Managing Director
- FMA
- The Fabricator
- FABTECH
- Canadian Metalworking
Categories
- Additive Manufacturing
- Aluminum Welding
- Arc Welding
- Assembly and Joining
- Automation and Robotics
- Bending and Forming
- Consumables
- Cutting and Weld Prep
- Electric Vehicles
- En Español
- Finishing
- Hydroforming
- Laser Cutting
- Laser Welding
- Machining
- Manufacturing Software
- Materials Handling
- Metals/Materials
- Oxyfuel Cutting
- Plasma Cutting
- Power Tools
- Punching and Other Holemaking
- Roll Forming
- Safety
- Sawing
- Shearing
- Shop Management
- Testing and Measuring
- Tube and Pipe Fabrication
- Tube and Pipe Production
- Waterjet Cutting
Industry Directory
Webcasts
Podcasts
FAB 40
Advertise
Subscribe
Account Login
Search
Tube bending technology buoys shipbuilding
How efficient technology meets the tube bending challenges of supplying the maritime industry
- By Bert Zorn
- March 2, 2021
- Article
- Tube and Pipe Fabrication
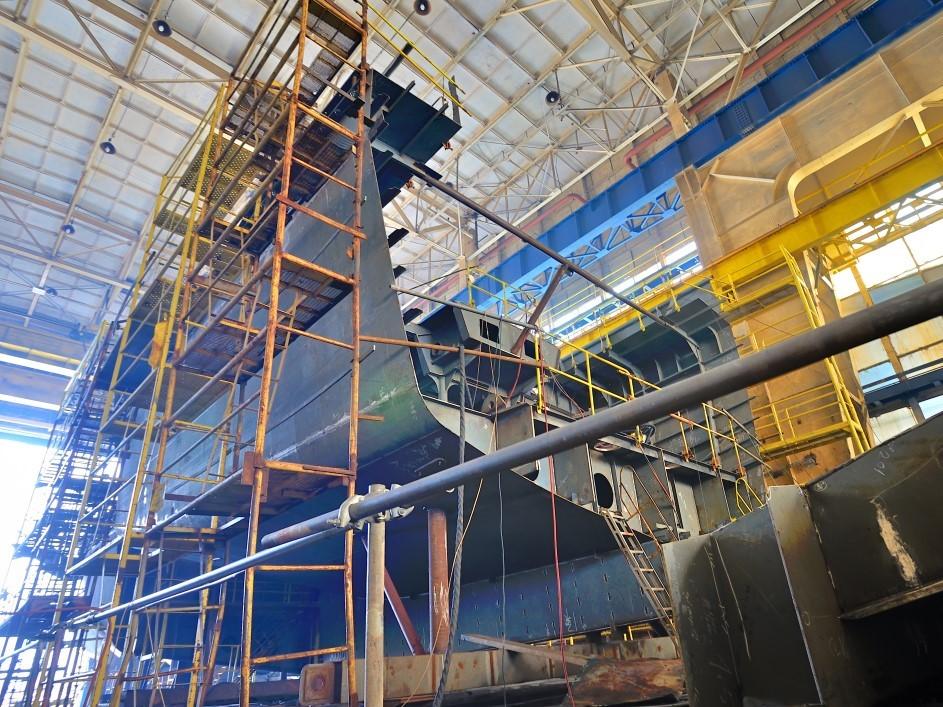
It used to take two years to build a new cruise ship; today it is launched in just a few months. Tube bending fabricators must accelerate production.
To survive in the competitive maritime environment, shipbuilders around the world must produce faster and faster. Whereas it used to take two years to build a new cruise ship, today it is launched in just a few months. Cycle times in the maritime industry have been drastically reduced.
Maritime industry OEMs are passing this pressure on to their suppliers, including tube and pipe bending fabricators, demanding production technologies that save time and thus costs and increase productivity.
Miles and miles of piping–large and small diameter–are installed on tankers, container ships, and cruise liners to transport fuel, water, oils, gases, and hydraulic fluids, some of which are under high pressure.
Bending tube and pipe for the complex requirements of the shipbuilding industry comes with many challenges. Fabricators must meet tight time frames. The tube and pipe materials have become high tensile strength, putting the benders under heavy-duty conditions. The products must be bent with especially small radii because space onboard is severely limited. The tube and pipe benders are under continuous use to meet high-volume demands.
