Product Manager, ShopFloorConnect
- FMA
- The Fabricator
- FABTECH
- Canadian Metalworking
Categories
- Additive Manufacturing
- Aluminum Welding
- Arc Welding
- Assembly and Joining
- Automation and Robotics
- Bending and Forming
- Consumables
- Cutting and Weld Prep
- Electric Vehicles
- En Español
- Finishing
- Hydroforming
- Laser Cutting
- Laser Welding
- Machining
- Manufacturing Software
- Materials Handling
- Metals/Materials
- Oxyfuel Cutting
- Plasma Cutting
- Power Tools
- Punching and Other Holemaking
- Roll Forming
- Safety
- Sawing
- Shearing
- Shop Management
- Testing and Measuring
- Tube and Pipe Fabrication
- Tube and Pipe Production
- Waterjet Cutting
Industry Directory
Webcasts
Podcasts
FAB 40
Advertise
Subscribe
Account Login
Search
Is it time to invest in new fabricating equipment?
Production tracking software can assess how current machines are performing before you add more
- By James Finnerty
- April 11, 2024
- Article
- Manufacturing Software
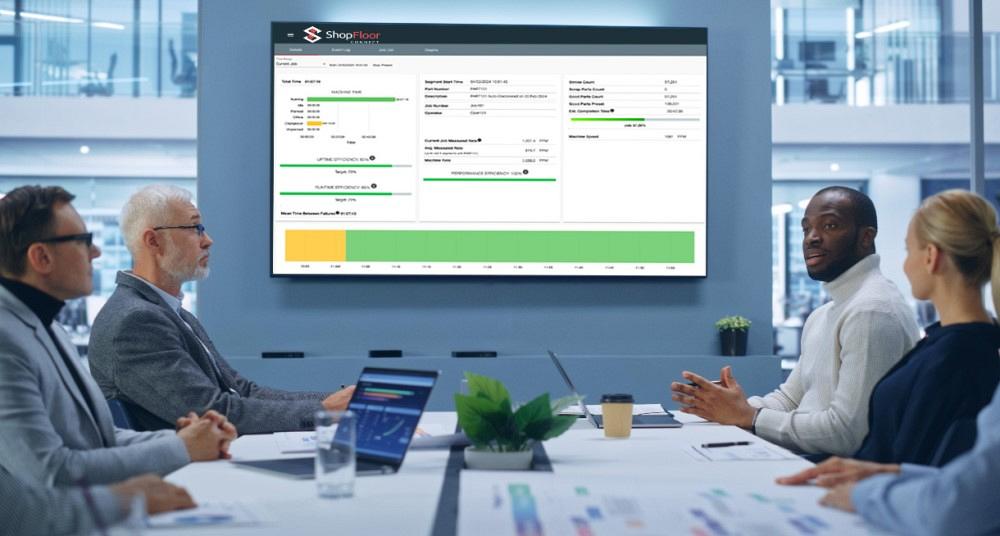
Production tracking software can help a metal fabricating company overcome the shortcomings of manual data collection.izusek/E+
Fabricating shops are constantly striving to improve productivity, minimize downtime, and enhance operational efficiency. While procuring a new laser cutting machine or turret punch press might seem like the best way to increase productivity to take on new business, the first step is to get an accurate view of how the shop is currently performing—before adding new equipment.
So how can you gain insight into how your shop is really doing? Many manufacturers collect shop floor efficiency and machine utilization data manually, and an operator then enters that data into a production tracking system. Unfortunately, because of three common problems with manual collection of shop floor data—untimeliness, inaccuracy, and bias—that data might not be as reliable as it could be.
Automating Production Tracking
To overcome these limitations of manual data collection, production tracking software is available that provides broad visibility into the overall production process and offers an overview of equipment utilization.
Data Collection and Reporting. This type of software enables real-time data collection from diverse manufacturing equipment, capturing critical information such as production rates, cycle times, and downtime occurrences. It offers seamless integration with a variety of machines, allowing for comprehensive monitoring across the shop floor.
This data, presented in intuitive dashboards, charts, and graphs, can help you identify bottlenecks, pinpoint inefficiencies, and make data-driven decisions to optimize your processes.
Overall Equipment Effectiveness (OEE) Enhancement. OEE is a key metric that measures the efficiency of manufacturing operations. By analyzing machine utilization, downtime, and production rates, the software provides actionable insights to improve OEE, which can help you increase productivity, reduce waste, and enhance profitability.
