Senior Editor
- FMA
- The Fabricator
- FABTECH
- Canadian Metalworking
Categories
- Additive Manufacturing
- Aluminum Welding
- Arc Welding
- Assembly and Joining
- Automation and Robotics
- Bending and Forming
- Consumables
- Cutting and Weld Prep
- Electric Vehicles
- En Español
- Finishing
- Hydroforming
- Laser Cutting
- Laser Welding
- Machining
- Manufacturing Software
- Materials Handling
- Metals/Materials
- Oxyfuel Cutting
- Plasma Cutting
- Power Tools
- Punching and Other Holemaking
- Roll Forming
- Safety
- Sawing
- Shearing
- Shop Management
- Testing and Measuring
- Tube and Pipe Fabrication
- Tube and Pipe Production
- Waterjet Cutting
Industry Directory
Webcasts
Podcasts
FAB 40
Advertise
Subscribe
Account Login
Search
EuroBLECH 2018: Ready for the new digital reality?
The future of fabrication is here
- By Tim Heston
- December 5, 2018
- Article
- Shop Management
Carel van Sorgen sat comfortably in his well-appointed EuroBLECH booth (or “stand,” as the Europeans call it), in Hanover, Germany, home to one of the largest tradeshow facilities in the world. The place makes Chicago’s McCormick Place look cozy.
Van Sorgen has been to more EuroBLECH shows than he can count. But one thing he could count is the number of cut and formed metal parts his company, 247 Tailor Steel, planned to ship that day.
“At this point we have about 150 tons of steel coming in every day, and the next day it’s all gone. Altogether, we have more than 4,500 customers.”
He knows exactly how many orders ship, when, as well as how much money the company made. How does van Sorgen know this? It’s all in the company’s proprietary software, accessible with a few swipes or mouse clicks.
The Dutch custom fabricator is a harbinger for the fabrication industry at large, very much like the EuroBLECH show itself. Talk of so-called “digitalization” and Industry 4.0 dominated the exhibition halls between Oct. 23 and 26, when the trade fair grounds transformed into a showcase of modern metal fabrication—what it is and, especially, what people expect it to become.
A Global Show
The 25th International Sheet Metal Working Technology Exhibition, EuroBLECH hosted more than 56,000 visitors who walked more than 960,000 square feet of exhibit space to see more than 1,500 companies from 40 countries. The biennial event has evolved to become a global show, with 37 percent of visitors coming from outside Germany.
EuroBLECH always has been the industry’s technological playground, a snapshot of metal fabrication’s possible future. This year’s show hinted at a fabricator that could be summed up in a phrase: Fewer, more powerful, flexible, self-learning machines producing more than ever, all in a connected environment.
A Different Power Race
When it comes to lasers, the industry is on the kilowatt race again, but compared to the CO2 laser’s prime growth years in the 1990s and 2000s, the fiber laser’s power race is a bit more nuanced.
Eagle, a Polish company represented in the U.S. by Maple Valley, Wash.-based Fairmont Machinery, introduced a 15-kW fiber laser, complete with a sealed cutting head with no moving parts adjacent to the optics; a vibration-dampening machine design; high-speed linear drives in X, Y, and Z; and a high-speed pallet changer.
Eagle wasn’t alone, of course. Bystronic, LVD, and others had their high-powered lasers on display, some touting high acceleration and precise control through intricate contours. What’s the use-case for these machines? They can pierce and cut very thick plate very quickly, of course. But they also can be true speed demons on thin plate and sheet metal.
Laser cutting isn’t just a power race anymore, though, with vendors touting how their machines can manipulate the beam itself for more effective and consistent cutting. Amada had its own 9-kW laser cutting system that makes changes to the beam parameters depending on the material being cut.
TRUMPF introduced what the company calls Active Speed Control. With a sensor that essentially “looks” straight through the nozzle into the cutting zone, the feature allows the laser to respond to material changes, including changes to the surface and thickness. When traveling over rusty surfaces, or if the sheet becomes thicker in places (common from stock that originated in a coil), the laser travel slows to accommodate.
