Editor-in-Chief
- FMA
- The Fabricator
- FABTECH
- Canadian Metalworking
Categories
- Additive Manufacturing
- Aluminum Welding
- Arc Welding
- Assembly and Joining
- Automation and Robotics
- Bending and Forming
- Consumables
- Cutting and Weld Prep
- Electric Vehicles
- En Español
- Finishing
- Hydroforming
- Laser Cutting
- Laser Welding
- Machining
- Manufacturing Software
- Materials Handling
- Metals/Materials
- Oxyfuel Cutting
- Plasma Cutting
- Power Tools
- Punching and Other Holemaking
- Roll Forming
- Safety
- Sawing
- Shearing
- Shop Management
- Testing and Measuring
- Tube and Pipe Fabrication
- Tube and Pipe Production
- Waterjet Cutting
Industry Directory
Webcasts
Podcasts
FAB 40
Advertise
Subscribe
Account Login
Search
The difference fiber lasers make on the shop floor
Robbins Mfg., Fall River, Wis., is embracing its increased production velocity
- By Dan Davis
- June 28, 2017
- Article
- Cutting and Weld Prep
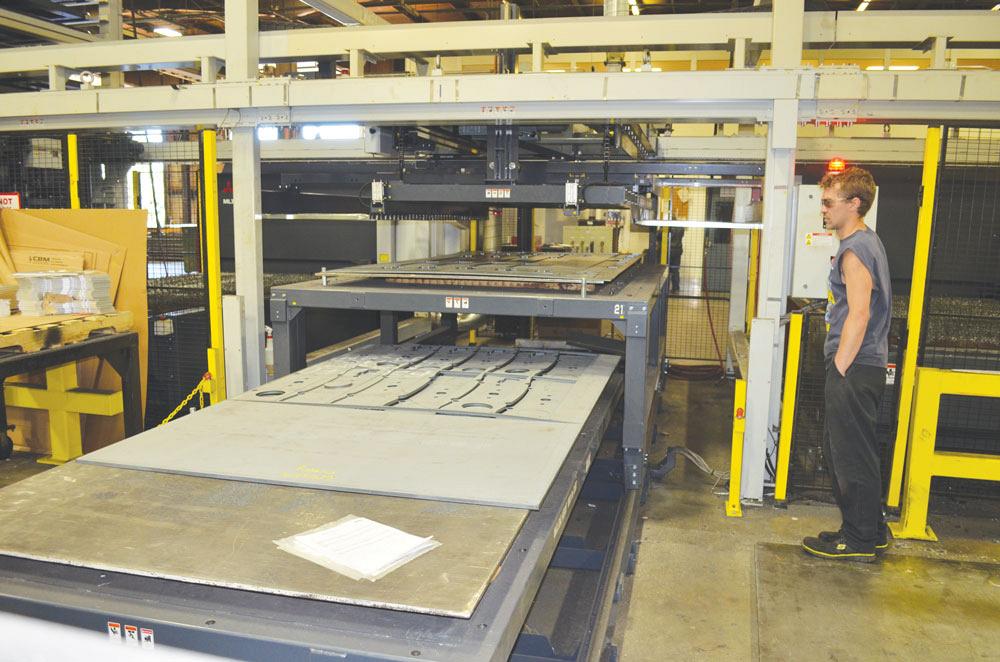
Figure 1
Robbins Mfg. Inc. has two 6,000-W ML 3015 eX-F60 fiber lasers from MC Machinery Systems/Mitsubishi Laser that it uses to cut all sorts of metal in a variety of thicknesses. On this day it was cutting a 0.5-in.-thick titanium alloy.
Since Robbins Mfg. Inc., Fall River, Wis., bought its first plasma and shear in 1989—the best technology available—it has committed to responding in the affirmative to customers’ demands and to keeping up with the latest technology to produce quality parts more quickly and more cost-effectively. That hasn’t changed over the years.
Robbins entered the laser age in the mid-1990s when it purchased its first laser cutting machine. Since that time it has invested in new cutting technology about every five years. Company management believes it is worth the effort, and the fabricating activity in the 300,000-square-foot facility seems to verify that belief. Almost 300 employees are working over three shifts to keep up with jobs from Robbins’ main customers, many of which have dramatically surpassed their own forecasts in early 2017.