Connect Your Factory Production
OEE and data collection software collects downtime and production efficiency data from virtually every machine, displays data in real-time, and produces indispensable manufacturing reports. Look for a solution that takes advantage of existing network infrastructures, providing the ability to gather valuable production data. Once collected, information is stored in a scalable database and is available for use by other software such as ERP programs. Initially, an automated factory data collection system provides huge benefits by identifying the leading causes of waste; allowing manufacturers to focus resources where they can have the biggest impact on efficiency. After a time, when efficiency is improved to the point where gains start to flatten out, the real-time production data display capabilities become more important in maintaining your newfound levels of efficiency by allowing the appropriate personnel to promptly respond to downtime events. The visual factory also gives managers the opportunity to more quickly detect areas that are starting to lag behind, allowing them to make more informed personnel deployment and scheduling decisions.
The following lists some of the important considerations, features and functionality to look for when choosing an OEE/ Data Collection system:
Achieving Automatic Data Collection. To collect accurate, unbiased, and timely data for OEE tracking, as much data as possible must be collected automatically from your machines and/or production lines. To accomplish this, one option is to use an integrator to modify your machine controls to provide production information to the software. A custom system provides flexibility to collect exactly the information that you need, however this flexibility comes at a steep price. The cost to integrate can run into the hundreds of thousands of dollars, and implementation can take years. A more efficient solution is to select a data collection software product that works in conjunction with a machine interface. The machine interface detects when a machine is running, and when it completes a cycle or makes a part (if appropriate). The machine interface may also provide scanner input or menus to enable operators to log in and out, and to specify reasons for downtime when a machine has stopped running. It also provides consistent production data to the software regardless of machine type, and provides an identical operator interface across all machines.
Easy Implementation. Look for solutions that are easy to install, only requiring a web browser and email client, including when installing from remote locations (provided you have remote access to your network). In addition, having access to virtual training can expedite putting the new process into production.
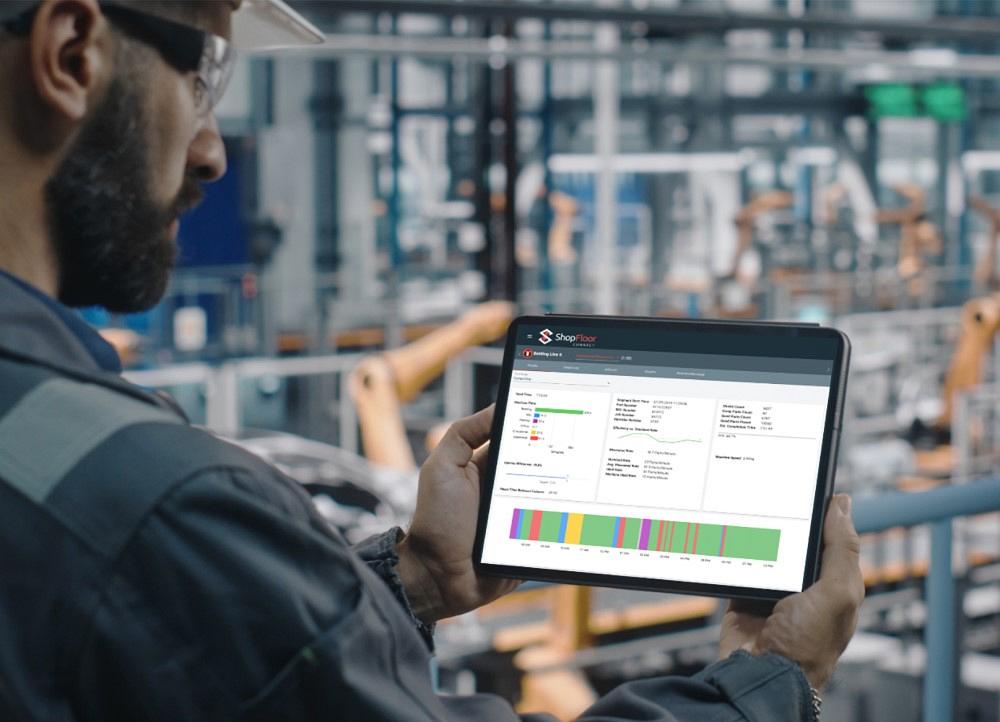
Machine uptime is just one of the metrics that can be tracked with software. Wintriss Controls Group
Easy, Fast Interface. It is important that the machine data collection solution has an intuitive interface that minimizes the interaction required by the operator. Streamlining the process is critical for operators and their management to embrace the solution.
