Editor-in-Chief
- FMA
- The Fabricator
- FABTECH
- Canadian Metalworking
Categories
- Additive Manufacturing
- Aluminum Welding
- Arc Welding
- Assembly and Joining
- Automation and Robotics
- Bending and Forming
- Consumables
- Cutting and Weld Prep
- Electric Vehicles
- En Español
- Finishing
- Hydroforming
- Laser Cutting
- Laser Welding
- Machining
- Manufacturing Software
- Materials Handling
- Metals/Materials
- Oxyfuel Cutting
- Plasma Cutting
- Power Tools
- Punching and Other Holemaking
- Roll Forming
- Safety
- Sawing
- Shearing
- Shop Management
- Testing and Measuring
- Tube and Pipe Fabrication
- Tube and Pipe Production
- Waterjet Cutting
Industry Directory
Webcasts
Podcasts
FAB 40
Advertise
Subscribe
Account Login
Search
Trends in liquid industrial coatings
Fabricators with painting operations should be aware of advances in paint makeup that can lead to stronger corrosion protection and lower application costs
A discussion of industrial coatings for many metal fabricators would be as interesting as watching paint dry.
Most shops aren’t involved in any sort of finishing. If something requires paint, they send it off to a custom coater. For those fabricators that do run paint lines or batch operations, they likely don’t focus on it like they do on their fabrication operations. After all, painting is a value-added activity. They are paid mostly for their fabricating knowledge. The paint line keeps some customers happy because they are dealing with only one vendor when questions arise about part and finish quality.
Even if coating is not a core competency for a metal fabricator, the company is better off knowing about advancements in protective coatings technology. It can mean a big difference in possibly delivering a better final product to the customer while pocketing some production-related savings simultaneously.
The FABRICATOR engaged three coatings experts to find out just what is happening with material developments and what they mean to metal fabricators that have to paint products.
The FABRICATOR: In what ways have coatings evolved over the past several years to deliver improved corrosion resistance?
Chet Dinkins, industry sales manager, Sumter Coatings Inc.: The concern over volatile organic compounds is driving people to use more water-based coatings and coatings with less solvent. That has really taken precedence over improving coatings. So much time and research have been spent on trying to make coatings environmentally friendly to meet regulations. So a lot of the lab time is spent doing that rather than coming out with coatings that may be a lot better.
Having said that, today’s coatings have improved somewhat. In my opinion, they could have improved more with more research being done in the area of corrosion resistance versus trying to find something that is friendlier for the environment.
Terry Welch, president, Prime Coatings Co.: There has been tremendous advances in waterborne chemistry with better corrosion resistance than in the past. So there are more options there.
We have seen advances in UV chemistry for UV coatings [in which the coatings are cured when exposed to UV light], especially for temperature-sensitive substrates. The curing temperatures are just too high. We have seen tremendous advances in UV coatings for metal.
I would say those are the biggest trends that we’ve seen.
FAB: Has the variability in materials, such as the emergence of high-strength steels and advanced aluminums, posed a challenge to coatings makers?
Steve Dickey, senior director, global product strategy, Sherwin-Williams Protective & Marine Coatings: No, we have coatings for all types of metals and environments. It is really just a matter of matching the correct coating to the specified metal and the expected environment.
Welch: I don’t think so. I think with most of those types of substrates, adhesion is not a problem.
FAB: In what ways have water-based coatings achieved a performance level that more traditional solventborne coatings used to deliver?
Dinkins: Waterbornes have improved, but they are still not, in my opinion, where the solvent-based, traditional coatings have been. But they are getting closer.
Welch: We have corrosion-resistant primers that work well. There are good baking systems. We have acrylic melamine resins that work really well. We have emulsions. We have water reducible paints. There are a number of tools that you can throw at a given problem compared to the past, when you were limited to just [solventborne] materials. For example, we are making air-dry waterbornes with excellent UV resistance, adhesion, and flexibility.
The type of coating that still might be a challenge for waterbornes would be a very high-gloss, wet-looking clearcoat, such as the final clearcoat for an auto or a motorcycle. We don’t have a waterborne, nor does anyone else, that will give you a super-high gloss, wet-clearcoat look. So we are still using two-coat polyurethanes mainly for that, as well as enamels and lacquers.
FAB: What is the state of solventborne coatings in today’s environmentally conscious world?
Dickey: In the protective and marine coatings arena, solventborne and ultra-high solids (UHS) coatings still dominate the market. They have been formulated to comply with the latest standards for volatile organic compounds and hazardous air pollutants.
Waterborne materials have improved greatly in performance over the past decade, but still do not protect as well or perform as long in medium and severely corrosive environments. In fabrication operations, solventborne and UHS coatings are used in all aspects, including as corrosion-inhibiting primers and aesthetic topcoats.
Dinkins: Lead and some of the chromates have been taken out. Again, the emphasis is on environmental friendliness. In terms of protection, lead was one of the better corrosion resisters in the market, and since it’s been removed, we took a few steps backwards. It’s moved forward somewhat in terms of better performance because some of the corrosion packages, the resin systems, and the higher-solid coatings have become available.
If you look back to 20 or 30 years ago, many of the resin companies had to cut their resins with solvent to make them pourable and usable. Now they have been able to offer higher-solid resins that offer more coverage of the surface at a lower viscosity. As a result, companies can offer a higher build of film and higher-solid paints that are applicable.
Welch: Solventborne coatings are still important. You can’t beat the film properties. Certain solventborne coatings have been very difficult to replace with a waterborne coating.
Obviously, powder intruded upon that market, and to some extent, UV-cured coatings did the same thing. We have seen an increase in UV-cured coatings because the energy required to cure the product is so much less than the powder, yet you are getting very good film properties, excellent hardness, and abrasion resistance, for instance.