Automated Tool Change Goes Mainstream
If a press brake operator had left the industry 20 years ago and then decided to return by dropping by the EuroBLECH show, he’d see an entirely different bending environment, one designed to handle the industry’s unprecedented level of cutting capacity.
While different press brake vendors have their unique approaches to it, automated tool change (ATC) is now everywhere. Judging by their presence at the show, it’s not too outlandish to imagine ATC brakes becoming more common than their manual cousins. And like a high-powered fiber laser producing more parts than several older CO2 systems, a modern ATC can produce the equivalent of two or three manual press brakes. They can minimize and sometimes outright eliminate setup between disparate bending jobs—a benefit that has been a true game changer at many fab shops.
Amada had its ATC brake on display, and LVD introduced a 4-meter ATC machine with a frame design that pivots the machine supports to the front, doubling the space for tooling behind the bed.
Technology on display hinted at how this concept could be taken even further, essentially by making robotics more flexible. For instance, SafanDarley introduced an automated press brake with a robot suspended from above. Should a job requiring manual intervention show up on the schedule, the robot can move to the side and be safely locked out to make room for the operator to bend parts manually.
Why does a fabricator bend a job manually? It comes back to setup. These days bending robots can be simulated offline, but the programs still take time to develop, and machine developers are aiming to reduce that time.
One effort is Bystronic’s robotic press brake, designed for high-product-mix production. The software develops the robot path, which is downloaded to the robotized brake, and the machine then bends the first part—slowly. The system tests the bend path and sequence, adapts, and makes necessary corrections. Then on the second part, the robot moves at full speed to perform the bend.
Of course, a press brake isn’t always the best bending solution. Schroder, represented in the U.S. by MetalForming Inc., introduced a folding machine that can manipulate the part in multiple directions and, most significantly, gauges parts not with backgauge fingers but with a unique camera system positioned near the tools.
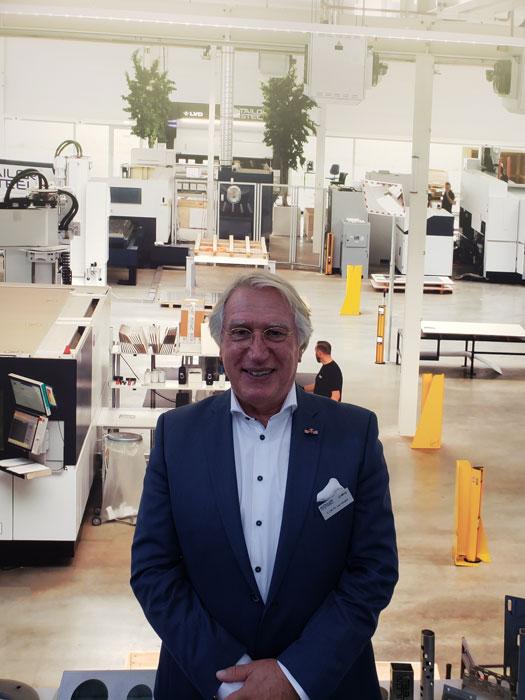
Carel van Sorgen, founder and president of 247 Tailor Steel—a custom fabricator based in the Netherlands—posed in his EuroBLECH booth in front of a photo of the company’s new plant in Oyten, Germany. Company sales grew more than 40 percent over the past year.
Prima Power showcased its robotized bending cell that alternates between a panel bender and press brake, along with its unique part removal technology on its laser cutting system. For certain parts nested in thin material, the gripper maintains contact with a part while the laser cuts the profile. Once the profile is complete, the device lifts and removes the part from the skeleton.
Salvagnini showcased its automated concept that also involved a press brake and a panel bender—this one fed not by a robot, but by an automated guided vehicle (AGV) that retrieved parts directly from a laser cutting system with automated part removal.
From Cut to Ship
Look down in the Salvagnini booth, and you’d see not a blank floor but a stripe where the AGV traveled, with the help of sensors to navigate a crowded show. Bystronic’s booth also had stripes on the floor to illustrate the company’s concept of a fully automated fab shop, with a separate table for small-hole tapping followed by cutting and automated part removal and sorting. Next came an AGV ride to automated bending and other downstream processes.
