Editor-in-Chief
- FMA
- The Fabricator
- FABTECH
- Canadian Metalworking
Categories
- Additive Manufacturing
- Aluminum Welding
- Arc Welding
- Assembly and Joining
- Automation and Robotics
- Bending and Forming
- Consumables
- Cutting and Weld Prep
- Electric Vehicles
- En Español
- Finishing
- Hydroforming
- Laser Cutting
- Laser Welding
- Machining
- Manufacturing Software
- Materials Handling
- Metals/Materials
- Oxyfuel Cutting
- Plasma Cutting
- Power Tools
- Punching and Other Holemaking
- Roll Forming
- Safety
- Sawing
- Shearing
- Shop Management
- Testing and Measuring
- Tube and Pipe Fabrication
- Tube and Pipe Production
- Waterjet Cutting
Industry Directory
Webcasts
Podcasts
FAB 40
Advertise
Subscribe
Account Login
Search
Advanced technology to bridge the gap in skills development
Fabricators learning that the right capital equipment investment can make up for an inability to hire
- By Dan Davis
- January 2, 2024
Without a doubt, some metal fabricating companies in November experienced a slowdown. We heard from them, but they were likely more surprised than worried. It’s been a wild ride since the pandemic occurred.
That ride is going to continue in the coming months. The trends are a metal fabricator’s friend.
What was once thought to be the world’s job shop, China is now reporting declines in exports. The trade deficit between the U.S. and China contracted 4.1% to $65.5 billion in June, the lowest level seen in more than 18 months. Meanwhile, leaders of multinational companies are starting to turn their backs on China as a source for manufacturing expertise, as the country copes with an unreliable manufacturing base and a more demanding workforce. In fact, a 2023 survey of U.S.-based manufacturing executives by Forbes, Xometry, and Zogby revealed that 82% of them were either moving overseas factories back home or were in the process of doing so.
Meanwhile, the billions associated with the one of the biggest investments in U.S. infrastructure—courtesy of the Inflation Reduction Act, the Infrastructure Bill, and the CHIPS Act—is going to start working its way into the economy in the coming months. This is going to invigorate traditional manufacturing segments like structural steel shops, but also fuel the growth of alternative energy industries, such as hydrogen production, storage, and delivery.
Metal fabricators should have plenty of opportunities to remain busy and profitable in the near future. But will they be able to take advantage of the opportunities as they struggle to find workers? Since the pandemic, manufacturing companies have done well in replacing jobs that were lost, but as of August 2023, 616,000 total manufacturing job openings still remain unfilled. Given that the White House wants to create another 5 million manufacturing jobs as part of this Build Back Better initiative, that’s a lot of current and potential job vacancies to fill.
On the bright side, some societal shifts make it more likely that young people might more seriously consider a career in manufacturing. More school districts are investing in vocational skills development at the behest of local manufacturing companies. Generation Z is cognizant of the need to develop skills for which they can maximize life outside of work, and they aren’t keen in amassing debt to attain those skills.
But that’s not likely to solve the problem for all manufacturing companies, particularly the small and medium-sized shops that make up the backbone of the metal fabricating industry. They need something more sure than the whims of an 18 year old who might be interested in welding because of a virtual reality experience. That foundation for increased manufacturing capacity and optimized operations is going to be provided by advanced manufacturing technology.
You are starting to see it already. Cobots have been around for a couple of years now, but shops are starting to use them more seriously, particularly when it comes to welding. “Cobot helps build capacity at Skyvington Manufacturing” from the upcoming January 2024 issue of The Fabricator provides a glimpse into how an automation investment can make a big impact. Brett Skyvington, manager of the company’s fabrication operations, estimates that the company’s experience using the cobot in welding situations allows it to now run certain gas metal arc welding jobs three to four times faster than a human welder. The welds also are good enough that they don’t require any type of postprocessing.
“It used to be that we needed large-run jobs to be able to utilize our robotic solutions, but now we can do it for much smaller runs. Being able to use an automated solution on jobs that were previously unfeasible for us is a big gain,” he said.
That’s just one example. Quoting software is going to be able to learn from real-time manufacturing operations to offer more accurate quotes and delivery times. Nesting software will continue to grow smarter, avoiding cutting scenarios that result in tip-ups, for example, which leads to risk-free, lights-out cutting. Even machines, such as plate roller machines and tube bending machines, will make those black arts a little more user-friendly. The examples are many.
The use of advanced technology does not guarantee that a company will be successful, but it puts it in a much better position to accomplish its goals. That’s something on which metal fabricators can count.
subscribe now
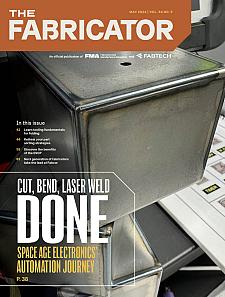
The Fabricator is North America's leading magazine for the metal forming and fabricating industry. The magazine delivers the news, technical articles, and case histories that enable fabricators to do their jobs more efficiently. The Fabricator has served the industry since 1970.
start your free subscriptionAbout the Author
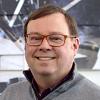
Dan Davis
2135 Point Blvd.
Elgin, IL 60123
815-227-8281
Dan Davis is editor-in-chief of The Fabricator, the industry's most widely circulated metal fabricating magazine, and its sister publications, The Tube & Pipe Journal and The Welder. He has been with the publications since April 2002.
Related Companies
- Stay connected from anywhere
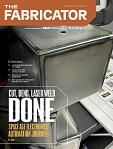
Easily access valuable industry resources now with full access to the digital edition of The Fabricator.
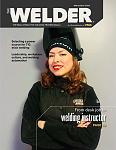
Easily access valuable industry resources now with full access to the digital edition of The Welder.
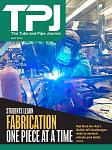
Easily access valuable industry resources now with full access to the digital edition of The Tube and Pipe Journal.
- Podcasting
- Podcast:
- The Fabricator Podcast
- Published:
- 04/16/2024
- Running Time:
- 63:29
In this episode of The Fabricator Podcast, Caleb Chamberlain, co-founder and CEO of OSH Cut, discusses his company’s...
- Trending Articles
Tips for creating sheet metal tubes with perforations
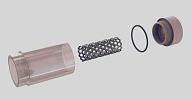
Supporting the metal fabricating industry through FMA
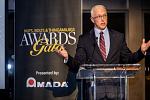
JM Steel triples capacity for solar energy projects at Pennsylvania facility
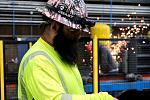
Fabricating favorite childhood memories
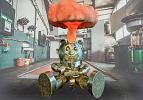
Omco Solar opens second Alabama manufacturing facility
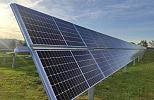
- Industry Events
16th Annual Safety Conference
- April 30 - May 1, 2024
- Elgin,
Pipe and Tube Conference
- May 21 - 22, 2024
- Omaha, NE
World-Class Roll Forming Workshop
- June 5 - 6, 2024
- Louisville, KY
Advanced Laser Application Workshop
- June 25 - 27, 2024
- Novi, MI