Vice President of Sales
- FMA
- The Fabricator
- FABTECH
- Canadian Metalworking
Categories
- Additive Manufacturing
- Aluminum Welding
- Arc Welding
- Assembly and Joining
- Automation and Robotics
- Bending and Forming
- Consumables
- Cutting and Weld Prep
- Electric Vehicles
- En Español
- Finishing
- Hydroforming
- Laser Cutting
- Laser Welding
- Machining
- Manufacturing Software
- Materials Handling
- Metals/Materials
- Oxyfuel Cutting
- Plasma Cutting
- Power Tools
- Punching and Other Holemaking
- Roll Forming
- Safety
- Sawing
- Shearing
- Shop Management
- Testing and Measuring
- Tube and Pipe Fabrication
- Tube and Pipe Production
- Waterjet Cutting
Industry Directory
Webcasts
Podcasts
FAB 40
Advertise
Subscribe
Account Login
Search
Advances in exoskeleton technology improve productivity, safety
Modern exoskeletons are lighter, cooler, more comfortable
- By Kirk Stema
- July 26, 2023
- Article
- Safety
Worker safety and productivity do not have to be competing objectives. After all, without safe workers, there is no productivity. When productivity demands are high and employees are expected to work an abundance of overtime, they get fatigued and the potential for injury increases. Add to this an aging population and the risk for injury goes up even more. So, what can be done about it?
Workers can wear an external skeleton, or exoskeleton.
The literal meaning of the word exoskeleton is “outside skeleton.” In nature, an exoskeleton is a reinforced covering that supports and protects the bodies of many invertebrates (animals without backbones).
Types of Exoskeletons
Exoskeletons designed for humans come in four basic types:
- Upper-body exoskeletons support the arms, elbows, shoulders, and neck during work in elevated arm postures.
- Mid-body exoskeletons help alleviate compressive forces on the back during repetitive lifting.
- Lower-body exoskeletons offer relief during repetitive squatting, ankle flexion, standing, and walking.
- Full-body exoskeletons are designed for people, such as military personnel, who transport packs and supplies from point to point in extreme and various conditions.
Each type comes in many different forms with varying levels of complexity, cost, and weight. Some are powered and use batteries or electric cable connections to run sensors and actuators. Others are passive, using only springs and cables or stretch materials to support or restrict movement.
Design Evolution
Commercialized exoskeleton technology advanced rapidly in 2015, although the speed at which exoskeletons are being introduced into the market has slowed over the last year. This slowdown might be due to the extra time being spent on technology advancements to make exoskeletons more flexible, comfortable, and reliable.
Some companies are focusing on more complex designs, and many others are chasing particular design innovations for specific applications. This is viewed by some as a good sign that the potential users are starting to ask the right questions before purchasing an exoskeleton and taking time to select the right one to meet a specific need.
When exoskeletons first hit the market, they came with safety, weight, and comfort concerns, and user feedback has prompted redesigns. As the market responds to what users like and don’t like about these products, exoskeletons are becoming lighter, cooler, and more comfortable.
Moving from rigid designs to flexible designs has been a recent evolution for most exoskeletons. Rigid designs are applicable when posture correction is needed; otherwise, a flexible design is more natural and comfortable.
Designs using powered actuators, electric clutches, and microcontrollers to replace springs and cables are starting to make their way into the market, and smart sensors that help control gait or provide static support are becoming a reality. Robotic gloves for improved hand strength also are gaining acceptance.
Exoskeletons designed for humans come in upper-body, mid-body, lower-body, and full-body styles to assist with many industrial tasks, such as welding, inspecting, and assembly.
Another advancement allows for attachments. For example, one optional attachment provides head support engineered to make the head weightless when leaning forward or backward during assembly or welding. Wider strap configurations over body contact points are becoming the norm.
A recent development is a smart exoskeleton that uses sensors to monitor posture and movement over the course of the day to provide useful data. For example, the data can be used to quantify use time, different postures encountered during work, or repeatablity of work cycle time and
travel distances. Encouraging Worker Acceptance
Exoskeletons have to be comfortable and provide full range of motion. Heat buildup, weight, and interference with movement and working in tight places will impede worker acceptance.
Providing built-in comfort features like breathable pads for backs and hips, cooling fans, gel pads, padded armrests, lumbar support, and comfortable and breathable adjustment straps all help with employee acceptance.
Convenient line-side storage and regular maintenance also help with acceptance. If exoskeletons are “easy in/easy out,” with quick adjustments when needed, worker acceptance—and improved safety—are more likely.
Exoskeleton Limitations
Exoskeletons do not remove all risk for workers, so understanding their limitations is important.
Limitations are determined through performance testing in the lab and in the field, with real workers performing real jobs. For example, depending on the design type, an exoskeleton may provide maximum benefit when the user’s arms are elevated between 90 to 135 degrees, or during trunk bending at 45 degrees.
One exoskeleton may be designed for standing but not sitting; another may be designed for both. Some may be ideal for handling weights less than 12 lbs., while others can handle more than that. A combination of mid-body and upper-body units might be great for changing tires on a lift with arms extended at 90 degrees, but not while kneeling on the ground.
It is important to remember that exoskeletons are designed with a specific use in mind. Using it outside its intended purpose can come with its own set of challenges, safety risks, and employee acceptance concerns.
Testing Shows Impact on Productivity and Safety
Extensive field and lab research on how the body and the worker respond to working with and without an exoskeleton has shown the positive impact the technology has had on worker safety and productivity.
