Senior Editor
- FMA
- The Fabricator
- FABTECH
- Canadian Metalworking
Categories
- Additive Manufacturing
- Aluminum Welding
- Arc Welding
- Assembly and Joining
- Automation and Robotics
- Bending and Forming
- Consumables
- Cutting and Weld Prep
- Electric Vehicles
- En Español
- Finishing
- Hydroforming
- Laser Cutting
- Laser Welding
- Machining
- Manufacturing Software
- Materials Handling
- Metals/Materials
- Oxyfuel Cutting
- Plasma Cutting
- Power Tools
- Punching and Other Holemaking
- Roll Forming
- Safety
- Sawing
- Shearing
- Shop Management
- Testing and Measuring
- Tube and Pipe Fabrication
- Tube and Pipe Production
- Waterjet Cutting
Industry Directory
Webcasts
Podcasts
FAB 40
Advertise
Subscribe
Account Login
Search
2017 metal fabrication forecast: Voyage into the unknown
Under a Trump presidency, markets such as energy could see dramatic change—or not
- By Tim Heston
- November 29, 2016
- Article
- Shop Management
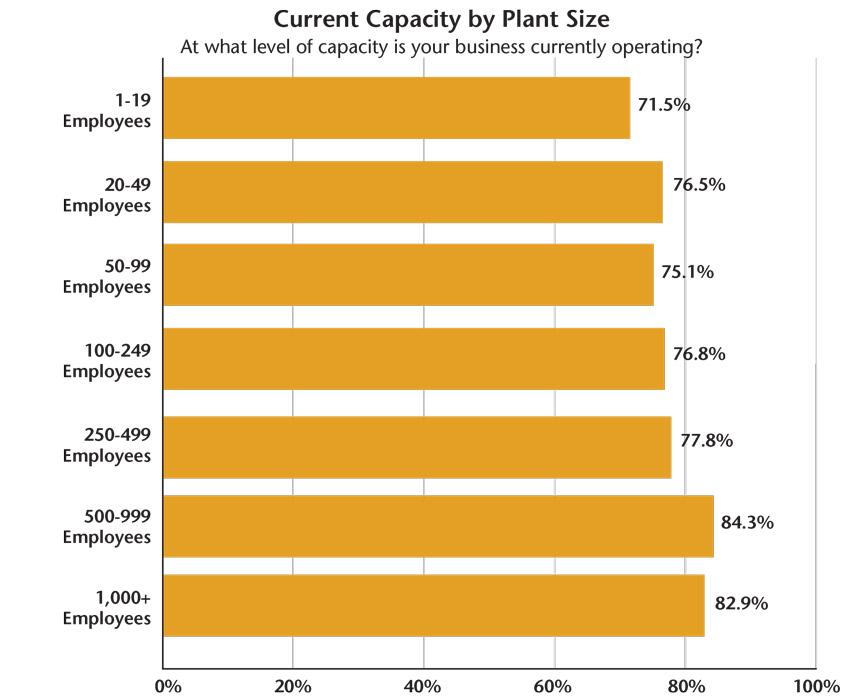
Capacity levels in metal fabrication seem to be higher at larger companies, a trend that may reflect tight capacity situations in certain sectors, like automotive. Source: “2017 Capital Spending Forecast,” FMA.
Before the election most economic forecasters were expecting 2017 to be more of the same: slow overall growth, commodity markets struggling, while markets like automotive sustaining at high levels.
Then Donald Trump won the election.
The FABRICATOR went to press just after election night, when many economists and analysts espoused concern, some very negative and—particularly as it became clear the stock markets would not tumble as predicted—some positive. Yet most espoused predictions with the same caveat: We really have no idea.
Chris Kuehl, economic analyst for the Fabricators & Manufacturers Association International®, said that some immediate postelection estimates for 2017 ranged from a recession with significant job losses to moderate growth of about 0.6 percent GDP. Then, hours later, the stock market jumped to record highs, driven by companies in the health and energy sectors, which are thought to benefit under a Trump presidency. At press time, many were predicting GDP growth for 2017 between 1.5 and 2.5 percent, or even slightly higher. So which is correct?
As of early November, it simply was too soon to tell.
In a report released in the early hours of Nov. 9, Paul Ashworth, chief North American economist for Capital Economics, said, “We simply can’t know what type of president Trump will be.”
Sector Forecasts
Considering dramatic changes in Washington, outlooks for 2017 continue to be a moving target. But as Kuehl pointed out, “The rules of supply and demand still apply.”
A report prepared before the election by the Center for Automotive Research in Ann Arbor, Mich., stated that automotive production will remain flat in 2017, but the level of production will likely remain high, with more than 17 million vehicles expected to be sold. If the automotive industry maintains record levels of production, that’s hardly bad news.
Construction, including commercial construction, is also expected to increase next year, though of course that depends heavily on the local market. In early November, sources at the Associated General Contractors of America in Arlington, Va., forecast mid-single-digit growth next year. Hot spots include office construction, hospitals, and, most significantly, entertainment venues.