TRUMPF’s booth also took a holistic approach, showcasing technology that can track jobs through the factory, with markers on job packets communicating via an ultrawide-band frequency (to avoid interference). Some of those parts could be coming from a TRUMPF laser cutting center that replaces slats with a brush table and removes parts with a series of suction cups and pins—a machine that made its second EuroBLECH appearance.
Most of the major machine tool makers put their part-removal automation on display, with suction cups and magnetics grasping disparate parts out of the nest and stacking them neatly on pallets or bins. Part removal automation is one reason punch/laser combination systems have been getting increased attention, with their ability to remove both the largest pieces (via suction cups) and the smallest (sending them down a chute).
All this put the show’s emphasis clearly on part flow. It’s no longer just about how productive a particular machine is; it’s also about how quickly and (perhaps even more important) consistently parts flow. And after a blazingly fast cutting process, parts ideally shouldn’t be sitting in a nest, just waiting for someone to bring them to the next operation.
Everything Is Connected
Why would those parts be just sitting there, trapped in a nest? Lack of denesting resources is sometimes a culprit, but so too are setup problems downstream. Press brake operators just can’t make their way through all the work they have. This can be due to lack of capacity, where ATC and robotized brakes can help. But the problem also can be more basic, with setups simply being inconsistent thanks to poor work instructions and tool organization.
A tiny data metric (DM) mark (a QR code’s smaller cousin) on tools aims to solve this problem. Wila, for instance, showcased its punches and dies with DM codes that work in conjunction with the company’s Tool Identification and Position System (TIPS). Communicating via Bluetooth, the operator is notified immediately if the tools are installed in the wrong position or orientation.
Welding data is now also tracked and analyzed too, and various welding vendors, including Fronius and ESAB, exhibited platforms that can do just that and more. ESAB’s HKS subsidiary, which it acquired in May 2017, demonstrated its data analytics system that relates specific arc characteristics with specific weld defects and discontinuities, including porosity. The ideal result, of course, is to predict problems before they happen.
Such predictive maintenance was a common theme in the metal forming hall, where Schuler demonstrated its Smart Press Shop, in which sensors monitor acceleration, oscillation, and pressure, with optimized slide profiles.
Autonomous Fabrication
A frequent buzzword heard throughout EuroBLECH this year, “autonomous” is likely to become a well-known adjective in this business, be it autonomous cutting, autonomous bending, or anything else. Traditionally, automation has come with a sticking point: Machines will do only what you tell them to do. But autonomous processes are different. The machines learn, adapt, and, thanks to artificial intelligence (AI), get better over time.
AI is everywhere in the consumer electronics arena, and it’s likely to utterly change the fabrication business in the decades to come. It may sound like a pie-in-the-sky notion—until you realize that a lot of it is already real.
Consider again the experience at 247 Taylor Steel, the fast-growing Dutch custom fabricator that had a EuroBLECH booth large enough to be a major equipment vendor—yet it was selling its job shop services, not machinery. With plants in the Netherlands and Germany, by the end of this year it will have more than 35 flatbed lasers, each with load/unload automation, as well as almost 20 ATC press brakes.
AGVs retrieve material and bring it close to the machine, where it’s stacked in an automated load/unload system. At its new factory in Oyten, Germany, the company designed its own multilevel AGV that uses 3-D vision to retrieve raw stock from a multishelf rack. The company installed the rack primarily for space reasons; for optimal cash flow, 247 still keeps only a few days’ worth of raw stock inventory on-hand.
From the cutting machine, parts are sorted manually (though the company is working on its own streamlined part sorting solution), then flow on to bending. After that, jobs are scanned, loaded on a truck, and tracked as they’re sent to customers. As soon as the delivery person (“company ambassadors,” as 247 calls them) drops off an order, it’s scanned, and invoicing—all paperless—occurs automatically and immediately.
Just 48 hours before, the customer had uploaded drawings of its parts to 247’s proprietary quoting software, which produces a quote within minutes. The moment the customer clicks “accept” on the webpage, software automatically processes, schedules, and nests the order. In less than 48 hours, the order (most of which are very small batch, between one and a dozen parts) is offloaded from a truck into customers’ hands.
