Senior Editor
- FMA
- The Fabricator
- FABTECH
- Canadian Metalworking
Categories
- Additive Manufacturing
- Aluminum Welding
- Arc Welding
- Assembly and Joining
- Automation and Robotics
- Bending and Forming
- Consumables
- Cutting and Weld Prep
- Electric Vehicles
- En Español
- Finishing
- Hydroforming
- Laser Cutting
- Laser Welding
- Machining
- Manufacturing Software
- Materials Handling
- Metals/Materials
- Oxyfuel Cutting
- Plasma Cutting
- Power Tools
- Punching and Other Holemaking
- Roll Forming
- Safety
- Sawing
- Shearing
- Shop Management
- Testing and Measuring
- Tube and Pipe Fabrication
- Tube and Pipe Production
- Waterjet Cutting
Industry Directory
Webcasts
Podcasts
FAB 40
Advertise
Subscribe
Account Login
Search
Metal fabricator broadens its customer base—and thrives
After tragedy, Pennsylvania metal fabricator moves forward with new facility, organization restructure, nonprofit
- By Tim Heston
- July 10, 2019
- Article
- Shop Management
When Chris Miller answered his cellphone on a job site in 2006, everything changed. The project manager at Herr & Sacco (H&S), a southeast Pennsylvania industrial fabricator and mechanical contractor, received news that his father, the company president, was ill. The next day his father was unresponsive. He died eight days later.
It happened so quickly. The two hadn’t spoken much about succession in general, much less about the worst-case scenario that had come to pass. After accepting initial sympathies and condolences, Miller began hearing chatter among the fabrication community. H&S was shutting its doors. Some thought it already had. The chatter was baseless but understandable. Unexpected deaths of strong leaders unravel small businesses all the time, and it wasn’t outlandish to think that H&S would do the same.
“When something traumatic happens, like what happened to us, it’s important to convey some level of security and comfort,” Miller said. “We can’t sit still and feel sorry for ourselves. We need to look forward, keep going, and create a future for ourselves.”
They did. The company moved out of its cramped facility in Landisville, Pa., to a greenfield plant outside Manheim. It made significant investments to streamline material movement. It expanded into laser cutting, both of sheet and tube, and purchased a nearby electrical contractor. In 2019 it created a parent company, Viocity Group, along with a new organizational structure designed to account for future growth, be it organic or through more acquisitions. It also launched a nonprofit organization, called Hope in the Air, that supports local causes.
Miller and his team set out to create their own future, and what a future it has turned out to be.
New Building, New Thinking
In December 2006, Miller, as the new company president—a position no one expected him to be in so soon—conducted his first companywide annual meeting. “At that point I made the decision that we were going to rebrand Herr & Sacco and look for a property to build a new facility, focusing on additional shop capacity and capabilities.”
Miller emphasized that such a bold move—particularly at that point in time—wouldn’t have been possible without a loyal team that bought into, supported, and helped define the changes the company made. Long tenure at H&S was and still is the norm. Some have been with the company for more than 40 years. “It all wouldn’t have been possible without our people buying into the changes and helping define them every day.”
A few miles northwest of Lancaster, Landisville epitomizes the small Pennsylvania town: leafy residential streets, wide front porches, and a compact downtown bisected by railroad tracks. “Compact” is the operative word. The streets were never built to carry giant pressure vessels and other large, industrial fabrications that had become H&S’s bread and butter. Oversized truck loads sometimes needed the help of a crane to get such large fabrications into and out of H&S’s shipping and receiving dock.
It was obvious to Miller that the fabricator had gotten just about all it could out of the old Landisville plant. The company needed more space, and it eventually found available land in the countryside outside Manheim, less than 10 miles from Landisville.
“We found the land in 2008, and we spent two years designing the current facility,” Miller said. “We didn’t need to move [from Landisville] immediately, so we took the time to really look at the entire business, including the efficiencies of the work flow, the services we offer, and the potential for growth.”
Company leadership scrutinized all aspects of production, from raw material storage to the final manufacturing step, which was almost always some type of finishing, including blasting and painting booths capable of handling large work.
Soon after the new plant opened in 2011, it boasted unique finishing capacity for the area. Its blast booth has a 22- by 24-foot door that leads into an 80-ft.-long chamber. The adjacent paint booth is the same size but also can be split into 40-ft.-long sections, depending on the mix of work.
The mix of H&S’s work changes day to day and week to week, and various stages of fabrication can take different amounts of time. When they are working on large industrial and structural fabrications, everything from platforms to ASME code-level pressure vessels, it’s just impractical to level-load the shop floor, where one workstation has roughly the same fabrication time as the next. The work is just too diverse.
At the same time, H&S avoided the traditional “work bay” approach, whereby an entire project is built in one place from the ground up. To make the operation truly efficient, workers would need every tool for every type of job, all at the point of use in each work bay. That’s fine for a small job with a limited scope of work, but broaden the scope and scale up the operation and things get complicated in a hurry.
