President
- FMA
- The Fabricator
- FABTECH
- Canadian Metalworking
Categories
- Additive Manufacturing
- Aluminum Welding
- Arc Welding
- Assembly and Joining
- Automation and Robotics
- Bending and Forming
- Consumables
- Cutting and Weld Prep
- Electric Vehicles
- En Español
- Finishing
- Hydroforming
- Laser Cutting
- Laser Welding
- Machining
- Manufacturing Software
- Materials Handling
- Metals/Materials
- Oxyfuel Cutting
- Plasma Cutting
- Power Tools
- Punching and Other Holemaking
- Roll Forming
- Safety
- Sawing
- Shearing
- Shop Management
- Testing and Measuring
- Tube and Pipe Fabrication
- Tube and Pipe Production
- Waterjet Cutting
Industry Directory
Webcasts
Podcasts
FAB 40
Advertise
Subscribe
Account Login
Search
Making the move to automated stretch wrapping
Answering certain questions can help you to determine if you need a new approach to packaging parts
- By Tom Brizek
- September 15, 2017
- Article
- Shop Management
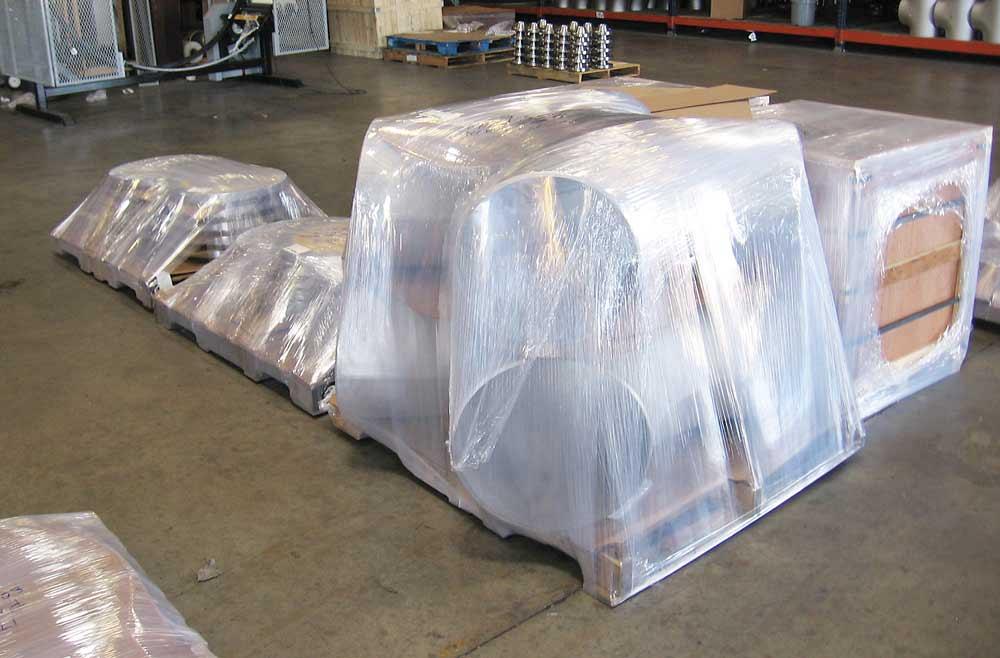
Figure 1
Automated stretch-wrapping machinery secures a load to the pallet. When manually stretch wrapping, employees get pretty good coverage around the load, but don’t typically secure the metal products to the pallet in a very complete manner.
Before manufacturing automated stretch-wrapping equipment, my company acted—and still does—as an East Coast distribution arm for a West Coast manufacturer of hollow metal doors and frames. We were struggling with some of the same packaging challenges that plague job shops and manufacturers today.
We had multiple personnel armed with rolls of stretch wrap running around pallets with products and getting dizzy. The wrapping jobs provided minimal support or product protection, and as a result, the company experienced increasing damage claims on products being shipped out on a daily basis.
