Senior Editor
- FMA
- The Fabricator
- FABTECH
- Canadian Metalworking
Categories
- Additive Manufacturing
- Aluminum Welding
- Arc Welding
- Assembly and Joining
- Automation and Robotics
- Bending and Forming
- Consumables
- Cutting and Weld Prep
- Electric Vehicles
- En Español
- Finishing
- Hydroforming
- Laser Cutting
- Laser Welding
- Machining
- Manufacturing Software
- Materials Handling
- Metals/Materials
- Oxyfuel Cutting
- Plasma Cutting
- Power Tools
- Punching and Other Holemaking
- Roll Forming
- Safety
- Sawing
- Shearing
- Shop Management
- Testing and Measuring
- Tube and Pipe Fabrication
- Tube and Pipe Production
- Waterjet Cutting
Industry Directory
Webcasts
Podcasts
FAB 40
Advertise
Subscribe
Account Login
Search
Custom fabrication: Right information, right technology, right time
How lean methods drive improvement at SAF
- By Tim Heston
- July 12, 2017
- Article
- Shop Management
Winston, Ga., residents know SAF Metal Fabrication as “that castle on the hill,” with its dramatic entryway and a façade of aluminum panels that arch upward. Just west of Atlanta, the “castle” exemplifies the core competency of an organization that has served commercial construction for decades (see Figure 1).
Architectural decorative metal for commercial construction remains the company’s focus, both in Winston and at SAF West, its sister fabrication plant in Redding, Calif. But the firm has expanded into other markets too. Drive a Tesla, and it’s likely the aluminum plates holding battery components came from SAF West, which (thanks in part to the Tesla job) has grown from 40 workers four years ago to 100 today. SAF employs a similar number in Winston.
SAF Metal Fabrication is one division of a larger organization, Southern Aluminum Finishing, a distributor of aluminum extrusions, sheets, and coil; an architectural metal fabricator specializing in aluminum and stainless steel; and a metal finisher, all rolled into one. Besides its Winston and Redding plants, SAF has distribution and anodizing in an Atlanta location and coil anodizing, slitting, and coating in Nashville. And it offers toll painting and anodizing (meaning the customer owns the material). At this writing, the company was planning to open an additional distribution and light fabrication facility in Indianapolis by early July.
“Manufacturing is really the IT business.”
So said SAF’s co-CEO Jim McClatchey during a tour earlier this year organized by the Georgia Manufacturing Alliance (www.georgiamanufacturingalliance.com). McClatchey was instrumental in developing proprietary business software in the 1980s that fit SAF’s unique business. And just recently the company launched the latest generation of that software.
His comment could be more broadly interpreted, though, not just for SAF but for any high-product-mix, quick-response operation. Information includes the constantly changing job requirements and delivery schedules; technology includes not only software but also machines and processing systems.
Everyone needs the right information at the right time to get the job done with the right technology. In this sense, SAF is where information and technology meet.
Quick Response for Decorative Metal
Walk the shop floor in Winston and you don’t see automated material handling towers by the turret punch presses. You see some new machine alongside some refurbished and retrofitted equipment. But you also see a spotless floor and signs showing where jobs are and where they’re going. You see standard work practices documented in “The Red Book,” and each department has one. You won’t see stacks of work-in-process.
The nature of SAF’s work demands quick response. Its decorative metal components are the last to arrive on the construction job site, and schedules change and remain fluid until the very end. If a structural fabricator or a mechanical contractor is late, SAF must adjust to suit.
