Vice President and National Sales Manager
- FMA
- The Fabricator
- FABTECH
- Canadian Metalworking
Categories
- Additive Manufacturing
- Aluminum Welding
- Arc Welding
- Assembly and Joining
- Automation and Robotics
- Bending and Forming
- Consumables
- Cutting and Weld Prep
- Electric Vehicles
- En Español
- Finishing
- Hydroforming
- Laser Cutting
- Laser Welding
- Machining
- Manufacturing Software
- Materials Handling
- Metals/Materials
- Oxyfuel Cutting
- Plasma Cutting
- Power Tools
- Punching and Other Holemaking
- Roll Forming
- Safety
- Sawing
- Shearing
- Shop Management
- Testing and Measuring
- Tube and Pipe Fabrication
- Tube and Pipe Production
- Waterjet Cutting
Industry Directory
Webcasts
Podcasts
FAB 40
Advertise
Subscribe
Account Login
Search
Structural steel processing on a smaller scale
A CNC ironworker can open the door to new opportunities in heavy fabricating
- By Ben Flamholz
- April 24, 2017
- Article
- Punching and Other Holemaking
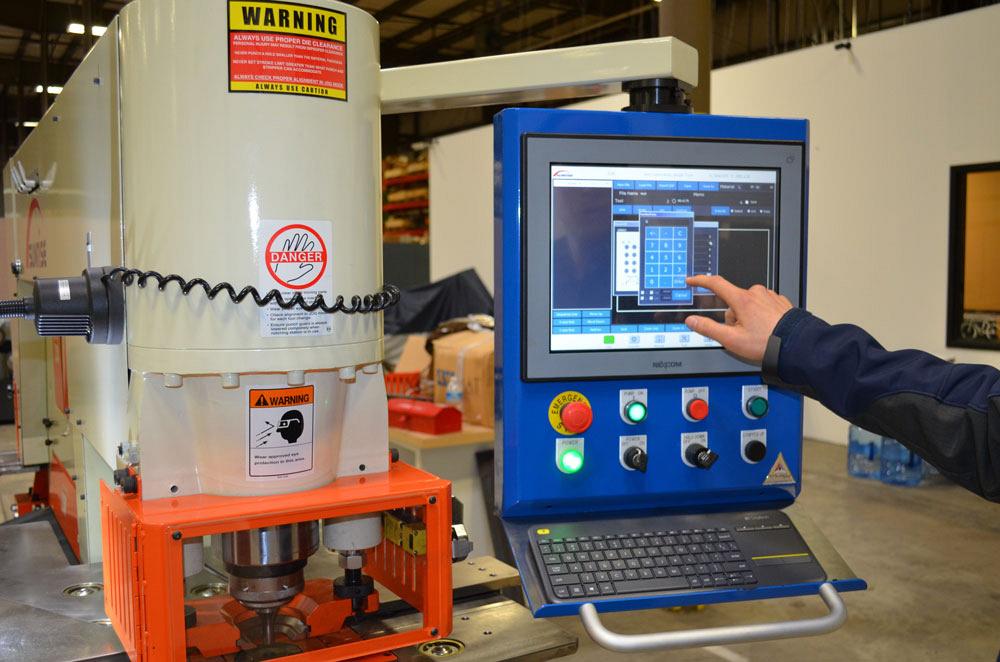
Figure 1
Using the touchscreen control, the equipment operator can plug in the material specifications and the punching instructions to set the machine up. The job then can be saved for future reference if a repeat order occurs down the road.
Structural steel and plate fabricating shops have been working hard to build up their businesses since the Great Recession. Success, of course, is tied to reinvigorating commercial building activity, which has seen a constant ebb and flow for the first half of the year. Dodge Data and Analytics is still forecasting $595 billion in commercial construction starts to hit the books in 2016. The same firm suggests that annual double-digit growth in commercial building activity will occur through 2018.
Are shops ready for this coming growth? In many instances, they may be challenged to keep up with the opportunities.
The fabrication industry in general hasn’t done a great job of grooming the next generation of shop floor talent, and this goes for the structural steel fabricating industry as well, which doesn’t have a consistent pipeline feeding new layout and detailer talent into shops. As baby boomers head for the exits, fabricators need to extract that knowledge from those experienced workers and impart it to the new generation of shop workers to maintain production efficiencies.
