this is not possible, because the press structure would fail at some point above its capacity.
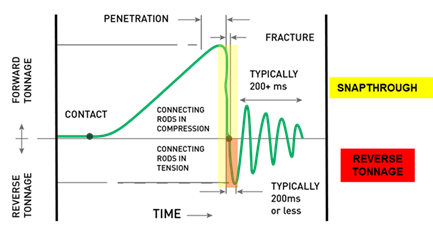
Typically, snap-through and reverse tonnage increase with increasing material thickness and strength, or with increasing press speed.
The distance above BDC where a slider-crank press reaches its full capacity is called the rating point. The rating point also is considered to be one of the main criteria for press selection. However, its usefulness varies with the forming process requirements. Therefore, selecting a press based just on its tonnage capacity or its rating point may not be the best approach. Instead, the available tonnage curve should be used. It describes the tonnage that a press can apply at any position in the stroke (see Figure 3).
Stampers should be aware that two presses of the same tonnage capacity and same rating point may have different available tonnage curves. This difference is related mainly to the press stroke and the press’s torque capacity. For constant torque (such as the same motor, clutch, and other components in the transmission), the shorter the total press stroke, the higher the available tonnage curve (see Figure 4).
While a press with a longer stroke provides flexibility to accommodate deeper draws, it comes with a trade-off in terms of available tonnage. The tonnage capacity would remain unaffected by the stroke length because it depends on the structural capacity of the press and its components.
Tonnage Required
A common practice among stampers is to evaluate the feasibility of a job by comparing the estimated peak load of the process with the press tonnage capacity. Even when this is an acceptable quick estimation, it is not the proper methodology. The required tonnage should always be below the available tonnage curve of the press. Therefore, it is important to consider the complete evolution of the tonnage and not only the peak value.
Available equations used for tonnage estimation only provide peak tonnage as opposed to the complete forming tonnage versus stroke curve. Therefore, the estimation of such a curve relies on the formability engineer’s experience; the use of finite element analysis (FEA) simulations is a powerful tool for this task. As a guideline, Figure 5 shows typical tonnage versus stroke curves for various sheet metal forming operations.
Excessive Tonnage
There are two different ways of exceeding press tonnage, and the consequences also are different.
If the tonnage required exceeds the available tonnage curve before the rating point, the driving system may fail and the press may stop. The clutch may slip (also known as “press sticking at the bottom”), or the motor can overheat. This is a common observation on the shop floor. Overloading the press above the rating point affects components under torsion stresses the most.
On the other hand, major failures on the whole press structure can occur if the tonnage exceeds its tonnage capacity.
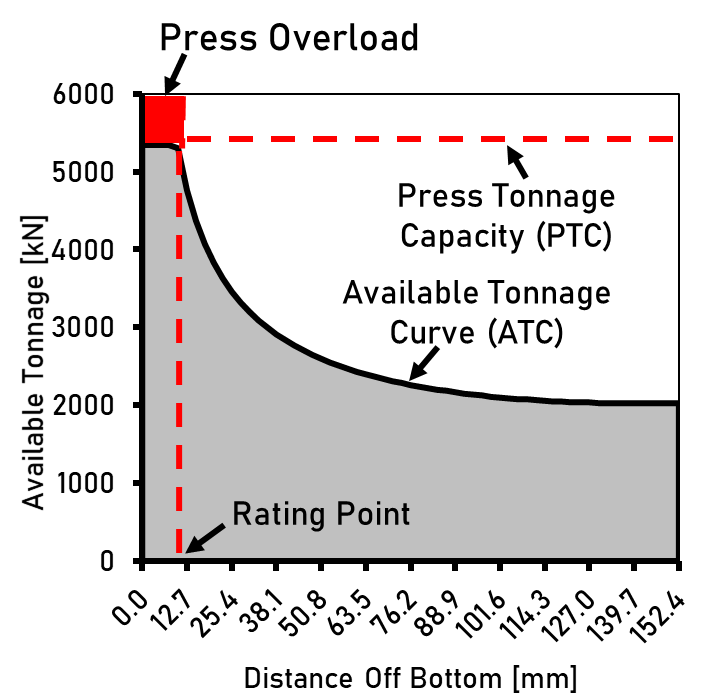
Selecting a press based on its tonnage capacity alone is not optimal. Instead, use the available tonnage curve because it indicates the tonnage that a press can apply at any position in the stroke.