At the same time, managers knew they couldn’t lay out a traditional fabrication and assembly line. This goes back to the level-loading problem. A particular pressure vessel might take a long time to weld, while the structural platform behind it could take half as long.
To overcome this problem, they went with a lane-based layout, essentially a four-lane highway with a large aisle that cuts across the four lanes—giving projects a “passing lane” of sorts. The layout allows projects to flow from one end of the plant to the other at their own pace. If a project in one lane undergoes a time-consuming manufacturing step, projects behind it move across to another lane.
Before the highway starts, plasma cutting tables, press brakes, and other equipment near the receiving dock are dedicated to parts fabrication that feed the main assembly lines. Also near the dock are material storage towers for plates and shapes (like tubes and angles), effectively making most of H&S’s raw stock inventory immediately retrievable at the push of a button. After all, it’s difficult to attain good flow if workers spend hours hunting for specific pieces of raw stock.
At the end of the lanes, projects flow to blasting and painting, after which they end up in shipping and receiving at the back of the building. It’s a classic U-shaped flow adapted to high-product-mix industrial fabrication.
Broadening Capabilities
The building’s layout facilitates rapid part flow, but it can’t by itself prevent all delays, particularly when it comes to subcontracting. Industrial construction involves the coordination of multiple functions, and for years Miller and the H&S leadership team have worked to provide as many of those functions as they can: metal fabrication, process and utility piping fabrication and installation, custom rigging, and blasting and painting.
“We’re always looking to provide our customers with a turnkey solution, so we can control the work environment,” Miller said. “It just makes sense to have more industrial trades in one organization, so we can all work together.”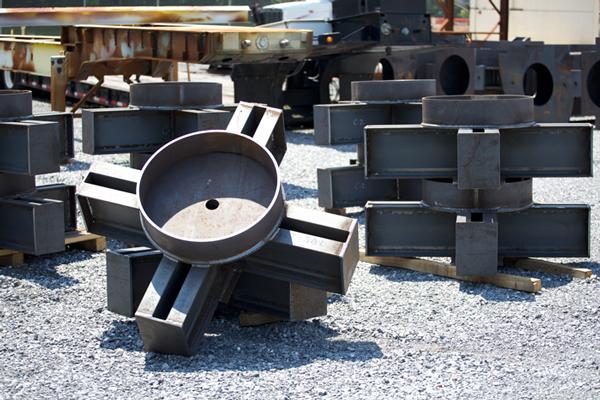
Industrial fabrication and installation have been the company’s bread and butter for decades. But in recent years, Viocity has branched out.
This was the thinking behind H&S’s 2018 acquisition of RSR Electric, a nearby, 30-employee electrical contractor—and, like H&S, a family business with longtime employees. Today electricians collaborate with the fabrication team on various projects. When H&S receives an order for, say, a piping skid project, it no longer needs to sub out the electrical work but can instead coordinate with RSR electricians from the very start.
The acquisition also broadened the H&S customer base and helped foster long-term relationships. Some companies might use only RSR Electric’s services, but others might have a need for other work. For instance, at first they might need electrical work involving power supplies; HVAC control systems; or infrastructure for data communications, testing, and certification, all provided by RSR Electric. Those customers might need industrial fabrication work from H&S down the road.
At the same time, RSR Electric happens to have a need for sheet metal fabrication, like for control cabinets and cable trays, which is prime work for a laser cutting division H&S launched in 2016.
“We knew we could utilize laser cutting for our internal work,” Miller said, “but the bigger vision was to bring in [laser cutting and precision bending] to attract a new customer base and go after different types of work.”
Within a smaller facility adjacent to the main plant, the company installed a TRUMPF laser complete with material handling storage towers and offloading automation, an investment tailored for production fabrication work for OEMs and similar customers. The thinking here: Industrial fabrication involves project-based work, which makes for “lumpy” work flow and challenges with capacity planning. Most jobs are one-off projects, and busy times require a lot of people working together to get fabrications out the door and installed at the job site.
Diversifying has helped, and so has cross training. “The more depth [in different market areas] you have, the more flexibility you have with capacity planning,” Miller said. “Our field employees are cross-trained for the shop, and our shop employees are cross-trained for the field—so much so that our pipefitters could be millwrights, or our millwrights could be pipefitters or welders. Similarly, the electrical company recently went through a very busy period, and we were able to support them.”
All this growth, with so many divisions and capabilities, eventually led to the company’s rebranding in January 2019. A new parent organization, Viocity Group, was created with three subsidiaries: H&S Industrial, RSR Electric, and Nitro Cutting Services for precision sheet metal cutting and forming.
Into Laser Tube Cutting
In spring 2019 Viocity Group leapt into an arena rarely touched by industrial fabricators and mechanical contractors: laser tube cutting.
“I’ll be honest, the tube laser was a surprise to a lot of people,” Miller said. “It’s brand new for us.”
