Welding Accessories Sales Specialist
- FMA
- The Fabricator
- FABTECH
- Canadian Metalworking
Categories
- Additive Manufacturing
- Aluminum Welding
- Arc Welding
- Assembly and Joining
- Automation and Robotics
- Bending and Forming
- Consumables
- Cutting and Weld Prep
- Electric Vehicles
- En Español
- Finishing
- Hydroforming
- Laser Cutting
- Laser Welding
- Machining
- Manufacturing Software
- Materials Handling
- Metals/Materials
- Oxyfuel Cutting
- Plasma Cutting
- Power Tools
- Punching and Other Holemaking
- Roll Forming
- Safety
- Sawing
- Shearing
- Shop Management
- Testing and Measuring
- Tube and Pipe Fabrication
- Tube and Pipe Production
- Waterjet Cutting
Industry Directory
Webcasts
Podcasts
FAB 40
Advertise
Subscribe
Account Login
Search
When hot, welding becomes not so hot
Exposure to heat, sweat makes welding difficult, but pole welders find a helmet helps
- By Gary Stubblefield
- February 28, 2012
- Article
- Safety
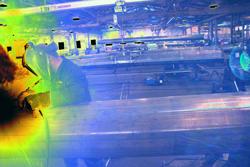
Figure 1: Welding transmission poles and structures is a challenging job even in the most comfortable of environments. Combine the activity with very hot conditions, and the task becomes that much more difficult. Valmont Industries, Tulsa, Okla., has found that an air-cooling system inserted into a lightweight welding helmet can help. Photos courtesy of Miller Electric Mfg. Co.
The North and South Poles may be the only places on the planet that don’t have poles manufactured by Valmont Industries.
The Omaha, Neb.-headquartered company bills itself as the largest manufacturer of transmission and structural products in the world. Its lighting, traffic, utility, and communication poles and towers are located in cities across the U.S. and the world. It also has other divisions, such as its irrigation equipment business that designs and fabricates products to bring water to croplands. Altogether, the company operates 95 facilities in 17 countries and employs more than 8,000 people.
At Valmont’s Tulsa, Okla., facility, about 100 welders are up to big things. Working out of a 350,000-sq.-ft. facility, they are fabricating structures that weigh from 500 to 60,000 lbs. In fact, the largest pole in the world—with a bottom section weighing 56,000 lbs.—is built there, according to Tony Schuler, Valmont’s operations director.
Everything that the Tulsa facility fabricates is done in-house. Massive sheets of grade 65 carbon steel, anywhere from 0.1875 to 7 in. thick, are shipped to the nearby inland Port of Catoosa and sent to the shop to be fabricated into the super-sized transmission poles and structures.
A lot of welding expertise is needed to weld up these large fabrications—all of which must meet American Welding Society D1.1 structural codes. But even the best welders sometimes struggle because of the environment. In Tulsa, that is particularly true, especially in summers.
The average daily high temperature in Tulsa in July and August is 93 degrees F. Coupled with an indoor work environment where welding is occurring, fabricators can get real hot, real fast.
“In the summertime, our welders are working in 100-degree and higher temperatures, so we are always looking for ways to move air and keep our employees cooler,” Schuler said.
Working with Best Welders Supply, the local welding equipment distributor, Schuler investigated ways to keep Valmont’s welders cool and productivity levels up. That led to a trial of a new headgear-integrated cooling device—and the results appear to be promising.
Keeping It Cool
Welders tested Miller Electric Mfg. Co.’s CoolBand™ system attached to Peformance™ welding helmets (see Figure 1). Schuler said that after three months of testing, welders appeared to be more comfortable and were able to get more work done in the same amount of time because the cooling device kept them refreshed and they spent less time wiping off sweat and defogging glasses and lenses.
“We decided to go full-blown and offer those to all the welders and fitters that we have out there on the shop floor,” Schuler said.
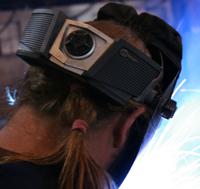
Figure 2: Most of the weight of the air-cooling band is in the back where the battery is located. It acts as a counterbalance to the front of the welding helmet that it is attached to.
The cooling technology, which is inserted inside a welding helmet (see Figure 2), runs on a rechargeable battery and comprises strategically located air vents. Downward air vents provide constant air movement over a welder’s face and temples, and upward air vents provide air movement over a welder’s entire head. The air movement can lower the temperature inside a welding helmet by 8 degrees F, according to Miller Electric.
“We’re in 105-degree heat, and we don’t set a break time. If a welder needs to stop and cool off, they just do it as needed,” Schuler said. “Before the CoolBand, our operators had to stop continuously, lift their hoods, and wipe the sweat off their faces and out of their eyes. Many times they’d have to splash cold water on their faces too.”
Heat is always going to be an issue for any fabricating facility in the summer. Truthfully, most welders are used to it, but that doesn’t mean they like it.
