- FMA
- The Fabricator
- FABTECH
- Canadian Metalworking
Categories
- Additive Manufacturing
- Aluminum Welding
- Arc Welding
- Assembly and Joining
- Automation and Robotics
- Bending and Forming
- Consumables
- Cutting and Weld Prep
- Electric Vehicles
- En Español
- Finishing
- Hydroforming
- Laser Cutting
- Laser Welding
- Machining
- Manufacturing Software
- Materials Handling
- Metals/Materials
- Oxyfuel Cutting
- Plasma Cutting
- Power Tools
- Punching and Other Holemaking
- Roll Forming
- Safety
- Sawing
- Shearing
- Shop Management
- Testing and Measuring
- Tube and Pipe Fabrication
- Tube and Pipe Production
- Waterjet Cutting
Industry Directory
Webcasts
Podcasts
FAB 40
Advertise
Subscribe
Account Login
Search
Fiber laser allows wheelchair manufacturer to bring cutting in-house
- March 6, 2018
- Article
- Laser Cutting
SITUATION
Action Mfg. in Marshall, Minn., started out in the recreational motorsports business but in 2008, 10 years after an accident left his son paralyzed, company founder Tim Swenson wanted to get his son back into the outdoors again.
The company now manufactures the Action Trackchair and Action Trackstander all-terrain wheelchairs. They are accompanied by a variety of accessory options, including rear utility racks, fishing rod holders, gun racks, and footrests.
“Starting out, we had no idea if we were going to sell 10 or 100 chairs,” Swenson explained. “Now we have sold over 3,500.”
The company soon realized it needed to make some operational changes. “With the increase in demand, we knew we needed a more efficient and more accurate system put in place,” said Swenson.
One of those changes was to bring previously outsourced work in-house.
The firm started out with a used 2-kW Mazak CO2 laser machine, but within two months, Swenson knew Action Mfg. needed a new fiber laser to improve production speed and accuracy.
RESOLUTION
Less than a year after purchasing the used laser, the company purchased a Mazak Optiplex 3015 4-kW fiber laser cutting system.
“We are now designing our products around the laser,” Swenson said. “We changed the way our chairs are being produced. We started with tubing, and because of the laser, we are now using sheet stock. This has allowed us to save time, which in turn saves money. We also have been able to utilize more aluminum instead of steel. With people in wheelchairs always wanting to go faster, further, and for longer, aluminum is a better option.”
With the increase in production and the new laser, the company needed more space. It added 12,000 sq. ft. to its 24,000-sq.-ft. facility and most recently purchased a robotic welding cell to help increase efficiency.
Mazak Optonics Corp.
www.mazakoptonics.com
Related Companies
subscribe now
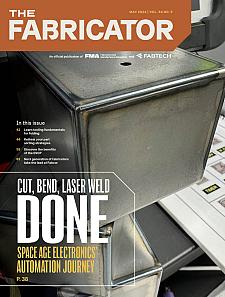
The Fabricator is North America's leading magazine for the metal forming and fabricating industry. The magazine delivers the news, technical articles, and case histories that enable fabricators to do their jobs more efficiently. The Fabricator has served the industry since 1970.
start your free subscription- Stay connected from anywhere
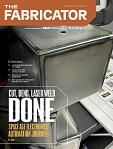
Easily access valuable industry resources now with full access to the digital edition of The Fabricator.
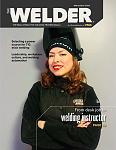
Easily access valuable industry resources now with full access to the digital edition of The Welder.
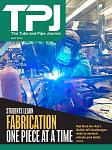
Easily access valuable industry resources now with full access to the digital edition of The Tube and Pipe Journal.
- Podcasting
- Podcast:
- The Fabricator Podcast
- Published:
- 04/30/2024
- Running Time:
- 53:00
Seth Feldman of Iowa-based Wertzbaugher Services joins The Fabricator Podcast to offer his take as a Gen Zer...
- Trending Articles
JM Steel triples capacity for solar energy projects at Pennsylvania facility
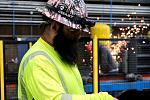
Fabricating favorite childhood memories
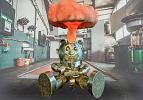
How laser and TIG welding coexist in the modern job shop
Robotic welding sets up small-batch manufacturer for future growth
Ultra Tool and Manufacturing adds 2D laser system
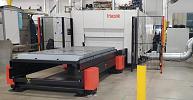
- Industry Events
Pipe and Tube Conference
- May 21 - 22, 2024
- Omaha, NE
World-Class Roll Forming Workshop
- June 5 - 6, 2024
- Louisville, KY
Advanced Laser Application Workshop
- June 25 - 27, 2024
- Novi, MI
Precision Press Brake Certificate Course
- July 31 - August 1, 2024
- Elgin,