Senior Editor
- FMA
- The Fabricator
- FABTECH
- Canadian Metalworking
Categories
- Additive Manufacturing
- Aluminum Welding
- Arc Welding
- Assembly and Joining
- Automation and Robotics
- Bending and Forming
- Consumables
- Cutting and Weld Prep
- Electric Vehicles
- En Español
- Finishing
- Hydroforming
- Laser Cutting
- Laser Welding
- Machining
- Manufacturing Software
- Materials Handling
- Metals/Materials
- Oxyfuel Cutting
- Plasma Cutting
- Power Tools
- Punching and Other Holemaking
- Roll Forming
- Safety
- Sawing
- Shearing
- Shop Management
- Testing and Measuring
- Tube and Pipe Fabrication
- Tube and Pipe Production
- Waterjet Cutting
Industry Directory
Webcasts
Podcasts
FAB 40
Advertise
Subscribe
Account Login
Search
Building success with the staggered truss
Structural fabricators take on a growing architectural market
- By Tim Heston
- June 17, 2008
- Article
- Shop Management
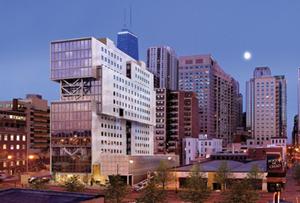
Click on image to view largerStaybridge Suites in downtown Chicago, slated for completion later this year, has a staggered-truss design that eliminates the need for interior columns. Digital rendering courtesy of Valerio Dewalt Train, Architect, Chicago.
These days Tabitha Stine could call herself a veteran road warrior. The director of technical marketing at the American Institute of Steel Construction, which works on building projects with the Steel Solutions Center in Chicago, has chalked up a lot of miles driving from site to site, promoting steel as a material of choice for commercial and industrial construction.
Today she's dealing with more than just the regular lineup of structural steel projects. She's also consulting with architects, engineers, structural fabricators, and erectors about a kind of steel construction that for the past few years has experienced a quiet resurgence in commercial real estate: the staggered-truss system.
Staggered-truss Basics
Developed during the 1960s by MIT graduate students, the staggered-truss system avoids the use of interior columns to transfer loads to the foundation; instead, trusses themselves carry the brunt of the load transfers. The system consists of story-high trusses that span the width of the structure and are staggered every other column line (seeFigures 1 and 2). Lateral loads are transferred from trusses on one floor to the plank, then to the truss below over on the next column line, then to the plank, essentially zigzagging their way to ground level. For structures up to 25 to 30 stories, these staggered trusses generally take both the lateral and vertical loads. Structures above this threshold usually require the building to have exterior moment frames, braced frames at interior stair towers or elevator cores, shear walls, or other elements to take the lateral loads.
The design gives architects and owners flexibility. A room of offices could be transformed into a large conference space with little difficulty; no interior support columns get in the way. The method also speeds construction because there are fewer pieces to pick and place, and because the structure relies primarily on steel and precast material. As long as on-site workers can handle the weather conditions safely, erection can continue—no concrete pouring to worry about. The plank typically is grouted at the seams, and a small leveling compound may be used, but no structural topping is required.
From the structural fabricator's standpoint, staggered-truss work doesn't differ too greatly from other truss work, except it brings more repetition and a greater volume of trusses. Certain trusses may mirror others, and truss design may alter slightly from floor to floor, but those changes don't require anything drastic. Usually it involves building one jig, after which fabrication can commence uninterrupted, building the same truss over and over.
"All the trusses are the same," Stine explained. "This means fabricators can start shipping pieces to the job site without a lot of extra coordination that normally accompanies a job with the complexities of construction sequencing."
It transfers more fabrication to the shop floor, less on the job site. In turn, it greatly streamlines erection, because it involves picking and placing fewer pieces. If a job has a sufficient footprint (and most greenfield sites do), a fabricator would use the laydown yard to place pieces consisting of a truss connected to two-story exterior columns; the erector would lift both the truss and columns at once. The fewer picks a crane can safely make, the better.
"We have some 12-story jobs out west [in which] all steel and planks were up in 19 days," Stine said.
According to sources, staggered-truss erection does take careful planning and close communication among the general contractor, fabricator, erector, precast concrete plank supplier, and others. Although the building exhibits solid support when finished, additional supports must be in place to keep the structure stable during construction.
More than anything, steel staggered trusses have potential to take various hotel, condo, and office-building projects away from other construction materials, like concrete, and that's certainly good news for structural steel fabricators everywhere.
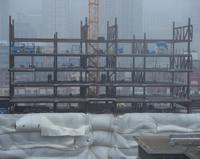
Figure 1Click image to view larger A current staggered-truss project, Staybridge Suites in downtown Chicago, shows how trusses stagger every other floor, between column lines. Photo courtesy of K&K Iron Works, McCook, Ill.
Pushing the Limits of the Staggered Truss
Scott Robbins keeps busy these days. Among other projects, he's been overseeing the fabrication and erection of the Staybridge Suites Chicago. By any measure, this is not your standard staggered-truss job. Most staggered-truss buildings are simple rectangles, but not the Staybridge (seelead image).