Meeting Tight Time Frames
Production time is a critical competitive factor for shipyards (see The Shipbuilding Industry subhead below). The faster the ship is launched, the better. Downtime costs time and money. That is why it must be avoided as much as possible.
Setup Times. Demands have increased for shorter refitting times on tube bending machines, so fast tool changes are of central importance. Therefore, continuous setup time optimization is critical.
The control plays a major role. Increasingly, the bending machines can prepare and accompany the tool changes themselves, whereas manual cranking had been required. Multistack bending tools make the biggest difference regarding refitting times. They allow tubes and pipes with different nominal diameters to be bent on one machine without refitting. Thanks to the sophisticated control and machine concepts, refitting times have fallen by up to 80% over the years, and machine utilization and productivity have increased as a result.
ERP Software. To meet shipbuilding schedules successfully, the fabricator must have every component available at exactly the right time in exactly the right place. Just-in-time delivery is required for the bent pipes. The right pipe must be installed at the right time without having to be stored for months beforehand.
The shipyards' ERP software maps the entire production process so that all process steps mesh seamlessly. This also applies to the installation of the pipelines onboard. Therefore, the tube and pipe bending machines used must also be capable of interfacing with it. The bending machine software must be easily integrated into the higher-level software system, and networking with the other production systems is required.
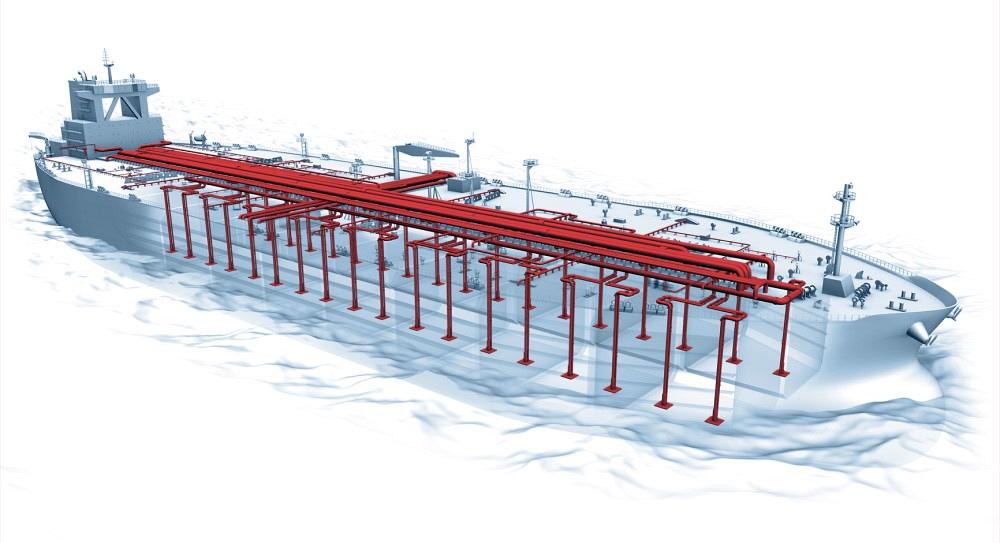
The system in a ship that transports fuel, water, oils, gases, and hydraulic fluids comprises miles and miles of tube and pipe.
However, because there is no uniform industry standard here, bending machine manufacturers deal individually with each user and its specific software. For the data exchange between the machines and systems to be implemented in a user-specific manner, the bending technology must have flexible software and control. The system must remain flexible enough to allow the fabricator to react to changes in plans or repairs that become necessary and to produce the pipes required for this purpose quickly.
Managing High-strength, Demanding Materials
The maritime and offshore industries are also relying on increasingly higher-tensile-strength materials. This is because maintenance represents a significant cost factor. The longer the maintenance cycles of the tube and pipe systems, and the longer the time before a pipe must be replaced, the lower the lifetime costs of a ship or oil platform.
To extend maintenance cycles effectively, manufacturers are using high-strength materials, such as corrosion-resistant alloys and stainless steel. But the composition of these alloys makes them more brittle and, thus, more difficult to bend. These materials bring new requirements which also call for the use of very robust and powerful machines.