FAB: What type of emissions levels are allowed, in general, when applying coatings?
Dickey: In the U.S., rules vary somewhat by state and even county. In general, the rules that govern protective and marine coatings in fabrication operations are 340 grams per liter of VOCs. Some areas have begun to reduce that further to 250 g/l, and in the Los Angeles area, that target has been moved down to a challenging 100 g/l.
In most areas of the country, local ordinances and input do not affect these rules, but at the state level, the rules are based on federal guidelines.
FAB: Obviously, production cost is always an issue in manufacturing. In what ways have coatings changed to help fab shops maximize first-pass yield and boost paint cycle times?
Dickey: Protective coatings producers have been focused on two approaches. First, we continue to research and develop rapid-curing systems that help to reduce handling times and increase throughput. Second, we have been developing high-performance technologies such as EnviroLastic® 940 LV, a rapid-cure direct-to-metal (DTM) polyaspartic, to reduce the number of coats and the amount of time steel spends in the painting process. This coating has proven to reduce production time by more than 50 percent.
Dinkins: Coatings that are able to deliver long-term durability probably are the two-part paints:
the epoxies, the urethanes, and the epoxy primers and urethane topcoats. [Two-part paints are mixed at the time of application and cure quickly to create a hard, durable surface.] They are going to be the better products to give you the ultimate finish that you are looking for.
When you are talking about fabricators, however, this may not be for them. When you mix Part A and Part B together for a paint that you plan to use, what happens at that point is that you have limited pot life. You can’t put the top back on the paint and put it back on the shelf. You have to use what you have mixed.
It also can be pricey. It could be twice as much as the regular coatings.
A lot of companies that offer contract painting services understand the coatings and understand what they need to do. They are more likely to mix what they need or use what they have and charge accordingly as well.
I would tell you this as a coating supplier that supplies metal fabricators, especially the smaller ones, the change that I have seen over the years is that folks don’t want to paint themselves, and they are sending work to a custom coater. There has been a lot of that.
But I’ve seen a pushback recently from fabricators, because 10 to 15 years ago, they were under the impression that if they sent it out and had a professional jobber paint the parts, they would pay more than doing it themselves, but they didn’t have the hassle to worry about. And they thought they had a lifetime coating. They have learned since then that that is not the case. When the coatings fail, because there was traditionally no primer underneath, you would have a real mess.
Welch: Everyone wants shorter oven times. Now that’s not as much of an issue as natural gas prices are good now, but that won’t always be the case. It’ll be a major concern again in the future.
FAB: Do you think metal fabricators that have a painting operation have a good feel for newer coating advancements available to them?
Dickey: I believe it’s up to the coatings manufacturers to educate metal fabricators on what’s changing in both the coatings and environmental worlds. As an industry, we have not always done a good job of educating, and this is something we are working on to improve and expand.
On the other hand, fabricators are often driven by the specification they’re handed and are reluctant to push for the adoption of new technologies by specifiers. We need to improve that side as well.
Dinkins: I would say no, especially not the small to midsized guys. Their world is built around the metal. The painting part is the necessary evil. He doesn’t like to do it. If you don’t like it, you don’t take the time to research it and learn about it.
There are the exceptions out there. These are the fabricators that are in their towns for the long haul and they want their jobs to look pretty good three years down the road. So they will spend the time to learn about it and invest in a good paint system.
Welch: I guess I’m not quite sure how to answer that. But I will say that there is a lot better selection of products than when I started formulating 35 years ago. A lot has changed in my time in the lab.
And it always helps to be one step ahead.
Prime Coatings Co., www.primecoatings.net
Sherwin-Williams Protective & Marine Coatings, www.protective.sherwin-williams.com
Sumter Coatings Inc., www.sumtercoatings.com
About the Author
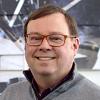
Dan Davis
2135 Point Blvd.
Elgin, IL 60123
815-227-8281
Dan Davis is editor-in-chief of The Fabricator, the industry's most widely circulated metal fabricating magazine, and its sister publications, The Tube & Pipe Journal and The Welder. He has been with the publications since April 2002.
subscribe now
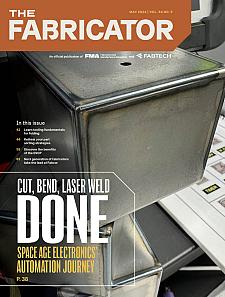
The Fabricator is North America's leading magazine for the metal forming and fabricating industry. The magazine delivers the news, technical articles, and case histories that enable fabricators to do their jobs more efficiently. The Fabricator has served the industry since 1970.
start your free subscription- Stay connected from anywhere
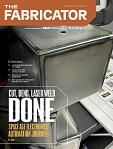
Easily access valuable industry resources now with full access to the digital edition of The Fabricator.
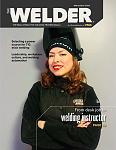
Easily access valuable industry resources now with full access to the digital edition of The Welder.
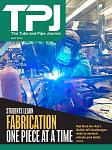
Easily access valuable industry resources now with full access to the digital edition of The Tube and Pipe Journal.
- Podcasting
- Podcast:
- The Fabricator Podcast
- Published:
- 04/30/2024
- Running Time:
- 53:00
Seth Feldman of Iowa-based Wertzbaugher Services joins The Fabricator Podcast to offer his take as a Gen Zer...
- Industry Events
Pipe and Tube Conference
- May 21 - 22, 2024
- Omaha, NE
World-Class Roll Forming Workshop
- June 5 - 6, 2024
- Louisville, KY
Advanced Laser Application Workshop
- June 25 - 27, 2024
- Novi, MI