Editor-in-Chief
- FMA
- The Fabricator
- FABTECH
- Canadian Metalworking
Categories
- Additive Manufacturing
- Aluminum Welding
- Arc Welding
- Assembly and Joining
- Automation and Robotics
- Bending and Forming
- Consumables
- Cutting and Weld Prep
- Electric Vehicles
- En Español
- Finishing
- Hydroforming
- Laser Cutting
- Laser Welding
- Machining
- Manufacturing Software
- Materials Handling
- Metals/Materials
- Oxyfuel Cutting
- Plasma Cutting
- Power Tools
- Punching and Other Holemaking
- Roll Forming
- Safety
- Sawing
- Shearing
- Shop Management
- Testing and Measuring
- Tube and Pipe Fabrication
- Tube and Pipe Production
- Waterjet Cutting
Industry Directory
Webcasts
Podcasts
FAB 40
Advertise
Subscribe
Account Login
Search
A new level of flexibility in fiber laser cutting technology
Fiber laser offers programmable beam quality
- By Dan Davis
- October 16, 2018
- Article
- Laser Cutting
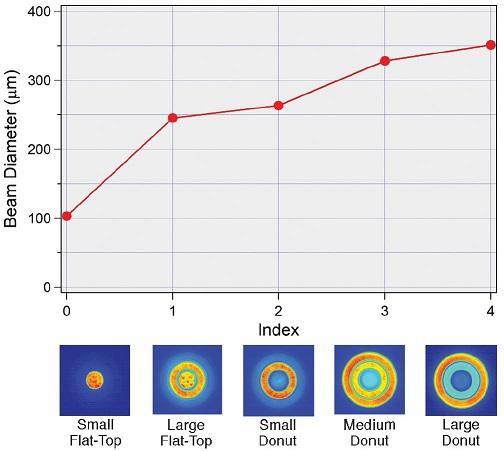
Figure 1
These are the five beam diameters for a 4-kW nLIGHT Corona fiber laser. The bottom images, recorded with a CMOS camera, show the beam shapes at the focus position. Photos courtesy of nLIGHT.
Fiber laser cutting machines have emerged as the technology of choice for sheet metal cutting in the metal fabricating industry. They are able to deliver unrivaled productivity, precision, and cost-effective operation when compared with the cutting technologies that came before them.
Having said that, fiber laser cutting technology has room for improvement. Many systems currently being used in fabricating shops are equipped with fiber lasers that generate beam widths of a particular size, limiting their flexibility. For instance, when the early fiber lasers were sold, they were used mainly to cut thin sheet metal; the laser beam’s small spot size provided much more focused power than a CO2 laser-generated beam and sliced through thin gauge quickly, but struggled with thicker metal. That changed with the advent of manual and automated systems that could vary the laser’s spot size, but those systems have complex cutting heads that have raised some questions about reliability in the eyes of some.
nLIGHT Inc. believes it has developed a new generation of fiber laser technology that answers the call for beam spot size flexibility without the cutting head concerns. This breakthrough enables rapid tuning of the spot size directly from the fiber laser, providing optimized cutting of a variety of materials and thicknesses with a single laser source, according to company officials.
“This unique capability greatly extends cutting tool performance and flexibility,” said Brian Victor, nLIGHT’s director, industrial applications.
How Laser Cutting Got Here
CO2 lasers powered early laser cutting tools. These lasers, which use a gas-filled tube energized by an electrical discharge to generate laser light, became the workhorse of the early 21st century fab shop. However, CO2 lasers are relatively large, inefficient, and fragile, and they require regular maintenance and expensive consumables. Moreover, the complex system of mirrors and purged beam tubes is susceptible to degradation from contamination, misalignment, and variations in environmental conditions, such as temperature and vibration level. Nonetheless, CO2 lasers continue to be used for cutting thick metals because they provide good edge quality.
Lamp-pumped Nd:YAG lasers emerged in the 1990s. They use a solid-state gain medium (a crystalline YAG rod doped with neodymium, a rare-earth element), eliminating the need for consumable gases. The Nd:YAG rod is energized, however, by a broadband arc lamp, which is optically inefficient and generates significant waste heat. The near-infrared wavelength (~1 μm) of an Nd:YAG laser allows the beam to be delivered to the process head via an optical fiber (a thin strand of glass that guides light), eliminating free-space optical beam delivery outside the laser cavity.
