- FMA
- The Fabricator
- FABTECH
- Canadian Metalworking
Categories
- Additive Manufacturing
- Aluminum Welding
- Arc Welding
- Assembly and Joining
- Automation and Robotics
- Bending and Forming
- Consumables
- Cutting and Weld Prep
- Electric Vehicles
- En Español
- Finishing
- Hydroforming
- Laser Cutting
- Laser Welding
- Machining
- Manufacturing Software
- Materials Handling
- Metals/Materials
- Oxyfuel Cutting
- Plasma Cutting
- Power Tools
- Punching and Other Holemaking
- Roll Forming
- Safety
- Sawing
- Shearing
- Shop Management
- Testing and Measuring
- Tube and Pipe Fabrication
- Tube and Pipe Production
- Waterjet Cutting
Industry Directory
Webcasts
Podcasts
FAB 40
Advertise
Subscribe
Account Login
Search
4 machine safeguarding myths debunked
Believing these myths can lead to a dangerous shop floor
Editor’s Note: This article is adapted from “Debunking Machine Safeguarding Myths,” a webinar presented by Rockford Systems LLC, Rockford, Ill.
Annual injuries resulting from lack of proper machine guarding aren’t declining at a significant rate. In fact, a lack of proper machine guarding ranks consistently among OSHA’s most common citations. But the actual price tag is much higher than simply the citation fines. Indirect costs also include damaged facilities or equipment, medical expenses, injured or replacement personnel, and lawsuits.
Accidents that occur on equipment without proper safeguarding can lead to life-changing injuries or even death. Per OSHA, workers who operate and maintain machinery suffer approximately 18,000 amputations, lacerations, crushing injuries, abrasions, and—most profoundly—more than 800 deaths per year. In 2016 alone, 88 percent of the total number of OSHA machine guarding violations were classified as “serious,” meaning one in which there is a substantial probability of death or serious physical harm, and that the employer knew, or should have known, about the hazard. And according to some surveys, 50 percent or more of metal fabricating machinery in the U.S. does not comply with the critical safety requirements for guarding outlined by OSHA, ANSI, and the NFPA 79 Electrical Standard for Industrial Machinery.
After a decade of abysmal statistics, manufacturers need to make proper machine safeguarding a higher priority. No one wants to see anyone get hurt on the job.
Much of the problem lies with several persistent myths that pervade industry. Debunking these should help manufacturers view their machine safeguarding situation from a fresh perspective, and perhaps spur proactive changes.
Myth 1: New Machines Are Safe
Many believe that new machines are safe because their manufacturers built them to meet up-to-date safety standards and regulations. But this depends on the country where the machines were built, as well as the safety standards the machinery manufacturers used as a guideline for designing, building, and installing the system. It also depends on the control and electrical systems the machines have.
When OEMs sell machines, they take manufacturing costs into account, and in some cases, they may be concerned about the liability of providing the safeguards. This can be especially true for machines that can be used in various ways, depending on application, workpieces involved, tooling, and other equipment used in the production process.
Consider a mechanical press. The press itself is, in effect, a big hammer that provides consistent force stroke after stroke. To keep an operator safe requires a machine owner to look at the entire system: not just the press, but the tooling, how the pieces arrive and depart from the work envelope, specific motions the operator makes to process that workpiece, and more. Machine OEMs sometimes hesitate to provide safeguarding for this very reason.
Note that this situation is changing somewhat, mainly because some Asian and European machine manufacturers are starting to provide their machines fully safeguarded. This has caused machine tool manufacturers around the world to start offering safeguarding, if not as a standard feature, then at least as an option.
Also, note that the European machinery guarding standards and the Canadian Standards Association (CSA) often require higher levels of protection than the U.S. OSHA and ANSI safeguarding standards. When the U.S. updates standards, the committees often incorporate elements from the European standards.
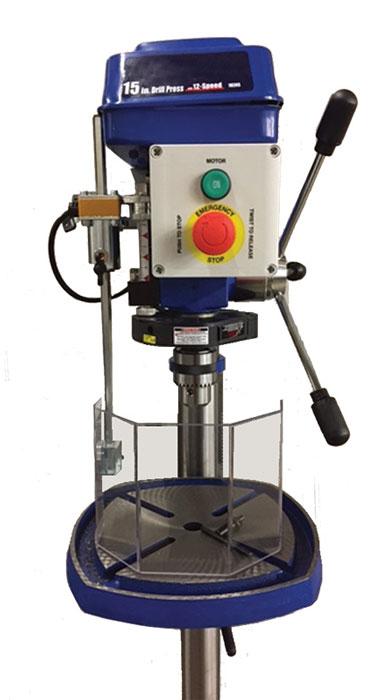
Figure 1
Safeguards, including a motor-starter device, emergency-stop bottom, electrically interlocked shield, and lockout plug, were added after this new drill press was purchased.