Robbins, project manager at K&K Iron Works, McCook, Ill., had the challenge of working on a building that pushes staggered trusses' flexibility, in a location without room to lay down materials. Like with all staggered trusses, fabrication remained relatively straightforward. K&K set up the initial jigs, then fabricated trusses to the design, cutting the 8-inch-square I beam with band saws. Top and bottom chords are preassembled, gussets prewelded, then the web members are placed in and welded (see Figures 3 and 4). It's more labor-intensive than mechanized beam-and-column work, but it requires much less on-site welding and assembly than alternative methods. In the structural world, more in-shop fabrication is a good thing. It never rains on the fab shop floor.
The Staybridge Suites is what Stine calls a "signature" staggered-truss building, one that shows how flexible the method has become, with a block of middle floors cantilevering out over the street. "This is the farthest it's ever been pushed," she said.
But architects and engineers have found a way to make this cantilevered structural challenge a success, transferring the load in the cantilevered sections through trusses and floor planks, and, ultimately, to the foundation below. The key is the way the trusses handle those loads: from top chord, through diagonal web members, to the plank, and on to the truss below.
In place, the truss's top-chord beams experience the most loads, so the engineer, fabricator, erector, and outside inspectors worked together to prevent web crippling within the trusses themselves. "For this job, the connections got heavy," Robbins said, adding that the erection team installed ¾-in. gusset plates to ensure sufficient support. Erectors placed studs on the inside of the flange, filled the void with grout, then set the plank on top.
By staggered-truss standards, the Staybridge had an extensive timeline. The project, which began in November, was at this writing scheduled to be complete later this year. Typical of urban erection, trucks deliver those trusses just-in-time, pulling up to the site on a lane closed off to general traffic. The fabricator uses five trucks in all; some carry left-side trusses, others carry ones for the right side, and the remaining haul columns and in-fill pieces.
The cranes pick the columns and trusses individually, directly from the trucks (see Figures 5 and 6). Because of the job's extremely limited urban footprint, the crane has to lift and place the perimeter columns and trusses separately, with the truss being carefully slid into place between a pair of two-story columns. Also, ensuring adequate support of the cantilevered floors takes a great deal of planning.
The winter weather didn't cooperate either. "We had a lot more snow and ice this year than we've had in a long time," Stine said, "but the job proceeded. We weren't limited by pouring concrete—even on the planks. There is no structural topping on the planks. They're high-end, what we refer to as 'carpet-ready.'" Such carpet-ready plank has been critical to the success of staggered-truss jobs in recent years, she added. Topping plank can produce heavier foundation loads, an increased floor-to-floor height, and more on-site work.
Still, according to sources, if it weren't for the staggered-truss design, the project would be slated for completion at a much later date. For the most part, erection continued through a seriously cold, snowy winter.
A Competitive Advantage
Sid Blaauw, sales manager for Steel Fabricators LLC, Fort Lauderdale, Fla., toured the Staybridge site one February morning during an AISC event promoting the steel building methodology. Work stoppages from cold aren't a concern for the South Florida fabricator, of course, but increasing market share is.
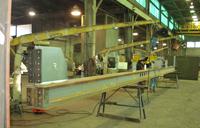
Figure 3Click image to view largerWelders at K&K Iron Works fabricate a truss chord for the Staybridge Suites project. Photo courtesy of K&K Iron Works, McCook, Ill.
Blaauw said the company hasn't landed a staggered-truss job yet, but at this writing Steel Fabricators had several possible jobs out for bid. In the long run, he said, the company hopes staggered truss will give his firm a competitive advantage. Steel Fabricators' principal competition isn't other steel fabricators; it is concrete, something that has remained a building material of choice for Florida contractors. Steel Fabricators hopes to change that. The bottom line, "Steel is less expensive and less labor-intensive," Blaauw said.
On the surface, structural steel may not seem that much of a bargain compared to its concrete counterpart. However, Blaauw said, the staggered-truss framing system is actually lighter per square foot than a freestanding steel frame, and both systems are considerably lighter than a concrete structure.
Overall, Blaauw said, he sees staggered truss's speedy erection as the method's biggest selling point and greatest money-saver. The faster a building goes up, the sooner the owner can start renting space and generating revenue.
More Trusses, More Jobs
Littell Steel has built a business on trusses, and, said Sales Manager Robert Thaw, the proliferation of staggered truss may mean more work for the company's niche.
Unlike many structural steel fabricators around the Pittsburgh metro area, the New Brighton, Pa.-based company doesn't have automated beam lines, so they can't churn out high-volume beam-and-column work. What they can do, though, is deliver complex trusses on demand.
"There's a certain skill that comes with trusses that makes it different from standard beam-and-column work," he said. "A beam that is born in the morning is a fabricated piece by that afternoon." Large, specialty trusses may take days to fabricate, and they require immense floor space. A structural fabricator with highly mechanized equipment might need only about 80,000 square feet of floor space. Littell, a 50-employee shop, has 150,000.