In the late 1990s, semiconductor (diode) lasers began replacing lamps as the pump source of Nd:YAG lasers, completing the transition to an all-solid-state laser. Diode-pumped solid-state (DPSS) lasers efficiently convert electricity to optical power, thus providing higher net efficiency than lamp-pumped lasers, with reduced needs for power and cooling. The rare-earth-doped disk was developed as an alternative geometry for the solid-state gain medium, enabling more effective thermal management than Nd:YAG rods and further scaling to higher powers. DPSS lasers are compatible with fiber delivery to the process head, although the laser cavities are still comprised of free-space optics.
Also in the 1990s, rare-earth-doped fibers emerged as a new gain medium for optical telecommunications. Fiber lasers are uniquely practical and reliable because they eliminate the need for free-space optics, such as mirrors. The diode pump source is delivered to the gain medium via optical fiber. The cavity is comprised of optical fiber, and fiber delivery is naturally supported because the laser beam is generated within an optical fiber. The large surface-area-to-volume ratio of the fiber gain medium enables efficient cooling.
The fiber lasers stood out because of their unique traits:
- No free-space optics within or outside the laser cavity (until the process head)
- A sealed, alignment-free optical path that eliminates the possibility of degradation and failure modes
- High wall-plug efficiency, which minimizes power and cooling requirements
- A high beam quality that is unaffected by environmental conditions and optical power level
- No need for routine maintenance, consumables, or calibration
The State of Fiber Laser Cutting
The above discussion explains why fiber lasers provide the best efficiency, reliability, and operating costs, but what about metal cutting speed and edge quality? Here, the situation is more complex.
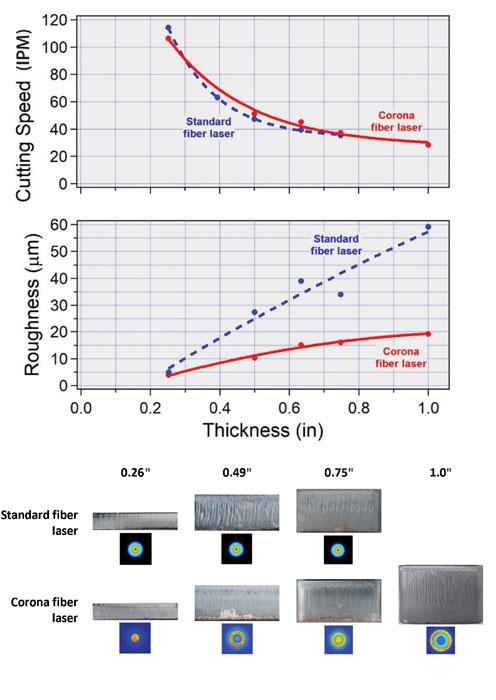
Figure 2
A comparison of oxygen-assisted cutting of mild steel using a standard 4-kW fiber laser with a 100-μm feeding fiber and a 4-kW Corona fiber laser is shown. The upper graph shows the cutting speed, and the lower graph shows the measured edge roughness values. Photographs showing the edge quality are presented below the graphs, with beam images included below each photo.
A typical job shop needs to process a diverse mix of metals and thicknesses, and limitations of current laser technology force tool integrators and end users to sacrifice something. They need laser cutting technology that can adjust spot size to cut a variety of metal thicknesses. Shops that don’t have that capability might have multiple laser cutting machines, such as a small-beam fiber laser tool for light gauges and a larger-beam fiber laser or a CO2 laser for thicker plate.
Shops that do have spot size adjustment capabilities with their laser cutting machines have concerns of the own. Some have to manually change the focusing lens in the cutting head to optimize the fiber laser spot size, which leads to lost productivity with every lens change. The fabricator also risks contaminating the lens or cutting head during this manual interaction.
Shops that have laser cutting machines that automatically vary the spot size have to be cognizant of the machine tool mechanics. Existing automated approaches typically employ motorized free-space optics. Examples include specialized cutting heads, fiber-to-fiber couplers, free-space-to-fiber couplers that vary the launch conditions into the fiber, or fiber-to-fiber switches with two to four outputs coupled to independent process fibers.
“Such free-space optical approaches entail significant cost and complexity and can degrade tool performance and reliability,” Victor said. “They also are sensitive to misalignment, contamination, and environmental conditions; introduce power dependence (thermal lensing) and optical loss; or have slow switching speed.”
Victor added that the specialized cutting heads often are larger and heavier than standard fixed-optic cutting heads, resulting in reduced acceleration and imposing additional design requirements on the gantry and motors.
This scenario of fabrication shops being forced to compromise between flexibility in the job mix and tool performance and reliability motivated nLIGHT researchers to look for a way to deliver spot-size tuning that could be done directly out of the laser source. The thinking was that such a development would give fabricators significant advantages in tool use and cost per part.
