Editor
- FMA
- The Fabricator
- FABTECH
- Canadian Metalworking
Categories
- Additive Manufacturing
- Aluminum Welding
- Arc Welding
- Assembly and Joining
- Automation and Robotics
- Bending and Forming
- Consumables
- Cutting and Weld Prep
- Electric Vehicles
- En Español
- Finishing
- Hydroforming
- Laser Cutting
- Laser Welding
- Machining
- Manufacturing Software
- Materials Handling
- Metals/Materials
- Oxyfuel Cutting
- Plasma Cutting
- Power Tools
- Punching and Other Holemaking
- Roll Forming
- Safety
- Sawing
- Shearing
- Shop Management
- Testing and Measuring
- Tube and Pipe Fabrication
- Tube and Pipe Production
- Waterjet Cutting
Industry Directory
Webcasts
Podcasts
FAB 40
Advertise
Subscribe
Account Login
Search
Do you need a high-power laser? Consider options carefully
20-kW-plus machines aren’t for everyone
- By Lincoln Brunner
- April 8, 2024
- Article
- Laser Cutting
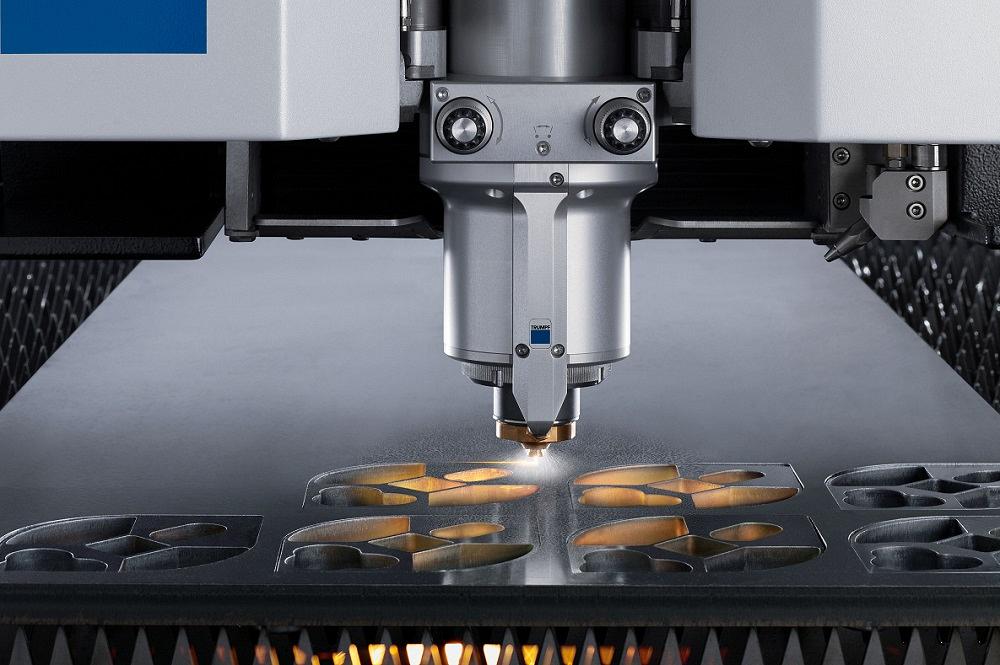
High-wattage lasers can thicker material that once was the nearly exclusive domain of plasma cutting, but it doesn’t mean that the latest machines are what a shop necessarily needs for its part mix. Images: TRUMPF Inc.
Anyone who grew up watching comedian Tim Allen deliver his signature “Oh-oh-oh” grunt while talking about tools knows the draw of more power. After all, it’s more power. What could go wrong?
If you’re anything like Allen’s character, Tim “The Tool Man” Taylor, the answer is “plenty.” And the same holds true for shops swooning over the ever-growing array of high-wattage laser cutting machines. Machines offering 24-kW and even 30-kW generators are now more and more common. These machines can produce incredible results in terms of material thickness capacity and turnaround times. However, the allure of all that raw power needs to be complemented by a shop’s overall needs and part mix, which may not be suited to the highest-wattage laser generator available—and, in fact, might very well call for less wattage.
For example, the 24-kW machines offered at the high end of TRUMPF Inc.’s line of laser cutting machines can cut steel up to 60 mm (2.36 in.) thick. TRUMPF noted that these newest lasers can cut through thick material up to three times faster than 6-kW machines.
That kind of wattage may be of great use to job shops that need to cut thick plate in smaller batches or with higher edge quality, but perhaps it is of less use to shops that deal heavily in high production runs with thinner sheet, explained Brett Thompson, a laser technology and sales consulting manager for TRUMPF Inc., Farmington, Conn.
“Customers can best use higher-wattage machines by primarily focusing on material in the mid-thick and greater ranges,” Thompson said. “Obviously, a high-power laser is going to cost more upfront, so there needs to be a big gap in actual part cutting run-time before the cost per part starts to tilt in favor of a higher-power machine.
“As a general rule, anything below approximately ¼ in. thick is probably going to cost more if it is cut at high power, even though the total processing times are shorter,” he said. “If you focus on material ranges where there’s a big difference in run-time—in particular, where you can replace oxygen cutting with nitrogen cutting—you’ll see big gains in profitability.”
Do You Really Need It?
Soon after laser cutting machines began making a big push into the metal fabrication world in the ’80s, it didn’t take long for the original 1-kW models to give way to 2- and 3-kW machines. At that point, the thickest carbon and stainless material cut with lasers generally topped out at ¼-in. plate. Fast-forward to the introduction of 6- and 8-kW machines a few years later, and suddenly ½-in. and thicker material were not only within the range of cuttability, but the edge quality and turnaround speed now made more sense to more fabricators.