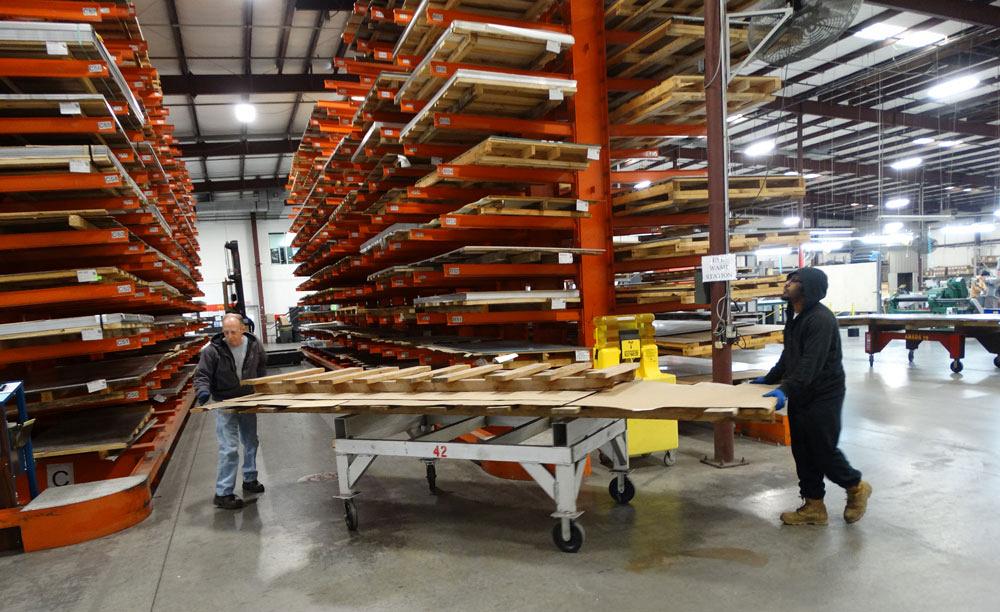
Figure 2
Workers transport raw stock on a wheeled cart. Although the plant has two fork trucks, the operation minimizes their use. Most jobs are simply wheeled between workstations.
The pace of projects also varies considerably. Some take a matter of weeks, others take years. During the tour, one component being gas tungsten arc welded, a decorative corner destined for a hotel in New Jersey, was part of a project that was two years in the making.
Considering this, you’d expect to see piles of WIP on the floor, ready to be finished to spec and shipped on demand. But you don’t see much WIP at all. Instead you see a lot of raw stock, mostly aluminum and stainless with some copper here and there, all different sizes and thicknesses, mostly between 0.040 and 0.125 in. (see Figure 2).
That’s expensive raw stock, for sure, but necessary to ensure everyone can react quickly to customer demands. But it’s less expensive than WIP, which is highly likely to become obsolete, considering how fluid construction projects are. Projects aren’t released to the floor until the building is up and dimensions are finalized. Then, it’s off to the races.
SAF’s sheet inventory in Winston includes a fair amount of 5005 anodizing-quality aluminum. “Anodizing is like staining wood,” said SAF Metal Fabrication Branch Manager Frank Buchholz, adding that anodizing one 5005 sheet from a different batch can result in an ever-so-slight variation in color—not a good thing for any façade. “We always try to anodize the same metal out of the same lot.”
Chrome conversion coating takes place on the other side of the plant (see Figure 3), as do painting and powder coating, another area where SAF carries a fair amount of inventory. “You would not believe how many colors there are in this world,” Buchholz said. “We have well over 4,000 active colors in the system. We have more than 200 different whites alone.”
All those variants require accurate mixing and a steady supply of fresh paint. Behind the facility are drums of paint from previous jobs that the company holds, just in case a need for that paint comes up again. By those drums are check lists that show when the paint needs to be discarded before it goes bad.
An upgraded IT system has helped SAF improve its inventory controls on wet paint. It now, for instance, helps track not only when the leftover paint goes bad, but also whether that paint color can be mixed with others in inventory to create a new color for current or future jobs. This saves paint (which can cost upwards of several hundred dollars a gallon) and minimizes the amount to dispose of safely, itself a costly and time-consuming process.
Shearing, Bumping, Welding, Grinding
In the cutting department, with its punch press and shears (see Figure 4), operators use carts to transport sheets at the right height, from raw stock to the cutting station, no fork truck required.
The shears epitomize architectural metal fabrication, cutting large, thin stock with straight edges. Even in these days of almost ubiquitous laser cutting among custom fab shops, a shear—set at the right rake angle and with a well-maintained, sharpened blade—still can cut a long straight edge faster than just about anything else. (Though sources at SAF concede that fiber lasers are giving the traditional shear a run for its money.)
Regardless, cutting at SAF isn’t the constraint, not by a long shot. Like in any job shop environment, the constraint moves depending on the job routing, but it’s rarely if ever the cutting operation. In fact, the day of the Georgia Manufacturing Alliance tour, the constraint likely was bending.