Variations in the raw material pose an additional challenge. Both the pipe diameter and wall thickness manufactured for use in the maritime industry are subject to certain tolerance requirements, which are regulated by the DIN EN ISO 1127 standard. For example, in 8-in.-NPS [nominal pipe size]-dia. (219-mm-dia.) pipes, deviations in the single-digit-millimeter range can occur.
A tube and pipe bending machine should be able to compensate for such deviations as much as possible. If the actual pipe diameter deviates from the nominal diameter, this can lead to difficulties during the bending process. For example, if the diameter is larger than specified, a greater clamping force is required during bending. The better the machine itself can compensate for such fluctuations, the more the pipe can deviate from the optimum within the standard specification.
The shipbuilding industry has high quality requirements for its components. Compliance with requirements for wall thinning and wrinkling is regulated by numerous standards and is therefore an important acceptance criterion against which suppliers are measured. For example, if tube and pipe walls are too thin when media is transported under high pressure through the pipelines onboard, safety can be compromised. The pipes must be able to withstand this pressure.
Again, shipbuilders are increasingly relying on sophisticated high-strength materials with thinner walls. The wall thickness to be maintained thus determines the entire bending process from the outset. In addition to a high-performance basic machine, the control technology is crucial for precise bending results to comply with required standards.
Bending Small Radii
Space onboard is in high demand. The less space tube and pipe networks for fuel, water, oils, gases, and hydraulic fluids take up, the more usable space there is for passengers and cargo containers--in other words, for what brings in shipping revenue. This increases cost efficiency.
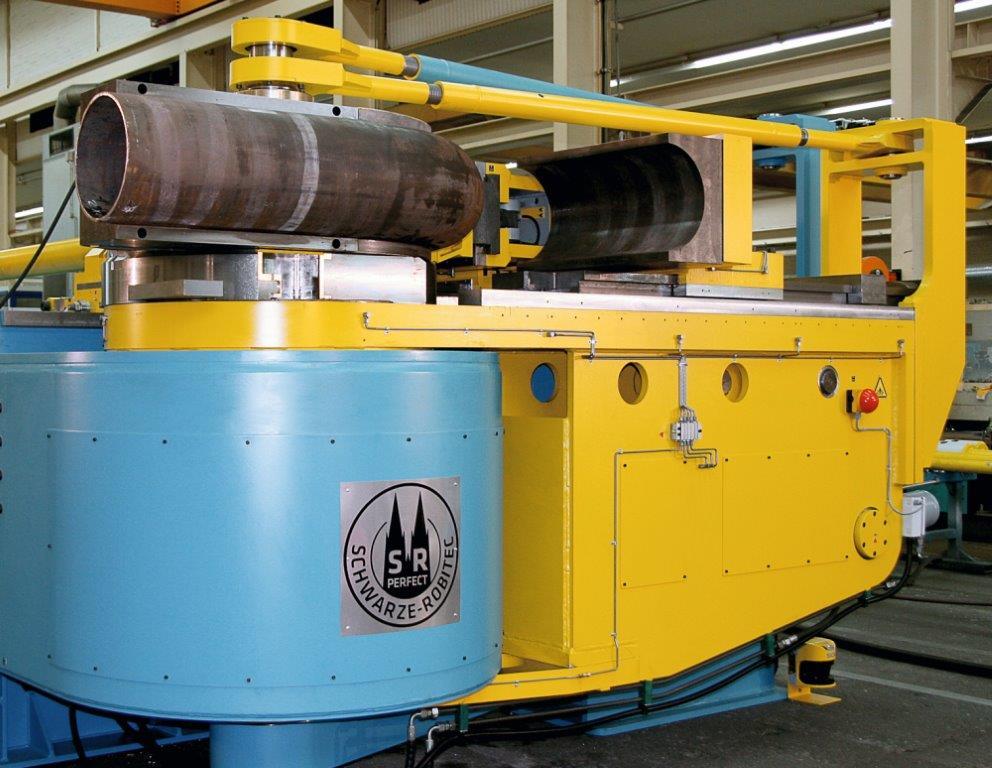
A bending machine for the shipbuilding industry must be robust enough to meet its material demands and tight radii requirements.