Regardless, when fabricators buy new machines, they should specify the safety-related standards with which the equipment must comply. The ANSI B11.19-2010 is one example of this. Also, it is a good idea to reference specific clauses, as opposed to just generally specifying that a machine needs to comply with all local, state, and federal safety standards.
For instance, consider a new drill press—which, again, does not have to be provided with all necessary safeguards by the manufacturer of the machine (see Figure 1). Based on the safety standards, a machine buyer may need to add a motor-starter device that prevents the drill from automatically restarting after a power interruption. A machine usually has this if it has a spring-loaded start button, as opposed to one that produces a mechanical “clicking” sound when pressed.
Drills need an emergency-stop button as well as an electrically interlocked shield that protects workers from chips and sparks. If this shield is removed or swung out of the way, the machine stops and can’t be started again until the shield is in its proper place. And to meet lockout/tagout requirements, a drill needs an electrical disconnect that makes it capable of being locked out when it requires repair or maintenance.
All these elements are needed to make this new drill press compliant with OSHA 1910.212 and the latest ANSI standards.
Myth 2: Older Machines Are Exempt
Many believe that older machines manufactured before certain safety standards existed are somehow grandfathered into compliance. While this may seem logical, it is not true. Machines such as old mechanical power presses, guillotine shears, and engine lathes need to be updated to comply.
Regardless of age, all machines must at least meet OSHA regulations, which were first promulgated in 1970; unfortunately, those regulations have changed little since then.
Unlike the OSHA regulations, ANSI standards must be revisited every five years. This means that the writing committees must either rewrite and update the standard or reaffirm it (that is, accept the standard as is). As a third option, the committee could drop the standard completely (if, say, technology has made the standard irrelevant) or combine it with another standard.
The ANSI B11 safety standards for metalworking machines have more than two dozen sections (though B11.19-2010 generalizes all the safeguarding sections of B11 into one booklet). The B11.1 standard for mechanical power presses and the B11.9 for grinding equipment have corresponding OSHA regulations, but the rest of the machinery, from power press brakes (B11.3) to tube bending (B11.15) to lasers (B11.21), fall under OSHA’s general requirements, 1910.212, which states that the employer must provide safeguarding to protect workers from hazards.
The No. 1 OSHA machine safeguarding violation in the U.S. has to do with a common—and sometimes very old—machine used in the fab shop: the bench or pedestal grinder. Like mechanical power presses, these grinders have both an ANSI standard (B11.9) and a specific OSHA standard. These are sometimes called vertical regulations, since both ANSI and OSHA cover the specific machine type.
To ensure the grinder complies, first ring-test the grinding wheel before you mount it to the machine and document that test for your records, as required by OSHA. Ring testing involves suspending the grinding wheel by its center hole and tapping it around its outside diameter with a nonmetallic object, like a piece of hardwood.
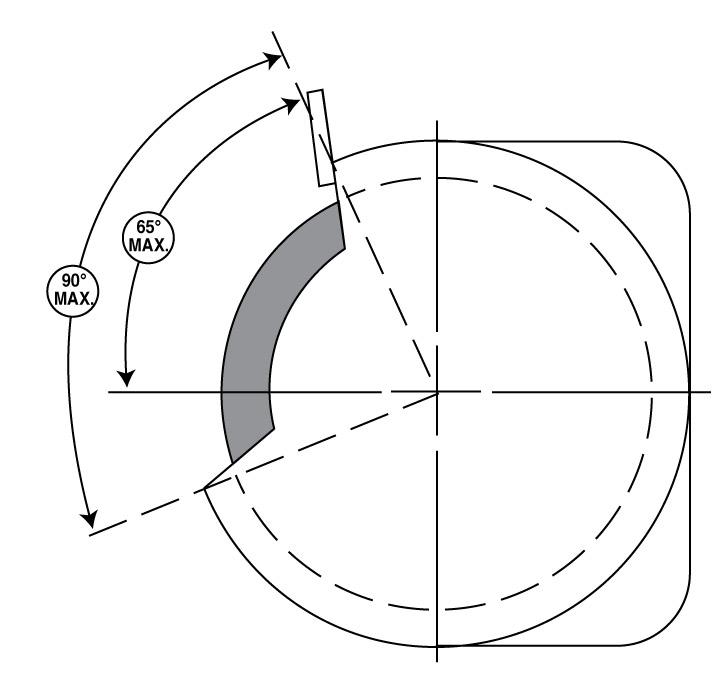
Figure 2
The grinding wheel cover on a bench or pedestal grinder should have an opening that’s no larger than 90 degrees, with no more than 65 degrees from the horizontal plane to the top of the cover, as shown.