Fortunately, Robbins installed two new 6,000-W ML 3015 eX-F60 fiber lasers from MC Machinery Systems/Mitsubishi Laser in December, which has helped them with the expected customer crush that became reality (see Figure 1). The transition to the new technology, which took place over a five-week period (from the time the old CO2
Robbins may have switched out its older CO2 lasers were moved out to when the first part was cut), is something that the shop takes in stride, according to Paul Osterhaus, Robbins’ director of manufacturing.
“I think people embrace the new technology,” Osterhaus said. “They look forward to it. They have been through change, so they know it may be difficult at first. But in the end, the product will be better, and we will be producing it faster. This helps us to offer something new and better to our customers.”
Faster, More Powerful Fiber Cutting
Robbins may have switched out its older CO2 laser cutting machines for new fiber laser technology, but the shop was no newcomer to fiber laser cutting. It installed two 4,000-W NX-F40 fiber lasers, also from MC Machinery Systems/Mitsubishi Laser, roughly three years earlier (see Figure 2). The performance of this latest generation of fiber laser cutting machines was too great to ignore, particularly on thick materials. (Robbins primarily cuts materials between 20 gauge and 1.25 inch thick, but it also churns out a lot of 0.25-in. steel.)
“Once we saw the 6,000-W fibers and how fast they were able to just pierce through thicker materials, we got excited,” said Travis DeBussey, Robbins’ production manager. “We were cutting faster than we were with the CO2
Robbins may have switched out its older CO2, and we were getting the same cut quality.”
Fiber lasers (named so because the laser beam is created using solid-state laser diodes and then delivered to the cutting head with fiber-optic cable) have come a long way in being able to handle the variety of metal thicknesses that a job shop has to tackle on a regular basis. The increased wattage from these power sources and cutting heads that have the ability to adjust the beam mode for thicker materials has made the fiber laser a machine tool capable of addressing all sorts of cutting applications.
These new fiber lasers come with the Zoom cutting head, which is sealed to protect it from the aggressive environment of cutting thick materials. In fact, the cutting head’s design includes an autofocus focal range from 3.75 to 10 in., which for the eX-F60 fiber lasers translates to being able to cut different thicknesses of materials without the need for manual changing of the lenses. In reality, if a laser operator is going to go from 20-ga. to 1-in. material, he only needs to change the nozzle on the machine.
“The ability to go from cutting something like thin stainless to cutting 1-in. material and only having to change out a nozzle for a different cutting condition was one of the biggest things that we noticed,” said Andy Ladwig, Robbins’ laser fabrication manager.
With the new laser cutting machines’ versatility and the 10-shelf automated material towers that feed the equipment (one tower is actually a leftover from an automated CO2 system that was replaced), Robbins now enjoys high productivity on some of its older laser cutting machines. The two NX-F40 fiber lasers, which also have material towers, can be dedicated to cutting similar thin material jobs, which minimizes downtime for lens changeover and refocusing between jobs. Meanwhile, an older CO2 stand-alone Mitsubishi laser can be used for cutting the thick parts, a task at which the machine excels.
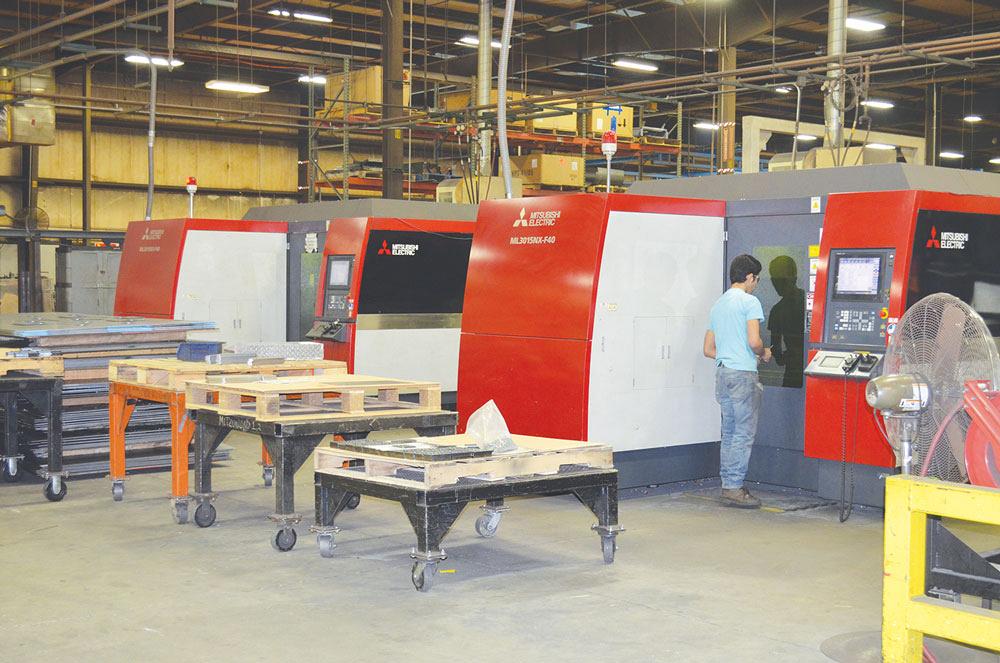
Figure 2
Robbins first migrated away from traditional CO2 laser cutting with the two 4,000-W NX-F40 fiber lasers it purchased about three years ago.