Shops also have been slow to adopt the latest processing technology. Plasma and oxyfuel tables are plentiful in the industry, but not all shops have modern beam processing lines. Also, some shop personnel may have some apprehension about working with CNC equipment.
So a manufacturing sector that doesn’t have a strong talent base to replace outgoing experts and is not fully invested in the latest technology to help offset the talent exodus might be in a difficult place in terms of trying to keep up with increased structural steel and plate fabricating work. That doesn’t have to be the case, though.
Ironworkers with semiautomatic and automatic features can help these shops attain production efficiencies without significant expense when compared to full-fledged processing lines. Ironworkers are also very familiar to many shop floor workers, and the CNCs are designed to be user-friendly, even for inexperienced workers.
To understand how a semiautomatic ironworker can change the dynamic on a shop floor, let’s look at four applications. In each example, the fabricator is forced to look at the ironworker in a whole new light.
Example No. 1: Pulling Work From the Plasma Table
One of the biggest challenges for any shop is production scheduling. Figuring out in what order jobs get fabricated and just how they are completed are the keys to ensuring the shop floor runs smoothly and customers get on-time deliveries.
The fabricator in this example sees his plasma cutting table being dominated with cutting out small base plates and connector plates with interior holes. The jobs take up valuable production time on the plasma cutting table and speed up the demise of plasma cutting consumables with each pierce to make a hole. Could there be a better way?
The fabricator finds that a CNC ironworker with a semiautomatic X- and Y-axis punching table might be a cost-effective answer to his production predicament. He can move parts to the ironworker, and the plasma table then can be used for cutting out larger blanks, which come off the table much more quickly than several smaller parts.
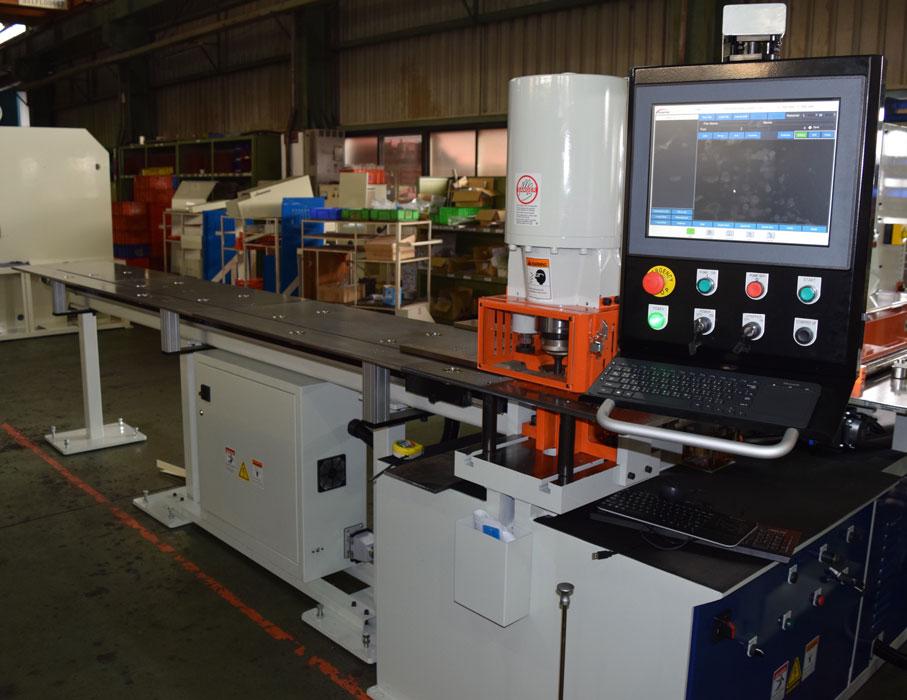
Figure 2
This is an example of a semiautomatic X- and Y-axis positioning table for punching. Once the program is initiated, the X and Y axis move into position. Changing out punches and dies takes only a few minutes and has the option of adding a triple punch feature to allow up to three different punch styles to be used.
The semiautomatic ironworker accepts the DXF and DWG files he is currently using on his plasma. The CNC equipment can access those files via Wi-Fi, USB, or Ethernet connection. This all but eliminates program time on the 15-inch color touchscreen controller (see Figure 1).