When the object taps the wheel, the wheel should ring like a bell. If you tap it and hear a dampened “thud,” you probably have a cracked wheel, and you should never mount such a wheel onto the grinding machine.
OSHA also recommends that the operator stand to the side of the machine for the first minute upon every startup; if the grinding wheel were to shatter, it usually happens within the first minute of operation. This should be part of the machine owner’s safety training.
All grinding wheels should have a directional arrow on the cover that shows the direction of wheel rotation. If maintenance works on the machine, disconnects the power, and accidentally reverses the phases, the grinding wheel will run backward when it’s restarted, which will loosen the grinding wheel—hence the need for those directional arrows.
The tongue guard, also called a spark arrester, can have no more than a 1/4-in. opening between it and the wheel. The work rest can have no more than an 1/8-in. opening between the rest and the grinding wheel. The wheel cover must cover the wheel and nut. That cover also needs all bolts in place and tightened to maintain its strength and integrity.
The cover itself cannot have an opening that’s more than 90 degrees, with no more than 65 degrees of opening from the horizontal plane to the top of the opening (see Figure 2). The larger the opening a grinding wheel cover has, the more particles and grinding wheel parts can eject and spread should the grinding wheel shatter during operation.
So, what is the most common OSHA violation with abrasive wheel grinders? It’s this: The distance between the work rest and the abrasive wheel surface is more than 1/8 in. This is so commonly missed because as the wheel surface wears down, the clearance between the work rest and wheel grows. If it’s larger than 1/8 in., the setup is in violation of OSHA regulation 1910.215(a)(4). That’s been the No. 1 machine safeguarding citation for more than four decades, going back to the beginnings of OSHA itself. To quickly check if the grinder complies, you can use a grinder check tool (see Figure 3).
Myth 3: Industrial Robots Come Fully Safeguarded
The robot supplier sometimes provides the safeguarding, but not always. Again, like machine OEMs, industrial robot manufacturers sometimes don’t install all the required safeguarding, because safeguarding requirements depend on how the robot is installed and used. Therefore, safeguarding usually is left to a third-party supplier.
Automated machine safety methods fall into two general areas: devices that detect workspace interferences, such as presence-sensing devices, and those that prevent access to the workspace, such as perimeter guarding. The most basic types of robotic safeguarding include pressure-sensitive mats. Moving up in complexity, automated cells can have perimeter guarding doors with monitored safety solenoid-operated interlocks, providing a backup safety circuit if the primary one should fail.
And, depending on the application, many robotic systems have presence-sensing devices with control-reliable circuits as well as area laser scanners to detect workspace interferences.
To follow best safety practices for the minimum perimeter guarding height around a robot cell, you now need to refer to a 2003 CSA standard, which specifies a 72-in. height and a 6-in. sweep between the floor and the bottom of the fence guarding. (An older standard, ANSI/RIA R15.06-1999, specifies a 60-in. height and a 12-in sweep. When U.S. standards committees meet, they often incorporate elements from European and Canadian standards when updating U.S safeguarding standards.)
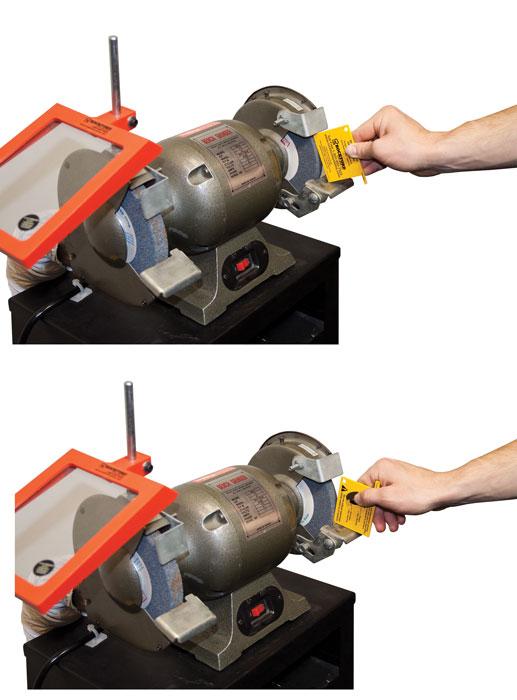
Figure 3
Using a grinder check tool, you can quickly ensure the upper tongue guard is no more than ¼ in. and the lower work rest is no more than 1/8 in. from the wheel surface.