That got me to thinking there had to be a better way. Coming to work one day, I noticed people baling hay and observed their orbital-style wrapping device bundling the hay. The hay being wrapped looked similar in size and shape to our loads, so I wondered if we could design something similar.
The company made four stretch wrappers that first year eight years ago. Today it makes about three per week.
Meanwhile, job shops and manufacturers still struggle with their shipping activities. Answering these questions can help these companies to find out if their packaging operations are ripe for a change, including a move to automated stretch wrapping.
Is more than one person involved in stretch wrapping of products? If so, how long does the operation take them?
It’s not unusual to see two or three people wrapping a pallet of metal products. They might each have a roll of stretch wrap, and they walk around in a circle as if they’re playing “Ring Around the Rosy.”
Depending on the size of the load, even more people might be involved. Consider one shop that had six people involved in shrink wrapping a large load. They laid the shrink wrap on the ground in a cross formation, and a lift truck placed the pallet and accompanying load in the middle of the cross. The employees then pulled up one side of the shrink wrap at a time and used an open flame to shrink the wrap around the product. The lift truck then picked up the pallet and backed up so a new cross of shrink wrap could be placed on the floor to initiate a new round of wrapping. The whole process took about 15 to 20 minutes for one load.
An automated stretch wrapper can wrap a load in about one minute and needs only one person to be involved. The lift truck driver positions the load into the ring of the stretch wrapper and initiates the wrapping sequence with the push of a button. Working around a horizontal axis, the automated wrapper stretches the film around the pallet and products. The wrapping cylinder, which carries a spool of stretch wrap on a moving dispenser, moves parallel to the forks of the lift truck. Stretch wrap is dispensed around and under the loaded pallet while the cylinder advances forward across the pallet.
The lift truck driver can slowly back up so that the entire length of the pallet is wrapped to satisfaction. To end the wrapping, the lift truck driver hits a button on the remote control, which is either corded or wireless, that initiates a sequence that cuts the shrink wrap and ends the wrapping process.
Once an automated stretch wrapper is in place, a metal fabricator can move labor to other more pertinent areas of the facility. Indirect labor costs once associated with packaging can be eliminated, and those resources can be applied to fabricating activities that customers are actually paying for.
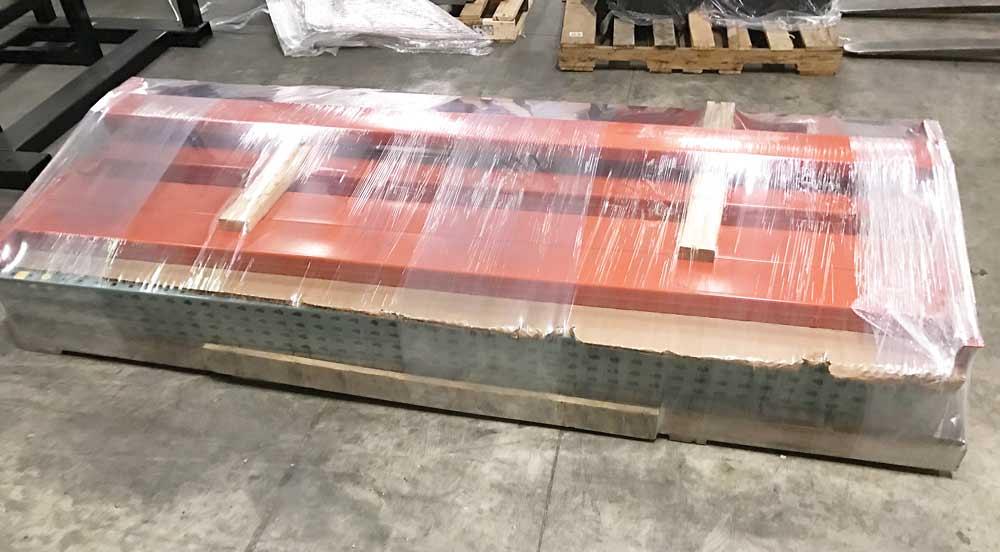
Figure 2
An automated stretch wrapper can accommodate a long pallet as long as there’s enough room both in front and behind the machinery. A lift truck driver can position the load within the wrapping area and slowly move backwards so that the entire pallet length is wrapped. When the end of the pallet is reached, the lift truck driver can shut off the machinery with a remote control.