Now the operator takes the plate, angle, or channel, which can be up to 1.5 in. thick, places it against the CNC X and Y stops, initiates the punch sequence, and simply holds the material against the stops as the machine runs the program (see Figure 2). Ball transfers on the table are used to make loading and unloading easier for the operator. The ironworker is cable of delivering 480 IPM of movement and ±0.004-in. accuracy.
Standard punches and dies are used, so the cost of running this equipment is minimized. An integrated lubrication system, hydraulic oil filter, and cooler further assist in keeping costs down.
The fabricator also has the flexibility to handle larger plates and structural sections on the CNC ironworker by extending the X-axis table to as large as 26 in. wide by 10 ft.
Example No. 2: The Stop-and-Go Workstation Goes Away
Metal fabricators are a creative lot. In this instance, a shop punches a lot of holes in 2-in.-wide, 20-ft.-long pieces of angle iron and has set up a rig with different stops to feed the angle iron into the punching area of a 1970s ironworker. The operator sets the angle in the rig and against the first stop, steps on the foot pedal, watches the punch make the hole, manually advances the material to the next stop, steps on the foot pedal, and proceeds until the job is finished. It’s simple and effective, but time consuming.
The owner of the shop recognizes that the operator is the bottleneck in this particular operation. Although the setup on the ironworker operates as designed, the ironworker is not in the greatest shape, and the changeover from one pattern to the next typically takes quite some time.
To speed up the processing of these angle pieces, the shop invests in a dual-cylinder ironworker with an automated feed and punching. The operator sets the angle iron into the feed, clamps the end, and watches the rack-and-pinion drive feed the entire length into the machine’s punch (see Figure 3). CNC software controls the punching sequence of one hole every 3 in., delivering a 0.004-in. tolerance when the job requires only a 0.125-in. tolerance. A hydraulic stripper keeps the slugs out of the punch’s way and assists in maintaining machine uptime.
The ironworker also can have two hydraulic cylinders, which allow the operator to run the automated punching function while he is shearing plate to length on the other side of the machine.
Example No. 3: Maximizing Labor
One of the most promising aspects of any upgrade to automated equipment is making the most of existing labor. Whereas an operator was once dedicated to one machine to perform manual tasks, now he can oversee two production operations if automation is a part of one of them.
A fabricator recognizes this potential when he sees an automatic feed attached to the shear of a CNC ironworker (see Figure 4). The shop is heavily involved in fabricating base plates, connector plates, and specialty parts for its metal buildings business, and that typically requires someone spending most of the day sawing or shearing the parts to length. The automatic feed, however, can take over that task.
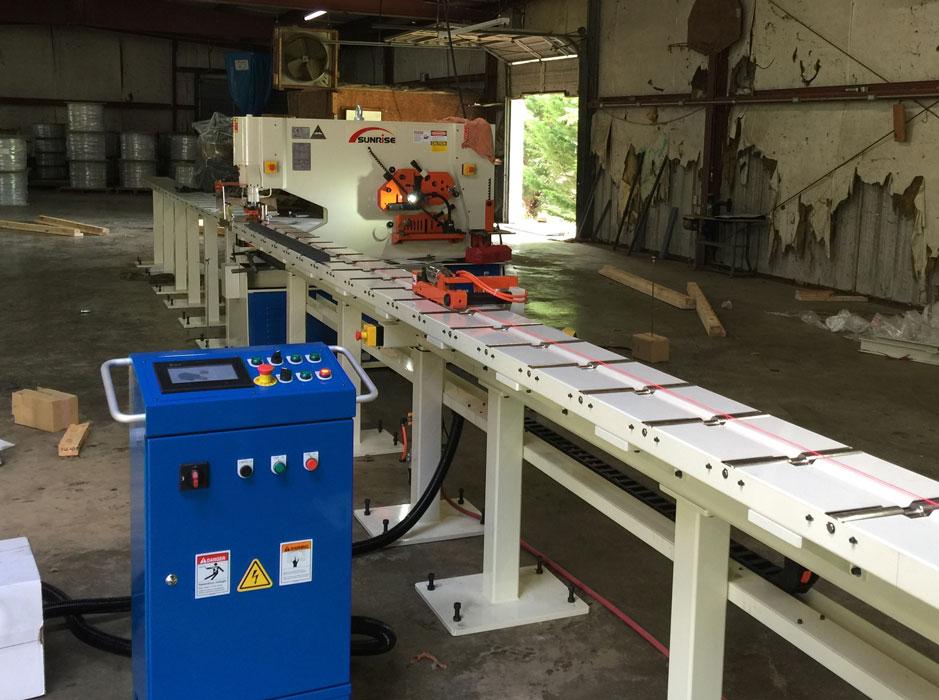
Figure 3
With an automated feed on the ironworker’s punch, the equipment operator can attend to other activities while the material is fed into the system.