That said, Viocity isn’t just an industrial fabricator anymore. Installed in the Nitro Cutting facility, the TRUMPF 4-kW tube laser can accept round tubes with outside diameters up to 10 in. and up to 3/8-in.-thick walls, depending on the material grade. It also has integrated flow drilling (which creates and heats the hole perimeter to form an extrusion that accepts threads) and tapping.
The system has a 30-ft. infeed and 20-ft. outfeed, enough to handle very long tubes, which was intentional. Not only will the tube laser help Viocity enter new markets, it will help the people at H&S think differently about certain fabrications. The tube laser’s beveling capability has helped reduce weld prep for pipe fabrications. And tab-and-slot, self-fixturing tubular assemblies are now finding their way to the production lanes of the main H&S plant, helping accelerate projects toward the (real and metaphorical) finish line.
Butterflies
Walk into the expanse of the H&S plant and you might see a massive pressure vessel in one area, a piping skid in another area, plate rolling and plasma cutting in action, and heavy machinery galore. Perched on the side of many of those machines is a delicate butterfly, laser-cut from thin sheet metal and intricately painted.
It began several years ago with some internal projects, shortly after the company installed its first laser. Operators began cutting butterflies—just something whimsical for home gardens.
“What began as an internal project transformed into community involvement,” said Sasha Wawrzyniak, Viocity’s general manager. “We began producing a limited number of custom butterflies for a local hospice and community care organization, which it sells for a 100 percent profit at a Labor Day auction and throughout the year. It’s typically around 400 butterflies, which we donate to them.”
“But now this has gone a step further,” Miller added. “About three years ago we formed an organization called Hope in the Air. And the butterfly symbolizes hope.” This year Hope in the Air became an officially recognized 501(c) (3) nonprofit organization.
Every year the nonprofit finds a local organization to support. “We try to work with organizations that don’t have big marketing budgets or large staffs, and we promote their cause,” Miller said, “and we hold an annual gala. So what started out as just a side project, just to see what our laser could do, has turned into an organization that hosts annual galas that raise more than $100,000 for worthy causes.”
In 2018 the organization raised money for Penn State Children’s Hospital’s Facility Dog Program, and this year it’s raising money for a similar facility dog program at Children’s Hospital of Philadelphia.
The nonprofit culminates a transformation that the company founders would appreciate, including Chris Sacco (the “S” behind H&S).
Sacco began his working life around 1930, just in time for the Great Depression. He took what job he could find, as a cook at Hotel Hershey in nearby Hershey, Pa. His brother-in-law, a wing designer for Glenn L. Martin in Baltimore, got him into pipe welding, and Sacco launched H&S with just one welding rig in 1949. With all the food processing plant repair work in the area, H&S continued to grow.
Miller’s father, Jim, joined Sacco in 1969 and became the president upon Sacco’s retirement in the mid-1980s. The past presidents didn’t live long enough to see the company grow into what it is today. No doubt they’d appreciate the future their successors have created.
About the Author
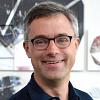
Tim Heston
2135 Point Blvd
Elgin, IL 60123
815-381-1314
Tim Heston, The Fabricator's senior editor, has covered the metal fabrication industry since 1998, starting his career at the American Welding Society's Welding Journal. Since then he has covered the full range of metal fabrication processes, from stamping, bending, and cutting to grinding and polishing. He joined The Fabricator's staff in October 2007.
Related Companies
subscribe now
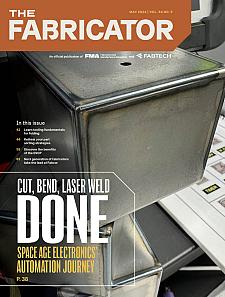
The Fabricator is North America's leading magazine for the metal forming and fabricating industry. The magazine delivers the news, technical articles, and case histories that enable fabricators to do their jobs more efficiently. The Fabricator has served the industry since 1970.
start your free subscription- Stay connected from anywhere
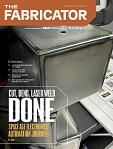
Easily access valuable industry resources now with full access to the digital edition of The Fabricator.
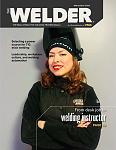
Easily access valuable industry resources now with full access to the digital edition of The Welder.
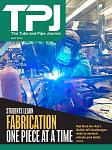
Easily access valuable industry resources now with full access to the digital edition of The Tube and Pipe Journal.
- Podcasting
- Podcast:
- The Fabricator Podcast
- Published:
- 04/30/2024
- Running Time:
- 53:00
Seth Feldman of Iowa-based Wertzbaugher Services joins The Fabricator Podcast to offer his take as a Gen Zer...
- Industry Events
Pipe and Tube Conference
- May 21 - 22, 2024
- Omaha, NE
World-Class Roll Forming Workshop
- June 5 - 6, 2024
- Louisville, KY
Advanced Laser Application Workshop
- June 25 - 27, 2024
- Novi, MI
Precision Press Brake Certificate Course
- July 31 - August 1, 2024
- Elgin,