Myth 4:OSHA Regulations Are Only Safety Guidelines, Not Law
That’s not true, and it never has been. The Williams-Steiger Occupational Safety and Health Act of 1970, which established OSHA, states the following: “Employers [must] provide a place of employment free from recognized hazards likely to cause death or serious physical harm to employees.” This clause applies to all states under the federal OSHA supervision as well as those under the state OSHA supervision.
Put simply, by law employers are legally required to follow OSHA regulations. Yes, OSHA regulations have changed very little since the 1970s, so they lack what employers need to know about current machine safety options. The bottom line: OSHA regulations have always been considered as only a starting point. Again, OSHA 1910.212 specifies the general machine safeguarding requirement, stating that the operator and others in the machine area must be protected from exposure to hazards.
To determine those safeguarding requirements, OSHA compliance officers rely heavily on ANSI standards, which include B11 and the R15.06 robot safeguarding standards, as well as the NFPA standards. This is because OSHA 1910.1(a) and OSHA 1910.3(b)(1) states that ANSI and NFPA standards are the recognized national consensus standards, for legislative purpose.
B11.19 covers the performance criteria of four safeguarding options: guards (fixed, adjustable, and interlocked), safeguarding devices (movable barriers, pull backs, restraints, presence-sensing, two-hand control, and others), awareness devices (barriers, signals, and safety signs), and safeguarding methods (distance, holding, opening, location, and procedures).
The law does say that employees also need to comply with OSHA standards, rules, regulations, and orders applicable to their own actions and conduct. In one case, an employee received proper training on how to avoid a dangerous activity, and yet that operator continued to perform the dangerous act and trained a co-worker to do the same. When that second operator was seriously injured, OSHA cited not the employer but the first employee who continued to work dangerously, even though he was trained to do otherwise (and, most important for the company, that training was well-documented).
Still, the general duty clause of OSHA states that employers must provide employees a workplace free from recognized hazards likely to cause death or serious physical harm. During a few years in the 1970s, OSHA had a window of opportunity to incorporate existing ANSI standards directly into OSHA regulations. That method is no longer available. All the same, OSHA 1910.212 (a)(3)(ii) states that the guarding device shall conform with any “appropriate standards.” Well, as stated earlier, the ANSI and NFPA standards are utilized by reference per OSHA 1910.1(a) and OSHA 1910.3(b)(1), for legislative purpose.
Abiding by and documenting best safeguarding practices, as spelled out in the latest standards, helps your company perform due diligence in case a serious machinery-related accident results in litigation. Most important is this: Abiding by best safety practices is simply the right thing to do.
Images provided by Rockford Systems LLC, 800-922-7533,
www.rockfordsystems.com.
Editor’s note: This article is for informational purposes only and does not represent an official interpretation of U.S. safety rules and regulations. For further information, refer directly to the standards and regulations mentioned in this article.
Related Companies
subscribe now
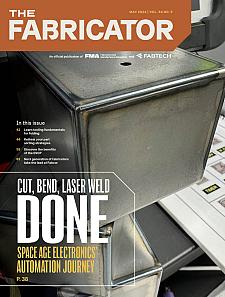
The Fabricator is North America's leading magazine for the metal forming and fabricating industry. The magazine delivers the news, technical articles, and case histories that enable fabricators to do their jobs more efficiently. The Fabricator has served the industry since 1970.
start your free subscription- Stay connected from anywhere
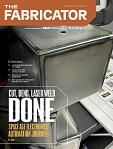
Easily access valuable industry resources now with full access to the digital edition of The Fabricator.
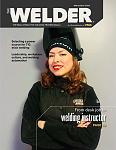
Easily access valuable industry resources now with full access to the digital edition of The Welder.
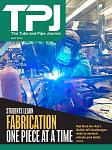
Easily access valuable industry resources now with full access to the digital edition of The Tube and Pipe Journal.
- Podcasting
- Podcast:
- The Fabricator Podcast
- Published:
- 04/30/2024
- Running Time:
- 53:00
Seth Feldman of Iowa-based Wertzbaugher Services joins The Fabricator Podcast to offer his take as a Gen Zer...
- Industry Events
Pipe and Tube Conference
- May 21 - 22, 2024
- Omaha, NE
World-Class Roll Forming Workshop
- June 5 - 6, 2024
- Louisville, KY
Advanced Laser Application Workshop
- June 25 - 27, 2024
- Novi, MI
Precision Press Brake Certificate Course
- July 31 - August 1, 2024
- Elgin,