Changing Beam Diameter from the Laser Source
That research led to the recently introduced fiber laser product that nLIGHT calls Corona™. It enables rapid tuning of the beam quality (spot size) directly from the feeding fiber.
“This all-fiber technology entails no free-space optics and thus eliminates their associated drawbacks and failure modes,” Victor said.“Corona fiber lasers have already shown greatly improved cutting performance up to 4 kW by providing high cutting speed for thin plate and high edge quality for thick plate that is equal to or better than that achieved with higher-power fiber lasers or even CO2 lasers,” said Dahv A.V. Kliner, vice president, fiber laser technology. “This versatility is achieved within the Corona fiber laser, inside the fiber, without making any changes to the cutting head.”
The Corona fiber laser output beam is tunable between ~100 μm and ~300 μm spot size, according to Kliner. Figure 1 shows the output beam diameters and beam shapes for a Corona fiber laser with five spot size settings.
Kliner said that the Corona fiber laser has produced some noteworthy results in edge quality when cutting thick metal. Figure 2 shows the cutting speed and surface roughness of mild steel cut with both a standard 4-kW fiber laser with a 100-μm feeding fiber and a 4-kW Corona fiber laser. A fixed-optic cutting head with 1.5x magnification was used for all tests, and the assist gas was oxygen. Photographs illustrating the edge quality are shown below the graphs, with the optimum Corona beam shape shown for each case.
Kliner noted these key observations:
• For thicknesses greater than 0.25 inch, the Corona fiber laser provides very good edge quality, with the roughness reduced by up to three times when compared to the traditional fiber laser. The maximum thickness at which the part consistently drops from the skeleton is 0.75 in. for the standard fiber laser. The Corona fiber laser substantially extends the thickness to 1 in. and higher with outstanding edge quality.
• The roughness of thick parts cut with the Corona fiber laser is much less noticeable than those cut with a standard fiber laser. The measured roughness of 1-in. mild steel cut with the new fiber source is even less than that of 0.5-in. mild steel cut with the standard fiber laser.
“An additional advantage of Corona is that beam tuning is very rapid, with a transition time from the smallest to the largest diameter of less than 30 ms,” Kliner said.
The Corona fiber laser continues to operate at full power during a spot size change, and the laser power and modulation parameters can be adjusted on-the-fly in conjunction with index spot size changes. Kliner added that this means Corona’s rapid tuning allows for optimum beam characteristics for each step of the cutting process—piercing, marking, cornering, and cutting of large or small features—not just for cutting of different materials or thicknesses.
Photos courtesy of nLIGHT, www.nlight.net.
About the Author
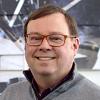
Dan Davis
2135 Point Blvd.
Elgin, IL 60123
815-227-8281
Dan Davis is editor-in-chief of The Fabricator, the industry's most widely circulated metal fabricating magazine, and its sister publications, The Tube & Pipe Journal and The Welder. He has been with the publications since April 2002.
subscribe now
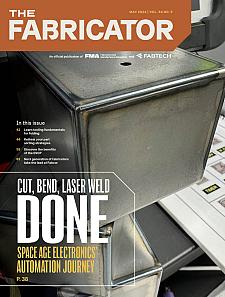
The Fabricator is North America's leading magazine for the metal forming and fabricating industry. The magazine delivers the news, technical articles, and case histories that enable fabricators to do their jobs more efficiently. The Fabricator has served the industry since 1970.
start your free subscription- Stay connected from anywhere
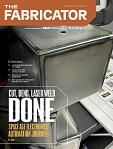
Easily access valuable industry resources now with full access to the digital edition of The Fabricator.
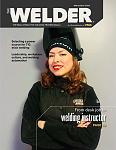
Easily access valuable industry resources now with full access to the digital edition of The Welder.
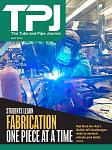
Easily access valuable industry resources now with full access to the digital edition of The Tube and Pipe Journal.
- Podcasting
- Podcast:
- The Fabricator Podcast
- Published:
- 04/30/2024
- Running Time:
- 53:00
Seth Feldman of Iowa-based Wertzbaugher Services joins The Fabricator Podcast to offer his take as a Gen Zer...
- Industry Events
Pipe and Tube Conference
- May 21 - 22, 2024
- Omaha, NE
World-Class Roll Forming Workshop
- June 5 - 6, 2024
- Louisville, KY
Advanced Laser Application Workshop
- June 25 - 27, 2024
- Novi, MI
Precision Press Brake Certificate Course
- July 31 - August 1, 2024
- Elgin,