To save space and thus costs, shipbuilders rely on space-saving piping systems. For this purpose, the pipes must be bent with especially tight radii. Modern tube and pipe bending machines can achieve bending radii of 1.5xD. Depending on the project requirements and the machine used, even a bending radius as small as 1.0xD is possible.
This calculation example shows the advantage of small bending radii: A 90-degree pipe bend with an 8.6-in. dia. with a bending radius of 1.5xD takes up approximately 1.48 sq. ft. of installation space. With a bending radius of 3.0xD, the required installation space increases to 4.56 sq. ft. In this case, the small bending radius results in a space saving of around 67%. Extrapolated to many miles of pipeline on a ship, the effect is immense.
However, the production of small bending radii places special demands on the bending technology used. The basic machine must be sturdily designed to reliably absorb the enormous forces generated during bending.
The clamping functions need sufficient power reserves because the smaller the pipe radius to be bent, the greater the clamping force required during bending. Clamping force is the pressure with which the pipe is pressed against the tool during the bending process. Bending radii of 1.5xD require enormous clamping forces and a machine that is precisely aligned for this.
To apply a sufficiently large clamping force for small radii as well as to be able to reliably bend demanding materials such as stainless steel and compensate for material fluctuations, a tube and pipe bending machine must have a stable design and be particularly powerful and durable. A great deal of experience and technical expertise are required in the design.
Fast and robust machines enable the bending of particularly small radii in a short time for the maritime industry. The decisive factor here is the interface-capable design of the machines, their components, and the software, so that the bending technology can be integrated easily into the entire production chain.
High-volume Demand, Continuous Use
Further productivity and efficiency gains are achieved by integrating the bending technology – not only on the software side, but also holistically–-into the overall production logistics.
Great importance is attached to linking with and automating upstream and downstream process steps. This is not only because bending technology increases tube and pipe bending productivity, it also makes all associated processes more efficient.
Systems upgraded to automated bending cells also simplify and accelerate processes such as machine loading/unloading, delivery of pipe sections via the internal conveyor system, removal of bent pipe, and insertion of flange tubes and pipes.
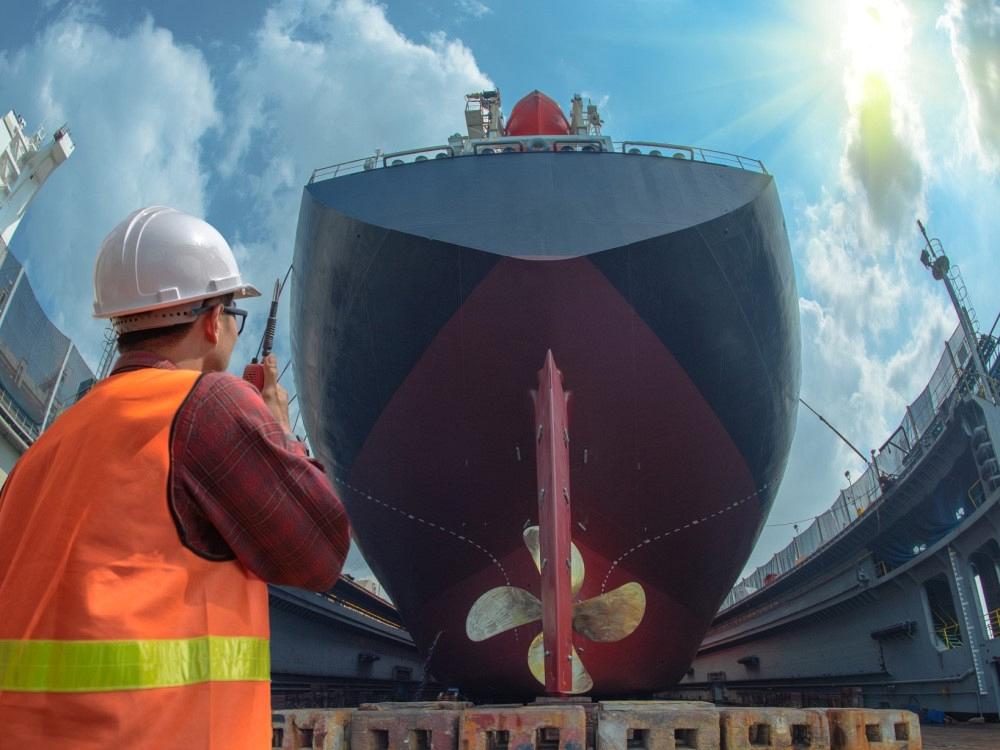
More than 11 billion metric tons of cargo were unloaded globally in 2019; more than 28 million cruise passengers set sail worldwide in 2018.