Note that after the election, stocks for Caterpillar and other construction-related firms soared, anticipating big changes to infrastructure spending, but these probably won’t be coming next year.
“These policies will have no impact on the economy in 2017,” Blu Putnam, chief economist with CME Group, told The Washington Post. “But that’s what markets do.”
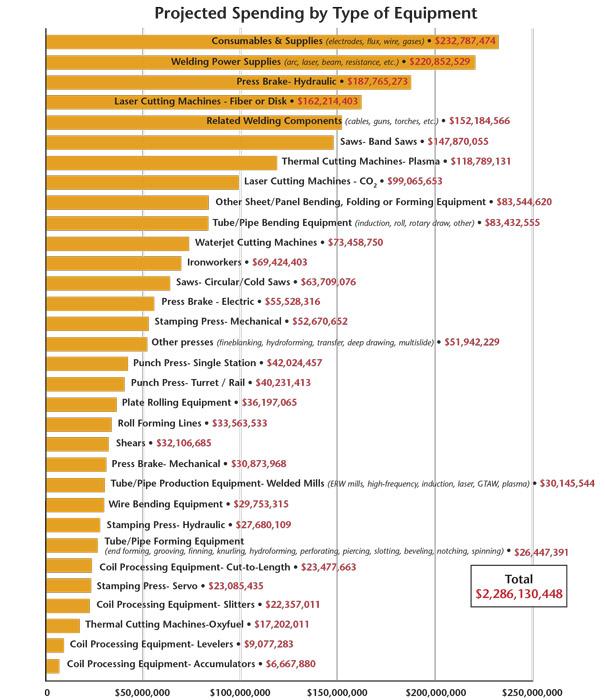
The distribution of planned spending for U.S. fabricators in 2017 reflects spending trends in 2016. Investment in solid-state (fiber and disk) lasers continues to rise, while spending on CO2 lasers continues to fall. Source: “2017 Capital Spending Forecast,” FMA.
Thanks to bumper crops driving down food prices, the agriculture equipment sector continues to struggle, particularly with larger pieces of equipment, though many fabricators are finding opportunities in small ag equipment work. Kuehl added that changes under Trump may spur a stronger dollar, which in turn may hurt food exports, which could affect ag equipment sales. But again, this all depends on what those changes will be and how they come to fruition.
Before the election, most expected sluggishness to remain in oil and gas, and it all hinges on the price of oil. That said, low oil and especially natural gas prices have spurred investments elsewhere, particularly in chemical processing and liquefied natural gas (LNG).
After the election, the predictions changed. As Christopher Helman, a senior editor who covers oil and gas for Forbes, put it, “Expect American oil and gas production to surge. We will see an abrupt end to the Bureau of Land Management’s efforts to grab authority to regulate hydraulic fracturing on federal lands … [and] Trump’s pro-infrastructure regulators will unlock private capital for pipeline projects.”
All the same, many prognosticators cautioned that any dramatic change would be mitigated by the laws of supply and demand, which won’t change no matter who sits in the Oval Office. The regulatory environment may be different, but the world is still awash with fossil fuels.
Meanwhile, after years of growth, aerospace is coming in for a landing. After a dozen years of growth, the industry is experiencing a period of slowing demand, though a bright spot is defense spending.
Commercial trucking continues its trend toward a hub-and-spoke distribution model, with short-haul truckers taking goods from those hubs to their final destination. Long-haul trucking continues its gradual decline. “The big change in trucking is now the warehousing and distribution model,” said Kuehl, whose firm, Kansas City, Kan.-based Armada Corporate Intelligence, follows the transportation sector, among others.
Regarding rail, “The industry’s three cash cows have been coal, agriculture, and oil and gas,” said Kuehl. “Coal is not as far gone as one would think, because we’re exporting a lot of it. But the oil and gas is still off dramatically. Fortunately, for most [rail companies], agricultural shipments are still pretty good.”
Kuehl added that the multimode model—containers from ships being transported by rail and, for the last leg, trucks—is still successful. “It hasn’t grown very much,” Kuehl said, “but it’s still very lucrative [for the rail companies].”
After the election, though, some predicted more bright spots for coal, which in turn could benefit rail. “There will be no chance of a federal carbon tax or a cap-and-trade regime,” Forbes’ Helman predicted. “That’s good news for coal miners and owners of coal-fired power plants.”
Forbes contributor James Conca added that “the oil and gas industry already has more drilling sites it can use. What they really need are more pipelines and transport facilities. So the Dakota pipeline will get built, along with many others in the U.S., with or without federal agents showing up to ‘help.’”

While most fabricators are either on track with their equipment spending or delayed a quarter or two, more than 27 percent said their equipment purchasing plans are delayed indefinitely, a 7 percent rise from last year. Source: “3rd Quarter 2016 Forming & Fabricating Job Shop Consumption Report,” FMA.
Conca added that renewable energy actually should be fine. “The Republican-controlled Congress already extended the renewable energy Production Tax Credit to 2021, so don’t look for renewables to decline anytime soon.”