“Year over year from September, we’ve grown by 41.9 percent,” van Sorgen said. According to van Sorgen, the company soon won’t be far away from becoming a $100-million-euro enterprise.
Any manager might read that and think such rapid growth would be simply unmanageable. Thing is, at their EuroBLECH booth, neither van Sorgen nor his staff were checking the phones, making sure this job shipped or that invoice was paid. Even if he did call the front office, he wouldn’t have too many people to call. In 2017, when I visited the main 247 plant in Vasserveld, near the eastern border of the Netherlands (as part of a press tour hosted by LVD), the office employed just a handful of people. Software automates most of the office functions, from purchasing and invoicing to quoting and engineering. Not every facet of every function is automated. Still, sales, engineering, and others only step in when software can’t perform the task.
“I always say to people, ‘Don’t ever be afraid you’ll lose your job because we’re investing in technology,’” he said. “Technology is helping us as human beings, and we have to think about the future. We have to innovate, but we don’t innovate to replace people. Technology is a tool that helps us grow, to achieve greater [revenue] with the same number of people, not by working harder but by working smarter.”
That statement pretty much sums up the spirit of this year’s EuroBLECH. Indeed, fabricators like 247 Tailor Steel and others are proving that the technological buzzwords of the tradeshow—industrial internet of things, Industry 4.0, digitization—are becoming very real on the shop floor.
EuroBLECH, www.euroblech.com
About the Author
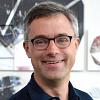
Tim Heston
2135 Point Blvd
Elgin, IL 60123
815-381-1314
Tim Heston, The Fabricator's senior editor, has covered the metal fabrication industry since 1998, starting his career at the American Welding Society's Welding Journal. Since then he has covered the full range of metal fabrication processes, from stamping, bending, and cutting to grinding and polishing. He joined The Fabricator's staff in October 2007.
subscribe now
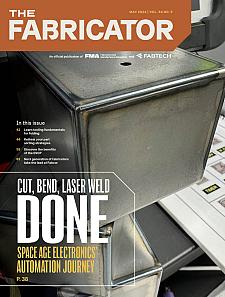
The Fabricator is North America's leading magazine for the metal forming and fabricating industry. The magazine delivers the news, technical articles, and case histories that enable fabricators to do their jobs more efficiently. The Fabricator has served the industry since 1970.
start your free subscription- Stay connected from anywhere
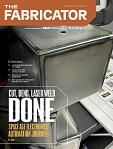
Easily access valuable industry resources now with full access to the digital edition of The Fabricator.
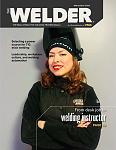
Easily access valuable industry resources now with full access to the digital edition of The Welder.
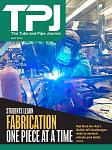
Easily access valuable industry resources now with full access to the digital edition of The Tube and Pipe Journal.
- Podcasting
- Podcast:
- The Fabricator Podcast
- Published:
- 04/16/2024
- Running Time:
- 63:29
In this episode of The Fabricator Podcast, Caleb Chamberlain, co-founder and CEO of OSH Cut, discusses his company’s...
- Trending Articles
Tips for creating sheet metal tubes with perforations
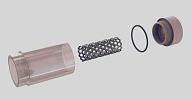
Supporting the metal fabricating industry through FMA
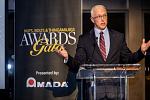
JM Steel triples capacity for solar energy projects at Pennsylvania facility
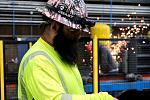
Are two heads better than one in fiber laser cutting?
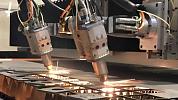
Fabricating favorite childhood memories
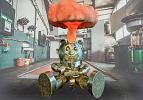
- Industry Events
16th Annual Safety Conference
- April 30 - May 1, 2024
- Elgin,
Pipe and Tube Conference
- May 21 - 22, 2024
- Omaha, NE
World-Class Roll Forming Workshop
- June 5 - 6, 2024
- Louisville, KY
Advanced Laser Application Workshop
- June 25 - 27, 2024
- Novi, MI