On that day, bending operators had their templates out, tools loaded—complete with solid urethane dies, tape, and a wide-radius punch—to form a radius wide enough to require bumping. The radius was at the very edge of the thin sheet, so forming them on the adjacent rolls (which requires prebends that form narrow flat sections near the sheet edge) just wasn’t an option. So operators spent time ensuring bend lines were close enough together to provide a seamless curve without any noticeable marks from the bend lines. To form just 16 panels takes more than a shift and a half (see Figure 5).
“That’s an aluminum column cover,” Buchholz said. “It costs almost a thousand dollars by the time we’re finished manufacturing it,” hence the need for careful, scratch-free handling and that urethane tooling.
Why not automate this? Couldn’t a panel bender or folding machine bump up this edge radius in short order? According to Buchholz, the problem for automation lies with the product mix. Press brake operators may have only one bumping job a month; sometimes it’s 16 pieces, sometimes it’s just one or two. And not all large-radius forming would fit in automated equipment, considering part geometry limitations in automated equipment (like the throat depth limitation in a panel bender). The same logic holds true for a custom brake tool. The radii operators work with are just too various.
Still, the operation runs smoothly, and much of it can be attributed to tools in the lean toolbox, including 5S and documented standard work.
“I managed the [Winston] facility for 10 years,” said co-CEO Penn McClatchey, “and I can think of two times when we hired somebody who was actually a fully trained and experienced press brake operator or welder. They usually don’t exist. So we realized we had to do our own do-it-yourself workforce development.”
This includes training regiments for new hires, and an important part of that is “The Red Book” in every department that details standard practices that are plainly documented, not locked away in tribal knowledge. Tool changeovers don’t take long thanks to clear shadow boards and a wheeled tool rack that holds segmented punches and dies inside a stainless steel enclosure (see Figure 6). Brake operators call it “the coffin.”
Measurement tools, including tape measures, squares, and radius gauges, are close at hand on the adjacent shadow board, clearly marked and plainly obvious when misplaced, so they’re not misplaced for long. If, say, an impact wrench is missing from the shadow board and no one is tightening a die on a brake, something’s amiss.
The company has retrofitted its brakes with modern controls, even a 20-ft. mechanical press brake from the 1960s. For a time that machine sat dormant, locked out and tagged out, with a big sign on it that read “Do not use.” The machine needed to be overhauled or dispensed with, but certainly not used to make parts, considering its condition.
SAF takes safety seriously. Every hydraulic press brake at SAF has side guards and laser-based systems that shoot infrared beams to detect obstructions just below the punch tip.
But the company needed greater throughput in bending, and so it decided to restore and retrofit the old mechanical system with a new control and, most important, modern safeguarding, including hard side guarding and, in front, a light curtain a good distance from the pinch point between the punch and die. (The flywheel-driven ram on mechanical brakes has long stopping distances.) The distance doesn’t present issues at SAF, though, which produces a lot of large workpieces.
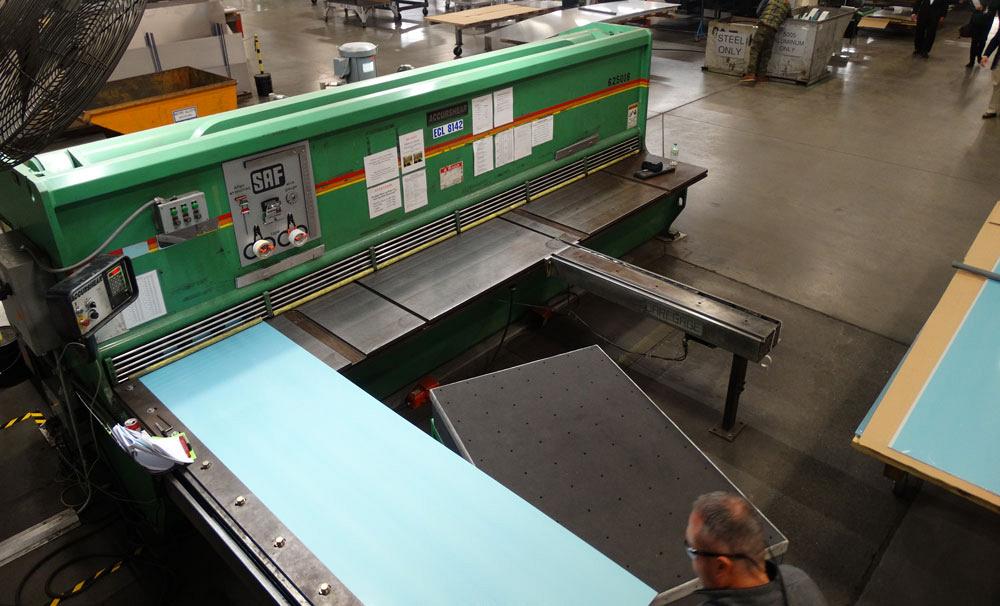
Figure 4
A shearing station is adjacent to the turret punch. Work flows in a circle (to the right in this image) and ends up in the final assembly and packaging area.