For both shipbuilders and tube fabricators to succeed in meeting today’s demands, bending machines must be designed with the appropriate interface capability and state-of-the-art controls so that tube bending fabricators can flexibly respond to customer-specific requirements and react to ever-changing production challenges.
The Shipbuilding Industry
The maritime industry is one of superlatives. This is demonstrated by a brief look at some key figures.
Just under 11.1 billion metric tons of cargo were unloaded in global seaborne trade in 2019. More than 28 million cruise passengers set sail worldwide in 2018. The world's largest cruise ships now take up to 5,500 passengers onboard at a time.
The largest shipbuilding nation is China. The country led the global shipbuilding industry in 2019 with an order volume of around 27 million compensated gross tons, followed by South Korea and Japan. Germany ranks fourth.
The German shipbuilding and offshore supply industry is strongly characterized by medium-sized companies. According to the German Ministry of Economics, the approximately 400 companies in the sector employed about 64,500 people in 2019 and generated sales of $13.6 billion. With an export ratio of 75%, the most important sales markets are abroad. After Europe and Asia, North America accounts for 11.4% of sales.
It used to take two years to build a new cruise ship; today it is launched in just a few months. Tube bending fabricators must accelerate production.
More than 11 billion metric tons of cargo were unloaded globally in 2019; more than 28 million cruise passengers set sail worldwide in 2018.
About the Author
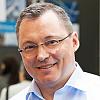
Bert Zorn
Olpener Str. 460-474
Cologne, Germany
49-221-8900-80
subscribe now
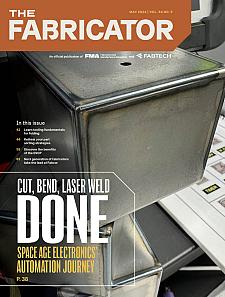
The Fabricator is North America's leading magazine for the metal forming and fabricating industry. The magazine delivers the news, technical articles, and case histories that enable fabricators to do their jobs more efficiently. The Fabricator has served the industry since 1970.
start your free subscription- Stay connected from anywhere
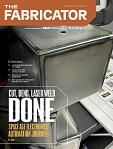
Easily access valuable industry resources now with full access to the digital edition of The Fabricator.
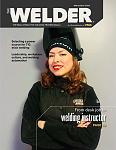
Easily access valuable industry resources now with full access to the digital edition of The Welder.
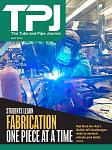
Easily access valuable industry resources now with full access to the digital edition of The Tube and Pipe Journal.
- Podcasting
- Podcast:
- The Fabricator Podcast
- Published:
- 04/16/2024
- Running Time:
- 63:29
In this episode of The Fabricator Podcast, Caleb Chamberlain, co-founder and CEO of OSH Cut, discusses his company’s...
- Trending Articles
Tips for creating sheet metal tubes with perforations
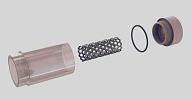
Supporting the metal fabricating industry through FMA
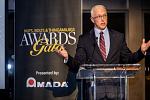
JM Steel triples capacity for solar energy projects at Pennsylvania facility
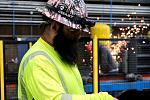
Fabricating favorite childhood memories
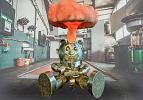
Omco Solar opens second Alabama manufacturing facility
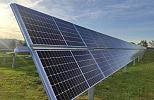
- Industry Events
16th Annual Safety Conference
- April 30 - May 1, 2024
- Elgin,
Pipe and Tube Conference
- May 21 - 22, 2024
- Omaha, NE
World-Class Roll Forming Workshop
- June 5 - 6, 2024
- Louisville, KY
Advanced Laser Application Workshop
- June 25 - 27, 2024
- Novi, MI