Selecting the Correct Press
As mentioned previously, the forces or tonnages that a press can withstand and apply should be higher than those required by the forming process. To ensure that the correct press is used, the following steps are recommended:
1. Find the available tonnage curve for the press. It can be approximated with a rule of thumb (This is not a substitute for the real available tonnage curve, which can be discussed with the press manufacturer): One-third of press tonnage capacity at a distance off bottom (DOB) equal to one-third of the press stroke. Half of press tonnage capacity at a DOB equal to one-tenth of the press stroke. Full press tonnage capacity at the rated DOB (rating point) and below.
2. Find the tonnage requirements from the process throughout the stroke and compare them with the available tonnage curve. While there are online calculators and relatively simple equations to estimate forming (forward) tonnages, this becomes a difficult task when forming complex geometries. An FEA simulation is recommended at this point.
3. Estimate the off-center loading conditions of the process and make sure they are within the off-center load capacity of the press for the desired parallelism based on die requirements. In general, the die cannot handle as much off-center loading as the press can. Process redesign may be needed to balance the operation within the press.
4. Identify any possible concentrated load (high tonnages and small die sets) and verify that it is acceptable based on the press manufacturer’s recommendations.
5. Consider reverse tonnage and snap-through. While there is not a practical way to calculate reverse tonnage beforehand, it typically is 10% to 25% of the forward tonnage. However, values as high as 50% of the forward tonnage have been observed. If the press is not sufficiently robust, it may need to be derated to 80% of the tonnage capacity in blanking or piercing operations. If excessive reverse tonnage occurs, reducing the speed can help.
6. Compare the energy required to form the part with press capabilities.
In conclusion, a proper understanding of forces involved in forming is crucial when selecting and maintaining a press. Although the negative effects of press misusage are not always immediately visible, in the long run these effects lead to more frequent downtimes and increased maintenance costs on the press. While stampers may have enough experience dealing with tonnage issues, it is always a good idea to work together with the press manufacturer to optimize the operation.
About the Author
David Diaz-Infante, Dr.
250 W 5th St.
Minster, OH 45865
o 419 628 2331, d 419 501 1890, m 419 733 7971
Related Companies
subscribe now
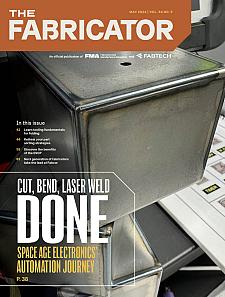
The Fabricator is North America's leading magazine for the metal forming and fabricating industry. The magazine delivers the news, technical articles, and case histories that enable fabricators to do their jobs more efficiently. The Fabricator has served the industry since 1970.
start your free subscription- Stay connected from anywhere
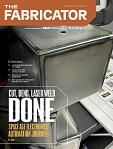
Easily access valuable industry resources now with full access to the digital edition of The Fabricator.
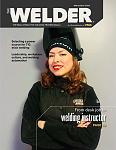
Easily access valuable industry resources now with full access to the digital edition of The Welder.
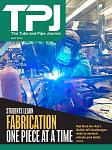
Easily access valuable industry resources now with full access to the digital edition of The Tube and Pipe Journal.
- Podcasting
- Podcast:
- The Fabricator Podcast
- Published:
- 04/30/2024
- Running Time:
- 53:00
Seth Feldman of Iowa-based Wertzbaugher Services joins The Fabricator Podcast to offer his take as a Gen Zer...
- Industry Events
Pipe and Tube Conference
- May 21 - 22, 2024
- Omaha, NE
World-Class Roll Forming Workshop
- June 5 - 6, 2024
- Louisville, KY
Advanced Laser Application Workshop
- June 25 - 27, 2024
- Novi, MI
Precision Press Brake Certificate Course
- July 31 - August 1, 2024
- Elgin,