“We have daily maintenance check lists and a daily check list for operators,” Buchholz said. “And we perform audits, from a quality perspective and a systems perspective.” The systems perspective includes how work flows and, of course, safety.
“We give every employee his or her own set of tools,” Buchholz said. “That way, we stopped all the searching. They have what they need.”
From bending the workpieces go on to welding, grinding, and polishing. Buchholz paused and pointed to the floor in the grinding area. “Notice how this area looks so clean?”
The floors shined and the air was clear, though workers wielding polishing wheels still wore N95-compliant masks. The pneumatic hand tools they used had vacuum attachments that drew in particulate, sending it to a vat of water to neutralize it—no chance of particulate getting caught in a ventilation system and creating a potentially combustible situation (see Figure 7).
The safety focus continues in the paint department. Painters wear self-contained breathing systems to prevent chrome exposure, and everyone who applies paint and powder undergoes a yearly test.
“We offer the [chrome exposure] test even if they don’t work at the company anymore,” Buchholz said. “We may not be able to get them in here for the test, but we at least have to let them know that we need to run the test. We want to make sure people are protected.”
Adjacent to the painting are baths used for chrome conversion coating, a process in which part surfaces are microetched and then dipped in a bath for coating. “The coating process converts the material’s surface through a chemical process,” Buchholz said. “The only way to get that coating off is to actually remove metal or by chemical stripping. To ensure that the coating complies with the [American Architectural Manufacturers Association] 2605 standard, we use an XRF gun to measure the coating weight.”
Training Fabricators, Not Just Assemblers
Perhaps nowhere are lean practices more important than the final assembly and packaging areas. Workers create assembly cells for the work at hand—be it panels, column covers, or anything else—moving tools and carts as necessary multiple times a day.
Wrapping in the packaging area is an especially critical process. “We have to avoid scratching,” Buchholz said. “If it gets scratched, we need to make a brand-new one, and that’s an expensive mistake. And if it gets scratched or damaged during shipping, we need to remake it. It goes to the top of the schedule as a rush job.”
He then pointed to a column cover on display, a column that got scratched in-house. “That’s an expensive mistake, and it makes us cringe. But we put those on display to remind us.”
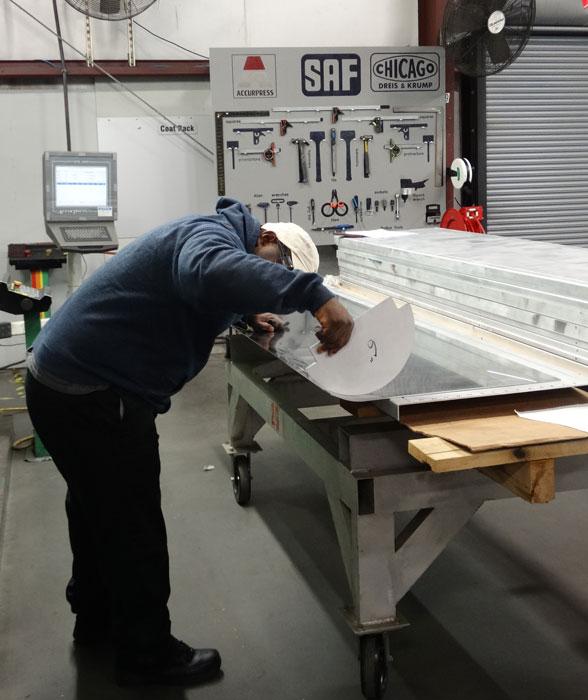
Figure 5
Standing in front of a shadow board in the brake department, a worker checks a bumped radius with a template.