The feed table accommodates plate up to 40 ft. long and up to 30 in. wide. The operator loads the part on the feed table, plugs in the job that details the cut list, and watches the feed pull the material into the shear that has an integrated hydraulic hold-down.
Because the machine has dual hydraulic cylinders, it can run two operations at once. As the shear cuts each piece to length, the operator picks up the drops and uses the ironworker’s punch station, typically outfitted with a CNC, to complete the job. The operator accomplishes both tasks in the time that it used to take just to shear the parts to size. Also, the two fabrication activities take place without the need to move parts across the facility from a shearing station to a punching station.
Example No. 4: Plate Processing, but Not Beam Processing
A structural steel fabricator that has traditional beam processing lines on its shop floor wants something to handle its flat bar projects. However, it has no plans to invest in a new beam line because of the expense. A fully automated CNC ironworker (see Figure 5) turns out to be the answer to fulfill this production niche.
The new automated punch and shear system is designed for parts with a maximum width of 20 in. and length of 30 ft. In the triple-punch arrangement, the line can work with a maximum thickness of 0.75 in. In a single-punch setup, it has a maximum material thickness of 1 in.
After the program has been loaded into the CNC, the operator can use the full suite of onboard editors to specify the quantity needed, material length, and width. The operator also has the ability to nest different patterns into each run.
Once the material is loaded onto the machine, the pneumatic clamps and material guides engage, beginning the process to feed the material into the punching and shearing booth.
The entire automated punching, shearing, and even stamping sequence is performed in an enclosed metal cube that has a window for inspection of the fabricating operations. Even though it may look like major structural steel processing equipment, an ironworker is at the heart of the line.
About the Author
subscribe now
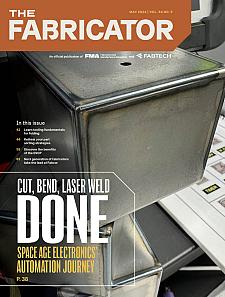
The Fabricator is North America's leading magazine for the metal forming and fabricating industry. The magazine delivers the news, technical articles, and case histories that enable fabricators to do their jobs more efficiently. The Fabricator has served the industry since 1970.
start your free subscription- Stay connected from anywhere
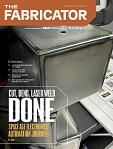
Easily access valuable industry resources now with full access to the digital edition of The Fabricator.
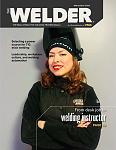
Easily access valuable industry resources now with full access to the digital edition of The Welder.
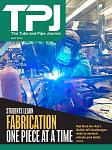
Easily access valuable industry resources now with full access to the digital edition of The Tube and Pipe Journal.
- Podcasting
- Podcast:
- The Fabricator Podcast
- Published:
- 04/16/2024
- Running Time:
- 63:29
In this episode of The Fabricator Podcast, Caleb Chamberlain, co-founder and CEO of OSH Cut, discusses his company’s...
- Trending Articles
Tips for creating sheet metal tubes with perforations
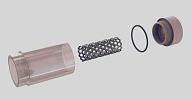
Supporting the metal fabricating industry through FMA
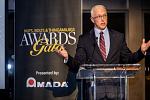
JM Steel triples capacity for solar energy projects at Pennsylvania facility
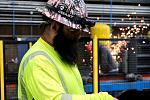
Are two heads better than one in fiber laser cutting?
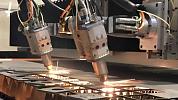
Fabricating favorite childhood memories
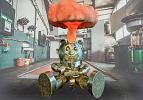
- Industry Events
16th Annual Safety Conference
- April 30 - May 1, 2024
- Elgin,
Pipe and Tube Conference
- May 21 - 22, 2024
- Omaha, NE
World-Class Roll Forming Workshop
- June 5 - 6, 2024
- Louisville, KY
Advanced Laser Application Workshop
- June 25 - 27, 2024
- Novi, MI