On the programming side of things, DeBussey said the transition to creating nests for the new fiber lasers was smooth. The coding is obviously a bit different, but the programming is designed to be as simple as possible. Nests are created for jobs scheduled for the day, and with the click of a button, the programmer is creating a nest for a specific laser. Functions such as piercing and common-line cutting are all addressed automatically.
After the Parts Are Cut …
Nesting and raw material management and delivery have kept up with the pace at which the new fiber laser cutting machines operate. The rest of the shop has had to adjust, however (see Figure 3).
When the parts and the corresponding skeleton come out of the machine, manual sorting is still necessary. DeBussey said the automated unload systems that he has seen really don’t fit the shop’s high-mix, low-volume work that makes up a majority of its business.
“That’s the next big thing we want to tackle,” DeBussey said. “With the increased speed of the fiber lasers, we have recognized that breaking out parts has become a bottleneck. The fibers are cutting faster, and the unload crews are working as they were previously. That’s the next challenge.”
The first step probably will start with some 5S activities in the laser cutting department. After the manual parts breakout operations have been thoroughly reviewed, the production team can begin to look at options, including material handling technology, that might be useful to expedite the process, DeBussey said.
What about the bending department? Robbins management actually saw that potential bottleneck when it purchased its first fiber laser cutting machines. That’s why it decided to install three 110-ton Amada HD 1003 press brakes with automatic tool changeout features (see Figure 4).
The press brakes, which have an attached tooling library, can make a full tooling changeout in about two minutes, time in which an operator can look for the next job’s parts. Automation retrieves the previous set of tooling, returning it to the library, and replaces it with another. The ATC system has 15 upper racks for tooling and 18 lower racks for the dies.
The press brakes also come with an inline angle measurement system, which the press brake operators use to verify the bend on new parts. DeBussey said they don’t use the angle verification for every part because it would take up too much time.
One of the Amada brakes has all ¼-in. tooling, and the other has 1/8-in. tooling.
This is reflective of a new approach to fabricating jobs, DeBussey said. Instead of simply batching parts coming off the lasers by customer, parts needed for welding, painting, or both are sent to the right press brake for expedited processing.
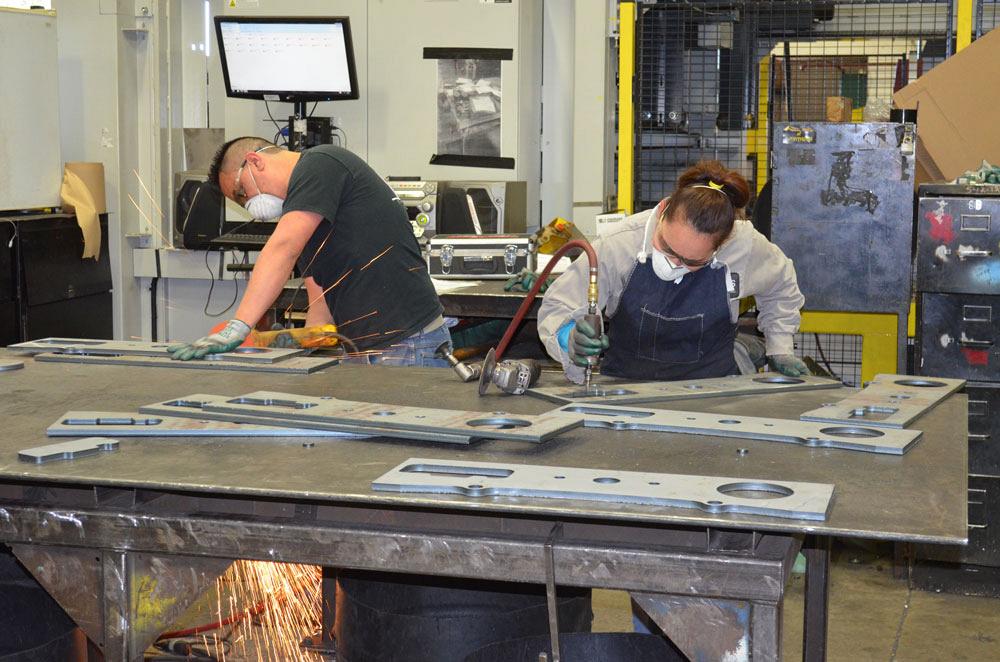
Figure 3
The fiber laser cutting machines produce more parts compared to the output of CO2 lasers, which means employees have to stay on top of breaking parts out of skeletons at an increased pace. The same faster pace affects those involved with secondary finishing activities, such as the edge grinding that takes place on these titanium alloy parts.