Robust Reporting. The data collected should give Key Performance Indicators (KPIs) in visually appealing reports that can be easily accessed and read on a variety of devices. Also, having browser-based reporting allows for report setup and generation on demand, or for setting up schedules to automatically deliver pre-configured reports. Data from a specified time period, also from specific machines, operators, part numbers (or other important parameters depending on machine type), and/or shift is critical for reporting.
Alert Capability. Having the ability to automatically generate conditional alerts from any machine can significantly increase productivity. Alerts can be a custom text or email message that is sent to selected recipients whenever preset conditions are met at a machine. The alerts can be used to notify an operator when an unattended machine has stopped running, to alert management when a critical customer job goes down, or to summon certain resources when specific conditions exist at a machine – such as automatically notifying a forklift driver when a scrap bin needs to be replaced. Because events can be responded to more quickly, manufacturers can significantly reduce downtime – even on machines where further process-related downtime reductions are considered cost-prohibitive.
Connecting With Success
For several manufacturing companies, data collection for production monitoring has had a transformative effect on operational efficiency and productivity.
A metal fabrication facility faced challenges with identifying bottlenecks and optimizing its production processes. By implementing the software, the fabricator gained real-time visibility into its shop floor operations. The software’s analytics capabilities helped the company identify underutilized machines, streamline workflows, and reduce downtime, resulting in a 15 percent increase in OEE and improved production rates.
Another fabricator offering capabilities such as weldments, assemblies and laser cutting understood the need to measure and track machine downtime, prompting it to implement OEE. With over 35 machines including press brakes, welders, laser and tube cutting machines, saws and more, the manufacturer had substantial opportunity to improve its uptime and throughput. Before installing the software, the company was having difficulty determining why some machines were down. However, after installation a 10 percent increase in productivity was quickly realized, fully returning the software investment in less than three months.
About the Author
James Finnerty
100 Discovery Way, Unit 110
Acton, MA 01720-4483
800-586-8324
Related Companies
subscribe now
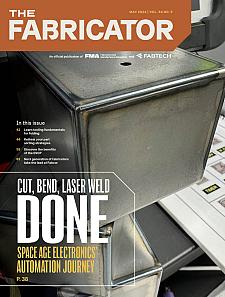
The Fabricator is North America's leading magazine for the metal forming and fabricating industry. The magazine delivers the news, technical articles, and case histories that enable fabricators to do their jobs more efficiently. The Fabricator has served the industry since 1970.
start your free subscription- Stay connected from anywhere
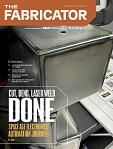
Easily access valuable industry resources now with full access to the digital edition of The Fabricator.
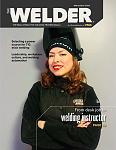
Easily access valuable industry resources now with full access to the digital edition of The Welder.
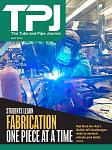
Easily access valuable industry resources now with full access to the digital edition of The Tube and Pipe Journal.
- Podcasting
- Podcast:
- The Fabricator Podcast
- Published:
- 04/16/2024
- Running Time:
- 63:29
In this episode of The Fabricator Podcast, Caleb Chamberlain, co-founder and CEO of OSH Cut, discusses his company’s...
- Trending Articles
Tips for creating sheet metal tubes with perforations
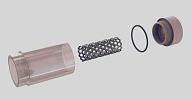
Supporting the metal fabricating industry through FMA
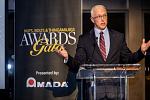
JM Steel triples capacity for solar energy projects at Pennsylvania facility
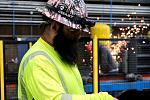
Fabricating favorite childhood memories
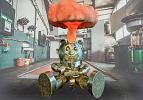
Omco Solar opens second Alabama manufacturing facility
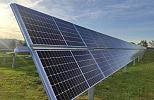
- Industry Events
16th Annual Safety Conference
- April 30 - May 1, 2024
- Elgin,
Pipe and Tube Conference
- May 21 - 22, 2024
- Omaha, NE
World-Class Roll Forming Workshop
- June 5 - 6, 2024
- Louisville, KY
Advanced Laser Application Workshop
- June 25 - 27, 2024
- Novi, MI