Editor-in-Chief
- FMA
- The Fabricator
- FABTECH
- Canadian Metalworking
Categories
- Additive Manufacturing
- Aluminum Welding
- Arc Welding
- Assembly and Joining
- Automation and Robotics
- Bending and Forming
- Consumables
- Cutting and Weld Prep
- Electric Vehicles
- En Español
- Finishing
- Hydroforming
- Laser Cutting
- Laser Welding
- Machining
- Manufacturing Software
- Materials Handling
- Metals/Materials
- Oxyfuel Cutting
- Plasma Cutting
- Power Tools
- Punching and Other Holemaking
- Roll Forming
- Safety
- Sawing
- Shearing
- Shop Management
- Testing and Measuring
- Tube and Pipe Fabrication
- Tube and Pipe Production
- Waterjet Cutting
Industry Directory
Webcasts
Podcasts
FAB 40
Advertise
Subscribe
Account Login
Search
Put fears about job availability aside when talking automation
The presence of robots on the metal fabrication shop floor only likely to grow
- By Dan Davis
- July 20, 2022
Do you have a fear of robots? That’s not as strange of a question as it might seem.
Some people actually have a specific fear of human-like figures, like the robots found in science fiction movies, called automatonophobia. Others are OK with the idea of a robotic Mr. Belvedere, but are more concerned about the automated help reaching a level of sentience, leading to a refusal to clean bathrooms and possibly plotting to eliminate the human race.
That’s some scary stuff, but somewhat limited in scope. Most of us go about our day without worrying about the toaster plotting to replace us with lifelike automatons.
But if you are working in a metal fabricating facility, you know that the arrival of a robot is a big deal. The reaction of many people is that the robot is there to take someone’s job. That’s exactly what Bobby Silber, vice president of operations at TPI, a metal fabricating company in Garland, Texas, found when the shop brought in its first laser cutting machine with automated material delivery and removal, the robotic welder, and later an automated bending cell.
“When I got the automation, they thought it would help eliminate people. When I got the robots, they said it would help eliminate people,” Silber said.
That hasn’t been the case. If anything, Silber said that the extra fabricating capacity that the automation has added has opened the door to grow the business. The laser cutting machine and automated bending cell can run lights-out on a second or third shift that TPI would have difficulty finding workers for in the first place. As a result, people haven’t lost their jobs; they’ve been redeployed elsewhere. At TPI, they’ve been redeployed to help with material handling and packing of parts.
“You actually keep increasing people because of it,” Silber said.
TPI is not alone when it comes to embracing robots. In 2020, the Association for Advancing Automation (A3) reported that yearly orders of robots from nonautomotive sectors surpassed automotive robot orders for the first time. That’s 31,044 robots ordered by North American companies in 2020.
Last year saw robotic orders climb even higher. According to A3, the number of robots sold in North America set a new record in 2021, with 39,708 units sold at a value of $2 billion, a 14% increase over the previous high in 2017. Nonautomotive orders now represent 58% of the North American total. In the metals sector alone, robot sales increased 91% over 2020; the next most-active segment was food and consumer goods, where sales increased only 29% year over year.
“More industries recognized that robotics could help reverse productivity declines and fill repetitive jobs human workers don’t want. It is no longer a choice whether to deploy robots and automation,” said Jeff Burnstein, A3’s president. “It’s now an absolute imperative. As we’ve long believed—and users continue to confirm—robots help companies compete, ultimately creating more jobs to handle their growth.”
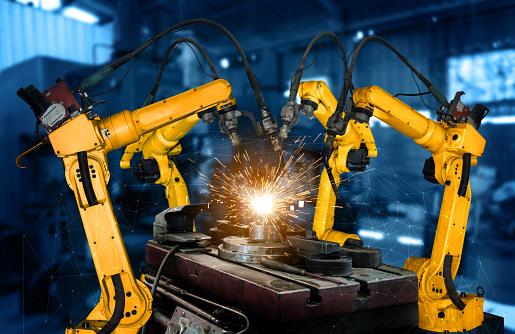
Robots won't take someone's job in a metal fabricating company. They will help management redeploy personnel to where they are needed, helping the company keep up with business opportunities. NanoStockk/iStock/Getty Images Plus
That’s being proven each and every day in the metal fabricating space, and it’s also probably feeding employee fears. Sure, it’s easy to tell employees that they have positions with a company when a robot arrives, but those positions are going to be different, something that can make people anxious. Can they master new machine controls? Will they get enough training to do the job effectively? Can they handle the physical requirements to do the job?
The fears only multiply for older workers, many of which are already behind the technological curve. Their younger colleagues grew up with smartphones, while they still hold onto their landlines. Change can be intimidating and frustrating for anyone, especially those that already feel overwhelmed with the pace of technology advancement around them.
With the fear of change, however, comes opportunity. Metal fabricating companies faced with integrating automation into the production process for the first time can begin honest conversations with employees about what this means for the company’s growth plans—and perhaps new career paths. Perhaps management wants to introduce more cross-training at this time to increase flexibility within the workforce. Automation might be the first step in running additional shifts with a handful of select employees, providing leadership and growth roles for those deemed worthy.
People’s fears are real. They shouldn’t be dismissed easily.
Robots are a fact of life for many metal fabricating facilities. They need to be accepted as reality. Believe it or not, they are here to help, no matter what Hollywood and the web forums might suggest.
subscribe now
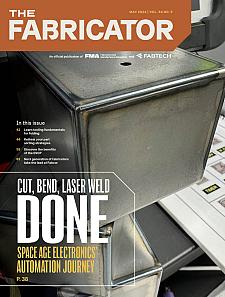
The Fabricator is North America's leading magazine for the metal forming and fabricating industry. The magazine delivers the news, technical articles, and case histories that enable fabricators to do their jobs more efficiently. The Fabricator has served the industry since 1970.
start your free subscriptionAbout the Author
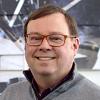
Dan Davis
2135 Point Blvd.
Elgin, IL 60123
815-227-8281
Dan Davis is editor-in-chief of The Fabricator, the industry's most widely circulated metal fabricating magazine, and its sister publications, The Tube & Pipe Journal and The Welder. He has been with the publications since April 2002.
- Stay connected from anywhere
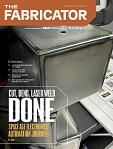
Easily access valuable industry resources now with full access to the digital edition of The Fabricator.
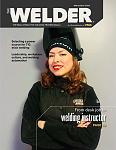
Easily access valuable industry resources now with full access to the digital edition of The Welder.
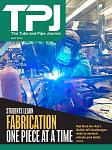
Easily access valuable industry resources now with full access to the digital edition of The Tube and Pipe Journal.
- Podcasting
- Podcast:
- The Fabricator Podcast
- Published:
- 04/30/2024
- Running Time:
- 53:00
Seth Feldman of Iowa-based Wertzbaugher Services joins The Fabricator Podcast to offer his take as a Gen Zer...
- Industry Events
Pipe and Tube Conference
- May 21 - 22, 2024
- Omaha, NE
World-Class Roll Forming Workshop
- June 5 - 6, 2024
- Louisville, KY
Advanced Laser Application Workshop
- June 25 - 27, 2024
- Novi, MI
Precision Press Brake Certificate Course
- July 31 - August 1, 2024
- Elgin,