Tackling staggered-truss work is a natural extension of the business, Thaw said, and it has distinct advantages. Staggered-truss fabrication is straightforward, with all trusses either being identical or of very similar sizes. This also simplifies delivery requirements. With only a few different "parts," so to speak, delivery is easy to coordinate. The shop also finishes more fabrication on the floor, so the crane picks fewer pieces on-site.
This doesn't mean snags never happen. Thaw conceded that because steel erection happens fast, if any one party drops the ball, problems can snowball. "The rude awakening about staggered truss is the erection," he said.
For instance, Littell recently completed work near downtown Pittsburgh on the Hampton Inn—a standard, rectangle staggered-truss building. The entire job required about 40 trusses, all in the 70-foot range. That was simple enough for Littell's fab shop, but at the job site supervisors found an error with delivered planks.
"The design called for a welded plate at each end of the planks" to provide additional support during erection, Thaw explained. "The first three levels of plank came with only one weld plate on each side. So as we were at the line of scrimmage, as we started to erect, we had to re-engineer how to stabilize the building as we were erecting it."
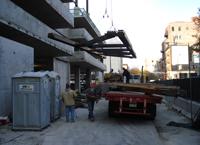
Figure 5Click image to view largerK&K Iron Works, which is the fabricator and erector on the Staybridge Suites project, picks a truss directly off the delivery truck. The urban site has no laydown yard for fabricated material. Photo courtesy of K&K Iron Works, McCook, Ill.
Ultimately, the erection team, subcontracted by Littell, had to integrate additional struts and cabling to keep the truss chords fixed so they could handle vertical loads during the erection process. The lesson? As Thaw put it, fabrication may be simplified, but the fast-moving erection process requires the involved parties to be on the same page at all times.
Thaw summed up staggered-truss jobs this way: "It may have 10 positives and six negatives; at the end of the day, you're still at plus four."
Steel Construction's Horizon
Stine said that AISC's Steel Solutions Center has seen more staggered-truss projects during the past two years than ever before. "In the last two years, we have looked at nearly 30 of them in the conceptual phase in all locations across the country." It's by no means the dominant method in steel construction, she added, but more are becoming aware of its benefits.
Considering a slowing economy and the rise of raw material prices, the staggered-truss system's popularity at first doesn't add up, until you consider what's being built: hotels. With the credit crunch, condo construction has slowed dramatically, but the falling dollar has made touring the U.S. a bargain, and hoteliers are cashing in, Stine explained.
For many of those jobs, staggered truss, offering owners and architects flexibility and design creativity, has stepped up to the plate—and more structural steel fabricators are ready to take a swing.
About the Author
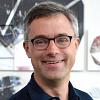
Tim Heston
2135 Point Blvd
Elgin, IL 60123
815-381-1314
Tim Heston, The Fabricator's senior editor, has covered the metal fabrication industry since 1998, starting his career at the American Welding Society's Welding Journal. Since then he has covered the full range of metal fabrication processes, from stamping, bending, and cutting to grinding and polishing. He joined The Fabricator's staff in October 2007.
subscribe now
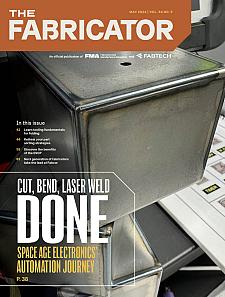
The Fabricator is North America's leading magazine for the metal forming and fabricating industry. The magazine delivers the news, technical articles, and case histories that enable fabricators to do their jobs more efficiently. The Fabricator has served the industry since 1970.
start your free subscription- Stay connected from anywhere
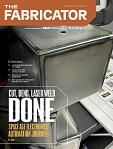
Easily access valuable industry resources now with full access to the digital edition of The Fabricator.
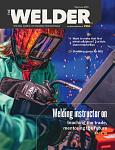
Easily access valuable industry resources now with full access to the digital edition of The Welder.
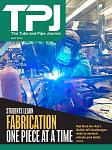
Easily access valuable industry resources now with full access to the digital edition of The Tube and Pipe Journal.
- Podcasting
- Podcast:
- The Fabricator Podcast
- Published:
- 05/07/2024
- Running Time:
- 67:38
Patrick Brunken, VP of Addison Machine Engineering, joins The Fabricator Podcast to talk about the tube and pipe...
- Trending Articles
White House considers China tariff increases on materials
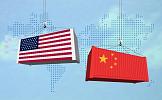
A deep dive into a bleeding-edge automation strategy in metal fabrication
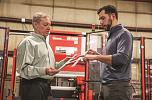
A visit to Automate 2024 reveals the future might be now
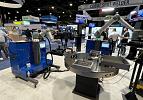
Majestic Steel Arkansas fully operational
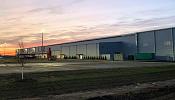
Rivian to expand Illinois facility to manufacture midsized SUV
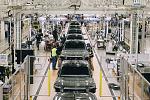
- Industry Events
Laser Welding Certificate Course
- May 7 - August 6, 2024
- Farmington Hills, IL
World-Class Roll Forming Workshop
- June 5 - 6, 2024
- Louisville, KY
Advanced Laser Application Workshop
- June 25 - 27, 2024
- Novi, MI
Precision Press Brake Certificate Course
- July 31 - August 1, 2024
- Elgin,