“I can take the heat anywhere else; I just don’t want it in my face. In this job there’s a lot of lifting, going from seam to seam, weld to weld—and I used to have to stop and wipe my face off and clean my glasses and lens,” said Brian Mears, a Valmont welder. “Now I don’t have that problem. It’s gone.”
Fogged-up glasses are a problem in both summer and winter. Wearing a helmet with safety glasses—an often-overlooked regulation—makes for a tight environment with humid air.
“We weld a lot of long poles that have a bunch of clips on them. We can do this so much faster now because we don’t have to stop, pick up our hood, wipe off our glasses, and then move on,” Mears added.
What Are the Effects of Wearing the Added Gear?
Schuler said welders had two important concerns about a cooling system attached to a welding helmet:
- Would the cooling system run out of battery life too quickly?
- Would the helmet weigh too much with the cooling device attached?
The cooling system battery is designed to last six hours. Mears said he usually charges his during lunch because he works eight- to 10-hour shifts. Even then, he admitted that all of that time is not spent with the arc on, but it’s important that the helmet is ready to go when he is ready to weld.
As for the weight of the helmet, the Performance series is designed to be lighter than previous generations of welding helmets, weighing 17 oz. The cooling system adds another 13 oz. of weight.
Mears said that he used to get headaches as a result of using heavier welding helmets. Because the hood was heavy, he had to tighten the band so that it wouldn’t fall; the tight headband gave him the headaches.
The lighter helmets eliminate those tight bands. In fact, because of the helmet’s autodarkening feature, he keeps his hood down when he moves from weld to weld on the long structural parts.
Looking back, Mears said he believes he raised and lowered his hood hundreds of times per day to wipe away sweat and clear the fog from his safety glasses. Since working with the new cooling system and helmet, he said he has decreased that activity by 60 to 65 percent.
Metal-cored Wire Shortens Long Welding Job
Valmont welders work on plenty of long poles. Anything that can be done to help the welder to complete the job more quickly is good for the person under the welding helmet and good for the company because productivity increases.
One step that the company has taken to boost productivity is to move from flux-cored wire to metal-cored wire for all of its welding applications. Hobart’s Tri-Mark Metalloy Vantage NI1 metal-cored wire has helped to increase deposition rates and travel speeds, while also reducing postweld cleanup, according to Tony Schuler, Valmont’s operations director.
“We found that metal-cored [wire] is very clean, has a high deposition rate, is extremely strong, galvanizes well, and requires very little cleanup,” he said.
As an example, Schuler said that he can run 0.052-in. metal-cored wire against 0.0625-in. flux-cored wire on an 18.375-in. bevel plate, and he will run off the end of the plate about 25 percent faster with the metal-cored wire.
“Metal-cored is a little more costly, but for our operation, only 15 percent of our welding costs are consumables. Eighty-five percent of our costs are labor,” he said. “So if I can save 2 percent in labor, then I am doing better than even a 25 percent savings in wire and gas.”
It’s all about a better welding process, not so much about saving money on gas and wire.
“I’m looking more as to how many minutes can I save on this piece,” Schuler added.
About the Author
Gary Stubblefield
Miller Electric Mfg. Co.
1635 W. Spencer St. P.O. Box 1079
Appleton, WI 54912
920-734-9821
Related Companies
subscribe now
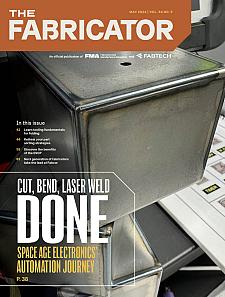
The Fabricator is North America's leading magazine for the metal forming and fabricating industry. The magazine delivers the news, technical articles, and case histories that enable fabricators to do their jobs more efficiently. The Fabricator has served the industry since 1970.
start your free subscription- Stay connected from anywhere
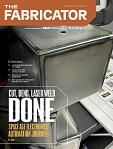
Easily access valuable industry resources now with full access to the digital edition of The Fabricator.
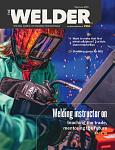
Easily access valuable industry resources now with full access to the digital edition of The Welder.
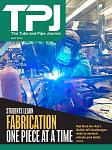
Easily access valuable industry resources now with full access to the digital edition of The Tube and Pipe Journal.
- Podcasting
- Podcast:
- The Fabricator Podcast
- Published:
- 05/07/2024
- Running Time:
- 67:38
Patrick Brunken, VP of Addison Machine Engineering, joins The Fabricator Podcast to talk about the tube and pipe...
- Industry Events
Laser Welding Certificate Course
- May 7 - August 6, 2024
- Farmington Hills, IL
World-Class Roll Forming Workshop
- June 5 - 6, 2024
- Louisville, KY
Advanced Laser Application Workshop
- June 25 - 27, 2024
- Novi, MI
Precision Press Brake Certificate Course
- July 31 - August 1, 2024
- Elgin,