Are products being damaged during delivery? Are customers complaining about it?
Because manual stretch wrapping in many cases is only barely connecting the load to the pallet, the metal products are not always secure. They can shift during transportation, and that can lead to damaged goods.
The same thing can happen to those metal fabricators that use metal banding. When you strap an irregular shape with metal banding, a simple shift in the load can result in the band loosening. At that point the band is useless, and the load is in jeopardy.
When a pallet with products is presented to the automated stretch wrapper, it is secured thoroughly because the wrapping is horizontally applied around the load and the pallet (see Figure 1). It’s not a single thick layer of stretch wrap connecting the payload to the pallet; it’s several layers. In fact, the stretch wrap conforms to the shape of the load and actually gets tighter as it goes down because it is being prestretched during application. The stretch-wrap material is always trying to contract, and the product is locked on.
How much space do we dedicate to manual stretch-wrap operations?
The staging of pallets on the floor waiting to be wrapped is a common sight in manufacturing facilities. In a fast-paced production environment, these pallets can add up, particularly if the wrapping takes about 15 minutes per pallet.
An automated stretch wrapper allows pallets to be wrapped within a minute and placed on a truck for delivery only minutes after that. Products are being moved through shipping at a pace that helps to prevent a huge buildup of pallets on the floor, freeing up space for something else.
Some fabricators keep the automated stretch wrappers in the area where pallets of products are racked. The lift truck can remove the pallet from the racking, drive to the nearby stretch-wrapping equipment, complete the wrapping process, and load it on the waiting truck at the nearby dock.
The equipment, which is about the same width of traditional racking systems, needs to be only about a foot away from the wall, so a lift truck can wrap a 4- by 4-foot pallet without interference.
Does our shipping department struggle with wrapping awkward or large loads?
Manual stretch wrapping of modest pallet loads takes time. Trying to do the same with awkward and large loads takes up even more time.
Automated stretch-wrapping equipment can be designed to accommodate these large sizes. Standard equipment, with a wrapping area of 100 in. ID, can handle loaded pallets as large as 5 by 5 ft. or 4 by 6 ft.
If that doesn’t work, custom machines can be fabricated, such as one with wrapping area of 154 in. ID. At that size, the equipment has a split-frame construction so that it can be delivered via the highway system and fit under overpasses. It also has to be assembled on-site, unlike standard equipment that can be delivered and running in a matter of minutes.
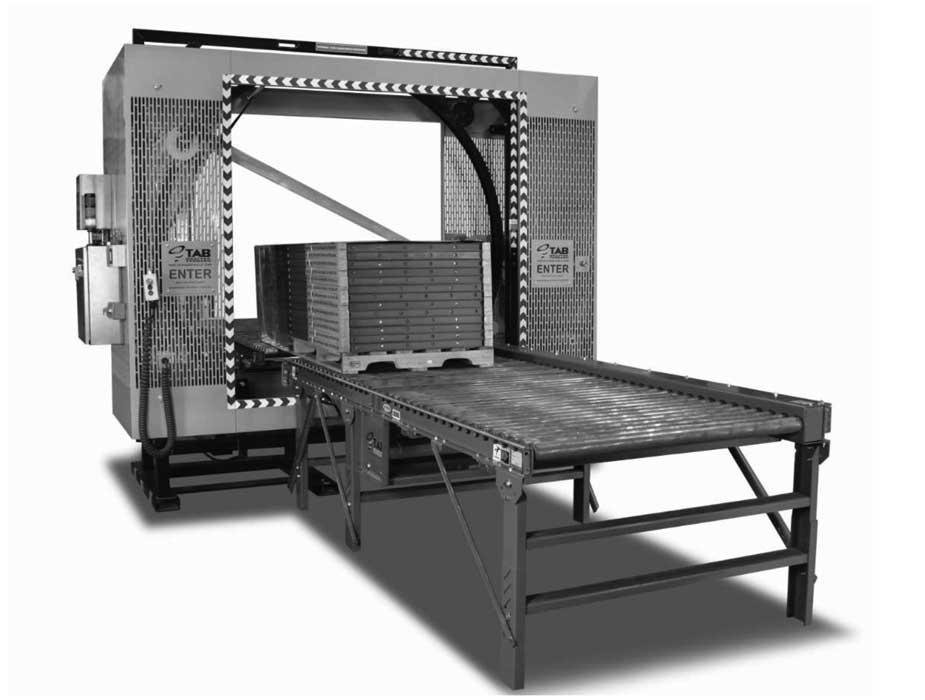
Figure 3
With the addition of automated material handling features such as conveyors and index tables, metal fabricators can automate packaging and reduce labor costs even more.
