Vice President of Operations
- FMA
- The Fabricator
- FABTECH
- Canadian Metalworking
Categories
- Additive Manufacturing
- Aluminum Welding
- Arc Welding
- Assembly and Joining
- Automation and Robotics
- Bending and Forming
- Consumables
- Cutting and Weld Prep
- Electric Vehicles
- En Español
- Finishing
- Hydroforming
- Laser Cutting
- Laser Welding
- Machining
- Manufacturing Software
- Materials Handling
- Metals/Materials
- Oxyfuel Cutting
- Plasma Cutting
- Power Tools
- Punching and Other Holemaking
- Roll Forming
- Safety
- Sawing
- Shearing
- Shop Management
- Testing and Measuring
- Tube and Pipe Fabrication
- Tube and Pipe Production
- Waterjet Cutting
Industry Directory
Webcasts
Podcasts
FAB 40
Advertise
Subscribe
Account Login
Search
Ensuring a plant's electrical system safety
One company's experience with infrared thermography
- By Mark Paulson
- November 29, 2001
- Article
- Safety
![]() |
Many people work in buildings that were constructed more than 40 years ago. At the time they were built, no one could have imagined the power requirements of the 21st century.
An older plant has much more equipment today than it did when it was built, and each piece of equipment pulls more power than was previously required. Computers on every desktop and dozens of printers and copiers throughout a building add to the power usage.
To make matters worse, the typical older plant has been expanded many times, and each time electrical systems simply were added to the original electrical infrastructure. Can the existing electrical system support all the current requirements? What electrical fire hazards are hidden within the walls and ceilings?
This was the situation we found ourselves in recently. Our worries were compounded when we learned that fires have caused more physical plant damage in the past three years than any other single hazard.
We needed a way to verify that our electrical system was safe and to identify potential problems before they became fire catastrophes. As we wrestled with how to accomplish this, we were approached by a representative from our local power company who suggested that we have an infrared thermography inspection.
Inspection With Infrared
Infrared thermography takes thermal radiation from electrical and mechanical systems and converts it into an electronic image or picture. This allows for the detection of problems before these temperatures reach the point at which they can cause an electrical outage or, worse yet, a catastrophic fire.
Infrared thermography also can be used to evaluate roof systems for leaks; to detect problems in steam traps and valves in piping systems; to survey buildings for energy leaks; to examine furnace refractories for gaps and voids; and to detect damaged bearings in motors, pumps, and other rotating machinery.
We were fortunate that our local power supplier, Carolina Power and Light, provided an infrared thermography service. As part of this service, the power company representative came to our plant and, working hand in hand with our maintenance group, surveyed our entire electrical system.
We dictated the extent of our survey. It could be as limited as reviewing only junction boxes and power distribution points or as extensive as reviewing every wire in the plant. In our case, to review all office wiring (10,000 sq. ft.) and all panels throughout our 119,000-sq.-ft. plant took one day. The length of the inspection will vary with the complexity and size of the electrical system to be reviewed.
In some areas power companies do not offer infrared thermography services, leaving companies to search out their own service providers. An inquiry to a local electrical contractor usually can yield information about a service provider in a given area.
Categorizing and Solving Problems
During an infrared thermography inspection, problems are divided into three categories:
1. Minor problems, in which temperatures have risen no more than 36 degrees F above the ambient temperature, require corrective action as scheduling permits.
2. Serious problems — those causing temperature increases of 36 to 90 degrees F above ambient — require corrective measures as soon as possible.
3. Critical problems, in which temperatures have risen more than 90 degrees F higher than the ambient temperature, are considered urgent and require immediate corrective measures. In some cases use of these circuits should be discontinued until repairs are made.
Minor problems can be caused by poor splices in wiring, loose or corroded connections or conductors, loose wires, or load imbalances. Undersized components or loose or corroded conductors can lead to serious or critical problems if left uncorrected.
Our infrared thermography inspection revealed nearly a dozen minor, serious, and critical problems. We determined solutions as each problem was identified and classified. All problems were resolved within a matter of weeks, and we could then operate with peace of mind, knowing that our electrical systems were reliable, capable, and safe.
Staying Alert
To ensure the continued safety of our electrical infrastructure, we have decided to reinspect all systems, with the help of our local power company, on an annual basis. By inspecting annually with infrared thermography, we can anticipate problems long before they become potential fire hazards.
About the Author
Mark Paulson
Aeroglide Corp.
100 Aeroglide Drive
Cary, NC 27511
919-851-2000
subscribe now
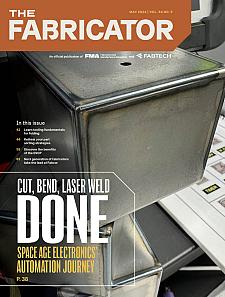
The Fabricator is North America's leading magazine for the metal forming and fabricating industry. The magazine delivers the news, technical articles, and case histories that enable fabricators to do their jobs more efficiently. The Fabricator has served the industry since 1970.
start your free subscription- Stay connected from anywhere
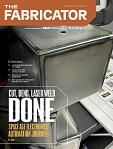
Easily access valuable industry resources now with full access to the digital edition of The Fabricator.
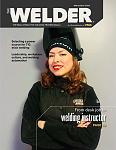
Easily access valuable industry resources now with full access to the digital edition of The Welder.
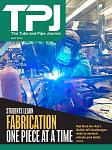
Easily access valuable industry resources now with full access to the digital edition of The Tube and Pipe Journal.
- Podcasting
- Podcast:
- The Fabricator Podcast
- Published:
- 05/07/2024
- Running Time:
- 67:38
Patrick Brunken, owner of Addison Machine Engineering, joins The Fabricator Podcast to talk about the tube and pipe...
- Industry Events
Pipe and Tube Conference
- May 21 - 22, 2024
- Omaha, NE
World-Class Roll Forming Workshop
- June 5 - 6, 2024
- Louisville, KY
Advanced Laser Application Workshop
- June 25 - 27, 2024
- Novi, MI
Precision Press Brake Certificate Course
- July 31 - August 1, 2024
- Elgin,