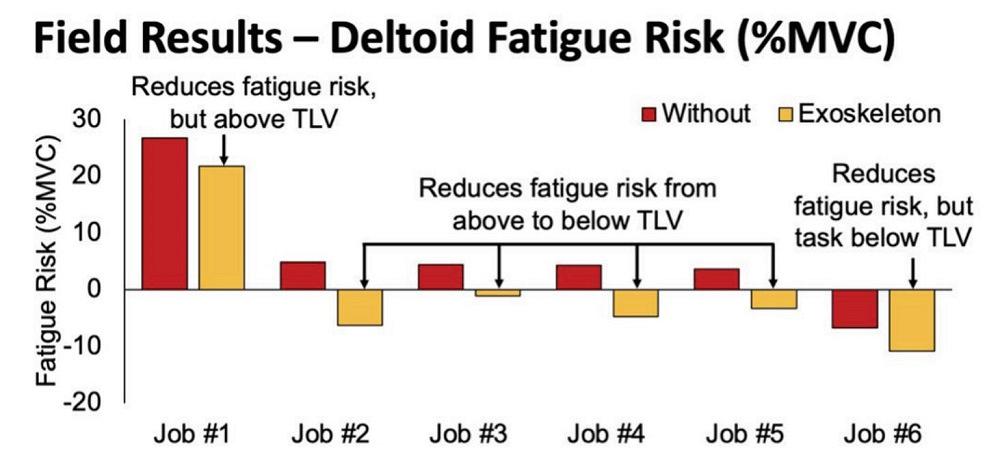
FIGURE 1. Iowa State University conducted IRB-approved studies to document the benefits and limitations of exoskeletons. Billions of data points continue to be collected on users while working with and without an exoskeleton during lab and field testing. Shoulder injury risk assessment (SIRA) for water mitigation installers in Whitter Alaska showed injury risk and fatigue with an exoskeleton to be lowered below or closer to the Threshold Limit Value (TLV Zero Line).
Numerous review boards have been formed to ensure that the designs are safe for deployment and daily use. For example, ASTM Intl. formed Committee F48 on Exoskeletons and Exosuits in 2017, which comprises numerous subcommittees working on voluntary consensus standards for what is being manufactured today and in the future.
Studies are being conducted to document what happens when a user works with and without an exoskeleton (see Figures 1 and 2). Some upper-body exoskeleton studies show productivity gains of 3% to 8% depending on the job (see Figure 3).
This data, coupled with advancements in AI machine learning and 3D video capture technology, can provide accurate shoulder injury risk assessments (SIRA) in minutes on a smart phone or tablet (see Figure 4). Currently, the SIRA app is undergoing extensive accuracy testing.
Safety and Productivity Go Hand in Hand
Toyota, one of the earliest adopters of exoskeletons, started using them in 2017. Records of their use showed a reduction in workers’ compensation claim costs. Shoulder injuries dropped to zero on one assembly line after exoskeletons were adopted and provided as personal protection equipment.
Not every company will experience the same level of success, but any risk reduction is a chance to avoid an injury.
Considering both the injury reduction and productivity gains, exoskeleton technology makes sense. Exoskeletons are not going away, and with innovation and advancements, the technology will continue to help reduce injuries and employee suffering, improve quality of life, permit employees to work longer, and boost productivity.
About the Author
Related Companies
subscribe now
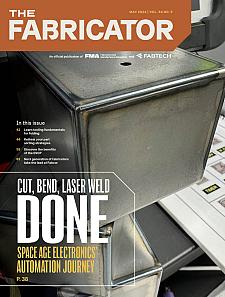
The Fabricator is North America's leading magazine for the metal forming and fabricating industry. The magazine delivers the news, technical articles, and case histories that enable fabricators to do their jobs more efficiently. The Fabricator has served the industry since 1970.
start your free subscription- Stay connected from anywhere
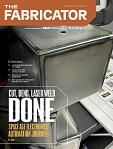
Easily access valuable industry resources now with full access to the digital edition of The Fabricator.
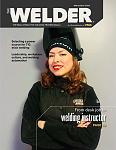
Easily access valuable industry resources now with full access to the digital edition of The Welder.
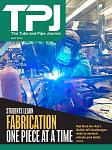
Easily access valuable industry resources now with full access to the digital edition of The Tube and Pipe Journal.
- Podcasting
- Podcast:
- The Fabricator Podcast
- Published:
- 04/16/2024
- Running Time:
- 63:29
In this episode of The Fabricator Podcast, Caleb Chamberlain, co-founder and CEO of OSH Cut, discusses his company’s...
- Trending Articles
Tips for creating sheet metal tubes with perforations
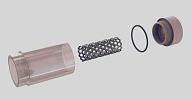
Supporting the metal fabricating industry through FMA
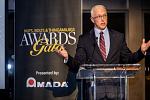
JM Steel triples capacity for solar energy projects at Pennsylvania facility
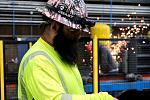
Fabricating favorite childhood memories
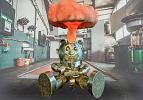
Omco Solar opens second Alabama manufacturing facility
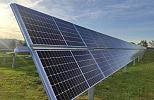
- Industry Events
16th Annual Safety Conference
- April 30 - May 1, 2024
- Elgin,
Pipe and Tube Conference
- May 21 - 22, 2024
- Omaha, NE
World-Class Roll Forming Workshop
- June 5 - 6, 2024
- Louisville, KY
Advanced Laser Application Workshop
- June 25 - 27, 2024
- Novi, MI