“We have reduced our bucket sizes quite a bit to get more through the machines instead of running massive nests that lead to stacked parts,” he said. “With that bending technology on the back end and the fibers on the front, our bucket sizes are smaller, and we can compete with the best of the high-mix, low-volume shops.”
Farther Downstream
Robbins is really no different from other metal fabricators in the U.S. If the company could find the right welders, it would find a place for them almost immediately.
In the meantime, it works with what it has. The metal fabricator currently has about 70 welders working over multiple shifts. Where it can, the company uses one of its eight robotic welding cells (see Figure 5). DeBussey said that they continue to look at automated welding technology for various jobs, including ones that may have the tight tolerances often associated with robotic welding (see Figure 6).
Unlike other metal fabricators, Robbins does operate a large-scale finishing operation. It has two full-scale finishing lines, one for liquid paint and one for powder coating, that both utilize the same seven-stage pretreatment system. It also operates two batch application booths for limited runs.
DeBussey said that finishing has gotten particularly challenging as one of its heavy-duty equipment manufacturing customers has shifted from a few standard colors for its products to several different colors that match up with the color schemes of the many large construction firms and rental companies in the U.S. That has led to the need for Robbins to apply as many as 20 different shades of gray.
As with laser cutting, Robbins is going to stay on top of these production challenges with the help of further technology investments. It’s a recipe that’s worked for more than 25 years, and the pace of change isn’t going to slow down anytime soon.
“Culturally, we aren’t going to say ‘no,’” DeBussey said.
Robbins Mfg. Inc., 920-484-4141, www.robbinsmfg.com
MC Machinery Systems Inc./Mitsubishi Laser, 630-616-5920, www.mcmachinery.com
Amada America Inc., 877-262-3287, www.amada.com
About the Author
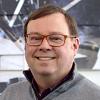
Dan Davis
2135 Point Blvd.
Elgin, IL 60123
815-227-8281
Dan Davis is editor-in-chief of The Fabricator, the industry's most widely circulated metal fabricating magazine, and its sister publications, The Tube & Pipe Journal and The Welder. He has been with the publications since April 2002.
subscribe now
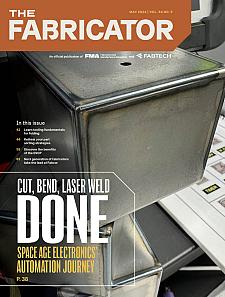
The Fabricator is North America's leading magazine for the metal forming and fabricating industry. The magazine delivers the news, technical articles, and case histories that enable fabricators to do their jobs more efficiently. The Fabricator has served the industry since 1970.
start your free subscription- Stay connected from anywhere
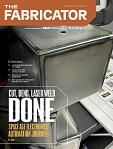
Easily access valuable industry resources now with full access to the digital edition of The Fabricator.
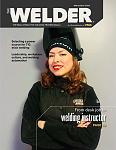
Easily access valuable industry resources now with full access to the digital edition of The Welder.
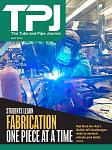
Easily access valuable industry resources now with full access to the digital edition of The Tube and Pipe Journal.
- Podcasting
- Podcast:
- The Fabricator Podcast
- Published:
- 04/30/2024
- Running Time:
- 53:00
Seth Feldman of Iowa-based Wertzbaugher Services joins The Fabricator Podcast to offer his take as a Gen Zer...
- Industry Events
16th Annual Safety Conference
- April 30 - May 1, 2024
- Elgin,
Pipe and Tube Conference
- May 21 - 22, 2024
- Omaha, NE
World-Class Roll Forming Workshop
- June 5 - 6, 2024
- Louisville, KY
Advanced Laser Application Workshop
- June 25 - 27, 2024
- Novi, MI