President
- FMA
- The Fabricator
- FABTECH
- Canadian Metalworking
Categories
- Additive Manufacturing
- Aluminum Welding
- Arc Welding
- Assembly and Joining
- Automation and Robotics
- Bending and Forming
- Consumables
- Cutting and Weld Prep
- Electric Vehicles
- En Español
- Finishing
- Hydroforming
- Laser Cutting
- Laser Welding
- Machining
- Manufacturing Software
- Materials Handling
- Metals/Materials
- Oxyfuel Cutting
- Plasma Cutting
- Power Tools
- Punching and Other Holemaking
- Roll Forming
- Safety
- Sawing
- Shearing
- Shop Management
- Testing and Measuring
- Tube and Pipe Fabrication
- Tube and Pipe Production
- Waterjet Cutting
Industry Directory
Webcasts
Podcasts
FAB 40
Advertise
Subscribe
Account Login
Search
Fabricators should take note of plasma cutting advancements
That 25-year-old plasma table can’t match today’s technology
- By John Zuehlke
- August 14, 2019
- Article
- Plasma Cutting

An older plasma cutting table is the workhorse for many shops specializing in heavy fabrication. A more modern plasma cutting system can help those same shops achieve new efficiencies that aren’t possible with older technology.
In many shops the “cutting machine” is the plasma cutting machine. Waterjets and lasers also cut metal, but when it comes to cost-effective and efficient cutting of steel plate, the plasma cutting machine is typically the equipment of choice.
Unfortunately, when many people think of their shop’s cutting machine, it’s a plasma cutting machine from the late 20th century. The cutting table has none of the capabilities of today’s modern equipment. In fact, fabricators will find many tables now are equipped with drilling, tapping, oxyfuel cutting, marking, and beveling capabilities in addition to plasma cutting.
Let’s look at some of the significant technological advancements made over the past 25 years.
Computer Numerical Control
CNC equipment from 25 years ago relied on cathode ray tubes and reel-to-reel tape drives for operation. Today CNC machines are PC-based and probably connected wirelessly to the web. This not only enables remote loading of cutting programs, but more importantly allows the manufacturer of the equipment to diagnose the technology remotely should operational errors occur. Furthermore, custom software and updates can be loaded easily into the CNC if a new capability, such as marking, is added to the equipment mix.
Plasma Power Sources
In the early days plasma cutting systems used a tungsten electrode, nitrogen as the cut gas, and CO2 as the shield. Most systems were 600 amps. Now a 300-amp plasma cutting power source with a hafnium electrode and with oxygen as an assist cutting gas can cut faster and more accurately (especially with holes) on carbon steel than the old 600-amp systems.
Changes are coming so fast in performance that it’s difficult to keep up. Whereas a metal fabricator had only three gases to choose from 25 years ago for ideal cutting parameters, today fabricators can choose from six: argon, CO2, hydrogen, methane, nitrogen, and oxygen. Some plasma cutting systems even use water to constrict the plasma arc when cutting materials other than carbon steel. The technological advancements have helped plasma cutting to emerge as an economical way to shape-cut stainless steel and aluminum.
Oxyfuel Cutting
Oxyfuel cutting is still the old standby and the most economical way to cut carbon steel that is more than 2 inches thick. Yet even this mature technology has undergone several changes over the years.
A quarter of a century ago, if a fabricator ordered an optional height control and igniters, after about six months the operator typically removed them. Operators saw them as something that just got in the way; were subject to moisture, slag, and dirt; and were restricted in movement, as the simple motor could only go up and down. Today fabricators can have an integrated height control that keeps the torch out of harm’s way and internal torch igniters that work consistently when needed. Servo controls provide for smooth and reliable movement of the torches, and no tools are required for tip changes.
In fully automated systems, the CNC can set oxyfuel ratios to include flow rates for different thicknesses. The operator just provides the thickness of the material to be cut and pushes the start button.
Beveling
Beveling has improved over the years with the advancements in hardware and software. Work still needs to be done, but fabricators are getting closer to the goal of using plasma cutting systems that make the job of beveling as simple and repeatable as possible for the machine operator.
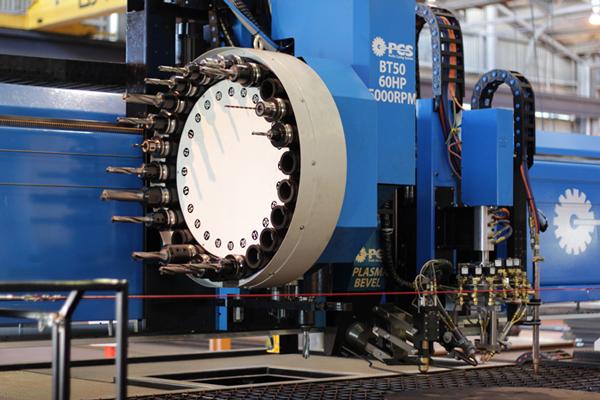
A finished part can be produced with a plasma cutting system that not only can cut, but also drill, tap, mill, bevel cut, and mark. With the addition of an oxyfuel torch, very thick material can be processed as well.