Workers don’t take assembly and packaging for granted, in part because they work in other areas of the plant. “We don’t train assemblers,” Buchholz said. “We train metal fabricators. They learn how to bend, punch, shear, and assemble.” They know the entire process chain and, hence, know how critical careful, scratch-free handling really is.
Directly adjacent to assembly and packaging, and directly behind the turret punch, is a fabrication cell with a brake fitted with punch tools, a manual leaf brake, a small roll, and a drill press, all fitted with hard guarding (like a chip guard on the drill press) and updated safety controls.
The location of this cell ties the plant layout together. Look from overhead, and you’d see how parts flow in a circle around the central inventory racks. Raw stock comes off the racks and is fed into the turret punch and shears at the 12 o’clock position. Some blanks then go on to the specialized fabrication cell, while others go on to forming at the brakes at 10 o’clock, then on to welding and polishing at 8 o’clock, painting and coating at 7 o’clock, then final assembly and packaging at 3 o’clock and 2 o’clock (a large area to account for large projects). This simple, open layout allows everyone to see where products are coming from and where they’re going.
Right Safety Information, Right Now
The last stop on Buchholz’s tour was by a board with posted cards, an integral part of SAF’s behavioral-based safety systems. Workers watch each other’s behavior, then post each other’s observations: green cards show good behaviors worth emulating; yellow cards represent potentially unsafe behaviors, like someone driving too fast in the parking lot (see Figure 8).
The SAF safety committee now works less reactively and focuses more on prevention. Prevously, people would meet, discuss unsafe practices, then spread the word after those unsafe acts were observed. Today everyone observes everyone else, communicates, and documents problems as they occur, or at least soon after. They then work on ways to prevent those problems from occurring in the future.
Buchholz conceded that this requires a progressive work culture. People aren’t reprimanded for unsafe behavior—otherwise, no one would report the problems they see—but people are recognized for making good observations. “This is all built into everyone’s performance review,” Buchholz said.
IT in Action
Due to the nature of construction, SAF simply can’t produce any parts ahead of schedule. It’s about having the right technology to maintain flow and throughput, and the right information at the right time—about the job, work procedures, and, most important, safe work practices.
The operation, as with any modern manufacturer, boils down to the marriage of information and technology. Walk SAF’s shop floor, and you see the IT business in action.
SAF Metal Fabrication, 770-942-1207, www.saf.com
About the Author
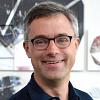
Tim Heston
2135 Point Blvd
Elgin, IL 60123
815-381-1314
Tim Heston, The Fabricator's senior editor, has covered the metal fabrication industry since 1998, starting his career at the American Welding Society's Welding Journal. Since then he has covered the full range of metal fabrication processes, from stamping, bending, and cutting to grinding and polishing. He joined The Fabricator's staff in October 2007.
subscribe now
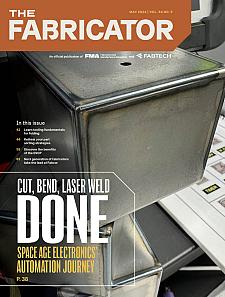
The Fabricator is North America's leading magazine for the metal forming and fabricating industry. The magazine delivers the news, technical articles, and case histories that enable fabricators to do their jobs more efficiently. The Fabricator has served the industry since 1970.
start your free subscription- Stay connected from anywhere
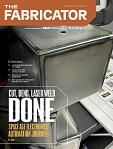
Easily access valuable industry resources now with full access to the digital edition of The Fabricator.
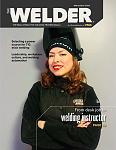
Easily access valuable industry resources now with full access to the digital edition of The Welder.
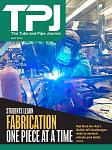
Easily access valuable industry resources now with full access to the digital edition of The Tube and Pipe Journal.
- Podcasting
- Podcast:
- The Fabricator Podcast
- Published:
- 04/30/2024
- Running Time:
- 53:00
Seth Feldman of Iowa-based Wertzbaugher Services joins The Fabricator Podcast to offer his take as a Gen Zer...
- Industry Events
16th Annual Safety Conference
- April 30 - May 1, 2024
- Elgin,
Pipe and Tube Conference
- May 21 - 22, 2024
- Omaha, NE
World-Class Roll Forming Workshop
- June 5 - 6, 2024
- Louisville, KY
Advanced Laser Application Workshop
- June 25 - 27, 2024
- Novi, MI