Today’s 20-kW (and more) lasers, however, put those early machines to shame, not only with their capacity to cut plate 1 in. and even 2 in. thick, but also with their ability to cut much more intricate contours into the thicker material.
That is where laser buyers truly need to consider their part mix and specific requirements, according to Thompson. Given the price of a high-powered laser (generally $1 million and up), laser users, and would-be users, at every level should count the cost carefully. For many customers and applications, other less expensive cutting technologies are more cost-effective—a distinction that even a laser manufacturer like TRUMPF readily acknowledges.
“A common misconception is that everybody needs higher-wattage lasers,” Thompson said. “In most cases, job shops are the main buyers of cutting machines with such high power levels. If you’re an OEM that primarily cuts gauge stainless, then a 24-kW machine isn’t going to do much for your bottom line. Even at an OEM that runs heavy plate almost exclusively, you need a lot of production hours for it to be necessary.
“There are plenty of cases in which a laser is a good alternative to plasma for cutting really thick material—say, 2-in. steel. But unless there’s a specific reason to use a laser on a part—for example, smaller inside contours or sharp corners—it might be better to use your existing plasma table simply because it is likely to be the cheaper way to produce the part. Of course, if you don’t have a plasma table, it’s obviously to your benefit to have a laser that can cut 60-mm steel while also doing normal ‘laser things’ like chopping up 1/8-in. steel all day.”
Full Systems, Not Add-Ons
Thompson cautioned that shops investing in high-powered generators should think of them as brand-new machines rather than simply add-ons to older lasers that retain the same optical chain, meaning the laser, the beam delivery system, and the cutting unit. Doing so can not only damage the old equipment but also significantly diminish the advantages of the upgraded power source and beam generation.
“Higher-wattage cutting machines should not just be a bigger laser source sitting atop an existing machine and optical chain,” Thompson said. “Higher-wattage machines work better and more consistently when they are specifically designed for this type of cutting work. Operators shouldn’t have to fret about what they’re cutting and that a miscut might damage the machine. Before introducing its higher-wattage cutting machine, TRUMPF put a lot of work into developing an optical chain … that would be up to the task of reliably supporting this level of power.”
In particular, higher-wattage systems should incorporate things like a more robust beam delivery cable structure and cutting unit, he noted. In addition, Thompson said his company addressed factors such as controlling the unit’s under-pallet conveyor speed relative to the cut speed, which is important because of the higher number of parts and cutouts falling out of sheets in higher-wattage systems.
That wrinkle dovetails with another issue that bedevils every manufacturer and user of higher-wattage lasers—increased pallet slat consumption. Even for users of easier-to-clean copper slats, the trouble remains.
“Pallet slats pose the biggest challenge in properly maintaining a higher-wattage laser machine,” Thompson said. “High laser powers cause the slats to be consumed much more quickly than regular laser cutting operations.”
About the Author
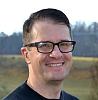
Lincoln Brunner
2135 Point Blvd.
Elgin, IL 60123
(815)-227-8243
Lincoln Brunner is editor of The Tube & Pipe Journal. This is his second stint at TPJ, where he served as an editor for two years before helping launch thefabricator.com as FMA's first web content manager. After that very rewarding experience, he worked for 17 years as an international journalist and communications director in the nonprofit sector. He is a published author and has written extensively about all facets of the metal fabrication industry.
Related Companies
subscribe now
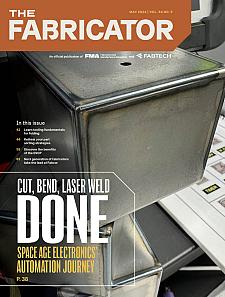
The Fabricator is North America's leading magazine for the metal forming and fabricating industry. The magazine delivers the news, technical articles, and case histories that enable fabricators to do their jobs more efficiently. The Fabricator has served the industry since 1970.
start your free subscription- Stay connected from anywhere
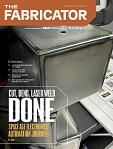
Easily access valuable industry resources now with full access to the digital edition of The Fabricator.
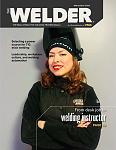
Easily access valuable industry resources now with full access to the digital edition of The Welder.
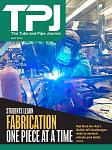
Easily access valuable industry resources now with full access to the digital edition of The Tube and Pipe Journal.
- Podcasting
- Podcast:
- The Fabricator Podcast
- Published:
- 04/16/2024
- Running Time:
- 63:29
In this episode of The Fabricator Podcast, Caleb Chamberlain, co-founder and CEO of OSH Cut, discusses his company’s...
- Trending Articles
Tips for creating sheet metal tubes with perforations
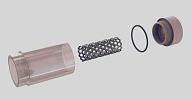
Supporting the metal fabricating industry through FMA
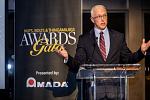
JM Steel triples capacity for solar energy projects at Pennsylvania facility
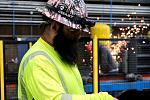
Fabricating favorite childhood memories
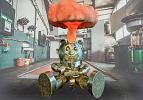
Omco Solar opens second Alabama manufacturing facility
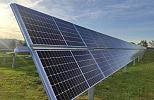
- Industry Events
16th Annual Safety Conference
- April 30 - May 1, 2024
- Elgin,
Pipe and Tube Conference
- May 21 - 22, 2024
- Omaha, NE
World-Class Roll Forming Workshop
- June 5 - 6, 2024
- Louisville, KY
Advanced Laser Application Workshop
- June 25 - 27, 2024
- Novi, MI