Long loads aren’t really a problem as long as the wrapping equipment is situated in a place that allows the entire load to traverse through the wrapping envelope (see Figure 2). Again, the lift truck can back up slowly and the wrapping will continue along the length of the pallet, no matter how long it is.
Do our pallets require total 360-degree coverage?
This can be addressed with automated material handling features (see Figure 3) attached to a couple of stretch wrappers. For example, a lift truck can deliver a pallet to the first wrapper, where it is wrapped in one direction and dispatched to an exit conveyor. From there the pallet goes to an indexing table where it spins and is sent its way to the second wrapping machine. Upon reaching the second unit, the pallet is wrapped in the other direction. Once completely enclosed in stretch wrap, the pallet is sent down another conveyor for final shipping.
This type of system, and others with automated material handling, can run entire shifts without human intervention. It’s just a matter of the pallet loads and volume lending themselves to such a system.
Metal fabricators don’t have to live with packaging inefficiencies. Automation can make the application of stretch wrapping quick and easy, and it provides complete coverage of the products on the pallet to create a sturdy and safe package.
About the Author
Tom Brizek
2525 N. 12th St.
Reading, PA 19605
610-921-0012
subscribe now
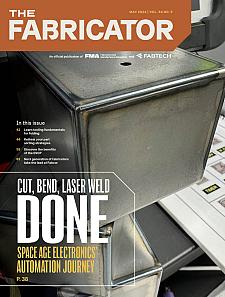
The Fabricator is North America's leading magazine for the metal forming and fabricating industry. The magazine delivers the news, technical articles, and case histories that enable fabricators to do their jobs more efficiently. The Fabricator has served the industry since 1970.
start your free subscription- Stay connected from anywhere
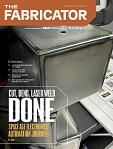
Easily access valuable industry resources now with full access to the digital edition of The Fabricator.
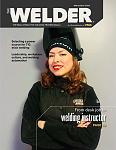
Easily access valuable industry resources now with full access to the digital edition of The Welder.
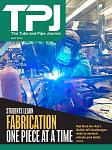
Easily access valuable industry resources now with full access to the digital edition of The Tube and Pipe Journal.
- Podcasting
- Podcast:
- The Fabricator Podcast
- Published:
- 04/30/2024
- Running Time:
- 53:00
Seth Feldman of Iowa-based Wertzbaugher Services joins The Fabricator Podcast to offer his take as a Gen Zer...
- Industry Events
16th Annual Safety Conference
- April 30 - May 1, 2024
- Elgin,
Pipe and Tube Conference
- May 21 - 22, 2024
- Omaha, NE
World-Class Roll Forming Workshop
- June 5 - 6, 2024
- Louisville, KY
Advanced Laser Application Workshop
- June 25 - 27, 2024
- Novi, MI