Some bevel heads now have zero offset. This greatly helps the programmer especially with internal bevels. The head itself can achieve angles of ±47.5 degrees while the machine remains completely stationary. (The machine does not have to move its X and Y axes to achieve angles.) In fact, this means that the torch can tilt as it approaches a corner, preparing for a bevel on the next side of the part. This effectively negates the need for a looped corner, which minimizes the amount of plate that is cut to achieve the bevel.
The mechanical systems on modern plasma cutting machines are compact. Now fabricators can even purchase beveling capability on a 5- by 10-ft. machine.
For those interested in oxyfuel beveling, servo controls simplify setup of the cutting job and actual operation of the machine. Also, continuous rotation with these oxyfuel cutting heads is possible without having to unwind them because of twisted hoses.
Marking
Twenty-five years ago marking was done solely with zinc or a punch. (Zinc marking involved the use of zinc powder that was then melted with the plasma flame. The semipermanent marking could be welded over without issues.)
Now a machine can use a punch, pin, plasma, inkjet, zinc, or laser for layout, part identification, and even bar coding in any axis.
Secondary Operations
Today’s plasma cutting systems can be equipped with tools to drill, tap, countersink, and even mill. Automatic tool changers are now common.
How effective are these systems? A 60-HP drilling tool on a plasma cutting system can make a 2-in. hole through 4-in. material in 27 seconds and a 3-in. hole through 5-in. material in 60 to 90 seconds.
The cost associated with material handling in a fabricating shop is really driving interest in these additional capabilities. If the cutting system can produce a finished product in one step without additional material handling to deliver the workpiece to downstream operations—all while avoiding possible processing errors resulting from human intervention—a company saves a lot of money.
Additionally, the introduction of through-tool lubricant delivery in minimal quantities has helped to improve drilling and eliminates both the mess and cost associated with relying on flooding coolant.
Other Factors
A modern plasma cutting system also may be equipped with additional cutting capabilities, such as an oxyfuel torch, laser, or water; material load and unload automation for sheet or plate; automated scrap removal devices; material handling devices for 3D shapes, such as tube and beams; and grate cutting capability. A plasma system could have all of these, but that’s not really probable. For example, a fabricator may find it more practical to have a separate machine for pipe if the plasma cutting machine is dominated with plate work. As always, management must do its research to determine what options are worth investing in.
The same thinking applies to software. Basic software can cover machine programming, and more elaborate packages can handle such tasks as production scheduling and even interfacing with existing ERP systems. Again, company management needs to decide just what aspects of these modern tools they want to better position the organization for the future.
John Zuehlke is president, Profile Cutting Systems USA, 190 Mesa Drive, Boulder Creek, CA 95006, 831-338-8251, www.pcsmachines.com.
About the Author
Related Companies
subscribe now
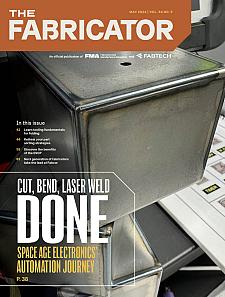
The Fabricator is North America's leading magazine for the metal forming and fabricating industry. The magazine delivers the news, technical articles, and case histories that enable fabricators to do their jobs more efficiently. The Fabricator has served the industry since 1970.
start your free subscription- Stay connected from anywhere
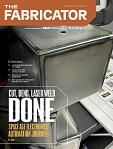
Easily access valuable industry resources now with full access to the digital edition of The Fabricator.
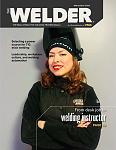
Easily access valuable industry resources now with full access to the digital edition of The Welder.
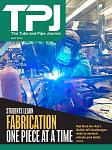
Easily access valuable industry resources now with full access to the digital edition of The Tube and Pipe Journal.
- Podcasting
- Podcast:
- The Fabricator Podcast
- Published:
- 04/30/2024
- Running Time:
- 53:00
Seth Feldman of Iowa-based Wertzbaugher Services joins The Fabricator Podcast to offer his take as a Gen Zer...
- Industry Events
Pipe and Tube Conference
- May 21 - 22, 2024
- Omaha, NE
World-Class Roll Forming Workshop
- June 5 - 6, 2024
- Louisville, KY
Advanced Laser Application Workshop
- June 25 - 27, 2024
- Novi, MI
Precision Press Brake Certificate Course
- July 31 - August 1, 2024
- Elgin,