Technology Spending
Because of the nature of the metal fabrication business, overall trends of a particular sector may not reflect growth trends for a specific company. As always, success hinges on a fabricator’s specific customer base. Those who have diversified and built good reputations in the right markets are feeling the benefits, while those who haven’t are feeling the pain. True, some shops have successfully gained market share in those sluggish markets, but that means other shops are losing business, because the market pie in many commodity markets isn’t getting bigger.
This may be driving the continued polarization of capital equipment spending in the market—that is, fabricators who are on track with their spending plans compared to those who’ve delayed those plans indefinitely. According to FMA’s quarterly “Forming & Fabricating Job Shop Consumption Report,” a little less than half of respondents said their capital spending expenditures were on track, while more than 27 percent said purchases were delayed indefinitely. The latter is up 7 percentage points from 2015.
Going by data gathered before the election, overall metal fabrication equipment spending projections next year reflect an industry that’s holding steady at a high level.
That’s according to FMA’s “2017 Capital Spending Forecast,” released in November 2016 at the FABTECH® tradeshow in Las Vegas. And the distribution of that spending is holding steady as well. Like last year, total expected spending on forming equipment (press brakes, panel benders, folders) is outpacing total spending for laser cutting and punching machines.
The only major movement this year has been in laser cutting. Expected spending on solid-state fiber and disk lasers jumped 36 percent from last year’s survey, while expected spending on CO2 lasers fell 18 percent—to its lowest level in three years. Last year fiber and disk lasers overtook CO2 laser spending for the first time, and that trend seems to be continuing at a swift pace.
Overall equipment spending at U.S. fabricators is decreasing ever so slightly, from $2.35 billion in 2016 to $2.29 billion in 2017—but again, this survey was taken before the election. In an interview after the election, Kuehl said that machinery orders may get a boost as companies buy equipment from overseas before any dramatic changes to trade policy take effect, including the potential for tariffs. “When Trump is in office, that urgency may accelerate.”
Today capacity levels in the industry are from the low 70 percent range to more than 80 percent, according to a recent survey from FMA. In general, the larger the company, the tighter the capacity, which hints at the peak capacity situation in some areas of the automotive supply chain.
Hence the need for continuous improvement and smart investments, both in people and technology, and the need to be ready for any changes that may lie ahead. It’s common practice for custom fabricators to keep capacity at a manageable level so they can react to unexpected variations in demand, a fact of life in most metal fabrication.
Those shops that can react are likely to grow; those who can’t may suffer. Given the years of steady, slow growth we have had—and considering the big unknowns that lie ahead—that statement is probably truer now than ever.
Information for this report came from Armada Corporate Intelligence (www.armadaintel.com), the Center for Automotive Research (www.cargroup.org), Loren C. Scott and Associates (www.lorenscottassociates.com), and Teal Group Corp. (www.tealgroup.com).
About the Author
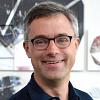
Tim Heston
2135 Point Blvd
Elgin, IL 60123
815-381-1314
Tim Heston, The Fabricator's senior editor, has covered the metal fabrication industry since 1998, starting his career at the American Welding Society's Welding Journal. Since then he has covered the full range of metal fabrication processes, from stamping, bending, and cutting to grinding and polishing. He joined The Fabricator's staff in October 2007.
subscribe now
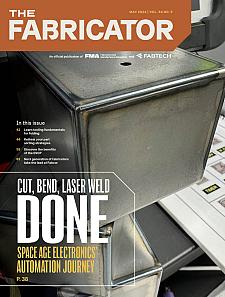
The Fabricator is North America's leading magazine for the metal forming and fabricating industry. The magazine delivers the news, technical articles, and case histories that enable fabricators to do their jobs more efficiently. The Fabricator has served the industry since 1970.
start your free subscription- Stay connected from anywhere
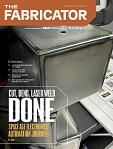
Easily access valuable industry resources now with full access to the digital edition of The Fabricator.
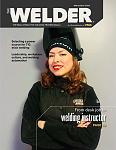
Easily access valuable industry resources now with full access to the digital edition of The Welder.
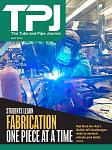
Easily access valuable industry resources now with full access to the digital edition of The Tube and Pipe Journal.
- Podcasting
- Podcast:
- The Fabricator Podcast
- Published:
- 04/30/2024
- Running Time:
- 53:00
Seth Feldman of Iowa-based Wertzbaugher Services joins The Fabricator Podcast to offer his take as a Gen Zer...
- Industry Events
Pipe and Tube Conference
- May 21 - 22, 2024
- Omaha, NE
World-Class Roll Forming Workshop
- June 5 - 6, 2024
- Louisville, KY
Advanced Laser Application Workshop
- June 25 - 27, 2024
- Novi, MI
Precision Press Brake Certificate Course
- July 31 - August 1, 2024
- Elgin,