President
- FMA
- The Fabricator
- FABTECH
- Canadian Metalworking
Categories
- Additive Manufacturing
- Aluminum Welding
- Arc Welding
- Assembly and Joining
- Automation and Robotics
- Bending and Forming
- Consumables
- Cutting and Weld Prep
- Electric Vehicles
- En Español
- Finishing
- Hydroforming
- Laser Cutting
- Laser Welding
- Machining
- Manufacturing Software
- Materials Handling
- Metals/Materials
- Oxyfuel Cutting
- Plasma Cutting
- Power Tools
- Punching and Other Holemaking
- Roll Forming
- Safety
- Sawing
- Shearing
- Shop Management
- Testing and Measuring
- Tube and Pipe Fabrication
- Tube and Pipe Production
- Waterjet Cutting
Industry Directory
Webcasts
Podcasts
FAB 40
Advertise
Subscribe
Account Login
Search
Which material test methods best influence metal forming success?
Question convention in an age of change
- By Bill Frahm
- April 16, 2018
- Article
- Metals/Materials
The many recent changes in sheet metal forming make us all feel a bit uncomfortable about the depth of our knowledge. In the past 20 to 30 years, the industry introduced hundreds of new grades of steel; aluminum became more common in automotive applications; warm and hot forming introduced time and temperature requirements to forming operations; machine suppliers introduced new forming technologies; and manufacturing automation continued to evolve.
With so many choices of materials and processes, it’s often difficult to choose the right approach. Often, even the experts don’t know which options are ideal for a given situation.
Metalworking is a proud and ancient industry full of traditions and “rules of thumb.” As Josh Welton mentioned in his recent article, we are too willing to accept the proclamations of experienced veterans as truth. In a changing world, however, our growth and success depend on our ability to challenge long-held truths about modern materials and practices. In an age of rapid technological change, it is imperative for us to challenge established practices.
Material Properties Assumptions
One area in which we must be more critical in our usage is in determining which combination of test methods best reflects the material properties that will influence our forming success. In an era of increasing need for reliable data for simulation and machine maintenance, we need to re-evaluate old rules, make information-driven decisions, and learn how experience and information can work together to support better decisions.
We traditionally place much importance on tensile testing and the resultant yield curve in making our material and forming decisions. The yield curve is a valuable source of information about the range of force required and limits of strain that define our material’s capability to take on permanent deformation before failure. The limitation of the tensile test is that the test sample is not in contact with another surface during the test, as required during stamping. Also, tensile testing determines our sample’s capabilities along a single axis.
Dome testing (including limiting dome height) is conducted under conditions similar to those of a stamping operation. The sample surface is in contact with tooling surfaces; friction and lubrication must be accounted for, and the test results reflect deformation behavior in all directions.
Dome testing forms the basis of forming limit curve determination, which measures the quantity of minor and major strains the material can withstand before failure.
Hole expansion testing and the hole expansion ratio (HER) offer insights into the stretchability of sheared edges. The HER is a useful measure to select the right material for shearing, laser cutting, and forming operations that require adequate stretchability of edges. As with other tests, the standards for hole expansion testing also must be evaluated critically. Some researchers question the common usage of a 10-mm hole, as the geometry of the hole itself affects the results of the test. Your hole diameter selection should take into consideration the forming application you are going to use.
The following is from a presentation at the International Deep-Drawing Research Group (IDDRG) conference in 2014: “However, the hole expansion test does not only examine the stretchability of cut edges, but also their sensitivity to the mechanical contact with the expansion tool, inducing additional local deformation and related damage. The contact conditions are strongly affected by the hole expansion geometry, where smaller initial hole diameters and smaller cone angles lead to significantly higher contact pressures and, hence, may lead to lower hole expansion ratios due to higher local damage at the hole edge (in spite of higher stabilizing effects). The consideration of these effects is an essential requirement of a reliable experimental assessment and simulative description and of the stretch-flangeability and the edge crack sensitivity.” (Towards More Efficient Hole Expansion Testing , C. Krempaszky, P. Larour, J. Freudenthaler, E. Werner, IDDRG 2014 Conference.)
The inputs into our simulation programs must evolve as we expand the use of new materials and forming technologies. Determining appropriate testing methods requires solid knowledge of metal forming fundamentals along with the applicability and limitations of these results. Until we know how our simulation inputs need to change to reflect the advanced sheet metals and forming operations, we may need a fair amount of trial and error to determine which test results best correlate to our observations.
About the Author
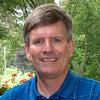
Bill Frahm
P.O. Box 71191
Rochester Hills, MI 48307
248-506-5873
subscribe now
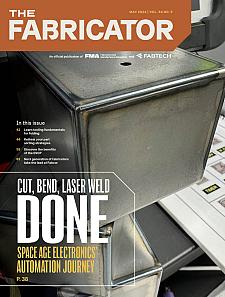
The Fabricator is North America's leading magazine for the metal forming and fabricating industry. The magazine delivers the news, technical articles, and case histories that enable fabricators to do their jobs more efficiently. The Fabricator has served the industry since 1970.
start your free subscription- Stay connected from anywhere
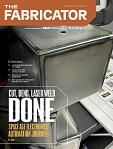
Easily access valuable industry resources now with full access to the digital edition of The Fabricator.
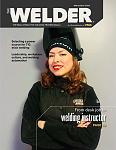
Easily access valuable industry resources now with full access to the digital edition of The Welder.
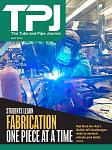
Easily access valuable industry resources now with full access to the digital edition of The Tube and Pipe Journal.
- Podcasting
- Podcast:
- The Fabricator Podcast
- Published:
- 04/16/2024
- Running Time:
- 63:29
In this episode of The Fabricator Podcast, Caleb Chamberlain, co-founder and CEO of OSH Cut, discusses his company’s...
- Trending Articles
Tips for creating sheet metal tubes with perforations
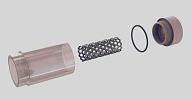
Supporting the metal fabricating industry through FMA
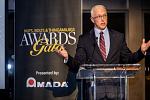
JM Steel triples capacity for solar energy projects at Pennsylvania facility
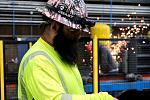
Fabricating favorite childhood memories
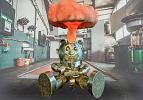
Omco Solar opens second Alabama manufacturing facility
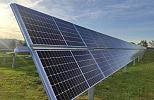
- Industry Events
16th Annual Safety Conference
- April 30 - May 1, 2024
- Elgin,
Pipe and Tube Conference
- May 21 - 22, 2024
- Omaha, NE
World-Class Roll Forming Workshop
- June 5 - 6, 2024
- Louisville, KY
Advanced Laser Application Workshop
- June 25 - 27, 2024
- Novi, MI